Industrials have spent the last twenty years singing the praises of additive manufacturing but reality shows that if there is one thing that truly enables to appreciate the benefits and the results of this technology, it is post-processing. The only thing is that post-processing is a complex, confusing and sometimes disturbing stage of the manufacturing process.
Post-processing is an umbrella term that covers a variety of stages that 3D printed parts have to undergo before being used for the final purpose. No matter what post-processing stage the AM part needs to go through, the goal remains the same: removing the undesired properties that have been built-in the final product during the additive manufacturing process.
Furthermore, as the name suggests, it takes place at the end of the manufacturing process, and the type of post-processing actions leveraged as well as the amount of work at this stage of the manufacturing depends on many variables including applications.
Post-processing jobs might, therefore, include and are not limited to Heat Treatment, UV Curing, Support Removal, Cleaning & Depowdering, Machining, Coating or Infiltration, Surface Finish Processes, Inspection and Dyeing.
This dossier aims at giving industrials key insights into post-processing, its different segments and its importance in AM serial production. To address this issue, AMT’s CEO, Joseph Crabtree and Manuel Laux, Head of AM Solutions will mainly take the floor to share their opinion on several key points. We also thank FIT AG, Solukon, Protolabs and Girbau, for the examples provided.
A post-processing stage can bring many improvements such as better aesthetics, geometric accuracy, mechanical functionalities and properties, desired surface characteristics, to name a few. However, to get the product in its “ready-to-use” form, operators face two main challenges:
- The first one is that a large proportion of the tasks carried out after the printing process are manual.
According to AMT’s CEO, Joseph Crabtree, “currently, up to sixty percent of the manufacturing costs of a 3D printed part are attributed to the highly manual steps of post-processing, the part after it has been printed. By automating the post-processing workflow, manufacturers will reduce costs by producing end-use parts with a technology that is reliable, repeatable, and reproducible.”
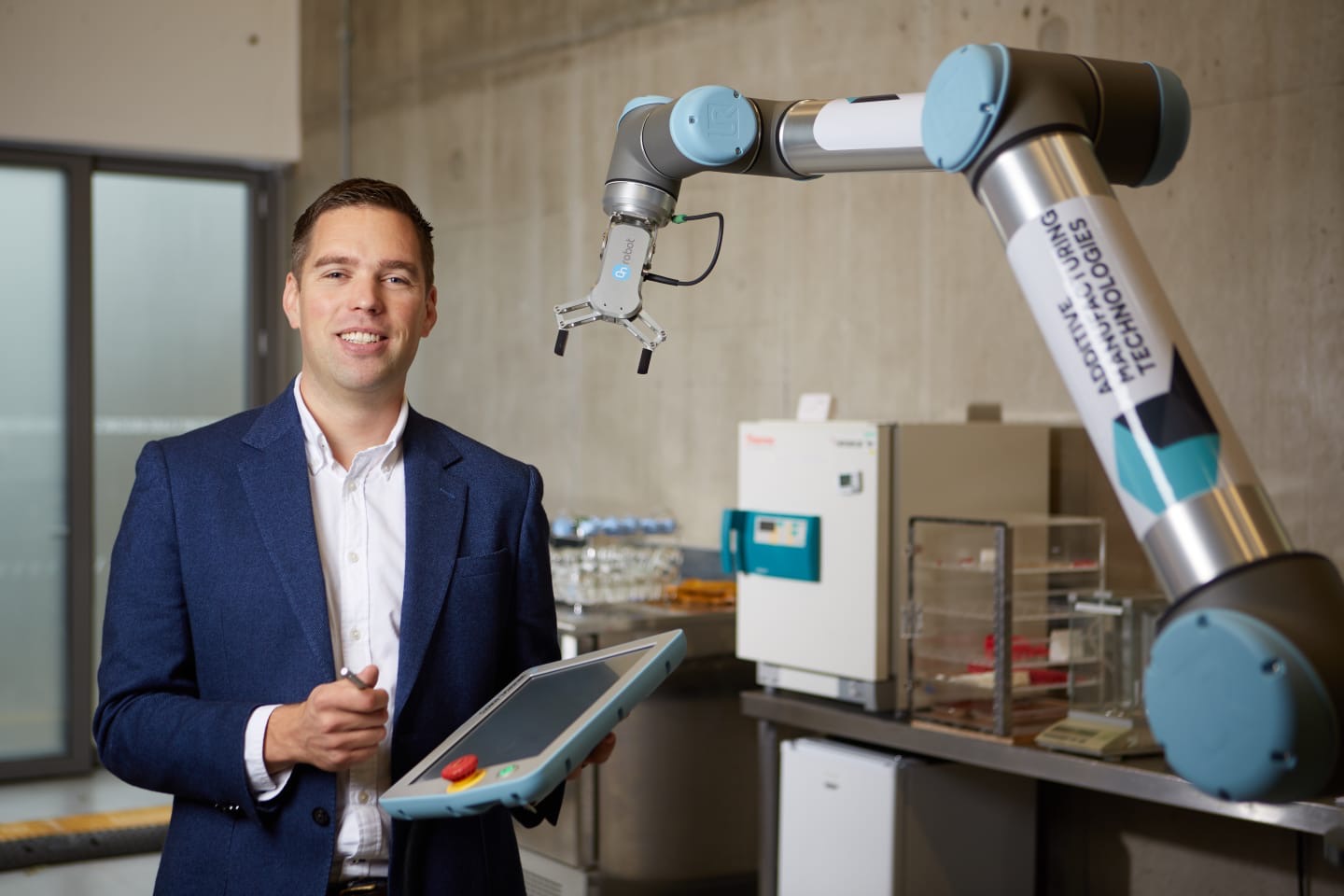
– The second issue is that be it resin, filament or metal, each AM process poses its challenges when it comes to post-processing. In this case, operators should first know the desired results they expect their part to have in order to determine the post-processing step that best suits their project. Furthermore, some post-processing tasks are mandatory for certain applications, others are not.
“Apart from powder-based SLS, HP MJF and binder jetting techniques for plastic components practically all 3D printing systems require support structures for components with overhangs. As part of the post processing process, these support structures must be removed. Also, depending on the printing method, residual resin and powder must be removed. And, finally, the surface of the printed components must be refined by edge radiusing, surface smoothing and, frequently, polishing. On average the removal processes (support structure, resin, powder) and surface finishing account for about 75% of the post-processing work. Other post-processing activities may involve vacuum drying and dyeing of the printed components.
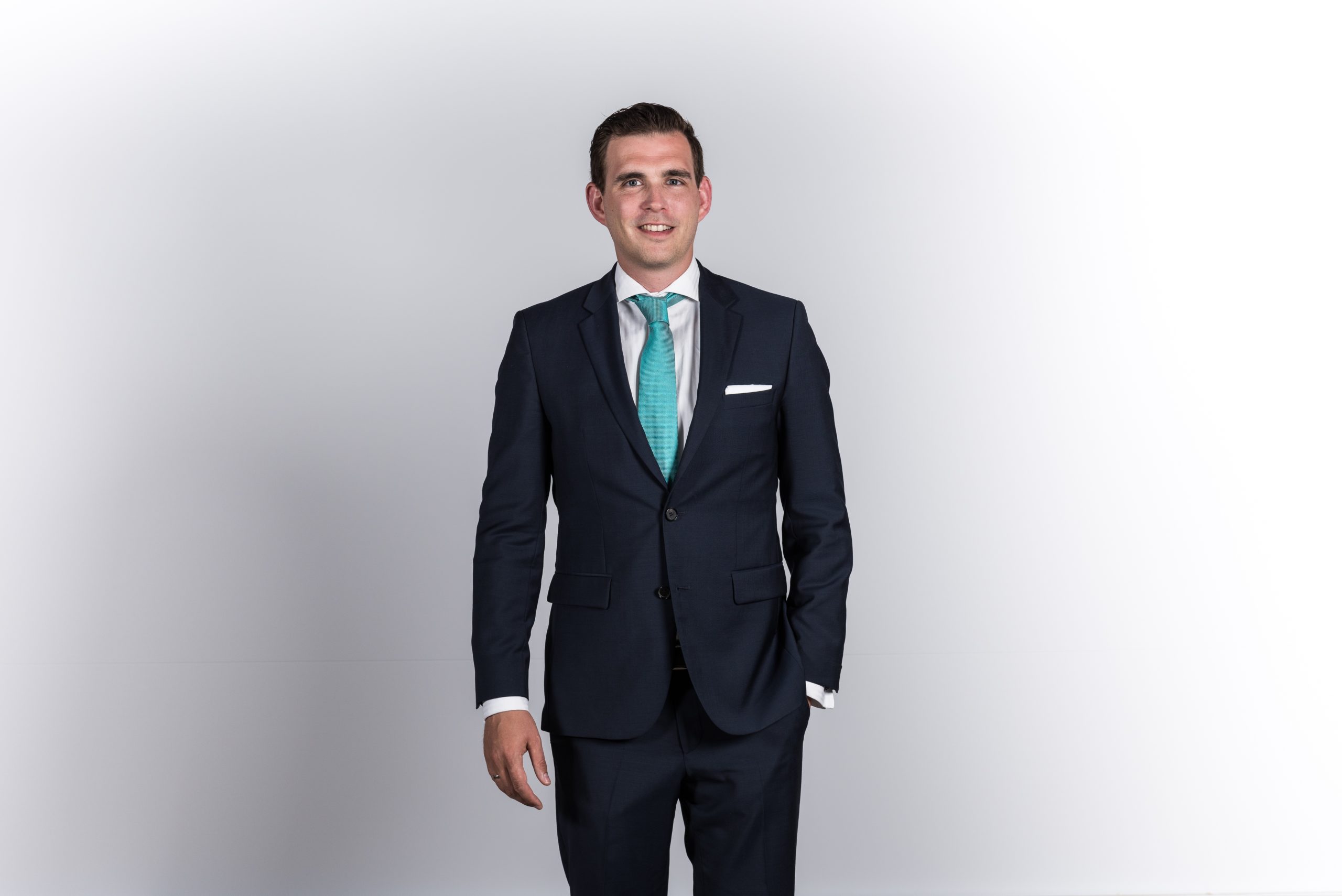
