Eleven years ago, when multinational oil and gas company Shell bought its first metal 3D printer, the company only aimed at producing prototype parts for their experimental installations. Fast forward to today, along with fellow companies of the same league, Shell is writing a chapter that could position the oil and gas industry as the fourth major adopter of Additive Manufacturing. Angeline Goh, 3D Printing Technology Manager at Shell, takes us through a journey rich in lessons, collaborations and hope for the future.
As you probably already know, healthcare, aerospace and automotive are the major adopters of AM. If AM is continuously opening up new applications across these industries and more, the technology’s ability to respond to a billion-dollar problem, at multiple levels can be enough to position the oil and gas industry as another source of growth for the technology. That problem is supply chain uncertainty.
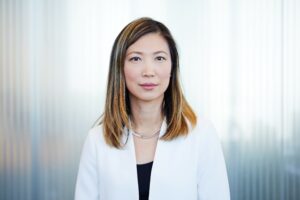
Unused or outdated parts take up storage space, resulting in increased inventory costs. Added to that the inability to identify and track obsolete spares, operational downtime, or safety and regulatory compliance, one may understand why oil and gas industries are riding a costs roller-coaster.
Since Covid-19, AM has emphasized its ability to address these challenges, giving oil and gas companies like Shell the chance to make the most of their resources – in-house, they have powder DED, SLM, SLS, SLA, FDM, Multi-jet fusion across a fleet of about 15 3D printers in Amsterdam and India:
“Today, we are using 3D printing to print obsolete spare parts on demand for our assets; develop novel equipment and rapidly prototype engineering designs. By developing an in-house capability, we want to bridge the gap between 3D printing manufacturers and the energy industry, and also become informed users of the service externally,” Goh explains.
While these resources supported the production of medical equipment during the Covid-19 pandemic, and in some development projects like the one conducted with the OEM B.F.E Bonney Forge, Shell does not aim to become a manufacturer. Just like Equinor, the company believes in a new digital inventory ecosystem, whereby it is important that manufacturing of spare parts for their asset is done locally as much as possible, leveraging qualified 3rd party local service providers to provide true lead time reduction and sustainability gains. As such, they only use their facilities for internal R&D and asset support projects.
Key areas of interest and collaborations
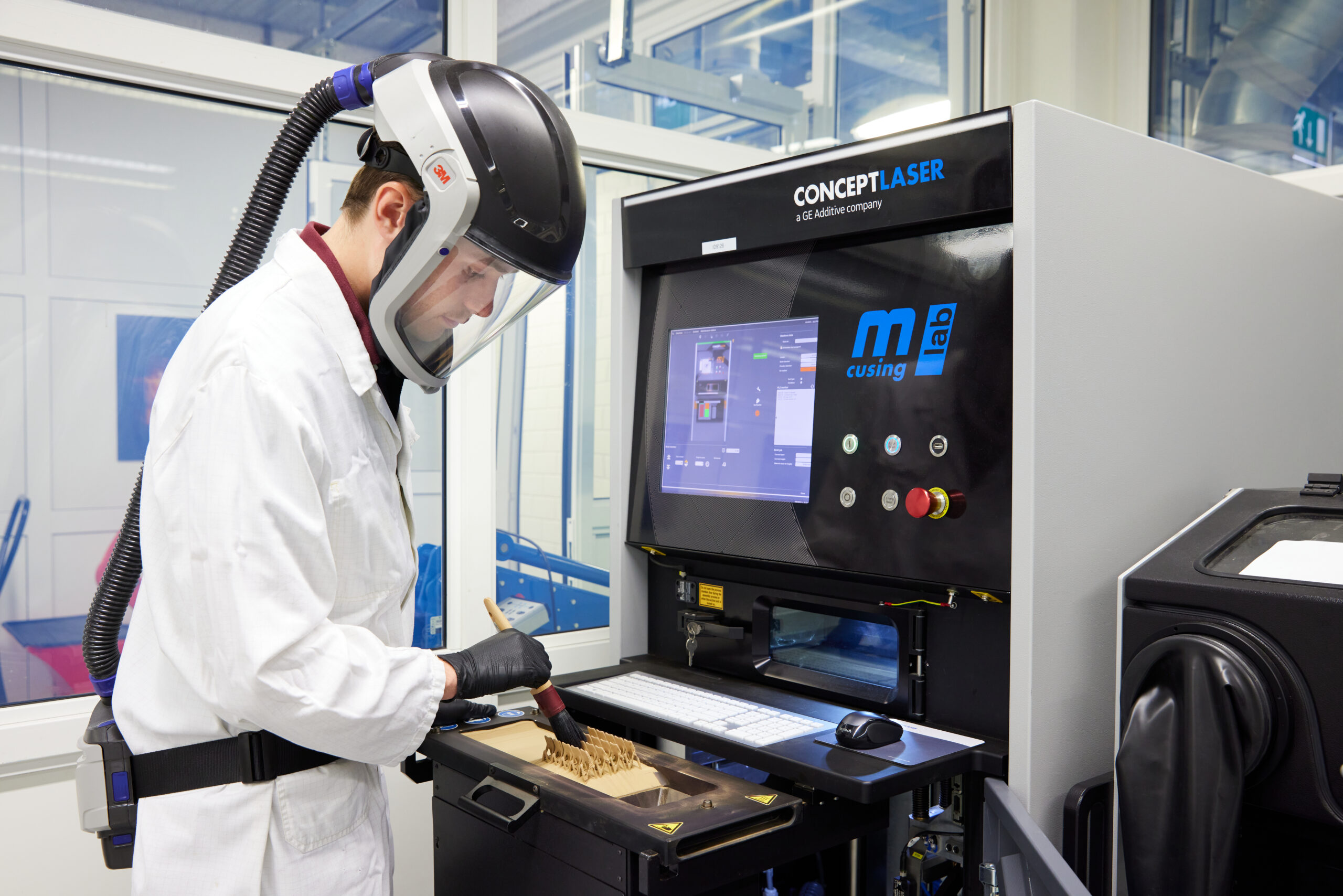
“There isn’t a typical day at work for us in the 3D Printing [unit] when it comes to R&D alongside asset support, but there are 5 broad categories of work that keep me busy, and the allocation of time to the categories may vary from day to day,” Goh said before listing:
- R&D work on novel designs or applications. These are projects aimed at achieving longer term objectives of AM applications to create business value for our company. Some of these are multi-year programs, such as the development we started on the 3D printed pressure vessel for 3rd party certification. It’s about addressing a problem worth solving and evaluating over the course of milestones set for the project if the hypothesis holds and we are able to make the breakthrough needed.
