2014. The excitement around ceramic 3D printing occurred when we first saw 3D printed vases and homewares but it faded progressively as the market understood it wasn’t necessarily the road to success for this field of activity. In the meantime, an exhaustive list of OEMs and material producers who had understood the potential and pertinence of ceramics for industrial applications have been working in stealth mode for several years, waiting for their technology solutions to reach a certain level of maturity for industrial applications before launching them. 2022. The ceramic 3D printing market is still considered as a relatively new segment, compared with polymer and metal 3D printing. However, increasing entrants into the field, solutions to major manufacturing challenges and a 7-fold growth for the Ceramic 3D Printing Market by 2032 are some of the items that drive the conversation around this topic today.
Any type or segment in Additive Manufacturing always strives to address the challenges raised by the conventional manufacturing processes counterparts. The same is true for ceramic 3D printing. Hot isostatic pressing, extrusion, and injection molding have been extensively used in the ceramics industry, but their expensive costs and the long lead times make it difficult to use these technologies for prototyping and small/medium-volume part production. Just like polymer 3D printing, Ceramic 3D printing can address these issues but with a different set of manufacturing processes.
The exclusive feature below ambitions to understand and identify:
- The technological landscape in which ceramic 3D printing fits;
- What didn’t work before, and what works today in terms of material & manufacturing solutions?
- The established business model in the ceramic 3D printing market and applications where there is a real potential.
The technological landscape of ceramic 3D printing
To provide a bit of technical background to those who are not familiar with the process, let’s note that a ceramic is an inorganic non-metallic solid that can be shaped and then hardened by heating to high temperatures.
We may all be familiar with traditional ceramics that are clay-based but today, the definition of ceramics covers materials like high-performance, advanced and technical ceramics, in a nutshell, materials that can be developed from a wide range of inorganic non-metal materials. To make it easy to understand the different categories of ceramics, experts have identified two main types of ceramics: classic ceramics that derive from natural raw materials (clay) and technical ceramics. This means that carbon and silicon can be considered ceramics, and that’s interesting to note because many of the 3D printable ceramics have names that sound more like metals as they are not derived from clay. Those high-performance or technical ceramics are “materials used for engineering purposes instead of tableware”. They may have the properties of high strength, high hardness, high durability and high toughness.
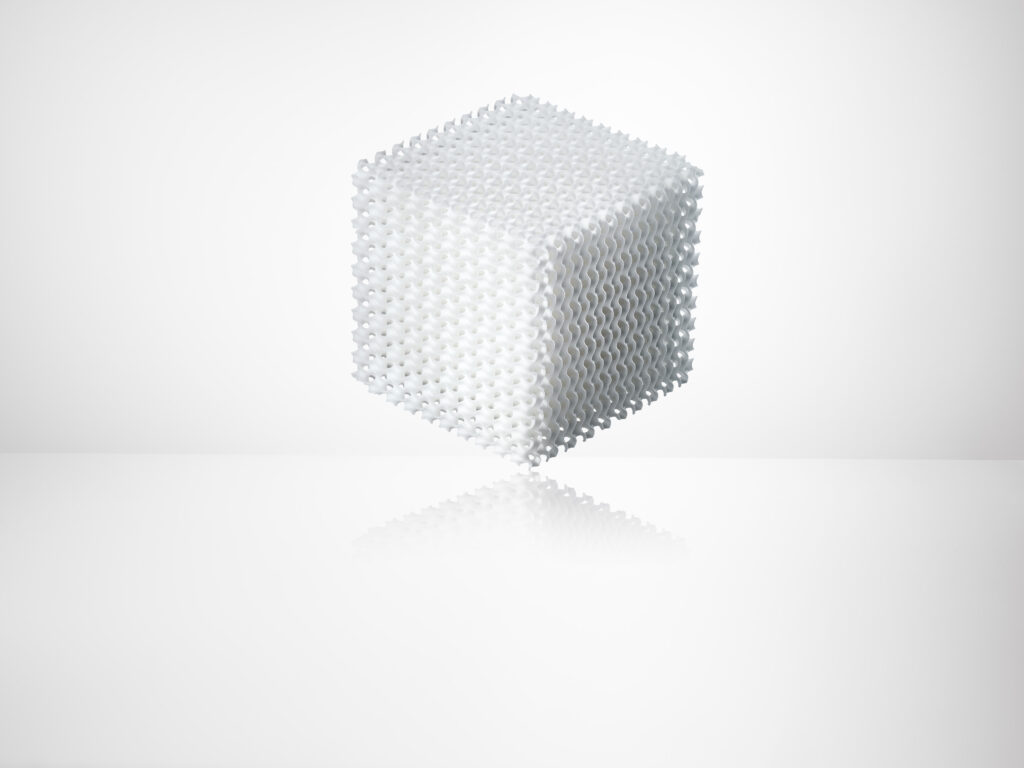
From the very beginning, whether it was meant for art or industrial purpose, the use of ceramic 3D printing has been defined by materials. And these materials have somehow defined the different technologies that can enable ceramic 3D printing applications for industry or art products.
