Dans le cadre de la production additive d’un composant médical critique, un défaut identifié après la phase de post-traitement a fait perdre à l’équipe un cycle HIP, une journée de post-traitement, des inspections de qualité, sans parler du temps et de l’argent. L’analyse des images des couches pourrait permettre d’éviter cela. Le problème est qu’avec des milliers d’images de couches à analyser lors de la recherche d’erreurs, il est facile de passer à côté d’un défaut critique qui entraînera la non-validation d’une pièce. Et pour cause : le processus est laborieux, épuisant pour l’ingénieur dont les yeux peuvent se fatiguer pendant l’analyse, et les données sont sujettes à différentes interprétations. Pour relever ces défis, l’équipe de Materialise a développé une solution qui pourrait aider les ingénieurs à identifier les défauts critiques en quelques secondes. Cette solution est le logiciel Materialise Quality & Process Control (QPC) Layer Analysis.
Malgré les avantages avérés de la FA, il faut reconnaître que les différents processus et conditions de fabrication peuvent entraîner des incohérences et des défauts dans la qualité des pièces. À ce jour, la formation de défauts reste un défi majeur pour les procédés de fusion de poudres au laser (LPBF). Ce défi est décuplé lorsqu’il s’agit d’applications critiques dans des secteurs hautement réglementés, comme dans l’exemple des soins de santé ci-dessus.
En outre, le post-traitement et l’inspection de la qualité – en particulier, l’une des trois principales phases de la production de pièces imprimées 3D, peuvent représenter une part importante du coût de production final, en particulier dans le cas de pièces critiques pour l’aérospatiale ou la médecine, ce qui fait perdre aux équipes de production un temps précieux et de l’argent.
Cela incite les ingénieurs à comprendre les mécanismes d’identification des défauts, les méthodes d’influence et de contrôle des défauts de la FA des métaux. En fin de compte, la compréhension de ces questions et la manière de les aborder dans les processus basés sur la fusion laser sur lit de poudre sont essentielles pour prescrire les paramètres de processus appropriés et les techniques de traitement sélectionnées. Plus important encore, il est essentiel de livrer une pièce qui réponde aux exigences rigoureuses de l’industrie.
Identification des défauts
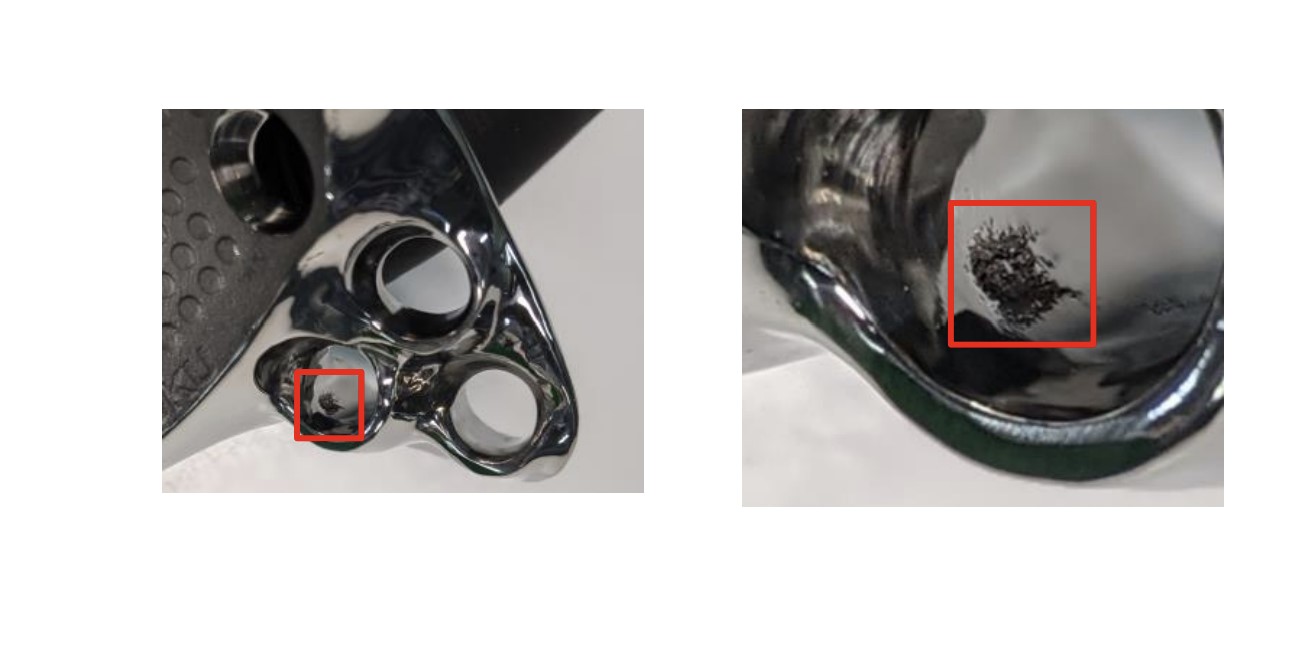
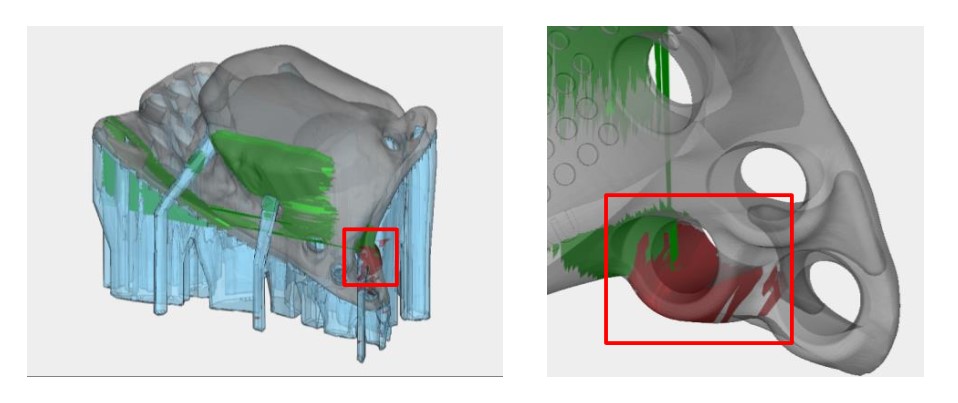