To be cost-effective, these jobs can no longer be handled by manual labour like pliers or old-fashioned immersion tanks for support removal, or hand sanding. This is too time-consuming, produces inconsistent results and is too costly. Preferably, the manual labor and traditional tanks must be completely replaced by fully automated chemical and mechanical systems”, explains Manuel Laux, Head of AM Solutions.
A look at the various post-processing steps
1- Heat Treatment
Several Additively Manufactured metal parts require a heat-treatment solution with precise temperature uniformity. This ensures the printed parts adhere to the metallurgical properties of the selected metal alloy. To avoid major distortion, metal 3D printed parts are usually stress relieved together with the build platform and heat-treated after being cut off from the build platform. This solution is often selected by companies because of the complexity of materials used in the AM process. For aerospace and medical applications, for instance, the AM process has to comply with very strict rules, therefore the benefits of heat treatment lie in its ability to reduce surface contamination and to maximize mechanical properties.
High-Pressure Heat Treatment (HPHT) is a new form of technology used for the consolidation and densification of metal, ceramic, and plastic parts. According to contract manufacturer FIT AG, typical pressures of 15,000 – 30,000 psi, temperatures of up to 4,000 °F, as well as cooling rates of up to 4,500 K/min allow for a maximum theoretical density, ductility, and fatigue resistance of high-performance materials.

2- UV Curing
This post-processing step is usually compatible with components that have been produced with photopolymerisation processes/resin 3D printing technologies such as Carbon’s Continuous Liquid Interface Production (CLIP™), and SLA. Components are exposed to UV light to fully cure to improve the physical quality of the part and enhance the aesthetic characteristics.