Indeed, the current AM technologies that enable the production of (nearly) fully dense engineering ceramics are Slurry-based Selective Laser Sintering (S-SLS); Slurry-based 3D Printing (S-3DP); Binder Jetting (BJ), Fused Deposition Modeling (FDM); Direct Inkjet Printing (DIP); Stereolithography (SLA), Photopolymerization (DLP) and Robocasting (direct ink writing DIW).
Research reveals that, while the extrusion based printing process (FDM) processes primarily classic ceramics, other types of AM processes are (increasingly being) qualified to work with technical ceramics. Those industrial ceramics are available under various formulas which range for instance, from aluminum oxide (Al2O3), Zirconia, Silicon Nitride, Silicon Carbide, to zirconium oxide (ZrO2) commonly called “ceramic steel”.
Overview of ceramics AM processes
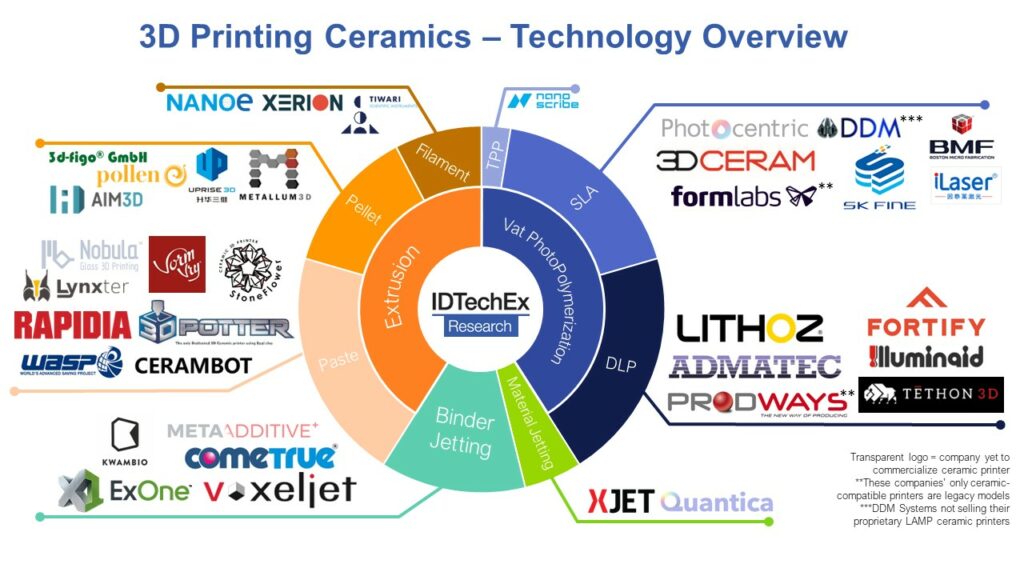
Extrusion or FDM-based processes might be pretty easy to understand as the paste or filament that is pushed through the nozzle enables to build up the part layer-by-layer. Italian OEM WASP develops a series of large 3D printers called delta, that are worth mentioning in this area. Pollen AM also recently entered the ceramic market with a range of technical ceramics available under the form of pellets.
