As part of the additive production of a critical medical component, a defect identified after the post-processing phase made the team lose one HIP cycle, one day of post-processing and quality inspections, not to mention time and money. Analyzing layer images could help to prevent this. The problem is that with thousands of layer images to analyze when searching for errors, it’s easy to miss a critical defect that will result in the non-validation of a part. For good reason: the process is laborious and exhausting for the engineer whose eyes can get tired during the analysis, and data are subjected to different interpretations. To address these challenges, the team at Materialise has developed a solution that could help engineers identify critical defects in a matter of seconds: the Materialise Quality & Process Control (QPC) Layer Analysis software.
Despite the proven advantages of AM, one should acknowledge the fact that different processes and manufacturing conditions can lead to inconsistencies and defects in part quality. To date, defect formation remains a critical challenge for laser powder fusion (LPBF) processes. This challenge is tenfold when one deals with critical applications in highly regulated industries as mentioned in the healthcare example above.
Furthermore, post-processing and quality inspection, one of three major phases of producing AM parts can account for a significant portion of the final production cost, especially in the case of critical aerospace or medical parts – making production teams waste valuable time and money.
This urges engineers to understand defect identification mechanisms, influence and control methods of metal AM defects, all of which constitute the goal of this article. In the end, understanding these issues and how to address them in laser powder bed fusion-based processes is pivotal for prescribing the appropriate process parameters and selected processing techniques. More importantly, it is pivotal to deliver a part that meets the stringent requirements of its industry.
Defect identification
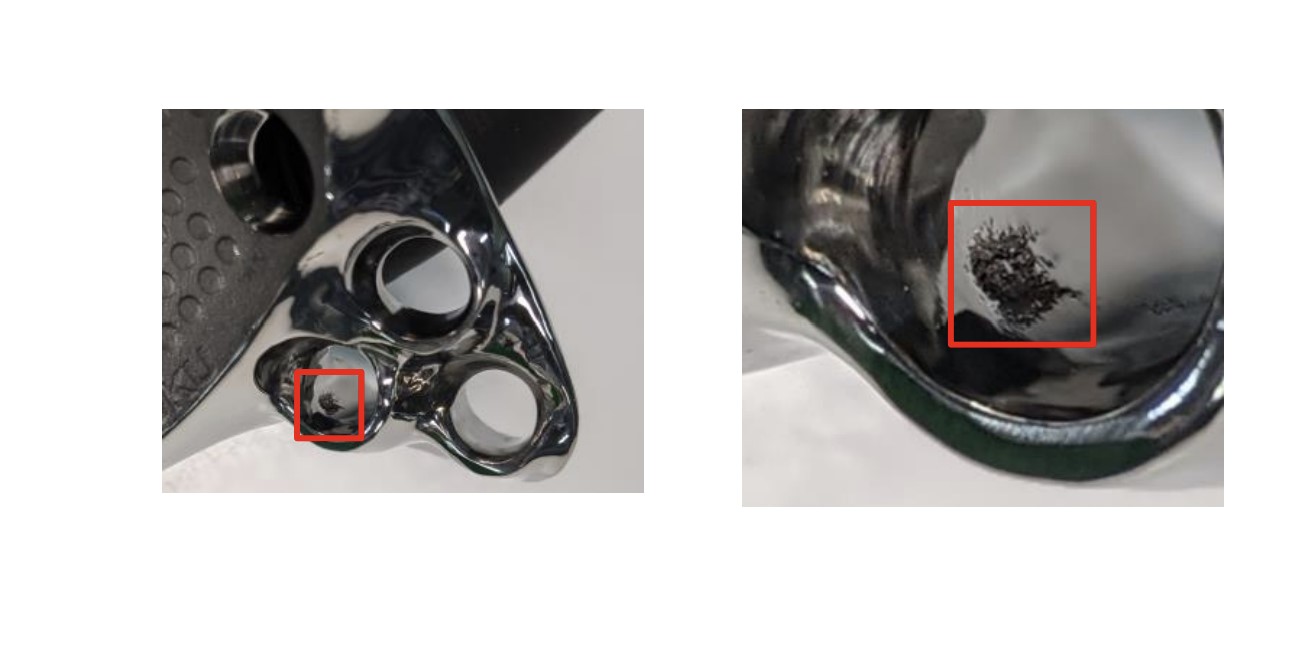
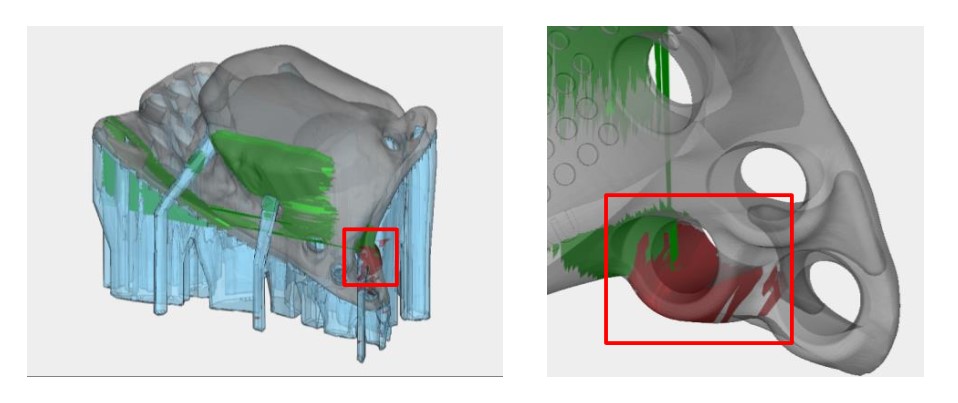
According to Gilles Claeys, Market Development Manager at Materialise, there is a broad range of tools that can be used to identify defects in 3D printed parts and this can be done “by a mix of monitoring and Non-Destructive Testing (NDT), both during the printing process and after the printing process. During the printing, there are multiple sensors in the machine that track the process quality, from monitoring oxygen levels to advanced melt pool monitoring systems. Additionally, a visual-based defect detection approach where the 3D printer will take visual images that will be analyzed during or after printing is – when the analysis is automated – a cheap and fast method for early scrap detection. After the print job, during the quality control process, a visual inspection and NDT methods like CT scans are a couple of methods that can also be leveraged to identify defects.”