Selon Gilles Claeys, responsable du développement des marchés chez Materialise, il existe une large gamme d’outils qui peuvent être utilisés pour identifier les défauts dans les pièces imprimées en 3D et cela peut être fait « par une combinaison de contrôle et d’essais non destructifs (END), à la fois pendant le processus d’impression et après le processus d’impression. Pendant l’impression, la machine est équipée de multiples capteurs qui contrôlent la qualité du processus, depuis la surveillance des niveaux d’oxygène jusqu’aux systèmes avancés de surveillance du bain de fusion. En outre, une approche de détection visuelle des défauts, dans laquelle l’imprimante 3D prend des images visuelles qui seront analysées pendant ou après l’impression, est – lorsque l’analyse est automatisée – une méthode peu coûteuse et rapide de détection précoce des rebuts. Après l’impression, pendant le processus de contrôle de la qualité, une inspection visuelle et des méthodes de contrôle non destructif comme les tomodensitogrammes sont des méthodes qui peuvent également être utilisées pour identifier les défauts. »
Comme vous l’avez peut-être déjà constaté pour de nombreux défis rencontrés dans l’industrie de la FA, il n’existe pas de solution unique en ce qui concerne les outils utilisés pour identifier les défauts. « La combinaison exacte des technologies de surveillance et de CND utilisées dépend fortement de l’application. Les types de défauts qu’on souhaite détecter dans un outillage ou une pièce prototype seront différents des défauts que l’on souhaite identifier dans un implant médical ou une pièce volante imprimée en 3D pour l’aérospatiale. Cela varie donc d’une application à l’autre ou d’un client à l’autre », explique Claeys. En ce qui concerne les types de défauts, l’anomalie qui peut altérer les performances d’une pièce métallique imprimée en 3D peut être liée à un événement survenu au cours du processus d’impression. Si vous travaillez avec un procédé de fusion laser sur lit de poudre, il y a de fortes chances que vous ayez déjà eu affaire à des défauts liés à la géométrie, à l’intégrité de la surface et à la microstructure. Certains de ces défauts peuvent être liés à l’effondrement des trous de serrure, à la porosité gazeuse, à la fissuration par solidification, à la fissuration à l’état solide ou même à la porosité liée à la surface.
Pour l’expert de Materialise, « il existe un large éventail de défauts qui peuvent altérer les performances d’une pièce métallique imprimée en 3D, comme les fissures, les pores, ou encore les inclusions. La cause première peut être une défaillance au cours du processus d’impression, par exemple en raison d’une distribution inégale du lit de poudre, ou un problème lié à la conception ou aux supports de votre pièce. Les logiciels de simulation peuvent vous aider à réduire le risque en amont mais, en fin de compte, vous devez également vous assurer que la qualité est au rendez-vous et que votre processus et votre qualité restent stables au fil du temps ».
