“We [the AM community], have homework to do to earn the credibility as a viable manufacturing technology”, Dr. Melissa Orme, Vice President, Boeing Additive Manufacturing.
I sat down with Dr. Melissa Orme, Vice President, Boeing Additive Manufacturing to discuss another perspective on the use of AM in the aerospace industry.
What I like about Orme’s background, is that she has built up extensive experience in AM between academia, SMEs (contract manufacturers – Morf3D prior to Boeing) and final user (Boeing). This means that not only does AM run through her veins, but she is in a unique position to understand the synergy that must exist between these three stakeholders in order to make AM a viable technology.
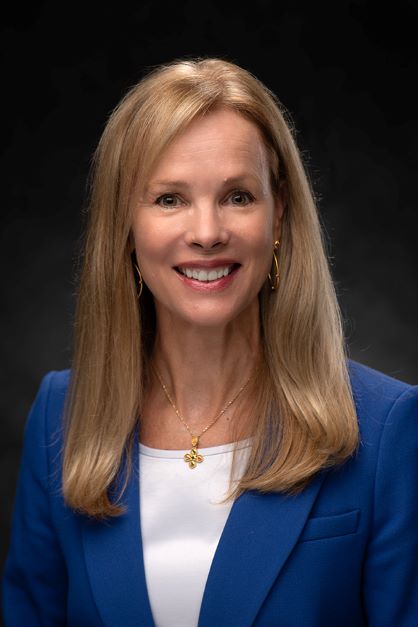
As she explains, “AM is a process-driven technology, where the mechanical attributes of the part are reliant on how it is built, which is not the case with conventional manufacturing, it is important that the final user closely collaborates with the part producer. Many times the part producers and the final users are one in the same. We rely on academia for basic science, or what we call ‘low TRL’* research. It is important that academicians are tied into the equation so that the research they perform drives toward a solution to a problem encountered by the end user”.
‘Low TRL’: Technology readiness level (TRL)*
While this vision should be an indisputable basic process organizations should go through to foster the adoption of AM in a more solution-oriented process, reality is often different.
In the aerospace industry for instance, the use of AM has first been stimulated by legacy systems that had gone out of production – (I am thinking of the Avro 146, or Airbus A310 as examples). For those systems, a small production batch achieved via AM turned out to be less expensive than setting up the original and traditional manufacturing process.
Furthermore, new programmes (re-engine options and new platforms) that were under development within aerospace companies or being fly tested for commissioning drove the developments of AM. For aerospace companies at the time, it made more economic sense to implement the technology this way – rather than investing efforts in existing systems which had only a few years of production left.
That being said, Boeing has always been amid the early adopters of AM. It was actually the first aerospace company to produce 3D printed parts for in-service aircraft and use them in commercial flights. About twenty years ago, the industry player developed an environmental control system duct for the F/A-18, which was later introduced on the Boeing 787. That environmental control system ECS duct was a polymer component developed and produced with Selective Laser Sintering (SLS) machines.
Today, over 70,000 3D-printed production parts fly through Boeing commercial and defense programs (AM Insight, Statistics, Boeing – Q4, 2019). Looking back, we can legitimately say the technology has evolved from research and development projects and low-cost tooling to printing high volumes of high-value metallic components and large families of tools.
Looking forward, it seems that there is still a long way to go when we look at the roadmap for AM workflow integration. How long? For Orme, the “length of the roadmap depends on the application and the regulator. Different regulators have different requirements in the number and types of tests performed. However, what is common with most regulators is the following: for aerospace and defense, we need to show that our process is stable and repeatable. Stability and repeatability is the holy grail in Additive Manufacturing. Different regulators have different ways of determining stable and repeatable processes. One of the challenges in achieving stable and repeatable processes is that the machines are still produced as one-offs, making it difficult to have two of the same machines providing the same results within the small level of variation that the aerospace industry requires. Issues like this make scale with quality difficult, but not impossible.”
