From mergers & acquisitions to bankruptcies, expected & unexpected milestones, 2022 led us through an emotional rollercoaster.
As 2022 draws to a close, 3D ADEPT Media is looking back over a year difficult to characterize. To paraphrase a well-known book, we rejoiced with those who rejoiced, we felt empathy with those who were in some real uncomfortable situations, and most importantly, we analyzed, learned lessons and takeaways that hopefully, the industry will consider moving forward. Here is a wrap-up of what we will keep from business, the manufacturing value chain as well as vertical industries & standards.
1.   “Fortune favors the brave”, the saying goes, but is it always enough?
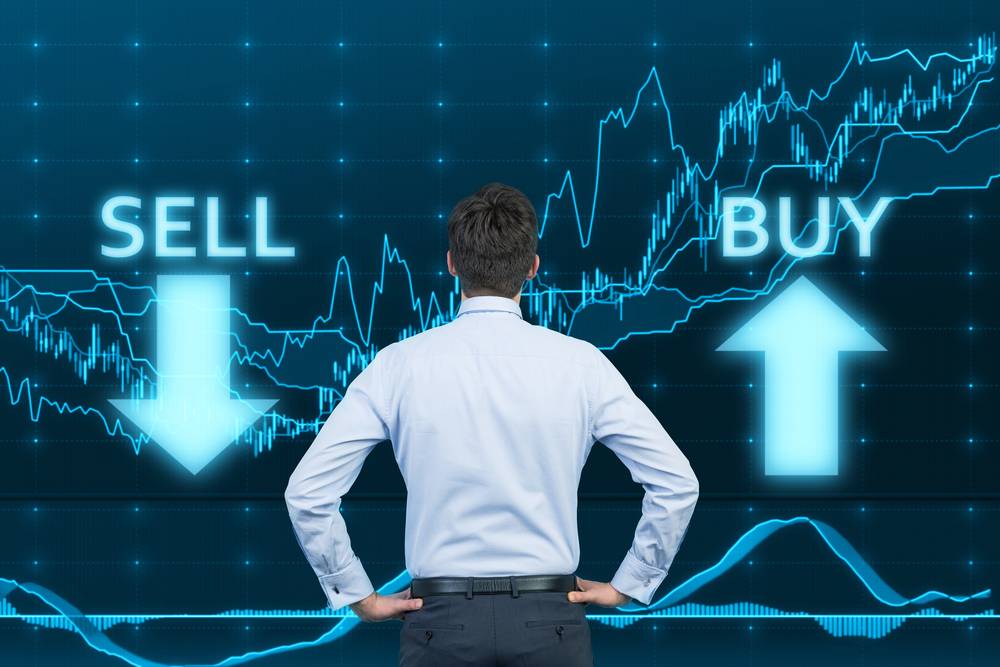
With over 53 acquisitions (including SPACs) recorded throughout the year – the biggest number ever reported since AM has been recognized as a true industry, 2021 was legitimately named a year of consolidation. With over 21 acquisitions reported this year, it’s fair to say this consolidation has continued in full force in 2022. However, unlike last year where the need for more financial resources was the main driver of these mergers & acquisitions, acquisitions reported this year highlighted a more thoughtful strategy from the buyers.
Buyer | Acquired | |
Stratasys | Covestro | |
Nikon | SLM Solutions | |
Lithoz | CerAMing | First company |
Materialise | Identify3D | |
Carbon | ParaMatters | First company |
Nano Dimension | Admatec, Formatec & Global Inkjet Systems Ltd. | |
Bico | Allegro 3D | |
Hyperganic | DirectFEM | First company |
3D Systems | Titan Robotics, Kumovis, dp polar | |
CORE Industrial Partners | RE3DTECH | |
Markforged | Digital Metal | |
Quickparts | Â Xcentric Mold & Engineering | |
Addman Group | Harbec, Castheon | |
HP | Â Choose Packaging | |
Prodways | Auditech Innovations | |
Authentise | Elements Technology Platform | First company |
Table shows a short overview of M&A reported this year.