According to researchers of KU Leuven AM Group, Selective laser sintering (SLS) of ceramic components can be categorized as direct or indirect. In direct SLS, a laser beam is used as the heating source to locally heat and sinter the deposited ceramic powder layers. Indirect SLS involves laser melting of a sacrificial organic binder phase in the polymer-ceramic composite powder to produce ‘green’ parts. This requires a subsequent debinding and furnace sintering step in order to produce the final ceramic parts. Both processes are still currently most explored at the research level. Unless we are mistaken, there is no machine (yet) based on this process on the current commercial market.Ceramic stereolithography (CSL) on the other hand, is often categorized as Photopolymerization ((SLA,DLP, LCD, CLIP). The process is based on the selective photo-polymerization of a photosensitive slurry (also called the ‘photopolymer’ that serves as ‘binder’ after polymerization) containing homogeneously dispersed ceramic particles to make ‘green’ parts, which need to be debinded and sintered. One company that stands out from the crowd in this segment is Lithoz.
“Our range of 3D printers are based on LCM technology, building individually-cured layers of ceramic slurry in a bottom-up manner to create high-performance complex parts without the need of a mold or other tools. Using this technique, it is possible to build far more intricate and fine features with outstanding levels of precision and accuracy unachievable using other production techniques. Our ceramic materials also offer significant advantages over other materials, such as high heat and chemical resistance and biresorbable qualities for medical applications”, Zoran Ostic, business & application expert at Lithoz states.
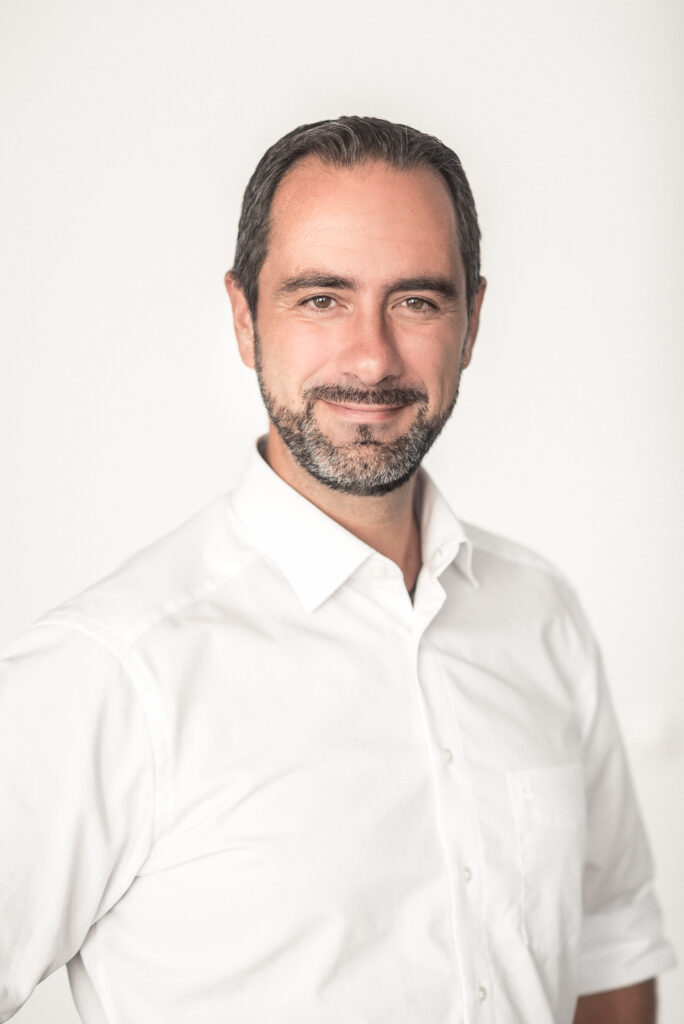
In a Binder jetting process, a binding agent is selectively applied to a bed of ceramic powder one layer at a time. The challenge with this process lies in the powder bed density of the machine that should be maximized while the volume of liquid binder required should be minimized to achieve strong green parts. ExOne, a Desktop Metal company today, is one of the company that has developed a binder jetting process that is really scalable in the industry. Voxeljet is another one. Indeed, Binder Jetting can produce hundreds or even thousands of green parts in a single build. However, one of the disadvantages often highlighted by industrials is the low green part strength and low surface finish quality.