3- Support removal
Support removal is necessary with parts that have been produced with resin or filament 3D Printing technology. Put simply, 3D printed components are usually attached to the build plates by scaffolding and support structures which enable the creation of overhanging structures, therefore reduce the degree of warping. These support structures can be made from soluble and insoluble materials. If the material is insoluble, then several accessories can be used (blades) to remove these support structures. However, a soluble support material offers a lower risk of damaging the model as the support structures can be dissolved in water or with a chemical called Limonene. Furthermore, those who would like to reduce the manual work can opt for a more automated solution. PostProcess Technologies, for instance, a partner of AM Solutions, provides various solutions that meet the requirements of these different AM technologies: “With the “Submersed Vortex Cavitation (SVC)” technology the PostProcess systems DEMI and FORTI reliably remove supports and excess resin. For support removal of products made from filaments (FDM/FFF) PostProcess offers the DECI and BASE units using the “Volumetric Velocity Dispersion (VVD)” process”, states Manuel Laux.
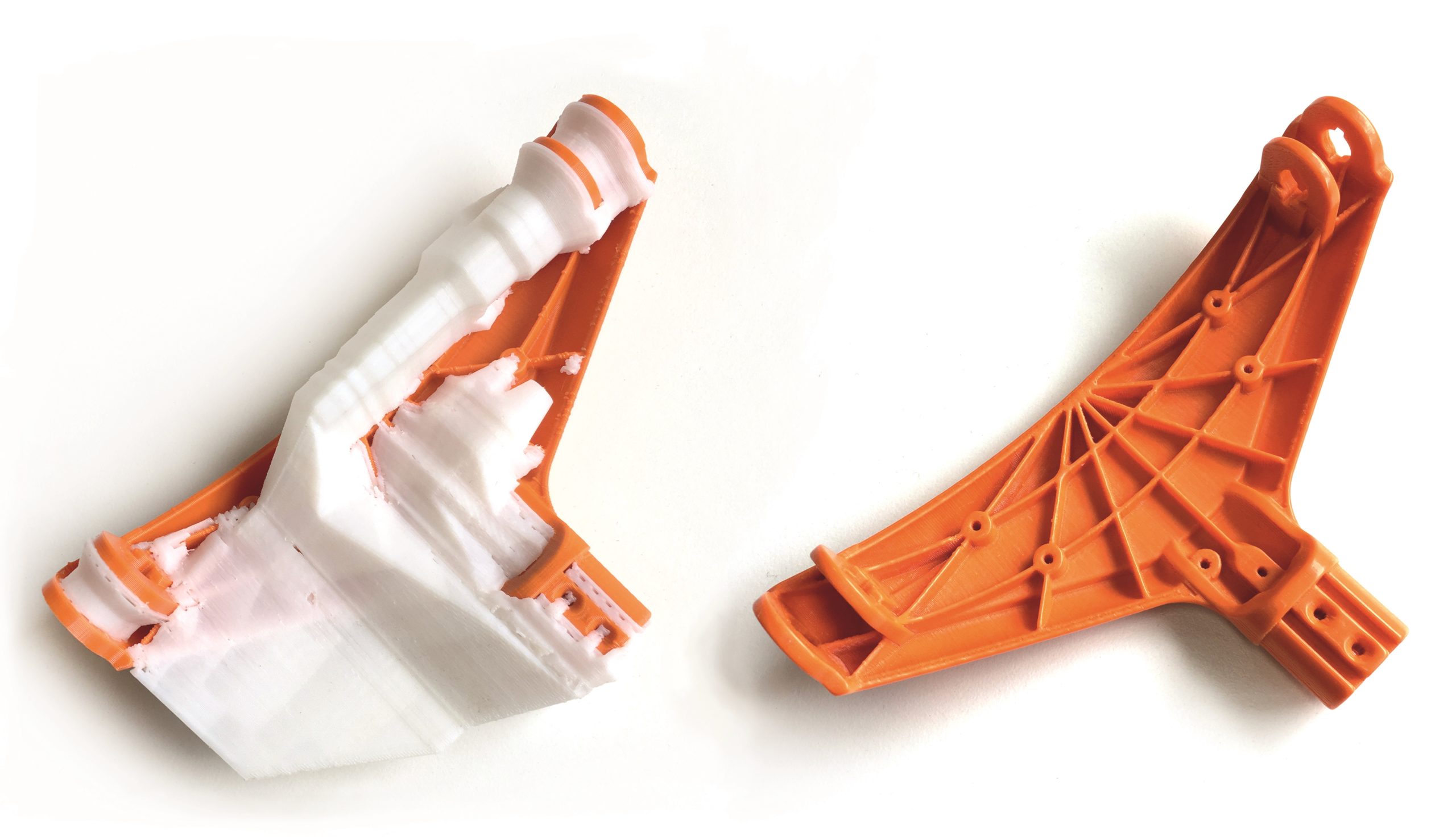
4- Cleaning & depowdering
The term “depowdering” is often used interchangeably with “cleaning”. However, if cleaning can refer to the ability to remove support structures for FDM, resin or material jetting technologies, depowdering remains the most explicit word to outline the ability to remove residues of powder that remain in AM parts.
