When we started discussing what a renewable energy transition with Additive Manufacturing (AM) looks like, a key focus was unconsciously placed on the role of metal 3D printing technologies like LPBF. Interestingly, various projects have popped up this year across Europe and have demonstrated the capabilities of ceramic 3D printing as an ideal production candidate that could bring the hydrogen economy closer to effective implementation. 3DCeram demonstrates the how and the why of these capabilities through the European HyP3D project.
From a manufacturing standpoint, the role AM can play in hydrogen production has often been hard to demonstrate. In theory, the capabilities of AM in any production can easily be outlined; in practice, applications of this specific segment are not really known, making it difficult to appreciate the tangible role of the technology.
This article aims to highlight:
- The European HyP3D project and the link with hydrogen production
- How 3DCeram’s SLA 3D printing is utilized to help redefine the landscape of hydrogen production
- What does that mean for the energy industry?
The European HyP3D project and the link with hydrogen production
To date, one of the promising methods to produce green hydrogen from renewable sources would be to rely on electrolysis.
The electrolysis process consists in using electricity to split water into hydrogen and oxygen. Among the different types of electrolysis systems that can be used to enable this reaction, those based on high-temperature Solid Oxide Electrolysis Cells (SOECs) are often the most efficient ones. The problem is that their adoption is often slowed down by their stable operation at atmospheric pressure.
The European HyP3D aims to address this limitation by demonstrating the viability of a disruptive high-pressure Solid Oxide Electrolysis Cell (SOEC) technology. At the heart of the project, one finds a wide range of research and industry experts: IREC, DTU, PoliTo, and BSC as well as VAC-TRON, H2B2, SNAM and 3DCERAM on the industry side*.
To develop an ultra-compact, high-pressure standalone SOEC stack that can turn electricity into compressed hydrogen, this consortium will harness the power of several technology solutions including 3D printing. A key milestone of this research will be the development of 3D-printed SOEC cells with a substantial active area of 70 cm², embedded functionalities, and the capacity to achieve hydrogen production at remarkably high current densities exceeding 0.90A/cm² (~1.3V) under conditions of 850ºC and 5+ bar pressure.
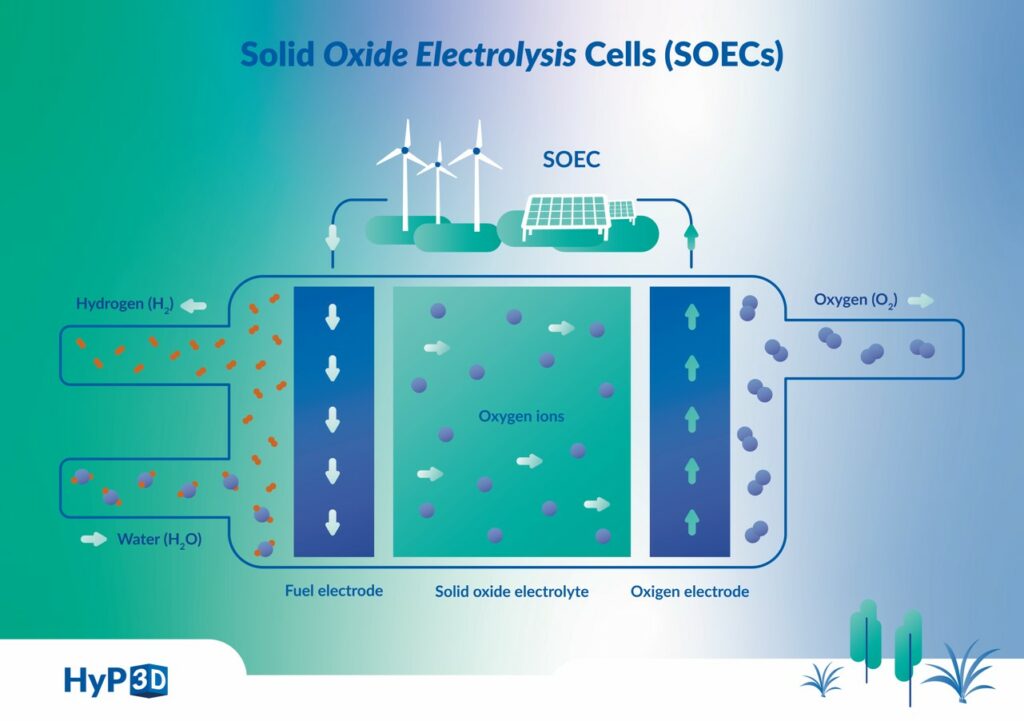
So, how exactly is 3D printing used at this level?