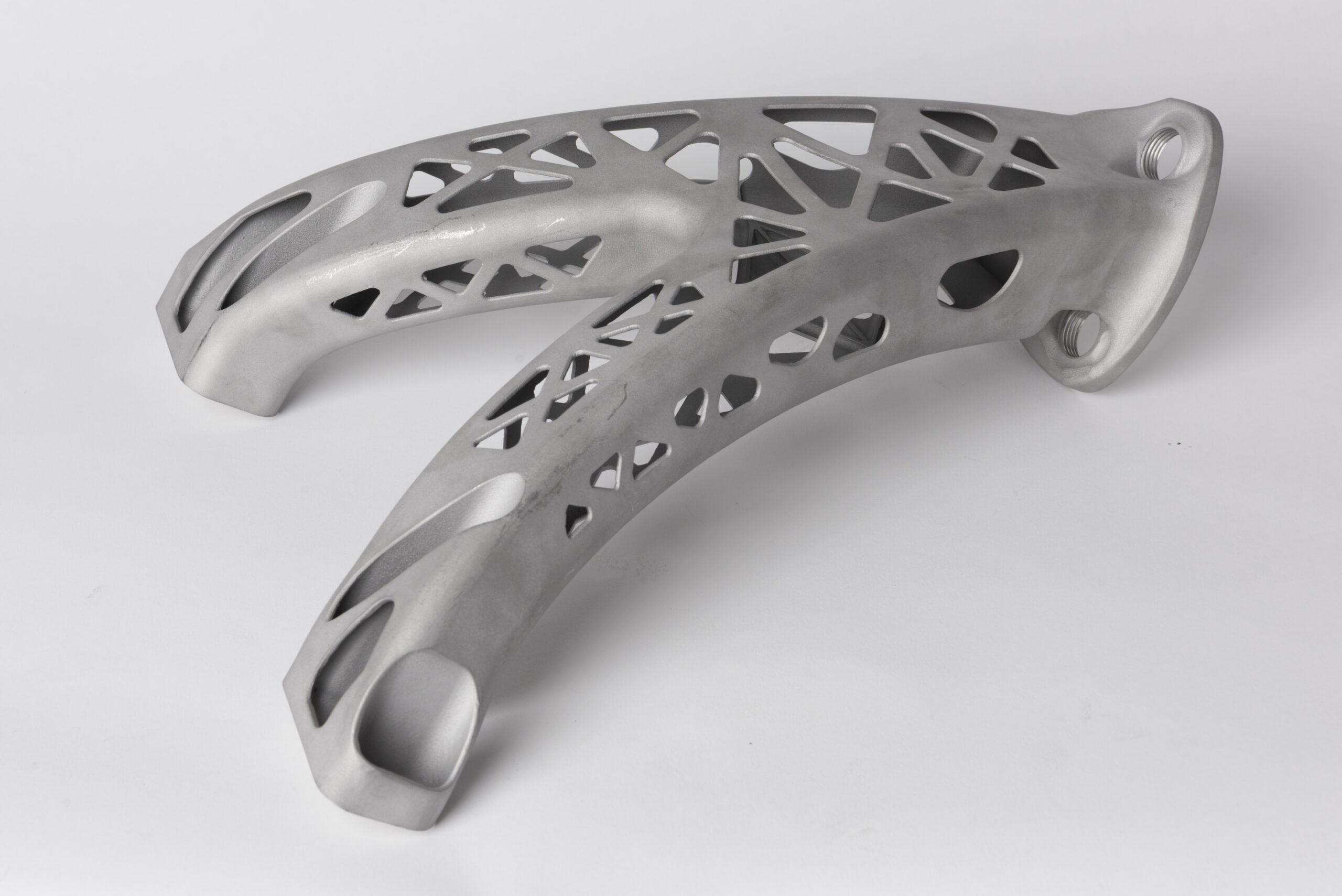
Yet Aerospace companies (be it part producers or final users) continue to invest in AM. Neff told 3D ADEPT Media that “It can be frustrating, but to get there you have to invest in the void. It can be hard to do for some organizations because it requires a lot of money, time and dedication to see value and that’s a risk many do not want to take.”