Depowdering” comes into play when components have been produced with powder-based metal additive manufacturing technologies. It is the first step and current bottleneck of the post-processing chain after the printing process. A wide range of other post-processing steps are often required after this task, that’s why some experts prefer to call this stage “pre-processing”.
Let’s take the example of a complex part produced on a Powder-Bed Fusion system. Depowdering this part will usually require a brush and vacuum cleaner. Thereafter, this part will have to be destressed, sawed-off and tumbled. Depending on the application, further tasks such as CNC and precipitation hardening can be performed. The reflection cost put asunder; these manual processes might take several days before getting the desired end-result. To remedy this situation, some machine manufacturers integrate post-processing steps into their AM systems, other manufacturers and AM users who already have a fleet of AM systems simply opt for an automated powder removal solution.
“A unique trait about AMT’s automated post-processing solutions is that all AMT’s technologies are safe and sustainable, and specifically designed for additive manufacturing, unlike other post-processing technologies on the market. Both AMT’s depowdering, PostProDP, and surface finishing, PostPro3D, technology gently finish parts on an industrial scale. Not only do AMT’s technologies improve the parts aesthetics, they also improve the part’s mechanical properties, such as elongation at break (EAB), and eliminate water and gas intake. Using smart algorithms and machine learning, AMT’s technologies are equipped with programmed recipes for each common material combination, therefore offering a truly plug and play solution”, Crabtree told 3D ADEPT Media.
