Thermwood has rolled out a new manufacturing approach that brings together its history in CNC routing and its work in large-format additive manufacturing. Named Cut Layer Additive, the new manufacturing process does not 3D print parts, yet it remains an additive process. How is it possible? The company’s CEO Ken Susnjara takes us through the how and the why of this latest development.
Thermwood, based in Dale, Indiana, is one of the first companies to develop CNC router technologies. During the past years, the company made a name for itself in the additive manufacturing world with its Large Scale Additive Manufacturing machines.
As you may know, 3D printing typically means extruding a soft material in layers. “That is how LSAM works but it is not how Cut Layer Additive works, so it would be confusing to call them both “3D printed parts”,” Susnjara says. Therefore, “Cut Layer Additive does not print, it cuts parts. It is still an additive process since it makes parts by adding layers, but it is not a “print” process in the normal sense,” he adds.
These first differences between an LSAM 3D printer and Cut Layer Additive might easily prompt any user to think that the Cut Layer Additive machine was created to solve problems the LSAM could not. I, myself fell into that trap until Susnjara laid emphasis on the reason why this process has been created:
First and foremost, “this process was trying to create something new”: giving users the ability to produce parts with the benefits of the additive process using materials one cannot print.
“One way to do that is to make a part by laminating layers of material cut from sheets. We decided to try to do just that, but to also make the final product similar in structure to the rather successful large format printed parts our customers are currently making. This means that the parts that make up each layer, although thick, would not be all that wide, with walls, just like printed layers. This meant they could be nested on sheets and cut out on a CNC router. The only problem with this is that programming all those parts would be a nightmare, so we came up with a unique approach where you don’t necessarily program, but instead, define the part you want and send it to an intelligent machine which then programs it for you. LSAM and Cut Layer Additive are different processes using different types of material-producing parts for different applications. Both work well, they just make things from different materials,” the CEO explains.
A closer look at Cut Layer Additive: how does it work?
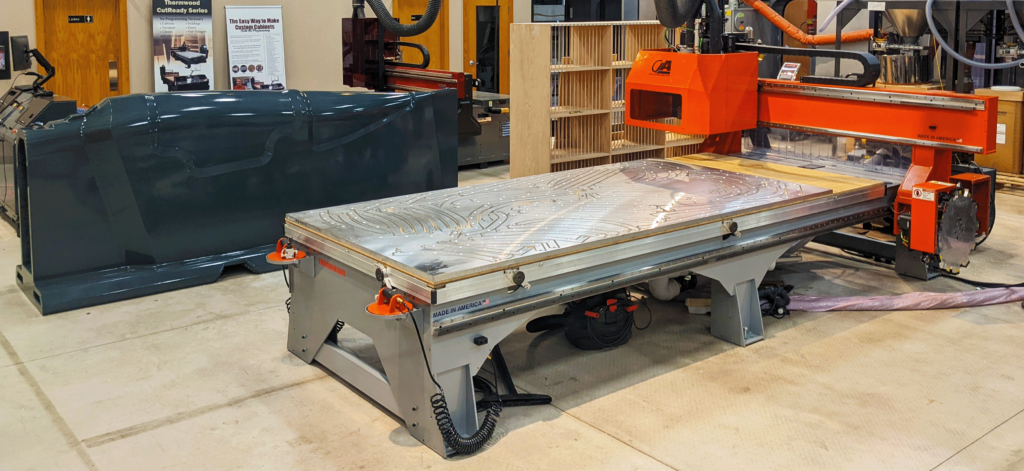
The machine cuts out each layer of the build, separating the layers into different segments to allow for optimized nesting on the sheet the parts are being cut from. The segments are then fit together with puzzle joints to form each layer of the build, which is typically put together by hand, layer by layer, using dowel alignment holes for faster assembly.
Thermwood says this process can be done with almost any material that can be CNC routed, including metals and porous materials that can be treated with resin to make a thermoset composite part.
In one of the first videos released on Cut Layer Additive, product manager Jody Wilmes says that the system can speed up the build by ordering the cutting to allow users to start assembly while the rest of the build prints, if it requires multiple sheets.