For instance, while the deal isn’t actually expected to close until early next year, speculation is well underway regarding the acquisition of SLM Solutions by NIKON. The multinational technology corporation is acknowledged for its metrology services in the additive manufacturing and for the quiet development of a 3D printer that has yet to be commercialized. However, with the acquisition of Morf3D, manufacturer of aerospace metal 3D printed parts and SLM Solutions, Nikon’s strategy is very similar to that of GE that acquired several big and specialized names to position itself as an undeniable expert on this maturing industry. In this case, if completed, this acquisition will bring an unparalleled range of possibilities across the entire value chain of the AM industry, but also across a key vertical that is driving the growth of this technology: aerospace.
Another interesting example might be the one of HP and Choose Packaging, a Scotland-based startup that fabricates paper containers that could be a wise alternative to packaging for drinks, laundry detergent, make-up or food. At first glance, the first thought might be: what does a company that makes paper containers, have to do with 3D printing? Well, at the heart of the manufacturing process, one finds HP’s Multi Jet Fusion (MJF) technology and a plant-based barrier material that can make molded fiber containers waterproof. The combination of these solutions results in packages that are recyclable, even compostable. Although this purchase builds on top of HP’s existing molded fiber tooling service, can we not see the fact that 3D printed tools are used to quickly fabricate molds as a boost for a vertically integrated sustainable business enabled by additive manufacturing; the one of eco-friendly containers for the consumer goods industry?
 The last example I would like to mention here is the one of Authentise that goes beyond AM with its acquisition of Elements Technology Platform. As of today, the software company is now gaining some market shares outside of the AM as well, by providing a unique self-serve tool for all types of manufacturing operations, to quickly create, capture and access repeatable shop floor processes. It’s the rule of not putting all your eggs in one basket. It’s that simple.
While these mergers and acquisitions have brought a breath of fresh air to the acquired companies, others have been suffocating due to the lack of air.
It’s crucial – in my opinion – to look at the companies that have filed for bankruptcy or shut down their activities. The reasons behind each disposal might be a warning that others should take into account to strive. We reported that 8 companies shut down or filed for bankruptcy this year: Digital Alloys (3D printer manufacturer), Local Motors (automotive manufacturer of 3D printed EV), Satori (resin 3D printer manufacturer), Fast Radius (AM Service bureau), Xerox, RIZE (3D printer manufacturer), and Clara.io (online 3D modelling company).
Most of the time, financial resources are pointed out as the number one reason behind a disposal, but I truly believe another crucial aspect to thrive – and therefore generate profits – is often overlooked: a thoughtful marketing strategy. Please, bear with me as I do not find any kind of joy in writing these lines. I do understand that one of the most heart-breaking decisions a founder can take is to close their business, but tech founders need to realize that sometimes, the company that sells the most is not often the one that has the best product, but just the best marketing strategy.
That being said, another reason that may explain the disposal of activities for some of these companies is the current economic environment. That was anyway the case for Fast Radius. The Chicago-based advanced digital manufacturing company states in a press communication it filed for bankruptcy due to “recent turbulence in the capital markets, which severely hampered [its] ability to set up the required capital structure.” The announcement was made last month, nine months after the company announced that it would list on the NASDAQ stock exchange, at which point a wave of layoffs started in the summer. The business has declared that it will remain operational and serve customers in the due course despite having filed voluntary petitions for relief under Chapter 11 of the United States Bankruptcy Code in the District of Delaware.
Disclaimer: This article was written before the acquisition of Fast Radius by SyBridge Technologies in $15.9M deal.
Photocopier pioneer Xerox which has sought to revitalize its business by venturing into AM with an ambitious acquisition that led to the deployment of the Elem X metal 3D printer, has completely eliminated its AM business. The company is now solely focused on supporting current installations.
To end on a lighter note of this “Business” part, I will say that fortune may not have favored those who are shutting down their activities, but it might favor the next wave of new comers entering the market. This is good news as most of them are spin-offs from research institutes or well-established companies with a solid expertise in another manufacturing field. Being backed by a bigger company is always good music for any player trying to find its move on the dancing AM floor. Some of these new entrants include EPSON, Jeol, Grob, Krauss Maffei and AviaTOOLS.