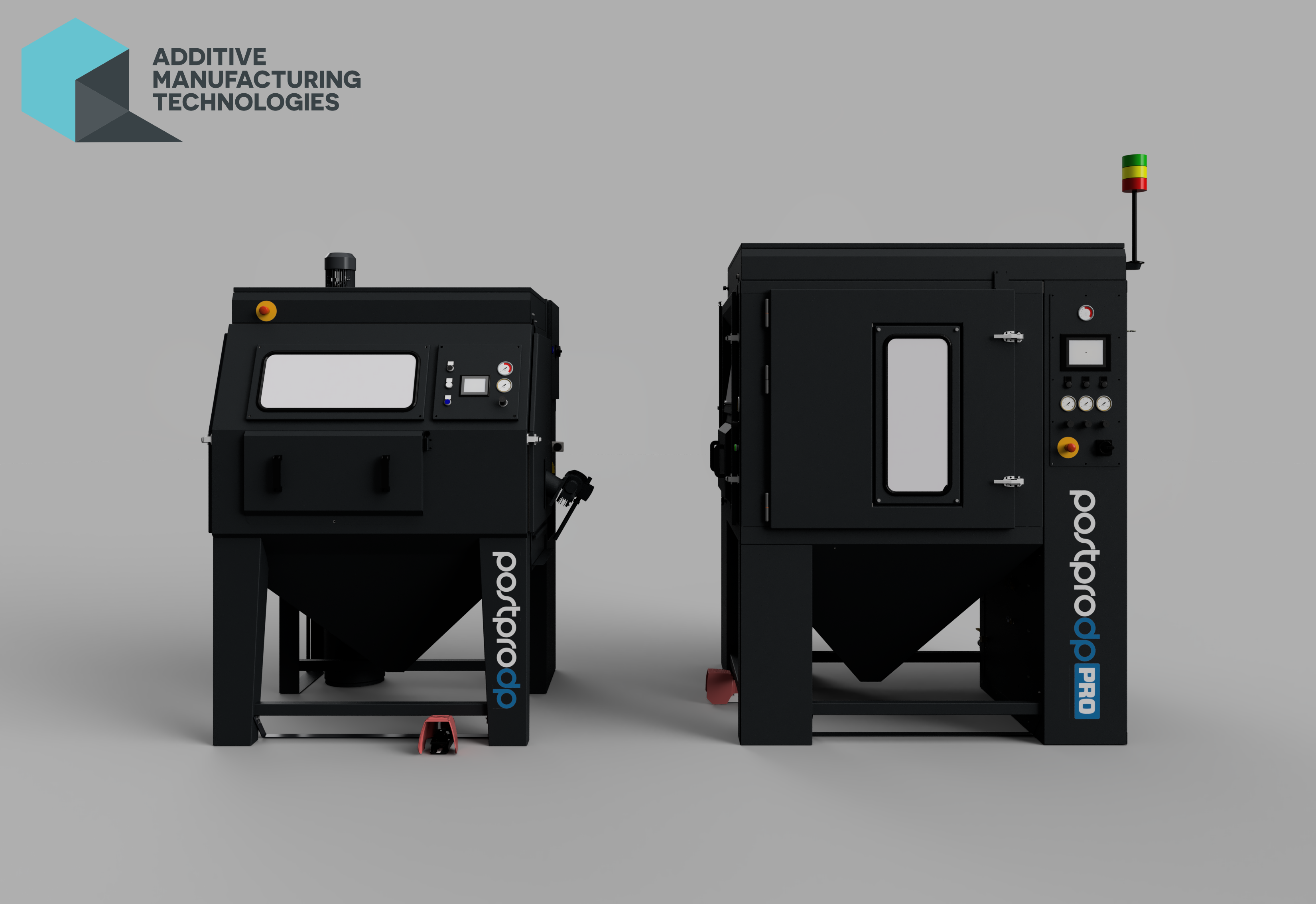
Another manufacturer that also stands out from the crowd is Solukon. To address issues related to the complexity of parts with channels and voids that retain powder, Solukon has developed a series of automated and programmable depowdering machines that remove powder from finished 3D printed metal parts. German company systems do not only rotate and vibrate in spatial direction to remove the remaining powder, but they also ensure a high degree of protection from hazardous dust build-up, and inert gas infusion to prevent an explosive atmosphere.
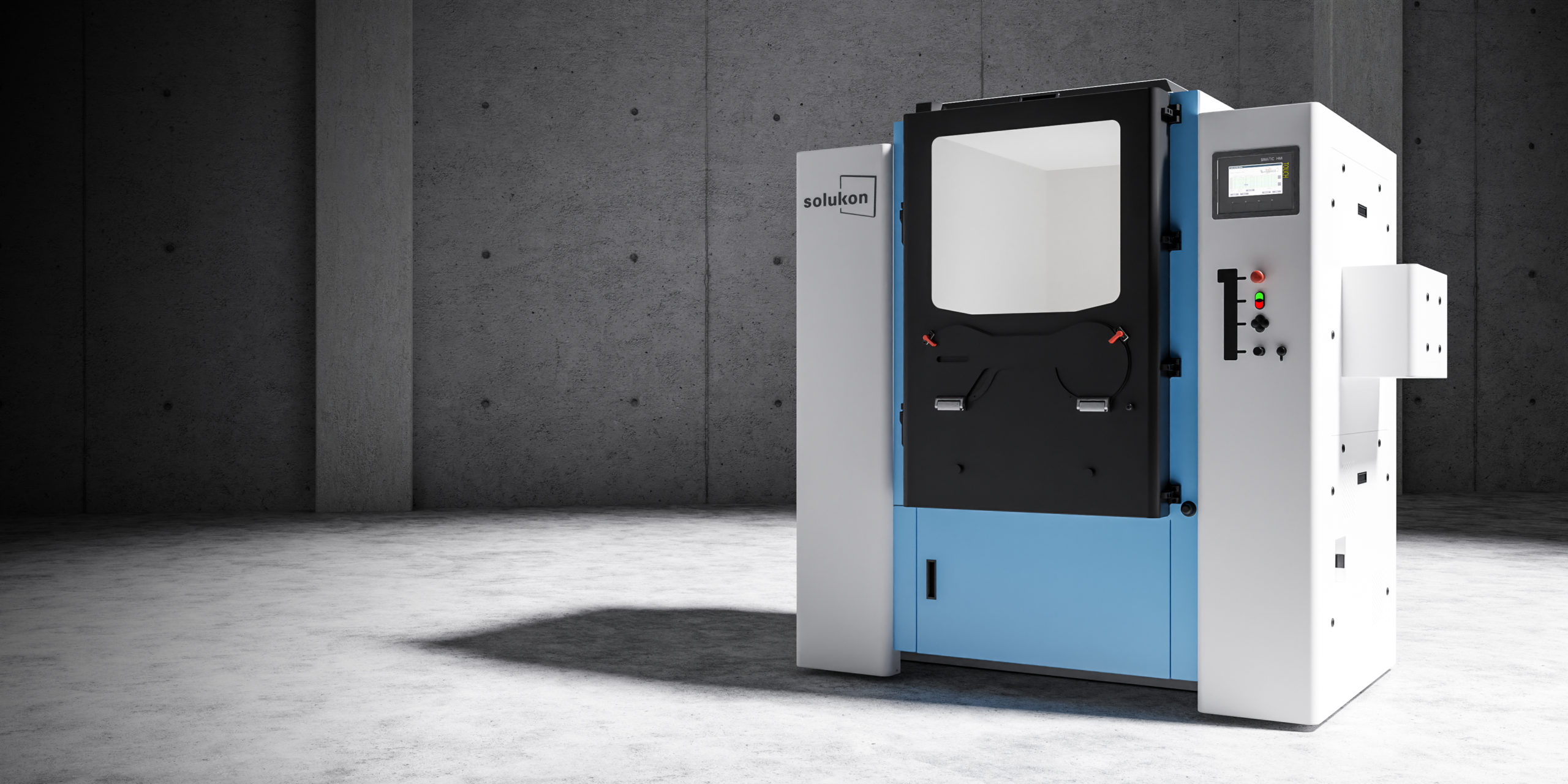
5- Surface finish processes
Depending on the application, 3D printed components may require a further surface refinement by edge radiusing, surface smoothing and, possibly, polishing.
In a surface refinement process that combines blasting and finishing systems, Laux from Head of AM Solutions explains: “the initial surface of 3D printed parts can sometimes be quite rough with Ra readings of up to 1,000 micro inches. In such cases, it can be beneficial running the workpieces through a blasting process for an initial reduction of the surface roughness before processing them in the actual finishing system. This allows reducing the Ra values down to < 20 micro inches.”
If the operator is looking for extra smooth surfaces on metal components, AM Solutions can offer a “finishing system producing extremely fine surface finishes with Ra values of < 5 micro inches on 3D printed metal components. This is achieved with the patented DRYLITE® dry electro-polishing technology, which does not require any liquid electrolytes.”
Moreover, the term finishing designates a range of post-processing activities such as priming, filling, grinding, preparing ready for painting, deburring, etc. They are generally used as the basis for further post-processing, such as metal coating.
6- Machining
Parts may require additional machining to remove further support structures. This post-processing task can be done after almost any AM processes. It is required for metal processes that do not deliver geometries close to the final contour.
7- Coating or Infiltration
Coating consists of the infiltration of microporous components with polymers. The goal of this activity is to produce components that are completely gas-tight or liquid-tight.
8- Dyeing
If the visual appearance of your powder-based polymer parts needs to be improved, then you probably need a dyeing post-processing step. Dyeing can be performed, either manually in pots of hot water or using automated dyeing equipment. This post-processing technique is mostly leveraged by HP MJF users. The results are most visible on parts that are subject to wear (glasses for instance), as the color penetrates the surface of the part. Girbau, for instance, is one of the specialists of the dyeing equipment industry that designed its equipment for HP MJF.