How 3DCeram’s SLA 3D printing is utilized to help redefine the landscape of hydrogen production
Founded in 2001, by Richard GAIGNON and Christophe Chaput, 3DCeram has built up extensive expertise in the manufacturing of ceramic 3D printers based on SLA technology. Over time, the company’s offering has evolved to support customers throughout the entire value chain
“When it comes to industrialization, stereolithography becomes a significant asset as it is a top-down construction process. This means that the layers are built from the bottom to the top, foregoing the use of many supports. This is a crucial point to consider. After printing, the parts are cleaned, and the fewer supports there are, the easier and faster the operation becomes, while also reducing the risks of waste due to possible breakage during support removal,” the company says.
As part of this project, 3DCeram’s role will be to define and implement the application scenario established at the research level. This means developing an intricate optimization process encompassing printable feedstock Zr8Y, 3D printing parameters, and thermal treatments.
To achieve their ultimate goal – producing complex-shaped parts mirroring the final cell dimensions – the team will go through a number of different steps: from designing optimal procedures to studying the rheological behavior and printing tests by formulating specialized slurries for SLA 3D printing utilizing commercial YSZ powders.
The production will rely on the company’s C1000 FLEXMATIC 3D printer which aims to drive automation throughout the process.
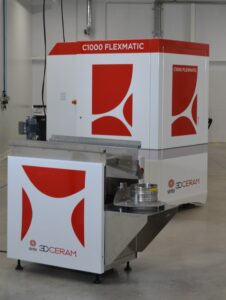
This semi-automatic production line features a 320*320 mm build platform that aligns with the project’s industrial ambitions. Unveiled last year, the 3D printer has been designed with two laser options that could meet different production needs. Its automation capacity ensures the recycling phase of the uncured material as well as the cleaning phase of the parts and the trays. The printing process enables us to save time as the 3D printed parts require little or no support.
Why is 3DCeram’s SLA 3D printing the ideal production candidate for the project?
To better understand the capabilities 3DCeram’s technology is bringing to the table, it’s important to keep in mind that these parts are still manufactured through conventional manufacturing techniques such as tape casting. The challenges of this manufacturing process are the difficulty of ensuring the rheological properties of green tape slurries that will enable electrolyte performance. Added to this is the fact that the manufacturing process produces a flat, non-functionalized cell, so one ends up with a process that is not always ideal for production.
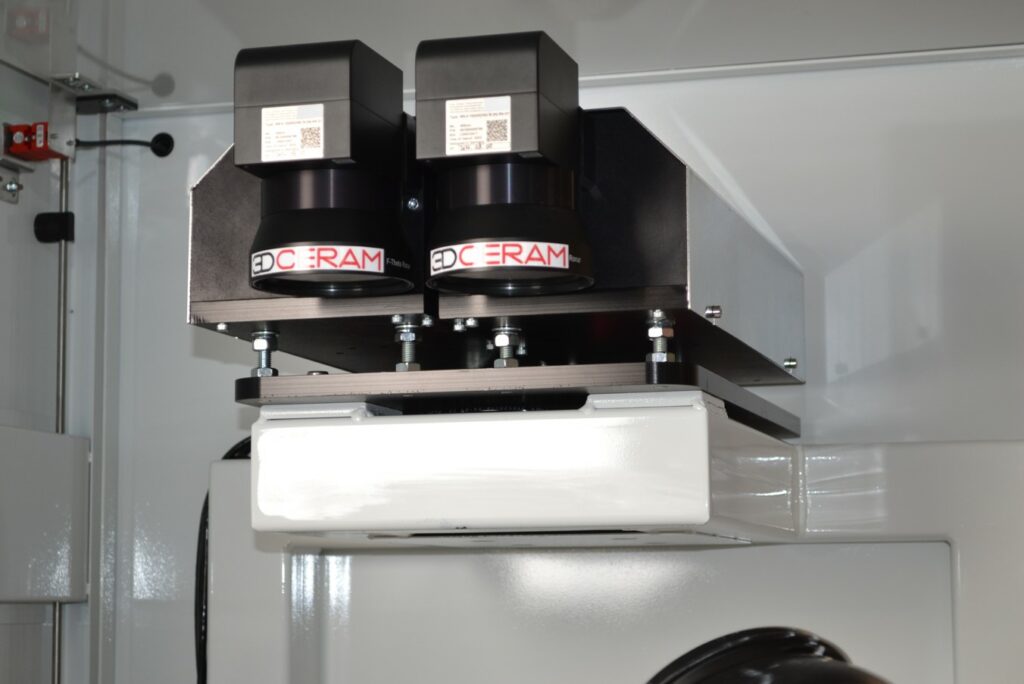
On the contrary, SLA 3D printing provides the cell with a complex geometry that allows the surface shape to be changed and adds gas paths to optimize the parts where it is needed.