2.   The manufacturing value chain: materials and software called the tune
Manufacturing has historically been the industry to carry the most weight when it comes to leading the overall economy out of downturns. This has never been truer than during this post-Covid era. Indeed, the spotlight placed on additive manufacturing (AM) during the pandemic as a tool to overcome supply chain hardships led to an increasing transition to AM for its flexibility and on-demand production capabilities, and toward the use of AM as a source of product development. This also led to key developments across specific fields of the manufacturing value chain and specific vertical industries that have also been observed in 2022.
Materials, first area of growth
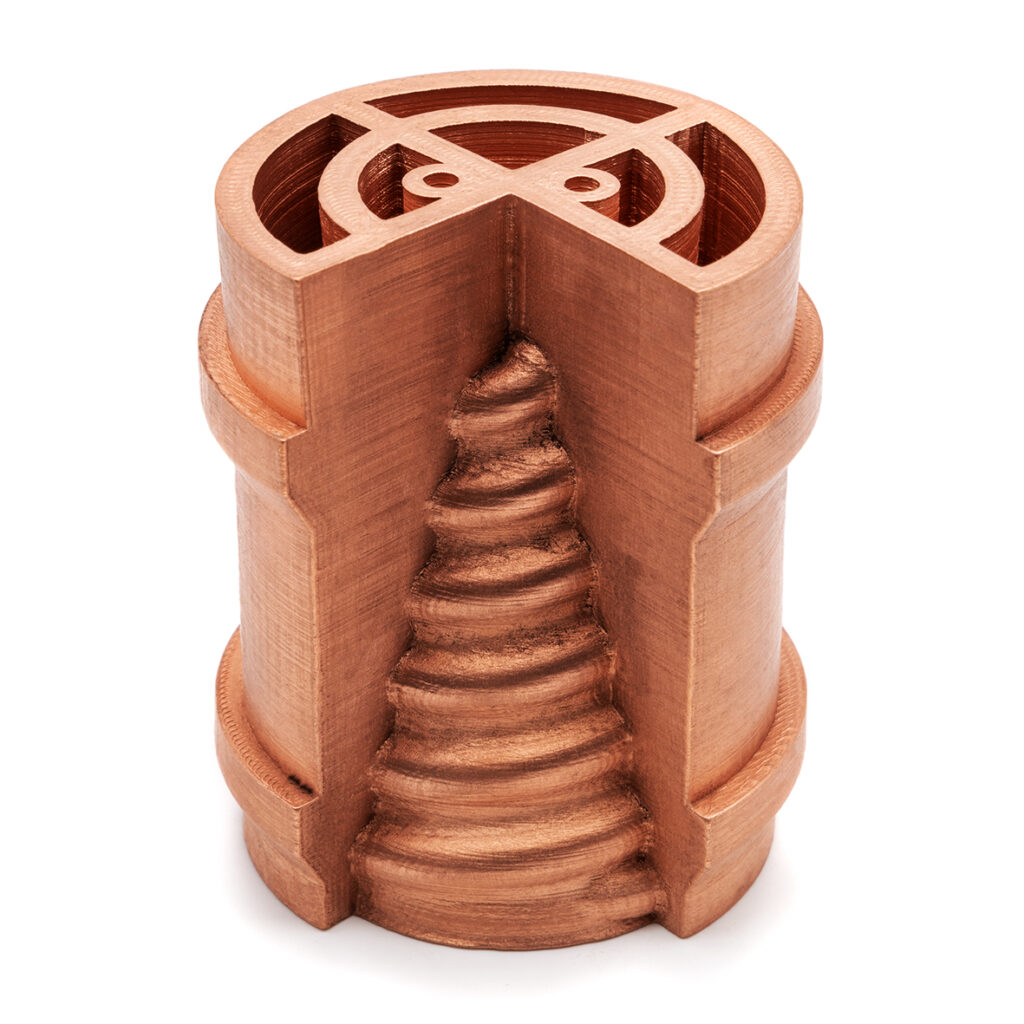
In this vein, the first area where we’ve observed interesting developments for the industry is materials. 2022 was another year where copper shone, be it in applications or new forms of materials available – That’s something Olaf DIEGEL also highlighted in his retrospective for 2022. Companies that added the third-most-consumed industrial metal to their portfolio include Infinite Flex, producer of smart materials, that has developed a pure copper powder for industrial SLM 3D printing; Kupros, a US-based company that develops an all-metal conductive copper filament; or 3D Systems that adds copper-nickel alloy for use with Metal 3D printing.