9- Inspection
This post-processing step allows for the validation of a part’s dimensional accuracy and mechanical properties. It is usually seen as a benefit in on-demand manufacturing situations. One Industrial manufacturing services supplier that integrates detailed measurement and inspection reporting services to its offering is Protolabs. The company explained that the “inspection process verifies that final parts comply with the original drawing, purchase order, and other specifications. Dimensional inspection uses CMM equipment to ensure part dimensions are within tolerance and align with measurements provided in the original drawing.
Final report details location on the build plate, how the geometry was oriented, support structure placement, and a build log file detailing the entire build process from the machine.”
Taking the example of parts that have been manufactured through Direct Metal Laser Sintering (DMLS), the manufacturer of parts explains that computed tomography (CT) scanning is often the ideal inspection method for these parts. Indeed, it offers a non-destructive means to part validation. According to Protolabs, the process can be used to inspect and validate hollowed-out features or internal channels. It can measure any variances in wall thickness, or detect warping and cracking. Lastly, it can verify that no residual powder remains within the part.
Can the same post-processing technology be compatible with several types of additive manufacturing technologies?
First, it should be noted that specialists of post-processing technologies usually develop their solutions to respond to specific demand of the additive manufacturing industry. Over time, applications tend to extend their area of expertise to other technologies.
Moreover, choosing among the array of AM technologies the ideal process for one’s project is quite complicated. However, despite the numerous aforementioned post-processing techniques, the choice can quickly be made for a post-processing solution.
“A small number of post processing equipment, be it for removal of supports and residual resin, de-powdering & cleaning or surface finishing, can be used for whole groups of additive manufacturing technologies. For example, for de-powdering, cleaning and initial surface smoothing the AM Solutions S-Line equipment can be used for plastic components and in terms of metal for initial surface smoothing.
When it comes to surface finishing of the same plastic or metal components the AM Solutions M-Line equipment line is suitable”, says AM Solutions’ Manuel Laux.
Furthermore, experience in various applications might easily enable operators to determine the ideal post-processing technique for their project.
In tooling applications, for instance, the texture of parts at the end of the printing process is similar to corduroy. That’s why those parts need to be machined after the printing and cooling processes.
Lastly, similarities and disparities between additive manufacturing technologies must absolutely be taken into account. Binder jetting, for instance, presents postprocessing requirements similar to Fused filament fabrication (FFF). Metal FFF parts, on the other hand, might require further investments in post-processing. Indeed, with this AM technology, the raw material is made up of a filament with a plastic or wax binder heavily loaded with metal powder. The binder must be removed once the part is right out of the machine. Thereafter follow a debinding with heat or an acid bath and a sintering step.
“It’s not just about making parts look good, it’s about improving the mechanical properties of the parts for high performance.”
Additive manufacturing itself has proven its capability to cut down production times to just a few days. However, its viability for volume and serial production is not yet unanimous.
For AM Solutions, “to a large extent, this is due to laborious post processing methods characterized by a preponderance of manual labour, use of old-style methods and lack of automation. The outcome is extremely time-consuming post-processing, inconsistent results with low throughput and very costly. Only with automated, intelligent post-processing solutions can additive manufacturing be truly integrated into industrial production lines. But automated post-processing will achieve a lot more: It will allow full usage of the printer capacities resulting in significantly reduced cycle times, an overall higher throughput and a drastically improved cost-efficiency. It will produce a consistently high quality of the post-processed components, thus significantly reducing the reject rate (less warpage & swelling due to water absorption, less breakage, etc.).
Welcome side effects of integrating automated post-processing treatments are lower work-in-process inventories, better workpiece traceability and higher workplace safety (manual de-powdering can be hazardous).”
“To scale post-processing safely and sustainably, new technology development and automation are key. It’s not just about making parts look good, it’s about improving the mechanical properties of the parts for high performance”, adds AMT.
Collaborations between 3D printer manufacturers and post-processing systems suppliers on the one hand, as well as collaborations between AM users and post-processing specialists, will certainly foster the integration of more automated postprocessing solutions in AM productions, but understanding these concerns, and disparities is a crucial key to serial production.