As you may have already seen with a lot of challenges faced in the AM industry, there is no one-size-fits-all solution when it comes to tools leveraged for identifying defects. “The exact mix of monitoring and NDT technologies that are used are very much dependent on the application. The types of defects that you want to be detected in a tooling or prototype part will be different from the defects you would want to identify for a medical implant or a flying aerospace 3D printed part. So, this varies from one application to another or from one customer to another,” Claeys explains.
As far as types of defects are concerned, the anomaly that can alter the performance of a metal 3D printed part can be linked to something that happened during the printing process. If you’re working with a laser powder bed fusion process, there is a great chance that you may have already dealt with geometry-related, surface integrity-related and microstructural defects. Some of these defects may be linked to keyhole collapse, gas porosity, solidification cracking, solid-state cracking, or even surface-connected porosity.
For Materialise expert, “there is a wide array of defects that can alter the performance of a metal 3D printed part like cracks, pores, inclusions… The root cause can be something that has failed during the printing process, e.g. due to an uneven distribution of the powder bed or it could be something related to the design or supports of your part. Simulation software can help you reduce the risk upfront but, in the end, you also need to make sure that quality is delivered and that your process and quality remain stable over time.”
What influences defect formation?
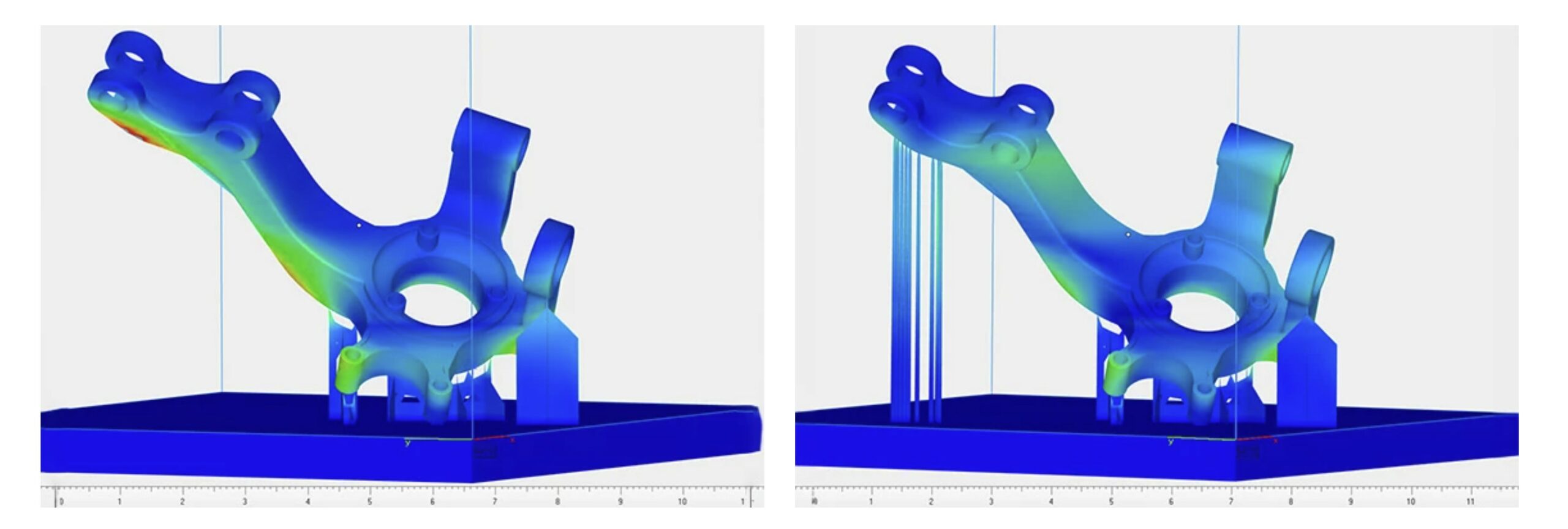
Claeys’ latest argument sheds light on those items that can influence defect formation during the printing process. Designing for AM and simulation are obviously important to try and get right to that first time. Even though simulation helps to reduce the amount of design iterations, many things can still happen in the printing machine that were not foreseen. A defect formation could be linked to a support coming loose during the printing, or it can simply be linked to your recoater dragging particles over the powder bed.