Qu’est-ce qui influence la formation des défauts ?
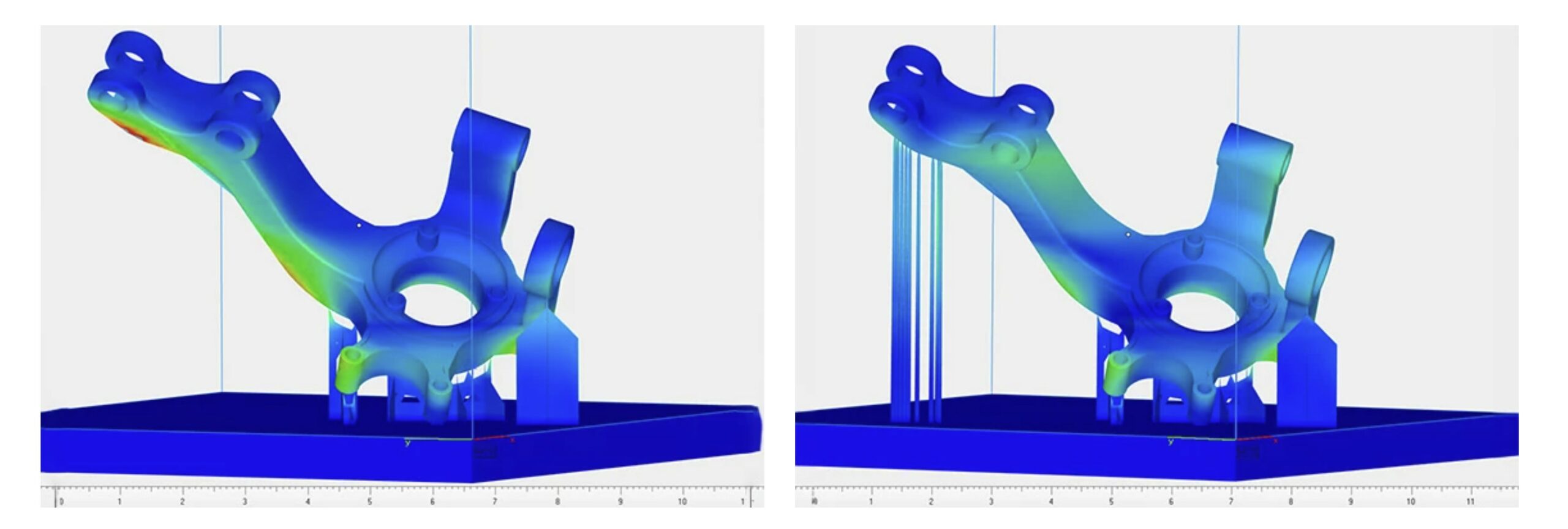
Le dernier argument de Claeys met en lumière les éléments qui peuvent influencer la formation de défauts au cours du processus d’impression. La conception pour la FA et la simulation sont évidemment des éléments importants à prendre en compte dès la première fois. Même si la simulation permet de réduire le nombre d’itérations de conception, de nombreux éléments non prévus peuvent encore se produire dans la machine d’impression. La formation d’un défaut peut être liée à un support qui se détache pendant l’impression, ou simplement au fait que votre recouvreur entraîne des particules sur le lit de poudre.
Quels que soient les facteurs qui influencent la formation des défauts, il est important de garder à l’esprit qu’un mécanisme d’identification des défauts vise à expliquer les raisons pour lesquelles des problèmes surviennent directement dans la machine d’impression.
Comme le souligne Claeys, « la conception, la préparation de la fabrication et le processus de fabrication peuvent tous avoir un impact sur la qualité d’une pièce. C’est pourquoi il est vraiment important de disposer d’un bon outil qui mette en corrélation toutes ces sources de données sur l’ensemble de votre chaîne de production afin de trouver la cause première de ce que vous pensez être en train de se produire. »
C’est là que le module Materialise QPC Layer Analysis entre en jeu.
