Founded in 2014, Arevo has been operating in stealth mode until 2018, when it unveiled its first 3D printed carbon-fiber eBike. The California-based company develops a robotic additive manufacturing platform for the fabrication of composite parts.
“From the very beginning, we realized that 3D Printing enables efficient automation for manufacturing. Our aim was to leverage this technology to provide the industry with ultra-strong, lightweight composite parts, rapidly and in high-volume”,states Hemant Bheda, Co-founder and Chairman of the company, our guest in this Opinion of the Week series.
Indeed, the aerospace and automotive industries are among the first sectors that pioneered the use of composites in manufacturing. The challenges to address vary from one industry to another. In the automotive industry for instance, developing lightweight and composites structures would result in more energy efficient and environmentally friendly transportation vehicles.
Despite the undeniable benefits, high cost structure, the lack of mass production and automation techniques have limited mass adoption of composite parts.
Arevo’s first application, an additive manufactured composite bike frame validates the benefit of it’s on demand localized manufacturing technology. It’s e-Bike, a battery-assisted bike that integrates a 3D carbon fiber frame. As a reminder, the technology company partnered with OECHSLER, a manufacturer of automotive and medical parts, to adapt their DRIVEMATIC three-speed automatic gearbox to AREVO’s 3D printed carbon fiber frame for an electric 3D printed bike.
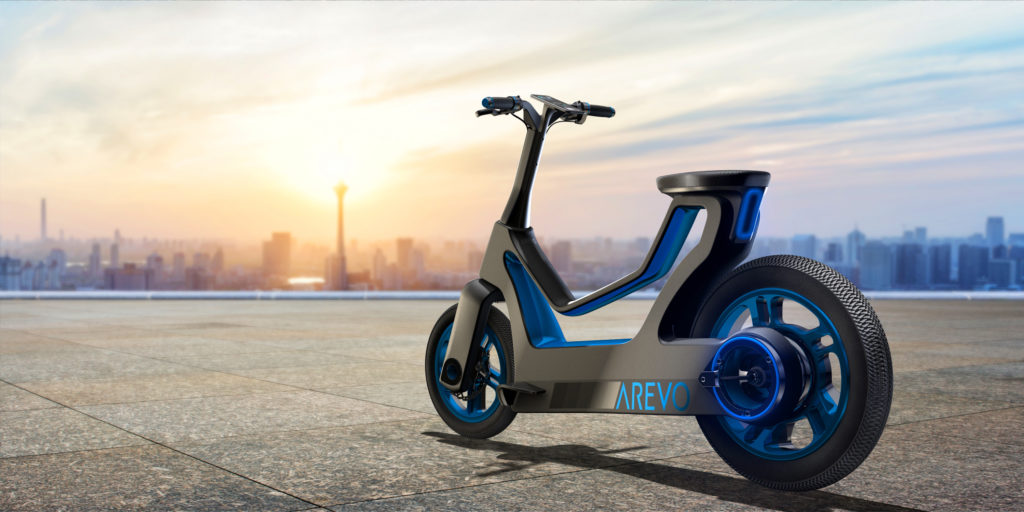
Speaking of the functioning of their robotic AM technology, Bheda points out that their multi-axis robotic arm achieves free-motion deposition. Rather than using a heated nozzle like we usually see in material extrusion processes, Arevo’s technology uses laser to provide rapid heating. That’s how the technology can achieve ‘direct energy deposition’ process for very high deposition rates. Named “Aqua”, the industrial-grade continuous fiber Composite Additive Manufacturing cell is acknowledged today for its ability to print parts of up to one-meter cubic volume.
The development of this electric 3D printed bike therefore, does not only demonstrate the capabilities of Arevo’s technology, but also enables the company to define key strategic areas of focus:
“The 3D carbon-fiber bike frame is the first application we developed with our additive manufacturing technology. This is an exciting opportunity as 2 million composite bike frames are made annually. Today, they are produced as 20 to 30 handmade parts, and glued together. Our mission therefore remains the same: combining the automation capabilities of our technology with the benefits of carbon-fiber to produce a unibody frame on demand while achieving superior performance.
Indeed, carbon-fiber is used as a reinforcement material in composites to enhance plastic performance. The material is stronger than steel but lighter than aluminum. It complies with the biggest requirement any high-performance component should have: strong and lightweight.
To make the most of this material and deposition technology, it was crucial to improve the design cycles. Today, a composite part takes 12 to 18 months from design to production. We developed easy to use software to accelerate design cycles from months to weeks. Our software performs generative design to minimize the use of material and optimize fiber orientations in 3D space for optimum part performance. Our software performs six degrees of freedom, allowing for true 3D additive manufacturing.