NanoParticle Jetting comes next. This process is developed and commercialized by XJET. It fabricates parts by jetting thousands of droplets of ceramic nanoparticles from inkjet nozzles in ultra-thin layers. With this inkjet and UV curing based approach, yielding green parts are similar to those obtained via stereolithography.
Interestingly, apart from XJET’s solution that doesn’t need debinding (and that has water dissolve support), almost all of these processes require debinding and sintering before obtaining the final part. However, the success or failure of these processes often depends on the material used.
The materials standpoint
“Ceramics are hard – and not just mechanically speaking! Compared with metals and polymers, ceramic materials are incredibly difficult to shape through subtractive forming methods like machining, thanks to their inherent mechanical hardness and brittleness. This is why 3D printing of ceramics is very enticing to the industry at large”,Bram Neirinck and Kevin Eckes, Research Engineers at Aerosint observed.
The truth is, each printing process might come with its share of pros and cons but in general, issues experienced are high firing contractions, low density and strength, and potential incompatibility with glazes. Other failures often identified, can be dropping, sticking, splitting, and flaking. While some researchers might see an opportunity to build custom-made machines, Tethon3D’s CEO Trent Allen sees an opportunity to create new materials.
“In traditional aqueous material science, you are more limited in the materials you can process. Also, there is immense opportunity in taking materials that are difficult to process in traditional manufacturing like SiC(Wet Layup) and being able to use a non-aqueous binder to make producing parts much easier. For us at Tethon, nearly 1/3 of our business is taking powders used in traditional manufacturing at Fortune 500 companies and turning them into 3D printing resins, or powders for binder jetting. We fully expect this business to grow as additive grows in parallel”, Allen explains.
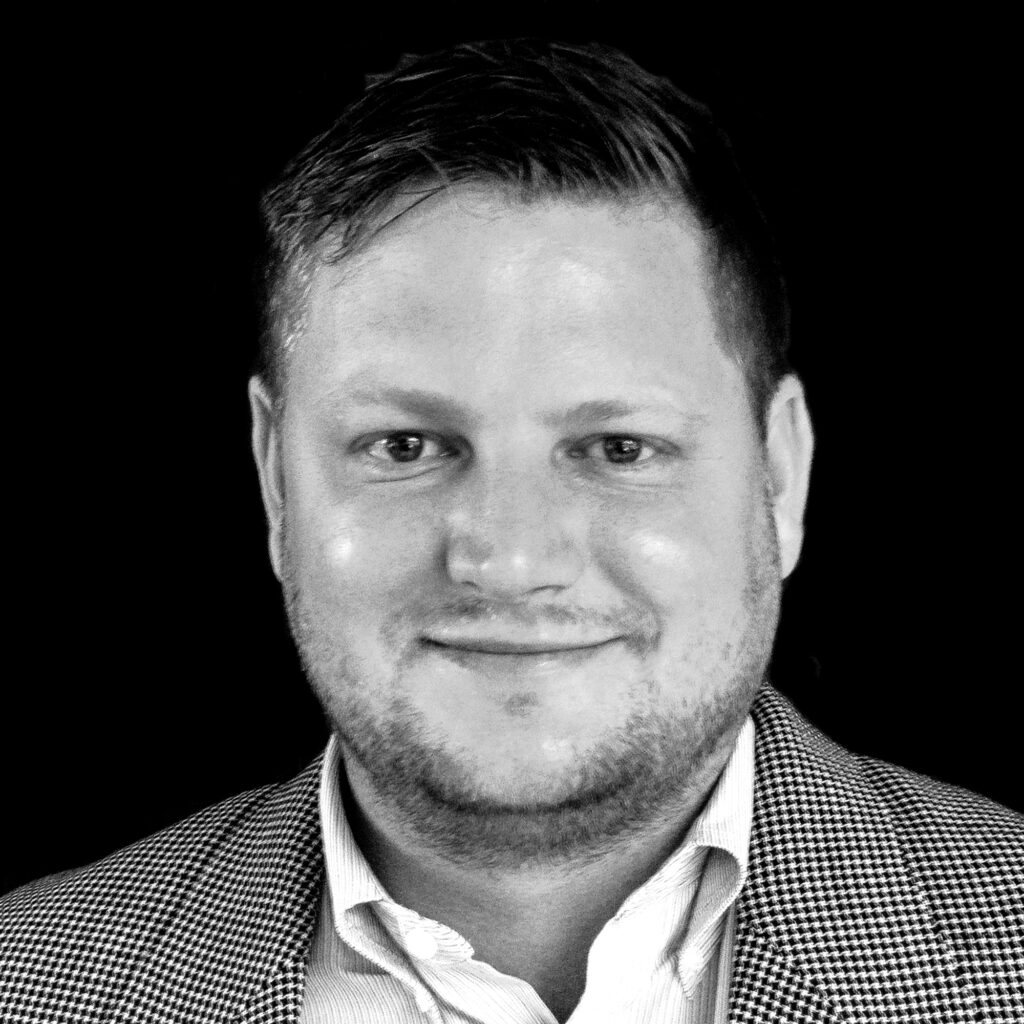
That being said, while the first solution that may come to anyone’s mind when it comes to overcoming challenges, might be to rethink the production process, Tethon3D highlights a more powerful and traceable alternative: a software tool. The company that sees itself more like a software company than a traditional ceramic materials producer believes that “anyone that has built software knows a product is never truly finished. Technology improvements within polymer material science and finding ways to improve powder processing is accelerating. With over 1,300 customers who trust our materials it can be challenging for us to make sure our global customer base knows why a material was altered, upgraded, or killed-off. Another challenge when innovating so quickly is you need to figure out how to scale from lab batches to production batches.”
