Following the in-house production of a 3D printed pressure vessel, Oil & Gas company Shell has obtained CE certification in accordance with the European Pressure Equipment Directive (PED).
This certification has been granted by LRQA (formerly Lloyd’s Register), a classification, training and advisory services company that specializes in engineering and technology for the maritime industry. The independent certification authority expert has already supervised several projects in the AM industry, especially in the heavy industry, like this gigantic 3D printed crane hook.
Shell’s certification follows a recent project that enabled the AM team to optimize their repair and replacement strategies. The milestone is even important for the energy company as it would be the first company in Europe to have obtained CE certification from a third-party authority for a part 3D printed in-house. Furthermore, LRQA categorized the printed vessel in PED Category III.
Moreover, this certification is even important in the energy industry as there are currently no legislation or global standards specifically for 3D printed pressure retaining parts. Shell explains that this lack in regulations means that the use of 3D printed pressure equipment is generally not permitted at industrial assets around the globe. Shell printed this pressure vessel to gather research data that help improve the sector’s trust in additive manufacturing as a technical solution to source spare parts “just in time” instead of stocking the spare parts for years.
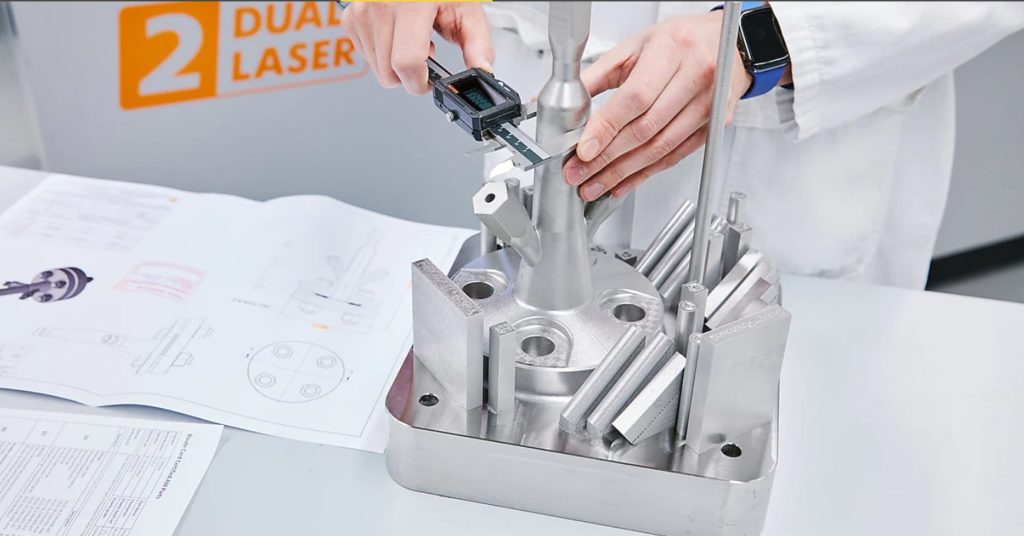
“This represents a significant milestone, not only for the additive manufacturing industry but also for the pressure equipment community. This is the first CE Marked pressure vessel approved by an independent Notified Body” explained David Hardacre, Lead Specialist, LRQA. “The journey taken together by Shell and LRQA has been technically challenging but immensely rewarding. We have now established a path for anyone to certify additively manufactured pressure equipment under the PED.”
As far as manufacturing is concerned, it should be noted that the AM team leveraged Powder Bed Fusion at the Energy Transition Campus in Amsterdam. The vessel is designed for pressures up to 220 bar.
“Shell will continue to be a leader in the research and development of additive manufacturing,” said Angeline Goh, 3D Printing Technology Lead at Shell. “We collaborate with multiple partners globally to grow our own capabilities and the scope application of 3D printing in the energy sector. We now have the knowledge to also help our partners certify their printed parts for commercialization”.
Remember, you can post job opportunities in the AM Industry on 3D ADEPT Media free of charge or look for a job via our job board. Make sure to follow us on our social networks and subscribe to our weekly newsletter : Facebook, Twitter, LinkedIn & Instagram ! If you want to be featured in the next issue of our digital magazine or if you hear a story that needs to be heard, make sure you send it to contact@3dadept.com