Des heures aux minutes : Le logiciel Materialise QPC Layer Analysis
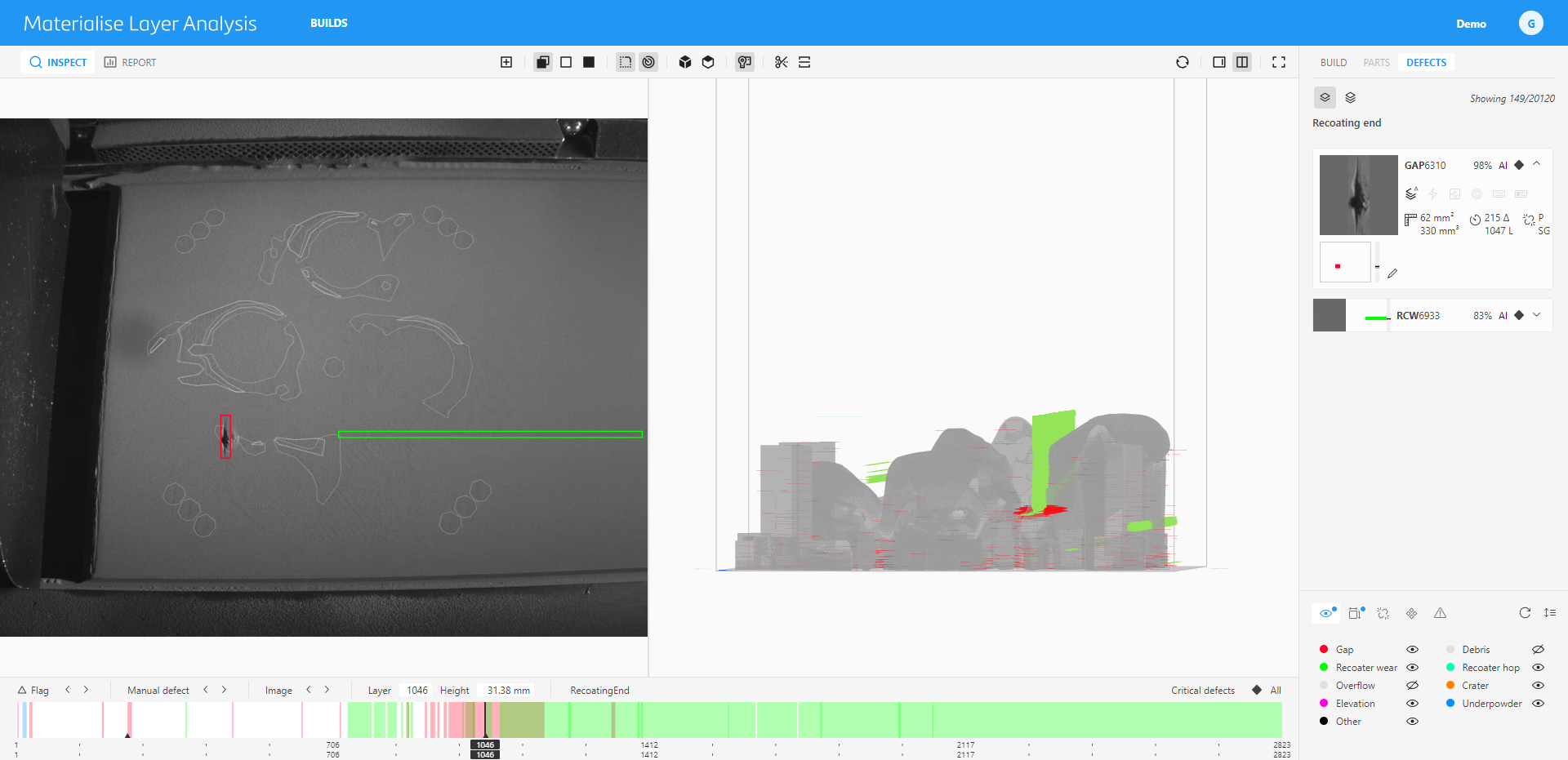
Sur base de la démonstration effectuée par Claeys, on remarque que le logiciel Materialise QPC Layer Analysis utilise l’intelligence artificielle pour inspecter méticuleusement les couches capturées par les caméras des imprimantes 3D. Dans un délai très court (de quelques secondes à quelques minutes en fonction de l’application), l’outil analyse chaque couche de manière exhaustive, identifie les erreurs et les présente visuellement à la fois sur la couche individuelle et sur le modèle 3D.