- Asset support work can come from any part of the world and could include a simple visualization for an engineering solution, to help with an emergency requirement of an obsolete spare part. Work requests from the assets need constant prioritization due to the potential impact they can have on the asset’s production.
- Knowledge Management & Transfer – I prepare materials for workshops, and webinars, and am involved in the 3DP network calls internally to upskill our engineers.
- The Joint Industry collaboration work for the digital inventory with partner operators is underway too and is an exciting piece of development.
- Technical Assurance work – reviewing new internal guidelines and preparing technical documentation & papers on the technology.”
Needless to say, the challenges may differ from one project to another, but one common thread in their job is that given the high standards of the energy industry for health, safety and environmental concerns, the introduction of any new technology needs to be thoroughly proven by robust and comprehensive testing and adequate data points.
Taking the example of the work they are doing with Kongsberg Ferrotech, Equinor, SINTEF, and Gassco, to develop 3D printing technologies for subsea equipment repair and maintenance, she explains:
“This is certainly a challenge for example, when there are no AM standards for hyperbaric and mobile applications.
The team has to harmonize applicable standards for the scope of repair, and we are working in close collaboration with vendors, operating companies and the class societies to achieve that. In this process of introducing AM-based subsea repair, it is important to identify and manage the risks as we go about engaging our assets that are candidates as pathfinders. In this way, we then build confidence in the whole value chain. A comprehensive qualification program with participation from the inventor and manufacturer to the first user asset is required to demonstrate the quality and value of subsea AM repairs.”
In this vein, in Goh’s view, enhancing quality management would drastically improve the way we source 3D-printed spare parts across the industry but not only. Improved lead time, costs and acceptance for AM also require a focus on data and people.
As far as data are concerned, “improvement leveraging online quality monitoring data for defect detection and quality control that reduces the amount of post-manufacturing testing” should be a key area of focus for the industry as it “is important to achieve higher-right-first time prints and reduce overall lead time and cost of the technology.”
Furthermore, I like the idea that Goh puts people at the heart of change. Let’s be honest. Transformation is notorious for its pitfalls and challenges – but perhaps the most common mistake organizations often make is neglecting the so-called “soft side” of change. Goh sees the importance of focusing on people – and collaborations in particular, with end-users “to upskill the community on knowledge of the technology, to build trust in the technology, as well as manage the changes in work processes related to [its adoption].”
“Similarly, there are advocates for digital inventory in the supplier companies that are original equipment manufacturers. However, even these advocates need support to transform their organizations to the new ways of supplying. Strategy and processes will have to change, and these require effort and attention to be implemented effectively,” she adds.
Can AM divisions of oil and gas companies do their part in this sustainability journey?