Today, taking examples on UV printing & Binder Jetting which are the main processes the company has developed expertise in, Allen explains that to truly move into production and create great parts, it’s essential to have consistent materials and limit the amount of shrinkage.
“Binder Jetting & UV printing complement each other. For us we generally print more precise, smaller, denser objects using UV and larger, blockier objects with thicker walls using Binder Jetting”, he adds.
In the end, the key for scaling into production does only lie in the development of new materials, but also in delivering the right final properties, while simplifying the process and ensuring safety issues. And if you’ve found this key, this certainly means you have figured out how to scale from lab batches to production batches.
The established business model in the ceramic 3D printing market and applications where there is a real potential.
It always starts with R&D and eventually prototypes. In addition to these two usages, first applications in ceramic 3D printing reveal an interest for ceramic tooling and small-batch parts across industries such as investment casting for aerospace & defense, chemical engineering, and dentistry.
Surprisingly, applications that are delivered on the market do not come from 3D printing service bureaus. As a matter of fact, we saw some leading service bureaus such as i.materialise or Shapeways cease their ceramic 3D printing services a few years go. For Lithoz, delivering successful ceramic 3D printing applications requires a close collaboration between the machine manufacturer and its customers. That’s anyway the path the team is following, as they support their customers in the discovery of new applications, thus establishing ceramic 3D printing as a reliable manufacturing technology for industrial production.
“Many of our customers service the industry by providing their specific know-how of our Lithography-based Ceramic Manufacturing (LCM) technology to players of various industries, from medical and dental to aerospace and semiconductors”, Peter Schneider, Business and Application development expert at Lithoz states. “Ceramic 3D printing, while very well suited to modern manufacturing and development in every field, is however still currently seen as a ‘new’ technology, much more than metal or polymer AM, and therefore companies need incentive to switch over from conventional methods. Service bureaus have by far the highest requirements for a manufacturing technology, meaning that they only offer processes with the best ROI at the lowest technical risk – there is little room for trying new technologies. In the same way, these bureaus do not have the time or resources to waste on a technology they do not already know for certain will deliver”, he continues.