3DCeram reports that the 3D printed ultra-high-power density SOEC stacks deliver a 2.14kW power output within a compact 630 cm3 volume. This translates to a threefold rise in specific power per unit volume to 3.4kW/, and a fourfold increase in specific power per unit mass to 1.10 kW/kg. These results currently exceed any benchmarks of the industry.
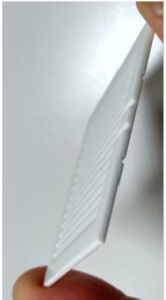
What does that mean for the energy industry?
As a key partner in the HyP3D project, 3DCeram is pushing the boundaries of its technology by demonstrating automation capabilities that will be needed for industries looking to scale production of 3D-printed SOEC cells.
At present, the company has demonstrated the potential of ceramic 3D printing for a critical sector like energy. With robots and automated production systems that can handle all stages, from design to firing of parts, 3DCeram is ready to help the energy industry scale production with its technology.
While with the C1000 FLEXMATIC 3D printer, 3DCeram already allows automation throughout the process (from scraping to lasering strategies to the quality of ready-to-print ceramic formulations to recycling and post-processing), it should be noted that the company’s production line includes 3D printers such as the C3600 ULTIMATE with bigger volumes. Our guess is that these 3D printers will also be appropriate for industrial production but that’s a topic we would be happy to discuss in another article.
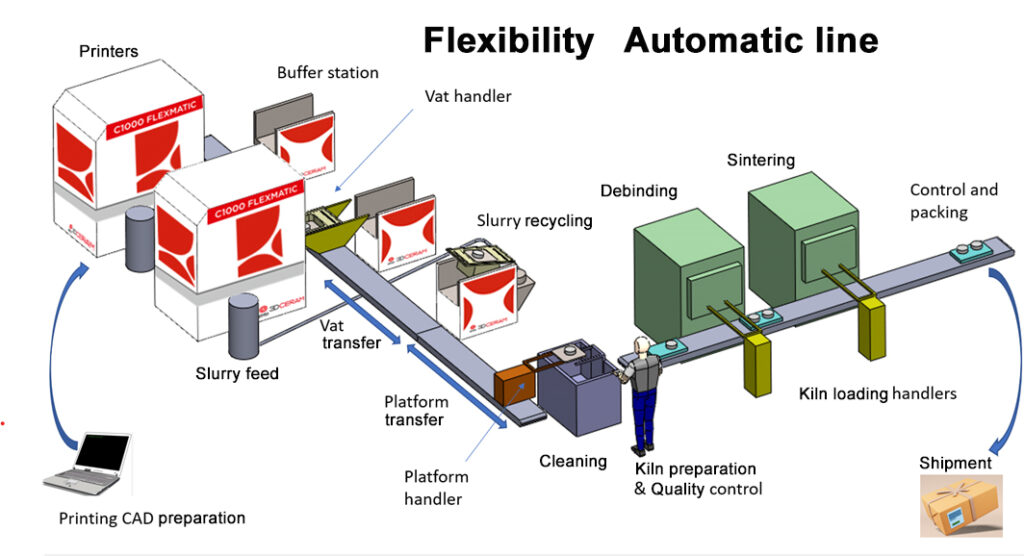
In the meantime, it’s important to keep in mind that HyP3D’s vision doesn’t stop at materializing dense, mechanically robust components. 3DCeram is currently going the extra mile to develop and model a stack for producing hydrogen. By closely working with IREC, a center of excellence in applied energy research, the company will now focus on optimal printing strategies, ensuring reliability and maximizing production yield.
If the project is successful – and it’s likely to be given promising first results –, it will help achieve the objectives of advancing the hydrogen economy, reducing time-to-market significantly, slashing raw material consumption by 76%, and minimizing the initial investment by 42% compared to conventional manufacturing processes.
“With this groundbreaking HyP3D initiative, the energy sector witnesses a convergence of 3D printing prowess and hydrogen innovation, propelling the world toward a more sustainable energy future,” 3DCeram concludes.
