As far as ceramic AM is concerned, one vertical industry where the growth potential is assured is the healthcare industry. This comes as no surprise when we know that this vertical industry is the largest and first one served by AM in general (SmarTech). With Aerospace and Automotive respectively placed on second and third ranks of vertical industries mostly served by AM, it makes sense to discuss the added value of ceramic AM within the wide range of AM processes currently leveraged in these markets.
The conversation around this topic comes from one observation: most of the time, Aerospace and Automotive companies are making headlines with applications achieved using FDM, metal AM, resin or polymer 3D printing. With the multitude of AM processes that are popping up every day – and taking into consideration the ones that are already commercialized -, our assessment of ceramic AM reveals a potential that is quite underestimated – or unknown? It’s hard to say, quite frankly. Nevertheless, we are wondering if this lack of communication is due to a gap between technology recognition and technology usage or is it simply a matter of privacy policy between contract manufacturers and companies across the aerospace and automotive industries?
The gap between technology recognition and technology usage poses the question of how potential users see the technology. Are they seeing ceramic AM as a disruptive technology or as an emerging one? The truth is, the words “emerging” and “disruptive” are often used interchangeably when it comes to technology while in reality, they are very different. As Dr. Johannes Gartner, Assistant Professor at the Johannes Kepler University Austria once explained, emerging technologies describe innovations with the potential of being disruptive, real disruptions are only realized when an emerging technology is used to either solve an unsolved problem or to solve an old problem in a better way.
This means that if AM users consider ceramic AM as an emerging technology, the lack of applications in the automotive and aerospace fields might be understandable as users rarely invest in emerging technologies (fear of not achieving an ROI).
According to Lithoz’ Director of Sales and Marketing, Isabel Potestio, “The main obstacle currently facing ceramic AM here is that manufacturers aren’t yet fully aware of the level this process is now at. The technology has matured significantly as a manufacturing technique over the last years -that is, while many manufacturers may have initially started using ceramic AM in a prototyping capacity, many have transitioned into full production. They have experienced the performance and workflow benefits of ceramics AM and are taking it to the next step. Today we see customers producing millions of ceramic 3D printed parts per year, which are not economically and viable for injection molding or machining.”
Furthermore, when discussing applications within the ceramic AM landscape, it’s important to keep in mind that there are AM technologies designed for technical ceramics and there are AM technologies designed for traditional ceramics. The former often leads to the production of high-performance parts that usually weigh just a few grams while the latter enables the production of large molds and foundry cores that weigh several kilograms.
The wide range of applications across technical and traditional ceramics often makes it difficult to understand the specifications around technologies and materials. However, the growing interest in technical ceramics will make us focus on this part of the market as part of this feature.
“Ceramic machining is very challenging. For instance, in comparison to metal machining, the risk of surface damage, chipping, and tool wear are much greater, and dimensional accuracy is much harder to achieve, so additive manufacturing is arguably an even greater step forward in the field of ceramics than it is in the established fields of metal and polymer AM. Together with the unique properties of ceramics, such as strength, isolation, etc., there’s huge potential for expansion of technical ceramic applications”, Guy Zimmerman, Chief Marketing Officer at Xjet, metal AM & ceramic 3D printer manufacturer, comments.
The lines below ambition to discuss the challenges and potential of ceramic AM across the automotive and aerospace industries.
Where do the challenges and opportunities lie within aerospace and automotive?
Whether we discuss applications in automotive or aerospace, the challenges and opportunities are reflected at two main levels:
- The materials
- The “High Value vs High Volume” decision
The materials
In general, technical ceramics are known for their contribution to a wide range of applications in the automotive industry. Whether fully electric or hybrid, high-performance parts for e-cars, e-buses, e-trucks and e-trains can be produced using technical ceramics, leading to better economy, comfort and safety. The only thing is, most of these applications are enabled by metal and ceramic injection molding.
As far as AM is concerned, one notes that technical ceramics are a great solution in critical applications where conventional materials like metals or high-performance plastics do not perform. With 8 main types of ceramic AM processes identified, the choice of one ceramic 3D printing technology mainly depends on the desired characteristics to achieve – characteristics related to material properties or resolution.
“The majority of leading mechanical ceramic applications in automotive are still made with traditional processes of CIM and Machining. The AM processes that start adding value in automotive are DLP and Direct Material Jetting. The reason is the requirement for high accuracy, repeatability and total cost per part, which requires high throughput and automated manufacturing processes”, Zimmerman outlines.
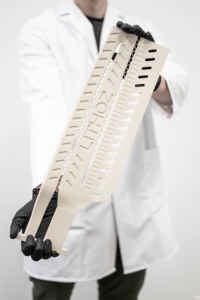
However, a wide range of applications is likely to pop up faster in the aerospace industry. By reducing manual assembly, and the weight of aircraft via modelling-developed designs, ceramic AM can be a great production candidate to enhance efficiency and performance. As a matter of fact, we have already witnessed the production of nozzles, thrusters, sensors and antennas via ceramic 3D printing.