Applications that have demonstrated the potential of this material when combined with AM, include for instance induction hardeners (inductors) for gear wheels in the automotive sector and for chain wheels on chainsaws (developed by Schunk and AIM3D); a 3D printed copper cooling plate developed by JX Nippon Mining & Metals (JXNMM) and Alloyed, or this radio frequency quadrupole (RFQ), one of the most complex parts of any accelerator complex – developed by TRUMPF for CERN-coordinated I.FAST project.
On another note, I have been pleasantly surprised to see the development of materials that increasingly takes into account the environmental challenges and the need to fight climate change.
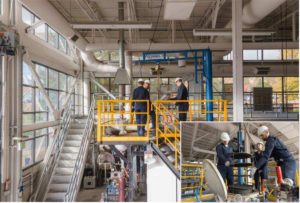
 In the metals side, one company that I would like to continue watching is IperionX (pp 38-40), a US material producer that is fostering a new age of low-cost Titanium for Additive Manufacturing. The material producer is one of the rare manufacturers that has demonstrated how its proprietary titanium metal processing technology does not involve the numerous carbon intensive melting processes seen in the Kroll process; and how they can produce titanium from either 100% scrap titanium or from conventional titanium minerals.
I wouldn’t stop looking at how companies take action in the polymer side, because as I always say, the challenge is higher for them due to the nature of their activity. Kudos to Evonik that is finally backing words with actions in the AM industry, with the introduction of a new grade of PA12 powders with significantly reduced CO2 emissions and which plans to go one step further next year. WASP is also one to mention as it develops a recycled fishing net material. This does not include the number of one-time applications that have been achieved with recycled materials.
Moving forward, my hope for next year is that more and more companies realize that sustainability should not be seen as a selling point, but truly as a core issue, given the fact that manufacturing has long been one of the most significant contributors to environmental pollution.
Software, finally taking off – and real solutions to reduce carbon footprintÂ
It’s been a couple of years that AM users have been asking for more robust software solutions across the manufacturing workflow; software solutions that can streamline workflows and integrate with existing enterprise solutions, software that can make it easier for engineers to design a part directly for additive manufacturing rather than having to design that part twice. I am not saying that what was available so far was not interesting, I am saying that they have been improved and others have been developed with a couple of magic ingredients.
AI is one of those ingredients. However, be aware that most companies use this word to make their product looks fancy, while a couple of them are actually taking advantage of it.
One company that really knows what they are doing here is Hyperganic that develops an AI-powered Algorithmic Engineering software. The latter uses customisable building blocks and frameworks to create individual applications and automate repetitive tasks, which may lead to applications for mass customisation, or generating complex internal cooling channels, lattice structures, and thin-walled geometries.
Speaking of SaaS solutions that can streamline workflows and integrate with existing enterprise solutions, I like the AI driven factory operating system developed by Oqton. The team brings to the table some solid expertise and their platform really encompasses all the capabilities one may look in product development. I was given a tour of the cloud-based manufacturing operating system, so I have been able to understand how it automates the end-to-end workflow across & beyond the production floor.