Lastly, we bet on manufacturing on-demand. Rather than making uncertain investments, we’ve realized that it is more economical for industrials to fabricate parts only when and where they are needed, hence the recently launch of our MaaS program”, Bheda explains.
MaaS, short for Manufacturing-as-a-Service, is a program designed for Arevo’s partners around the world who will provide on-demand production of ultra-strong, lightweight 3D-printed composite parts.
Those partners are chosen based on their “their expertise and commitment to working in manufacturing of composite parts as well as their geographical location”, outlines the chairman, when asked how the company selects its partners for this program. Japan-based industrial conglomerateAGC Inc.,for example, is the latest-announced partner for this new service. As a partner of Arevo, the company installed the Arevo’s AM technology in its facility and is uniquely positioned to meet the most rigorous manufacturing specifications of the aerospace industry — for primary structures and in other industries such as transport or consumer goods.
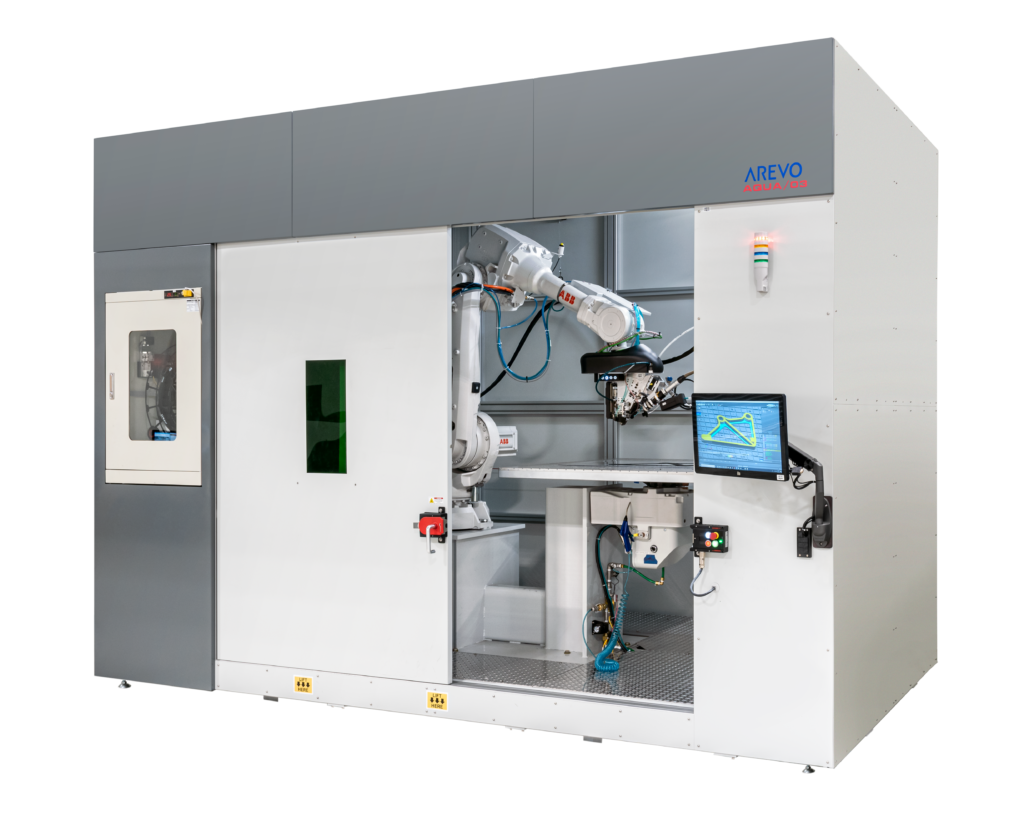
Although it was too soon for Bheda to unveil the company’s future plans, the company’s co-founder confirms that the current crisis has validated their business model: “a crisis usually highlights the strengths and the weaknesses of a system, and especially a company. In our case, I believe it has validated our business model, which is manufacturing-on-demand. Our software can design a production worthy composite part instantly, and with our network of manufacturing cells, we can make this part anywhere in the world cost effectivley.”
“AM has demonstrated its capability to solve many issues we recently faced in combatting the Covid-19 pandemic. The technology can be further leveraged around the world, but automation is crucial to foster its adoption and that’s where Arevo comes into play”, concludes Bheda.
Remember, you can post free of charge job opportunities in the AM Industry on 3D ADEPT Media or look for a job via our job board. Make sure to follow us on our social networks and subscribe to our weekly newsletter : Facebook, Twitter, LinkedIn & Instagram ! If you want to be featured in the next issue of our digital magazine or if you hear a story that needs to be heard, make sure to send it to contact@3dadept.com. Happy New Year!