Orme unconsciously completes her statement by reminding of the “immense value that AM can bring”. “For example, it enables the design for parts that are built to fit into small and odd shapes in the vehicle, reducing overall volume. Aerospace companies see that AM creates the possibility to optimize the vehicle, not just the part. It provides the opportunity to create differentiating vehicles, providing a competitive advantage. It is also very important to mention that AM produces positive sustainability trades, which is a key focus for Boeing, as it is for all aerospace and defence”, she adds.
As we assess the challenges that may arise when implementing this roadmap, we come to realize that, industry stakeholders necessarily take into account three main considerations.
Considerations to take into account in the roadmap for AM workflow integration in the aerospace industry
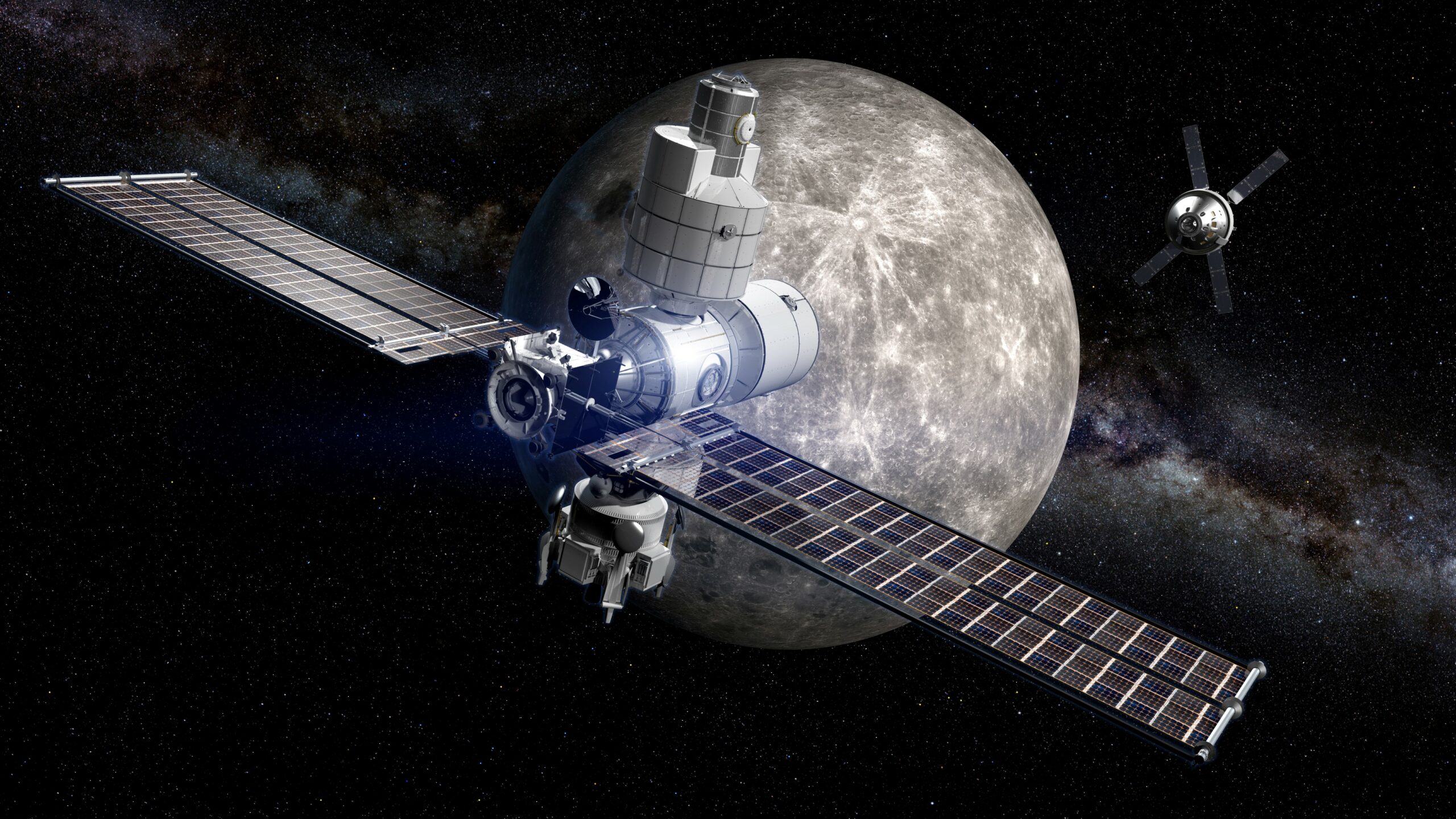
Those considerations involve the economic standpoint, the conservative nature of Aerospace as well as the cost consideration.