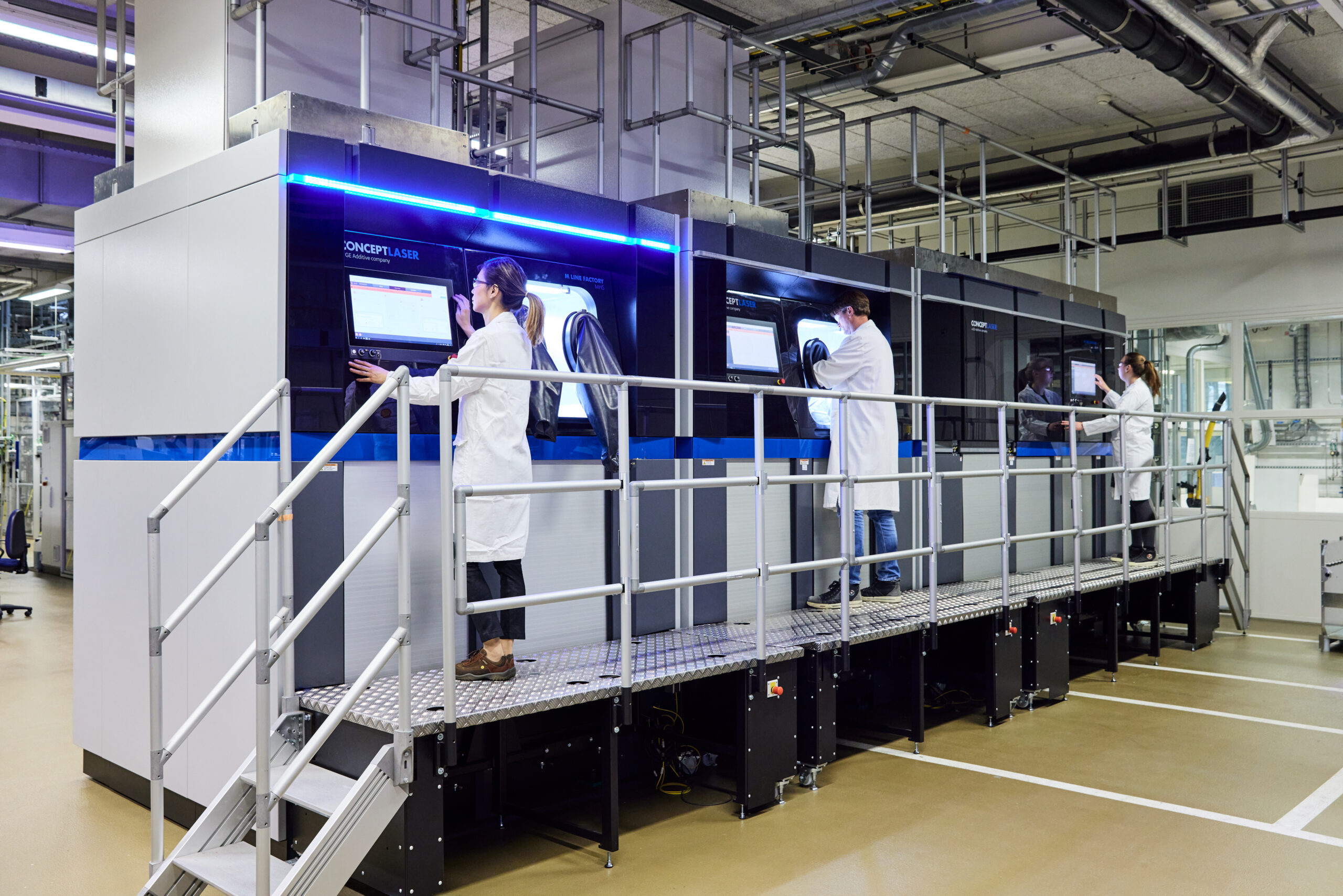
The oil and gas industry is facing increasing demands to clarify the implications of energy transitions for their operations and business models, and to explain the contributions that they can make to reducing greenhouse gas emissions and to achieving the goals of the Paris Agreement.
The increasing social and environmental pressures on many oil and gas companies raise complex questions about the role of these fuels in a changing energy economy, and the position of these companies in the societies in which they operate.
While improving the sustainability of its operations is a multi-faceted ambition, Goh reaffirms that Shell is pursuing both immediate and long-term opportunities to mitigate the impacts their operations have on people and the environments they operate in.
While the company’s ESG and sustainability journey is a topic that goes beyond her scope of expertise, she remains hopeful on what AM can do – especially when it comes to going beyond the development of novel designs to reduce the emission of operations and the local on-demand spare parts production:
“More can be achieved in improving repeatability and reducing the variation of printer quality, in the development of secure and autonomous transfer of data to remote printers for manufacturing and availability of AM specific datasheet for a wider range of material used by our industry to facilitate on-demand, local manufacturing.”
“Beyond the technical scope, the community can help propel growth in the adoption of the technology by sharing success stories as well as lessons learned on AM applications. There are various platforms for exchanging knowledge and experiences and I am certainly participating in a number of them and hope to see these forums grow. An example of AM community coming together to share experiences and inspire others is a book that I’ve read and found helpful. It is called the AM Change Management Guide and is published by the Mobility Goes Additive Group (MGA). There is a lot of effort still needed to develop new guidelines and standards requiring contributions from all partners in the AM ecosystem. Published standards would support the development of legislation to support the AM adoption,” she concludes.
This content has first been published in the 2023 September/October edition of 3D ADEPT Mag.