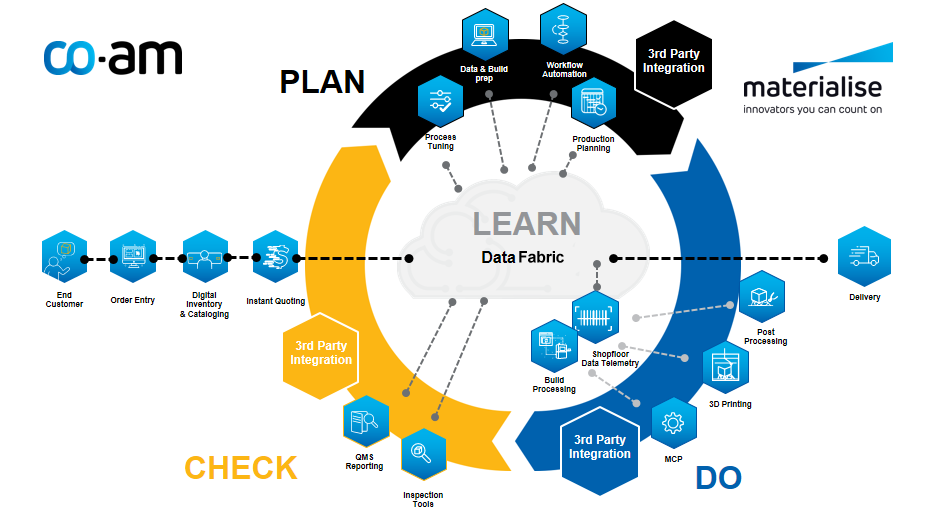
Another one that I can’t help but mention is Materialise CO-AM platform – built on LINK3D’s acquisition. With more and more partners that join the open access platform, Materialise truly provides seamless access to a full range of software tools for planning, optimising and monitoring every step of their 3D printing process.
At the design and simulation level exclusively, I didn’t have the opportunity to approach them yet, but I have heard good things about 1000 Kelvin GmbH, a start-up that delivers an AI-powered all-in-one solution. We will probably keep them in our radar next year.
Digital Twin (DT) is another one of those ingredients. A few companies may stand out from the crowd here, but my biggest takeaway for this year is the fact that post-processing solutions manufacturers (e.g. Solukon) have started improving their software solutions with this technology. Another key takeaway that will probably constitute a key trend for next year as well, is CFD powered by DT. With Flow Science for instance, we saw that computational fluid dynamics (CFD) solution powered by DT helps to address the need to test several designs quickly and efficiently before choosing one to build on an additive manufacturing system, or even the need to test the integration of the full design by connecting the simulation software to hardware. Speed and accuracy are also two other advantages of this type of software as they enable high-order numerics, scale-resolving simulations and hardware acceleration.
 A major milestone in terms of sustainability has been achieved by software companies that have developed “Product Carbon Footprint Calculator” tools for 3D printed parts. Two companies that are ahead of the curve here, are Siemens Digital Industries Software & CASTOR.
That being said, software is a big world that remains very platform-dependent – whether we talk about manufacturing processes or post-processing processes.
Manufacturing processes: a need for dedicated processes
Speed has always been the number one technological challenge to address in the development of industrial 3D printers – especially for industries driven by mass serial production – followed by materials. This year, speed has remained one of the top challenges to address in the development of 3D printers but sometimes, the need to address it was driven by a bigger vision.