The economic element brings us back to an argument we discussed with Neff. Rising production needs around the world continuously impact the way the business of aerospace and defence is transacted globally. And aerospace players such as Lockheed Martin, Airbus, Boeing, Northrop Grumman, and others who are at the forefront of commercial operations, spearhead new trade considerations. Needless to say, the current economic environment brought forth by the pandemic, requires us to be careful about how we do business. It may be difficult to have a general assessment of how this environment has impacted the aerospace manufacturing industry, but for Boeing there has been a positive turnaround.
“This is because we were able to focus much of our Additive Manufacturing work towards our Boeing Defense and Space division where we printed literally thousands of parts for satellites, drones, and vertical lift applications”, the Vice President notes. Orme hints at the growing applications where they will further explore the potential of AM. (Indeed, the company previously shared that it will grow the capabilities of AM — “in particular for its Millennium Space Systems subsidiary focused on the smallsat market, where 3D printing is proving to be an especially good fit for deploying systems on orbit faster than ever before”).
In the meantime, the division also doubled down on maturing their internal core competency in Additive Manufacturing through the research that they perform and the databases that they create to demonstrate stable and repeatable performance. During all of this time – Orme states – speaking of what they achieved during the peak of the pandemic, “our commercial airplane Additive Manufacturing applications continued along their development path and we plan for our first production airplane parts fabricated from powder bed fusion to be delivered one year from now.”
On another note, when it comes to accelerating the adoption of 3D printed parts in a vertical industry, cost – bringing down the cost per part – remains a touchy topic and that makes for a difficult conversation I often have with machine manufacturers regardless of the segment (3D printers, post-processing, etc.). Interestingly, the question is not only a matter of those who produce the AM technologies. As a final user, Boeing believes they also have their part to play in this conversation.
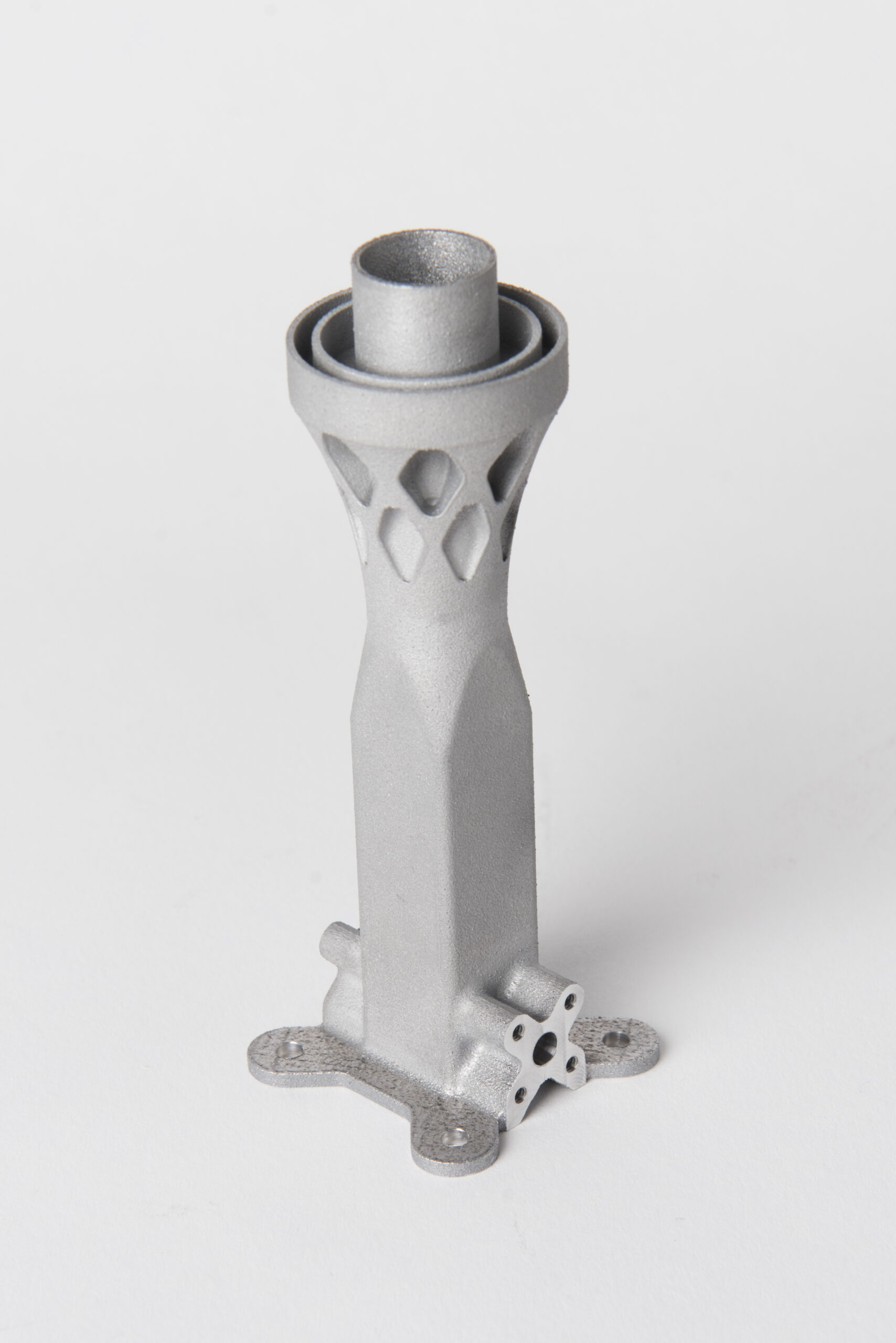