No matter what may influence defect formation, it’s important to keep in mind that a defect identification mechanism aims to explain the reasons why issues directly happen in the printing machine. As Claeys points out, “Your design, build preparation and manufacturing process can all have an impact on the quality of a part. That’s why it’s really important to have a good tool that correlates all these data sources across your entire production chain to find out what is the root cause of what you think is occurring.”
That’s where the Materialise QPC Layer Analysis module comes in.
From hours to minutes: The Materialise QPC Layer Analysis software
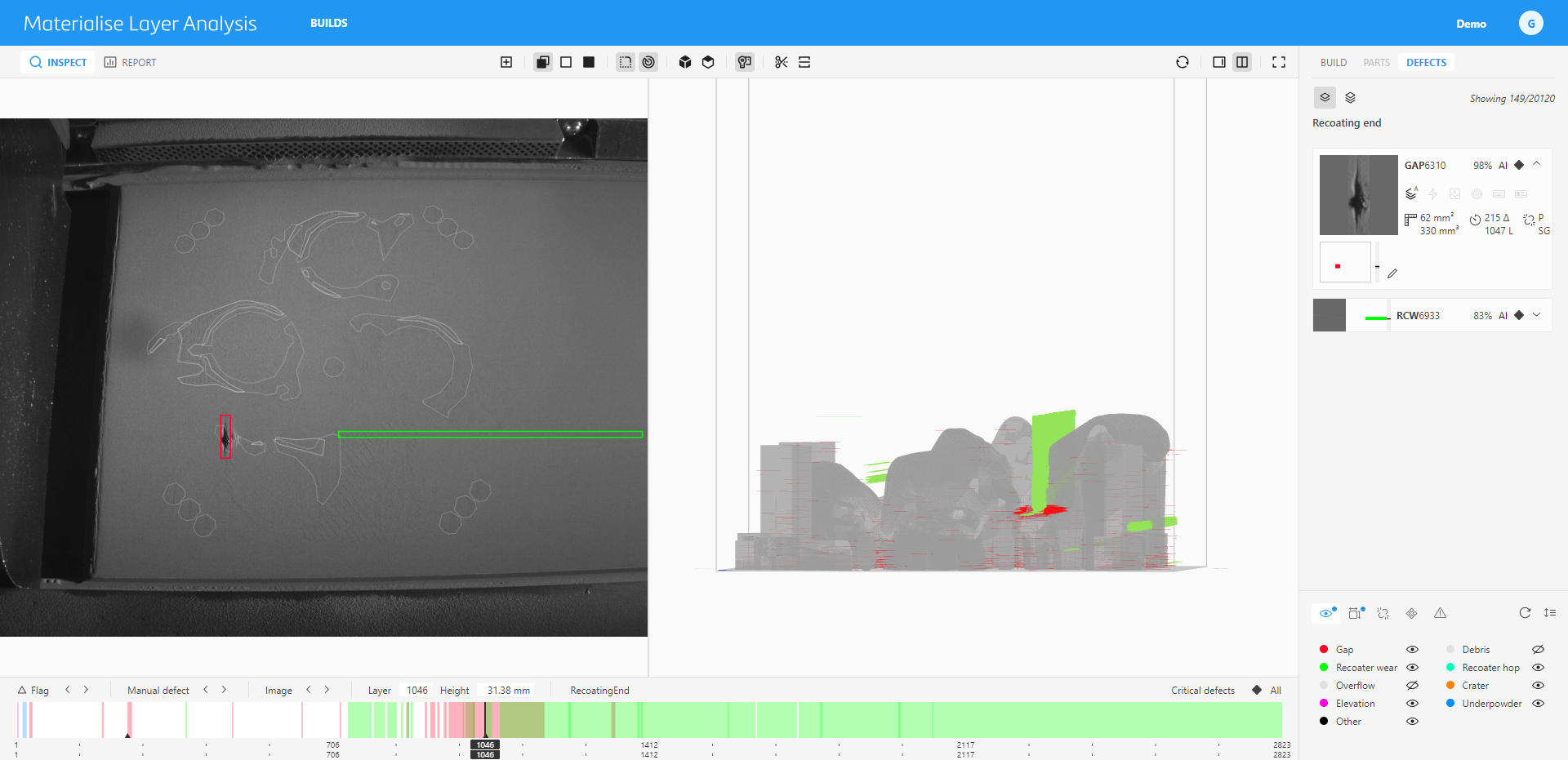
Drawing from the demonstration Claeys performed, the Materialise QPC Layer Analysis software employs artificial intelligence to meticulously inspect layers captured by the cameras on 3D printers. Within a brief timeframe (from seconds to minutes depending on the application), the tool comprehensively scans each layer, pinpointing errors and presenting them visually on both the individual layer and the 3D model.
The Market Development Manager explains that after this step, users receive a summary detailing defects within the build or opt for a meticulous examination of errors, color-coded by category. This feature facilitates root cause analysis, allowing users to discern the specific impacts of each error on the overall construction. This module can also help identify errors that may go unnoticed by the human eye.
We learned with Claeys that the Materialise QPC Layer Analysis software can be used at two main stages:
“At the R&D stage, the Layer Analysis software will help you answer the question “What is the root cause of these defects?”. At this level, for AM users who are not looking to achieve series production yet, the software solution will help them perform an analysis that will help them optimize their process and make sure that they can find the right design and process parameters for their part.
The second stage is the series production. Once you’ve passed the R&D stage, and your product is ready to be printed in a larger volume, then the software solution could also be used to detect deviations in your printing process and to make sure that every 3D printed part meets the production standards.”
By developing the software, the team at Materialise aimed to develop an independent and agnostic solution. Speaking of how this solution stands out from the crowd, Claeys emphasizes on its technology independence:
“The system is hardware agnostic. It is designed in such a way that it can assess visual images from any 3D printer using its integrated visual cameras. This means that the module is easy to get started with as there is no need to install additional hardware inside or outside the build chamber of the metal 3D printer.
Secondly, it facilitates collaborative work for each build. Multiple users can visualize and correlate additional data sources with one another. For example, it is possible to collect multiple data sources like other monitoring systems or CT scans and correlate all these sources together to get a complete overview of the quality of your build plate.”
Beyond these specifications that enable a better understanding of the Materialise QPC Layer Analysis software, one thing I can’t help to stress is the ability to make these defects measurable. If you want to understand how and where you save costs, having clear metrics that help you to do so is for me one of the greatest advantages of any defect detection tool. And that’s something, the Materialise QPC Layer Analysis tool can help you do.
The “fail-fast” mentality
Although the critical medical component has been mentioned as a key example at the beginning of this article, it should be noted that defect detection is critical in all highly regulated industries adopting AM. I see potential interest for applications in the aerospace and space, nuclear and heavy industries which often have to build critical parts.
Last but not least, costs remain one of the reasons brought forward to explain the slow adoption of AM across industries. The Materialise QPC Layer Analysis proves to be a strong tool to address this challenge. In the end, the luckiest guys would be those who have the “fail-fast” mentality as “you can fail fast with AM, but if you’ve found your path, you can grow fast”.
This content has been produced in collaboration with Materialise.
If you have any questions or are interested in getting a demo, get in touch with Materialise at QPC@materialise.com.
Materialise in a few words
Materialise is one of those 3D Printing/AM giants that no longer needs any introduction. With more than three decades of 3D printing experience in a range of software solutions and 3D printing services that empower sustainable 3D printing applications, the company’s open, secure, and flexible end-to-end solutions enable flexible industrial manufacturing and mass personalization in various industries — including healthcare, automotive, aerospace, eyewear, art and design, wearables, and consumer goods. Headquartered in Belgium and with branches worldwide, Materialise combines the largest group of software developers in the industry with one of the world’s largest and most complete 3D printing facilities.