However, “build rate depends on the material being processed,” Susnjara outlines. “On a large aerospace tool which was both printed using LSAM and made using Cut Layer Additive, Cut Layer was several hours faster creating the near net shape part, but there were some post operations needed for Cut Layer, to make it into a thermoset composite part, which made the two processes quite similar. Typically, if you are processing material that cuts easily, such as plywood, MDF, foam sheet or the like Cut Layer Additive will be significantly faster, even when you add assembly time. If you are processing aluminum, it will be slower but it will still be faster than about any other way of making the same aluminum part,” he continues.
Compared to LSAM, the Cut Additive Layer process would take the same amount of time and labor as needed to additively print the same part, and it can even be faster with some materials.
Moreover, the whole process is made possible by a programming software, which allows users to skip the hours of work that would be needed to program out the CNC specs for each segment of each layer of the build.
This means that users just need to provide the machine with a CAD file of the shape of the build, and details about how it should be made, including the material you are using, and the wall thickness. In an interview given to 3D ADEPT Media, Susnjara also points out the capabilities of this software solution as one of the key strengths of the manufacturing package:
“Software and part processing is actually the key to the process. It is not only highly advanced but it is actually a fundamentally different approach. Instead of trying to program all the components that make up the part, we simply tell the machine what we want and it makes it. This is done in basically two steps. First, you show it the shape. You do this by sending it a CAD file of the basic shape you want. Then, you tell it how you want it made. This is done by answering questions such as the dimensions of the material you want to use; and the thickness of the walls you want. The kind of joint you want between layer segments and the like. The machine then slices the part, creates the individual layer segments, nests them on your material, creates the program and then cuts it all out. The process is fast, often taking minutes instead of hours or days.
This capability is expanding to make things that I’m not sure can be made any other way. We will be putting information out about this shortly.”
So, prototyping or production applications?
A manufacturing solution that can help create an additive part from a CAD model, slices the part into layers, splits each layer into segments, adds connection geometry between segments, offsets for trim stock, staggers joint between layers, adds alignment holes for dowels, efficiently nests all the parts on your sheet material, and creates a multi-tool CNC program – all of this automatically looks like a dream come true but for which end goal: prototyping or production applications? At the end of the day, the answer to this question is what OEMs are looking for.
“Large format near net shape parts,” the CEO answers. “These parts can be used as any large format additive parts. The additive process is normally used to produce a single example, a production tool or initial pattern or prototype, for example. It can normally produce a new design faster and at a lower cost than any other way of making it. If a part needs to be produced in volume, it is normally preferable to build production tooling and use that to make parts.”
Achieving large format near net shape parts that are not 3D printed is the result of the combination of several competencies: their CNC and additive approaches on the one hand, and on the other hand, their CNC and “machine intelligence”, which they’ve been working on for almost a decade.
When asked about the key factors that would drive a customer to go to the new Cut Layer Additive product over Thermwood’s LSAM line, Ken Susnjara says: “If you want to make large format parts from thermoplastic composite material, LSAM is the logical choice. It works great for that application running that type of material. If you want to make parts from other materials, such as wood or aluminum, which you can’t print, you need Cut Layer Additive.”
That being said, while there isn’t a real limitation in terms of build volume for Cut Layer Additive – since each layer can be broken down to a number of segments to fit on the cutting table -, it should be noted that once the near net shape part is assembled, the operator will need a five-axis machine to trim it to the final surface. This machine needs to be big enough to accommodate the assembled part.
The new product is available now, anywhere in the world where Thermwood does business.
Thermwood believes executing this simple idea with cutting-edge technology can have a profound impact throughout the large-scale manufacturing world, allowing producers to build new designs faster and at a lower cost.
This interview has first been published in the September/October edition of 3D ADEPT Mag. Co-written by Cameron & Kety. Images: Thermwood.
Remember, you can post job opportunities in the AM Industry on 3D ADEPT Media free of charge or look for a job via our job board. Make sure to follow us on our social networks and subscribe to our weekly newsletter : Facebook, Twitter, LinkedIn & ! If you want to be featured in the next issue of our digital magazine or if you hear a story that needs to be heard, make sure to send it to contact@3dadept.com