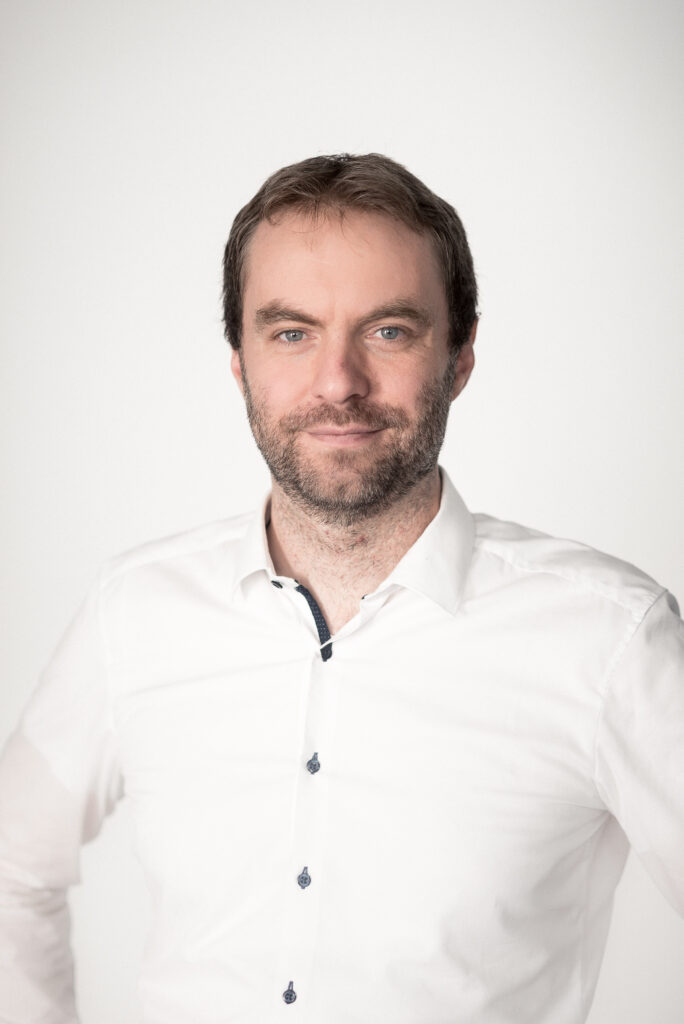
Moving forward, Schneider believes it’s only a matter of time for service providers to implement industrial ceramic 3D printing into their workflow. For the expert, one incentive that will drive this change is the combination of DfAM with the desirable material properties of ceramic materials – such as high chemical resistance, high strength and hardness – Such combination can open the door to applications that were previously unachievable and break into markets where metals and polymers have already reached their limits.
This incentive refocuses the debate on applications and the ones that are not yet fully explored by technical ceramics.
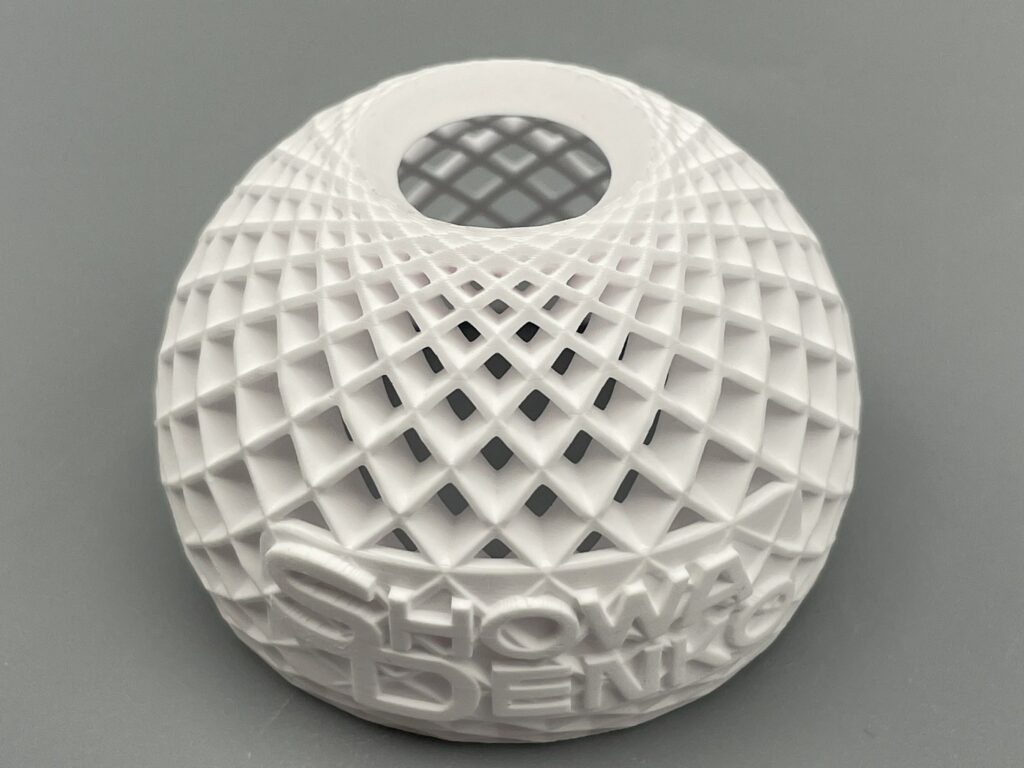
Currently, there is room for growth in R&D-related sales, as there is a large number of international research institutes working on progressing ceramic 3D printing in interesting applications like energy storage and carbon capture. Industry professionals currently need to tap into the healthcare industry. First, dentistry which constitutes a great potential for this technology – closely followed by ceramic medical implants. According to Lithoz’ Zoran Ostic, the potential of medical applications lies in the bioresorbability of ceramic materials.
“Bioresorbable ceramic implants, made of materials such as tricalcium phosphate or hydroxyapatite, dissolve in the body as the organic bone heals and grows. As such, ceramic implants promote bone healing and the need for a second surgery to remove the implant is completely eliminated. At the moment, however, metal implants – which often have considerable long-term side effects for the human body – are still the most common solution, meaning that the main challenge here is encouraging surgeons to shift away from a trusted solution to try a more innovative material.
In general, many applications for high-performance ceramics are under-developed by the market due to the fact that end-users of conventional technical ceramics buy from more established service providers. These manufacturers utilise traditional forming technologies and therefore have certain design limitations which the customer is accustomed to. They will design their parts based on these existing and well-known limits, despite there being huge potential