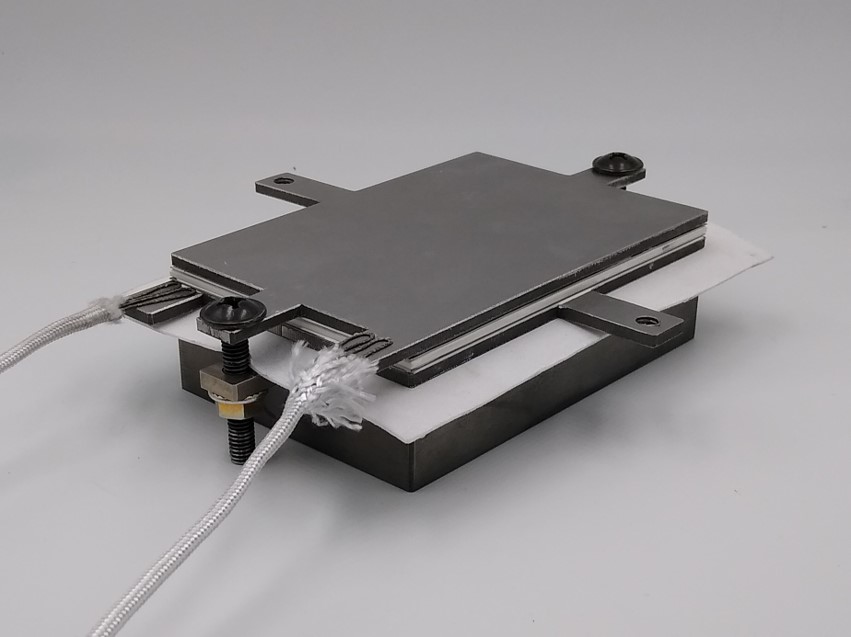
This article has first been published in the September/October edition of 3D ADEPT Mag. Co-written by Kety & Yosra. Images: 3DCeram.
*Editor’s notes:
At the heart of the project, one finds a wide range of research and industry experts: IREC, DTU, PoliTo, and BSC as well as VAC-TRON, H2B2, SNAM and 3DCERAM on the industry side. While we focus on understanding the capabilities of 3DCeram’s SLA 3D printing in this article, it should be noted that each of these partners brings valuable expertise to the project.
IREC is a centre of excellence in applied energy research. The Catalonia Institute for Energy Research (IREC) leads the HyP3D project and serves as a key coordinator. The Catalonia Institute for Energy Research (IREC), located in Barcelona, Spain, takes the helm in leading the HyP3D initiative and acts as the project’s principal coordinator. IREC holds a pivotal role in the realm of energy research. The Department of Nanoionics and Fuel Cells at IREC brings substantial proficiency in crafting and assessing solid oxide cells for both electrolysis and power generation, using cutting-edge 3D printing techniques.
DTU is a technical university in Europe with over 20 years of experience in developing and up-scaling advanced functional ceramics.
Politecnico di Torino (PoliTO) is a top-ranking university in Italy and Europe, with a focus on technical-scientific research, and a leader in materials. Their expertise will be combined to produce high pressure resistant joining for HyP3D.
The Barcelona Supercomputing (BSC) is a national institution in Spain dedicated to high-performance computing (HPC). It is managing MareNostrum, one of the most powerful supercomputers in Europe. BSC will carry out high fidelity fluido-dynamic, electro-thermo-chemical and mechanical models for HyP3D technology, in parallel with the creation of a digital twin of the HyP3D stack.
VAC-TRON is a SME specialized in glass-to-metal sealing technology for high demanding application such as aerospace and oil and gas industry, and will bring important expertise to the HyP3D project in the areas of joint design for high pressure and high temperature, also creating reliable mass-scale sealing procedures.
H2B2 is an organization specialized in hydrogen production systems utilizing water electrolysis at different levels: development, financing, design, integration, construction, operation, and maintenance. They offer end-to-end solutions for green hydrogen production, encompassing every stage of the process. They will provide HyP3D with their deep knowledge of energy efficiency and cost-reduction strategies of the designed systems. In addition, H2B2 is the owner of the manufacturing pilot line that will be used to produce HyP3D cells.
SNAM is a leading operator in natural gas transport and storage in Europe, with an infrastructure that supports the energy transition. Drawing upon its 80 years of experience in managing and developing networks and plants, Snam ensures the security of energy supply and drives the energy transition across various territories by investing in green gases, such as biomethane and hydrogen, as well as energy efficiency. SNAM will contribute to the balance of plant of the HyP3D system.