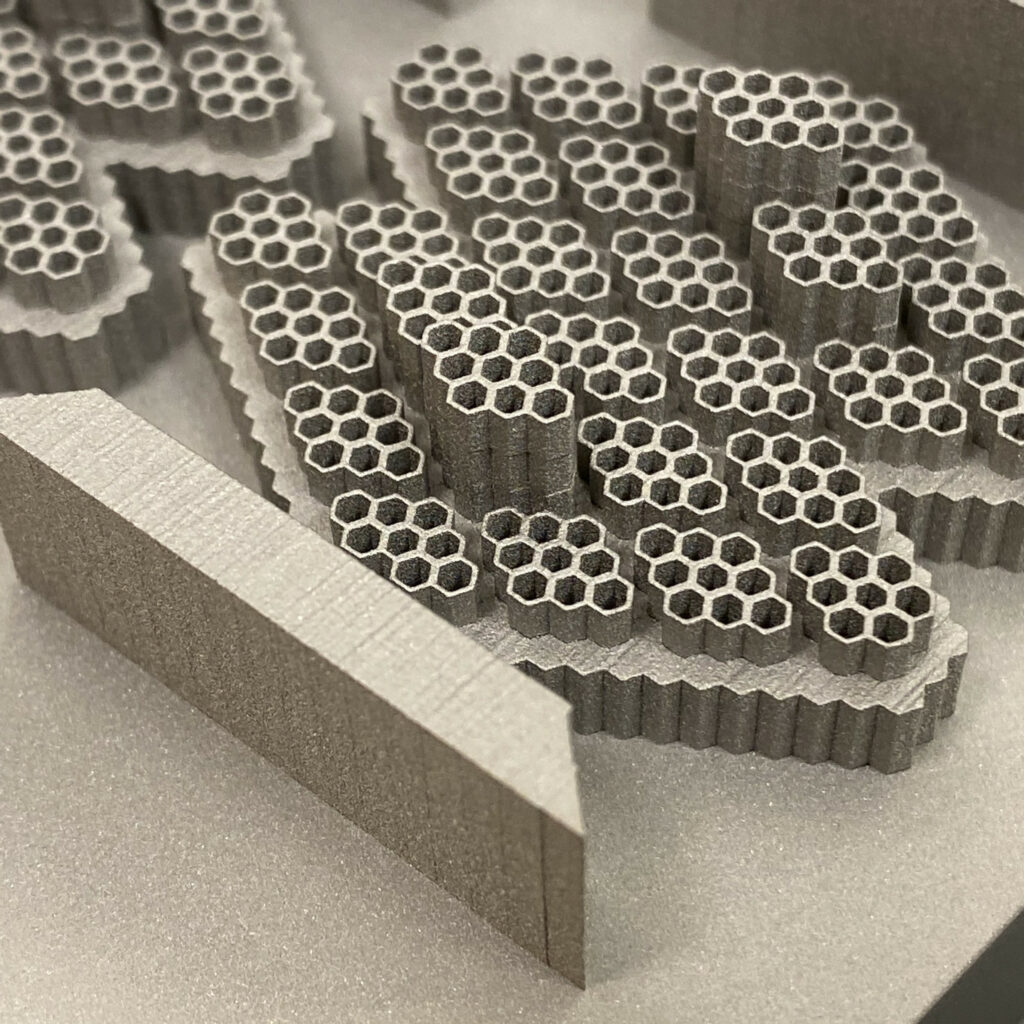
 On the metal AM side, I have had good feelings for Seurat, a US-start-up that started with the goal of improving speed of LPBF machines and over the road, became driven by the need to solve the energy problem. To migrate away from casting processes, which produce emissions equivalent to one barrel of oil per ton of metal, the strength of Seurat’s Area Printing technology in a high-powered laser. The process would split a single, powerful laser beam into up to 2.3 million separate beams and each of the 30kW laser’s pixels can be programmed to either block or let light through. Each of these pixels thereafter helps to define a laser spot by welding metal powder.
Furthermore, Seurat’s example highlights one key aspect that has been common to 3D printers’ developments observed this year: laser – While lasers remain one of the most expensive part in a 3D printer – and the most effective energy source in additive manufacturing, the challenge for OEMs has been, is likely to be, and is the exploration of new forms of laser for their machines.
As part of a collaboration with Blue laser developer NUBURU for instance, machine manufacturer ESSENTIUM will leverage NUBURU’s blue laser which would enable printing with 10x the build speed and the ability to print with a very high metal density without any post processes.
On another note, just as more materials (still) need to be qualified for use on AM machines, one should acknowledge the importance of new 3D printing processes that stand out from the crowd, and that are developed to process exotic, and sometimes more challenging materials. One of the first examples that come to my mind right now is “Goliath” a large-format 3D printer developed by Teu2tec GmbH and that enables printing of objects from any type of granules using the paste extrusion modelling process (PEM). Other examples that are worth mentioning, include silicone 3D printers – a type of printer that I thought, was no longer of interest to the market – but Lynxter and Spectoplast proved otherwise. And before I forget, FDM 3D printing is still on fire, since companies like DUPLEX debuted on the market with multi-directional printing and RAISE3D introduced a toolkit which could be the much sought-after solution to that speed problem.