“We understand that our initial efforts into the additive arena will require a lot of developmental research. In the beginning, that research will be absorbed into part cost. We also understand that AM is not a « commodity. » We see true value in the innovation that AM allows. For example, some innovative solutions will likely consolidate many parts into one, which will enhance production. Some innovative solutions will be multifunctional, so that a structural element may also be heat exchanger, or may also be an electrical component. We may use AM to streamline our products so they produce less drag, requiring less fuel and making it cheaper and cleaner to operate. This will contribute to our sustainability goals. We have also found that we’ve reduced a program schedule by many months using additive solutions. This is a tremendous cost saving. So although the individual part may cost more, the overall savings to the program outweighs that cost”, Orme points out.
The last consideration to take into account – the conservative nature of the aerospace industry – refocuses the debate on the “application vs regulator” argument highlighted above. Where I see limitations, Orme sees opportunity to earn real credibility. She does not deny this conservative nature and wouldn’t have it any other way. Most importantly, she calls on the duty of the entire AM community to make sure that [AM] “can earn the credibility as a viable manufacturing technology”.
“In order to earn that credibility, we have homework to do. Additive Manufacturing does not enjoy decades of data that conventional manufacturing does. We need to make sure that we understand any risk associated with AM and that we know how to mitigate that risk. Only then will engineers opt to design for the additive solution and then we will find it easy to integrate AM solutions onto the airplane”, our guest concludes.
This exclusive dossier has first been published in the 2022 January/February issue of 3D ADEPT Mag.
Remember, you can post job opportunities in the AM Industry on 3D ADEPT Media free of charge or look for a job via our job board. Make sure to follow us on our social networks and subscribe to our weekly newsletter : Facebook, Twitter, LinkedIn & Instagram ! If you want to be featured in the next issue of our digital magazine or if you hear a story that needs to be heard, make sure to send it to contact@3dadept.com