On another note, while higher cruise altitudes and speed of flight enable better efficiency and reach, it comes at the cost of extreme environments endured by part materials. Apart from their ability to withstand such stringent environments, ceramic materials deliver increased corrosion resistance, higher stiffness, lower density, and, in some applications, multi-functional properties.
“Ceramics are the material of choice in extreme environments where other materials fail, and so it is in these applications that ceramics are really becoming commercialized. One example is 3D printed ceramic cores for aerospace applications. With climate change being the major challenge facing the world today, manufacturers in every field are looking to be more sustainable by building more efficient parts to save resources. 3D printing offers a level of design freedom unachievable using conventional manufacturing techniques, allowing for the production of more fuel-efficient designs”, Potestio explains.
The problem is that the difficulty that comes with creating dense ceramic materials limits the applications in this sector to the exploration stage. Unfortunately, the latter depends on the investments that users are willing to make at the research level. However, if the research is not done in collaboration with players in the targeted vertical industries, it is in any case performed in-house by machine manufacturers and material producers.
Taking example on their solutions, Lithoz’ Potestio explains that each of their technology (LCM, LIS and LSD-print) answers different demands for applications across a variety of fields. For instance, Lithoz’ LIS is more suitable for coarser components and capable of large wall thicknesses and especially dark materials.
What if an opportunity lies in the ability to address a challenge that another AM process couldn’t meet?
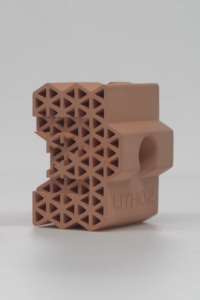
Most applications enabled by AM usually strive to address the challenges raised by their conventional manufacturing processes counterparts. That’s the reason why you’re likely to see the comparison with a given type of traditional manufacturing process. In this case, for ceramic AM to thrive, it could be interesting to explore its ability to address a challenge that another AM process fails to address.
Vincent POIRIER, CEO of ceramic 3D printing service bureau Novadditive, believes that all types of ceramic AM processes can create value in the automotive and/or aerospace industries. According to Poirier, ceramic AM has a unique way to create “unfeasible” shapes with enhanced properties. That being said, the expert states that the differentiation shouldn’t be a comparison between AM processes, but rather the choice of the right technical material.
Among the important criteria that manufacturers should take into account to choose the ideal technical ceramic for production, one notes the mechanical and thermal properties, stiffness and density as well as the CTE.
The “High Value vs High Volume” reality
It shouldn’t be a decision between “quality” and “quantity” as quality must always be part of the equation. It’s rather a discussion about where the added value has mostly been seen.
In the automotive industry, for example, components require high precision and equal performance. They have to deliver excellent strength at low weight, withstand high temperatures and need to be wear-resistant to achieve high performance at a cost-effective price. Ceramic AM might eventually meet these requirements for one part but is not ready for scaling production yet. The ceramic 3D printed piston that was produced by Spyros Panopoulos Automotive (SPA) using the XJet Alumina material for its Chaos Ultracar is a great example. However, the mass manufacture of Alumina parts in the field has yet to be seen.
Potestio notes that, in the automotive industry, there is definite potential for innovation via ceramic AM, particularly in those applications where miniaturization and extreme levels of complexity would greatly increase efficiency. In such examples, ceramic AM can really support the development of powerful solutions for e-mobility and future wireless systems.
In the same vein, the aerospace industry is filled with astonishing examples of application cases that demonstrate the capabilities of various ceramic AM processes. Fabricating a space launch vehicle is a brilliant way to demonstrate a product’s potential and high value, mass producing them with the same technology is a different battle. The reality is, the heat-resistant ceramic parts they require are extremely difficult to manufacture. Such parts should resist temperatures as high as 2,700 degrees Celsius and drag forces of hundreds of kilograms that are encountered at speeds of Mach 5 and higher, such as on nose cones, wing leading edges and engine inlets.
At the end of the day, 3D printed ceramic parts must be affordably mass-produced, which means initial ingredients must be chosen with cost in mind. If that’s not the case, then solutions should be explored to remove any unnecessary steps.
Last but not least…
Our dossier on the current manufacturing landscape of Ceramic Additive Manufacturing revealed that, with 8 main types of processes, the ceramic 3D printing market is overcoming its days of hype to focus on how it will cater to different industries’ needs. This conversation matters as the growth of AM technologies depends on an economic perspective that should not be overlooked: “the more applications there are, the more materials will be developed, and the more printers will evolve or be introduced to the market”. In the ceramic 3D printing market especially, understanding the gap between technology recognition and technology usage can make all the difference and open up a whole range of new applications in this sector.
This dossier has first been published in the January/February edition of 3D ADEPT Mag.
Remember, you can post job opportunities in the AM Industry on 3D ADEPT Media free of charge or look for a job via our job board. Make sure to follow us on our social networks and subscribe to our weekly newsletter : Facebook, Twitter, LinkedIn & Instagram ! If you want to be featured in the next issue of our digital magazine or if you hear a story that needs to be heard, make sure to send it to contact@3dadept.com.