improvements in part efficiency, design evolution and functionality using additive manufacturing instead. There is little motivation for the established service providers to move towards AM as they already have a successful and selling product. But we have also clearly seen that with the publication of some profitable business cases, the ceramic industry has really been roused from that sluggishness. Therefore, the most important focus of the ceramic AM market is to educate the industry and end-users in particular about the advantages of this technology, encouraging uptake and therefore spreading the message of this game-changing technique further”, the expert adds.
What’s the next big question?
Until four years ago, controversial debates built up conversations around ceramic 3D printing. Today, most industry players seem to agree with one fact: the market might still be described as “nascent”, but it’s ready for production applications. The only thing is that technology might be ready but industry players are not. And the only reason for this is fear.
According to Lithoz’ experts, ceramic 3D printing has in fact already mastered its most relevant hurdle – successfully upscaling materials, printers and software to empower industrial mass production whilst securing the same premium quality as offered with low volumes. The biggest obstacle now facing ceramic 3D printing is simply encouraging manufacturers and end-users to try a new technology and material over already established production techniques. Other materials, such as metal, have been used for certain applications for years and there is currently little motivation for service providers to shift away from what they trust. In the same way, other more conventional forming technologies also already enjoy great success in their fields, despite ceramic AM offering huge potential improvements in design freedom and part functionality. Consequently, this lack of incentive for trying a new technology is the biggest hurdle for ceramic 3D printing at this point.
So, the next big question might simply to know how we encourage industries to take that leap…and to this, the only response we can give (right now) is: to feel the fear and take action anyway.
This dossier has first been published in the March/April edition of 3D ADEPT Mag.