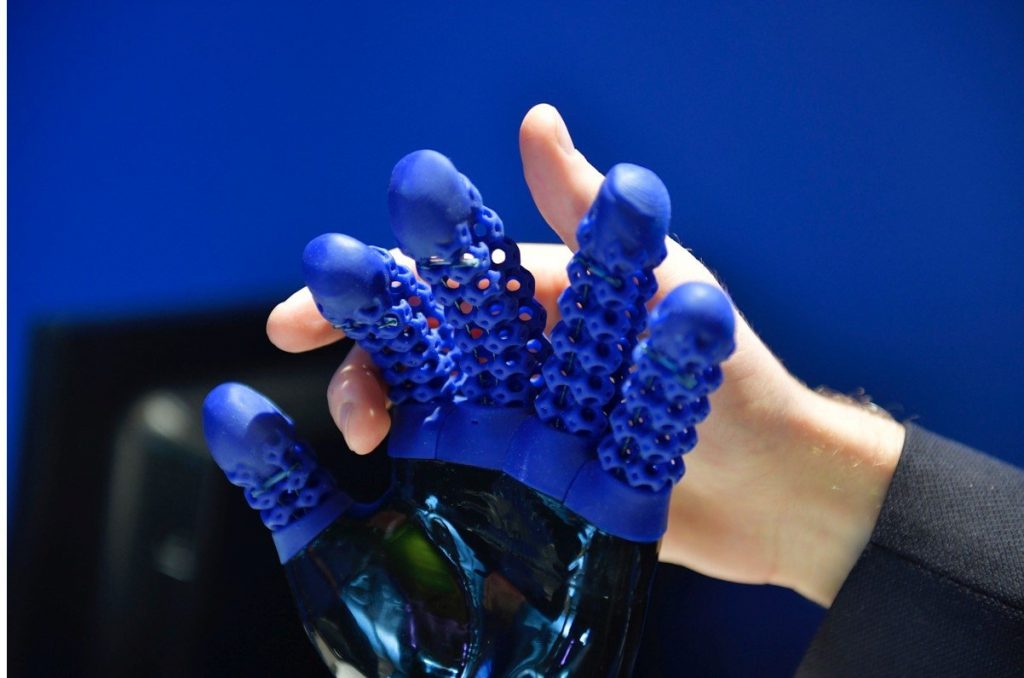
Post-processing: Quality Assurance and CT Scanning are and may be the next area of focus
We have clearly passed the stage where we had to inform, educate about the fact that post-processing is the most complicated task to perform because it was not automated, resulting therefore in a price increase of the final part; and long lead times.
Whether we are talking about powder removal, support removal, machining or any other post-processing solution, we are at a stage where users want more options – fancy, useful, more sophisticated – and they want to know how they can add value to their process. In any case, this has clearly been one of the trends observed in solutions introduced to the market this year – all solutions combined.
