With a decade of experience in Additive Manufacturing (AM), Honeywell has built a solid reputation as a major developer of commercial aerospace applications enabled by metal AM. Today, the company continues to explore new avenues of technology for its field of activity. Brian Baughman and Curtis Swift took fifty minutes off their busy schedule to walk me through these avenues. They also shared what they find the most challenging in their adoption of AM and how the industrial conglomerate is ready to continue winning billions in this business.
Â
Honeywell may have dedicated facilities in five countries, but the true magic happens in their Phoenix Additive Manufacturing Center. If every year brings its share of joy and lessons, Baughman drew our attention to 5 important dates that have been pivotal in Honeywell’s AM journey.
2008: Like many fellow aerospace companies, Honeywell started investigating the potential of AM through prototyping applications.
“Our goal was to learn about AM, what it could do and what it could not do,” Baughman said. These years saw the development of prototype parts produced in collaboration with external vendors. These years were decisive as they also helped the team understand the economics of the technology and what applications it should tap into to make the most of the technology.
2014 marked the purchase of their first laser powder bed fusion machines– which have remained the primary AM process of the company so far. The purchase comes along with the opening of their AM facility in Phoenix.
2015 saw the completion of the first functional metal 3D printed part.
2016 saw the expansion of that AM facility with an aluminum 3D printing laboratory in Phoenix. As you will see in the “Materials segment” of this edition of 3D ADEPT Mag, aluminum is a preferred metal for aerospace parts due to its lightweight and anticorrosive qualities.
2018 saw the completion of production applications for specific use cases.
The rationale behind the choice of AM technologies

Not surprisingly, laser powder bed fusion technology is the primary AM technology of Honeywell but the company makes use of other technologies like DED, Electron Beam Melting and polymer 3D printing technologies. The main reasons that justify the focus on LPBF are the ability to achieve production-scale manufacturing and consistency in material properties. Baughman explains while making a short comparison with DED – a technology that I believe is also quite advanced for aerospace parts, and for which he had first been hired:
“At the Phoenix metal AM Facility, laser powder bed fusion is the primary focus. We use other technologies like DED but not as extensively as LPBF. The reason for that is that DED is a hard process to control when you’re building up different geometric features. And you tend to have different grain sizes in these features which translate to different material properties. And that’s not great for aerospace. The consistency aerospace requires at the material properties level can more easily be achieved with LPBF. That being said, in our repair business, DED is used to repair the impellers on our engines.”
As for polymer 3D printing, “we don’t have any production parts made in plastics,” Swift acknowledges. “polymer 3D printing is used to support the design of next-generation cockpits, fixtures and testing. When you work in AM, it’s easy to assume that everyone knows about AM but that’s not always the case. Polymer 3D printing is one of these technologies that can help you raise awareness on the potential of AM – whether it is for a customer need or a life sciences project that is not directly related to commercial aerospace applications.”
In addition to these technologies, Honeywell representatives pleasantly surprised me when they said one of the technologies they are currently exploring right now is ceramic 3D printing. If you remember, during the first quarter of the year, we discussed in one of the first editions of 3D ADEPT Mag if ceramic AM can add value to the automotive and aerospace industries. One thing we realized is that the challenges and opportunities are reflected at the materials level, and when it comes to the “High Value vs High Volume” decision. Indeed, the difficulty that comes with creating dense ceramic materials may often limit the applications in this sector to the exploration stage.
“Honeywell uses ceramic 3D printing to create molds for casting. The technology is designed for a specific process.It allows us to cast turbine blades that have extremely accurate dimensions and features,” Swift explains.
“We focus on making hot section turbine components,” Baughman emphasizes. While he didn’t mention what type of ceramic 3D printing they use specifically, he did say the technology had already helped them achieve better efficiency for the production of engine-quality single crystal castings for a blade. “When you perform the casting with a traditional process, it takes about two years to make the tooling and about a million dollars per blade mold. With ceramic 3D printing, we were able to shorten that time to 6 weeks. To achieve that, we spent a lot of time developing our ceramic materials to make them stable so that they would work seamlessly with the casting process.”