Le responsable du développement des marchés explique qu’à l’issue de cette étape, les utilisateurs reçoivent un résumé détaillant les défauts de la construction ou optent pour un examen méticuleux des erreurs, avec un code couleur par catégorie. Cette fonction facilite l’analyse des causes profondes, permettant aux utilisateurs de discerner les impacts spécifiques de chaque erreur sur l’ensemble de la construction. Ce module peut également aider à identifier des erreurs qui pourraient passer inaperçues à l’œil nu.
Claeys nous a appris que le logiciel Materialise QPC Layer Analysis peut être utilisé à deux étapes principales :
« Au stade de la R&D, le logiciel Layer Analysis vous aidera à répondre à la question « Quelle est la cause première de ces défauts ?’’. À ce niveau, pour les utilisateurs de la FA qui ne cherchent pas encore à produire en série, la solution logicielle les aidera à effectuer une analyse qui leur permettra d’optimiser leur processus et de s’assurer qu’ils peuvent trouver la bonne conception et les bons paramètres de processus pour leur pièce.
La deuxième étape est la production en série. Une fois que vous avez passé l’étape de la R&D et que votre produit est prêt à être imprimé en plus grand volume, la solution logicielle peut également être utilisée pour détecter les écarts dans votre processus d’impression et pour s’assurer que chaque pièce imprimée en 3D répond aux normes de production. »
En développant le logiciel, l’équipe de Materialise a cherché à mettre au point une solution indépendante et agnostique. En ce qui concerne la manière dont cette solution se distingue, M. Claeys met l’accent sur son indépendance technologique :
« Le système est indépendant du matériel. Il est conçu de manière à pouvoir évaluer les images visuelles de n’importe quelle imprimante 3D à l’aide de ses caméras visuelles intégrées. Cela signifie que le module est facile à utiliser puisqu’il n’est pas nécessaire d’installer du matériel supplémentaire à l’intérieur ou à l’extérieur de la chambre de fabrication de l’imprimante 3D métal.
Deuxièmement, il facilite le travail collaboratif pour chaque construction. Plusieurs utilisateurs peuvent visualiser et mettre en corrélation des sources de données supplémentaires. Par exemple, il est possible de collecter plusieurs sources de données comme d’autres systèmes de surveillance ou des tomodensitogrammes et de corréler toutes ces sources ensemble pour obtenir un aperçu complet de la qualité de votre plaque de construction. »
Au-delà de ces spécifications qui permettent de mieux comprendre le logiciel Materialise QPC Layer Analysis, une chose que je ne peux m’empêcher de souligner est la capacité à rendre ces défauts mesurables. Si vous voulez comprendre comment et où vous économisez des coûts, disposer de mesures claires qui vous aident à le faire est pour moi l’un des plus grands avantages de tout outil de détection des défauts. Et c’est ce que l’outil Materialise QPC Layer Analysis peut vous aider à faire.
La mentalité de « l’échec rapide »
Même si le composant médical critique a été mentionné comme un exemple clé au début de cet article, il convient de noter que la détection des défauts est essentielle dans toutes les industries hautement réglementées qui adoptent la FA. Je vois un intérêt potentiel pour les applications dans l’aérospatiale et l’espace, le nucléaire et les industries lourdes qui doivent souvent fabriquer des pièces critiques.
Enfin, les coûts restent l’une des raisons avancées pour expliquer la lenteur de l’adoption de la FA dans les industries. L’analyse des couches QPC de Materialise s’avère être un outil efficace pour relever ce défi. En fin de compte, les plus chanceux seraient ceux qui ont la mentalité « fail-fast », car « vous pouvez échouer rapidement avec la FA, mais si vous avez trouvé votre voie, vous pouvez croître rapidement ».
Ce contenu a été produit en collaboration avec Materialise.
Si vous avez des questions ou si vous souhaitez obtenir une démonstration, contactez Materialise à l’adresse QPC@materialise.com
Materialise en quelques mots
Materialise est l’un de ces géants de l’impression 3D/FA qui n’a plus besoin d’être présenté. Avec plus de trois décennies d’expérience en impression 3D dans une gamme de solutions logicielles et de services d’impression 3D qui permettent des applications d’impression 3D durables, les solutions ouvertes, sécurisées et flexibles de bout en bout de la société permettent une fabrication industrielle flexible et une personnalisation de masse dans divers secteurs – y compris les soins de santé, l’automobile, l’aérospatiale, les lunettes, l’art et le design, les objets portables et les biens de consommation. Basée en Belgique et disposant de filiales dans le monde entier, Materialise associe le plus grand groupe de développeurs de logiciels de l’industrie à l’une des installations d’impression 3D les plus importantes et les plus complètes au monde.