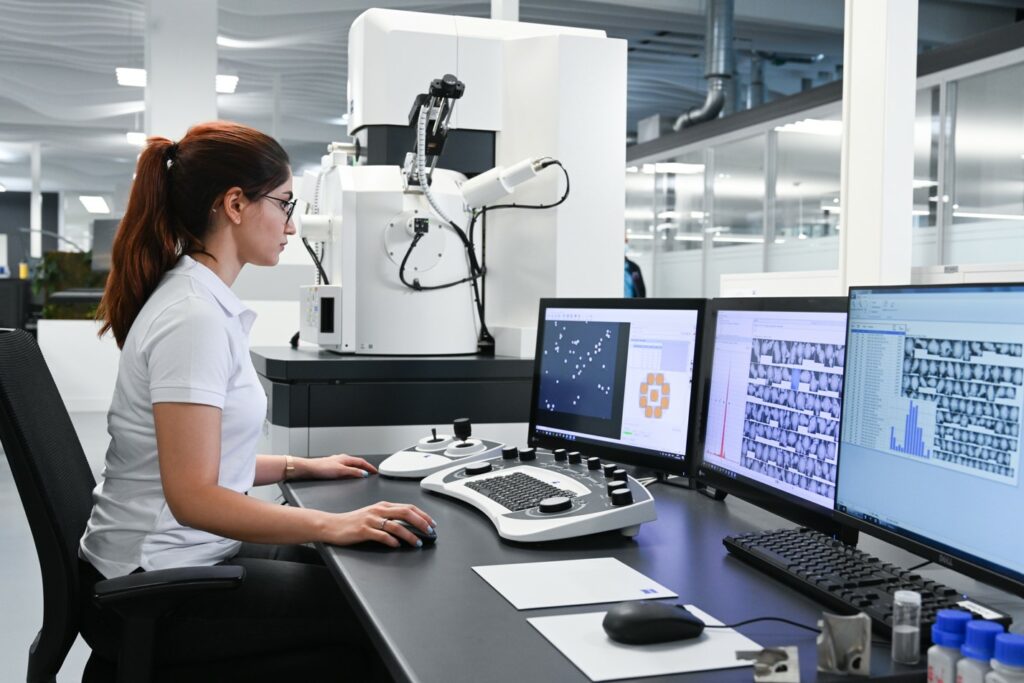
Amid the wide range of solutions developed and improved for the post-processing stage, I have to say that Quality Assurance (including CT Scanning) solutions stand out from the crowd and will probably continue to do so in 2023. The companies I would certainly be tracking here, include ZEISS, Sigma Additive Solutions and Lumafield.
On another note, the recent Formnext revealed that – whether they are used with post-processing solutions or manufacturing processes, the upcoming months or years will probably see a lot more of AM-dedicated developments compatible with robotic systems.
3.   Standards and vertical industries adopting AM technologies
 It is no secret that the growth of industries, technologies or processes emerge and grow along with the need for standardization – which helps ensure safety, reliability, and repeatability. Whether driven by regulators, standards bodies or the industry itself, this year saw an “emergence of an assurance culture in AM” that will definitely help build confidence across the value chain. This has been marked by the growing number of standards-developing organizations and classification bodies as well as the development of new standards for specific industries.
A few examples have been seen with the American Petroleum Institute (API) – an organization that represents all segments of America’s natural gas and oil industry – releasing two standards this year, namely the API Standard 20S, Additively Manufactured Metallic Components for Use in the Petroleum and Natural Gas Industries, and the API Standard 20T, Additively Manufactured Polymer-Based Components for Use in the Petroleum and Natural Gas Industries, the new standards reflect the industry’s incorporation of new technologies and innovations to improve operations.
Lastly, as I said before, whether we talk about technology advances at the machines level, at the software, materials or depowdering levels, enabling applications through all of these processes is the example that demonstrates they perfectly work together. It’s a virtuous circle. And amid the vertical industries adopting AM technologies, the aerospace & space industries remain the key verticals that have driven this market with new complex and fascinating applications and with the emergence of new companies that penetrate the market with AM as a key enabler of their operations. However, two other industries that leverage AM on their own way continue to expand: construction 3D printing and 3D bioprinting. While a lot of professionals remain cautious, those verticals saw a growing number of applications and developments – e.g. this 3D printed human lung scaffold in 3D bioprinting and new materials in construction 3D printing – , thus opening up a myriad of possibilities people are probably not ready to explore.
So…
Coming from a year of recovery, I have to say that 2022 did not disappoint me. There was a lot to see and discover, a lot to learn and obviously a lot I didn’t mention, but that’s fine because I have come to realize that until AM gets more mature, this industry will always make you feel this way: sometimes bored, which is good as it shows there is a certain steadiness, but most of the time, hungry for more.
This article has first been published in the 2022 November/December edition of 3D ADEPT Mag.