“We’re at the forefront of the ceramic 3D printing technology. I don’t know another company that does better than us,” Swift adds.
Overall, one learns with our subject matter experts that the team at Honeywell has been able to find the right opportunity for tooling, production parts, and obsolete parts. Given the number of examples mentioned during our conversation, our guess is that an important ROI lies in the fabrication of production parts.
Challenges across the adoption journey
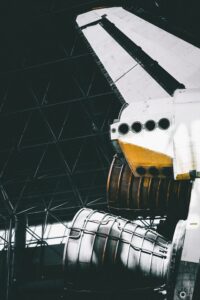
Among the many things I can learn from adopters of AM technologies, I am often keen to discover what they consider the most challenging in their learning curve. Responses obviously vary from one another, but they eventually often help AM technology providers know what they can do better in the way they develop their solutions.
In Honeywell’s case, I came to realize one thing: challenges are also inherent to individuals. In Swift’s view, “3D printing is the easy part. Post-processing is very difficult. Getting a part through to production is lengthy. It’s longer than what people think. But in the midst of all of that, I would say the biggest challenge for me is not having a full library of material properties. As Brian mentioned to me a long time ago, there is an entire library of material properties when you look at casting for traditional processes. In comparison, you only have a couple of boxes with AM. Trying to compete with that difference in material characterization is very difficult.”
For Baughman, this lack of a library of material properties is one of the top three challenges he encountered. “The qualification aspect of AM is also a big challenge. With so many regulatory bodies in the aerospace industry, we have to be able to make products that everyone is comfortable with.” For a given production part, approval must first be made internally, then by the customer and thereafter by the FAA which will certify the part meets the desired criteria.
Baughman also mentioned the cost of the process in this top three. When one compares the traditional manufacturing of a single part vs. its production via AM, AM remains expensive. “There are so many people who want to use AM but the key in using the technology today is not just about finding the right combination between qualification, process and costs; it’s about finding the right opportunity”.
With these two challenges, the Chief Engineer brings to the table two considerations previously discussed by Boeing VP of AM, Melissa Orme. As far as qualification is concerned, we have shared our lessons on how to approach it in the July/August edition of 3D ADEPT Mag. As for the costs, there are a number of tips AM providers have already shared to address the cost consideration, but that’s something we will discuss in another article.
Concluding thoughts
Aerospace might be a major adopter of AM but its progress remains slow for obvious reasons – strict regulations but also materials. Swift opened my eyes to the importance of understanding how the material will perform to be efficient in one’s production and this takes a lot of time.
Furthermore, the rationale behind the choice of every AM and the challenges across the adoption journey might be the main points discussed here but it should be noted that Honeywell has created opportunities across several other crucial areas: enabling supply chain transformation with AM is one that I would like you to keep in mind as the need for flexible supply chains became more pressing with the Covid-19 pandemic.
In the end, no matter what those other areas are, keep in mind Baughman’s strategic thinking if you work in the aerospace industry: your opportunity lies in the right combination of qualification, process and costs.
This interview has first been published in the 2024 September/October of 3D ADEPT Mag. Featured image: Honeywell
Editor’s notes:
Both Swift and Baughman work with Honeywell Aerospace, in the Additive Manufacturing Technology Center located in Phoenix, AZ. Swift is the Senior Additive Manufacturing Engineer whereas Baughman is the Chief Engineer in the AM technology center. Swift started his career in the automotive industry, working with active and passive safety systems, before switching to a Design Engineer role in avionics, as well as plastic 3D printing with the Honeywell Deer Valley location, and is now a Manufacturing Engineer for LPBF Metal 3D printing. Baughman, that I first discovered as the co-author of “Additive Manufacturing of Metals: The Technology, Materials, Design and Production (Springer Series in Advanced Manufacturing)”, held several roles of increasing responsibility in the Aftermarket Repair and Overhaul, Materials and Process Engineering, and Advanced Manufacturing Engineering groups. In a recent role, he was the Manager of Phoenix AM facility, ensuring the prototyping and production applications with AM. His work consists in introducing manufacturing technologies into the company’s manufacturing value chain.