« Nous [la communauté de la FA] avons du pain sur la planche pour donner à la fabrication additive la crédibilité en tant que technologie de fabrication viable », Dr. Melissa Orme, vice-présidente de Boeing Additive Manufacturing.
J’ai rencontré le Dr Melissa Orme, vice-présidente de Boeing Additive Manufacturing, pour discuter d’un autre point de vue sur l’utilisation de la FA dans l’industrie aérospatiale. Ce que j’apprécie dans le parcours d’Orme, c’est qu’elle a acquis une vaste expérience de la FA entre le monde universitaire, les PMEs (fabricants sous contrat – Morf3D avant Boeing) et l’utilisateur final (Boeing). Cela signifie que non seulement la FA coule dans ses veines, mais qu’elle est dans une bonne position pour comprendre la synergie qui doit exister entre ces trois parties prenantes afin de faire de la FA une technologie viable.
Comme elle l’explique, « la FA est une technologie axée sur le processus, où les attributs mécaniques de la pièce dépendent de la manière dont elle est construite, ce qui n’est pas le cas de la fabrication conventionnelle. Bien souvent, les producteurs de pièces et les utilisateurs finaux ne font qu’un. Nous comptons sur le monde universitaire pour la science fondamentale, ou ce que nous appelons la recherche « low TRL « *. Il est important que les universitaires soient associés à l’équation afin que la recherche qu’ils effectuent permette de trouver une solution à un problème rencontré par l’utilisateur final ».
« Low TRL » : Niveau de préparation technologique (TRL) | en anglais : Technology readiness level (TRL)*
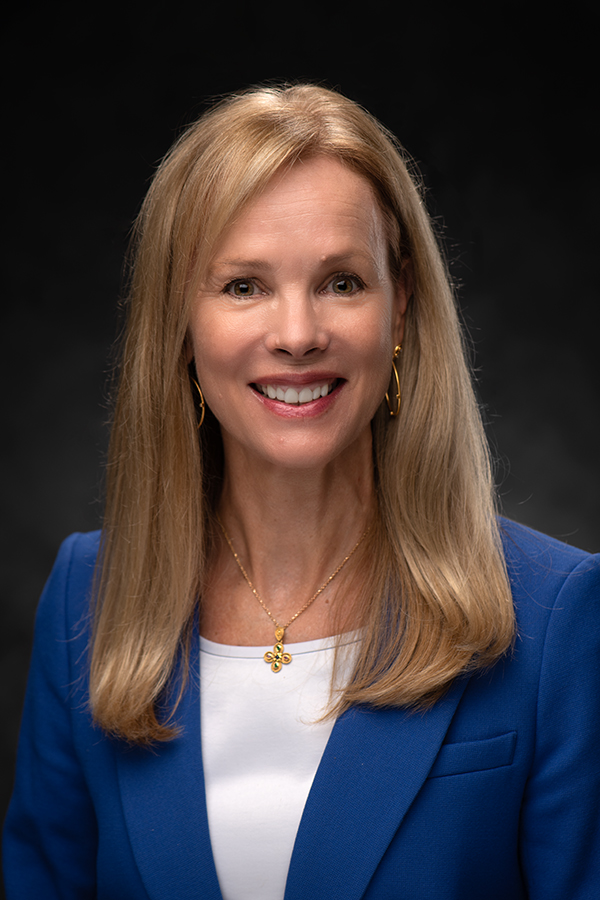
Alors que cette vision devrait constituer un processus de base indiscutable que les organisations devraient suivre pour favoriser l’adoption de la FA dans un processus plus orienté vers les solutions, la réalité est souvent différente.
Dans l’industrie aérospatiale, par exemple, l’utilisation de la FA a d’abord été stimulée par des systèmes hérités qui avaient cessé d’être produits (je pense par exemple à l’Avro 146 ou à l’Airbus A310). Pour ces systèmes, un petit lot de production réalisé par FA s’est avéré moins coûteux que la mise en place du processus de fabrication original et traditionnel.
En outre, les nouveaux programmes (options de remaniement et nouvelles plates-formes) en cours de développement au sein des entreprises aérospatiales ou faisant l’objet d’essais en vol en vue de leur mise en service ont stimulé le développement de la FA. Pour les entreprises aérospatiales de l’époque, il était plus judicieux, d’un point de vue économique, de mettre en œuvre la technologie de cette manière, plutôt que d’investir des efforts dans des systèmes existants qui n’avaient plus que quelques années de production.
Cela dit, Boeing a toujours fait partie des premiers adeptes de la FA. C’était en fait la première entreprise aérospatiale à produire des pièces imprimées en 3D pour des avions en service et à les utiliser dans des vols commerciaux. Il y a une vingtaine d’années, cet acteur du secteur a mis au point un conduit de système de contrôle environnemental pour le F/A-18, qui a ensuite été introduit sur le Boeing 787. Ce conduit de système de contrôle environnemental ECS était un composant polymère développé et produit avec des machines de frittage laser sélectif (SLS).
Aujourd’hui, plus de 70 000 pièces de production imprimées en 3D volent à travers les programmes commerciaux et de défense de Boeing (AM Insight, Statistics, Boeing – Q4, 2019). Avec le recul, nous pouvons légitimement dire que la technologie a évolué, passant de projets de recherche et développement et d’outillage à faible coût à l’impression de volumes élevés de composants métalliques de grande valeur et de grandes familles d’outils.
Pour ce qui est de l’avenir, il semble qu’il y ait encore un long chemin à parcourir si on considère la feuille de route pour l’intégration du flux de production de FA. Combien de temps ? Pour Orme, la « longueur de la feuille de route dépend de l’application et du régulateur. Chaque organisme de réglementation a des exigences différentes en ce qui concerne le nombre et les types de tests à réaliser. Cependant, ce qui est commun à la plupart des régulateurs est le suivant : pour l’aérospatiale et la défense, nous devons montrer que notre processus est stable et répétable. La stabilité et la répétabilité sont le Saint Graal de la fabrication additive. Les différents organismes de réglementation ont des méthodes différentes pour déterminer les processus stables et reproductibles. L’un des défis à relever pour parvenir à des processus stables et reproductibles est que les machines sont toujours produites en tant qu’exemplaires uniques, ce qui fait qu’il est difficile d’avoir deux machines identiques fournissant les mêmes résultats avec le faible niveau de variation requis par l’industrie aérospatiale. De tels problèmes rendent difficile, mais pas impossible, la mise à l’échelle de la qualité. »
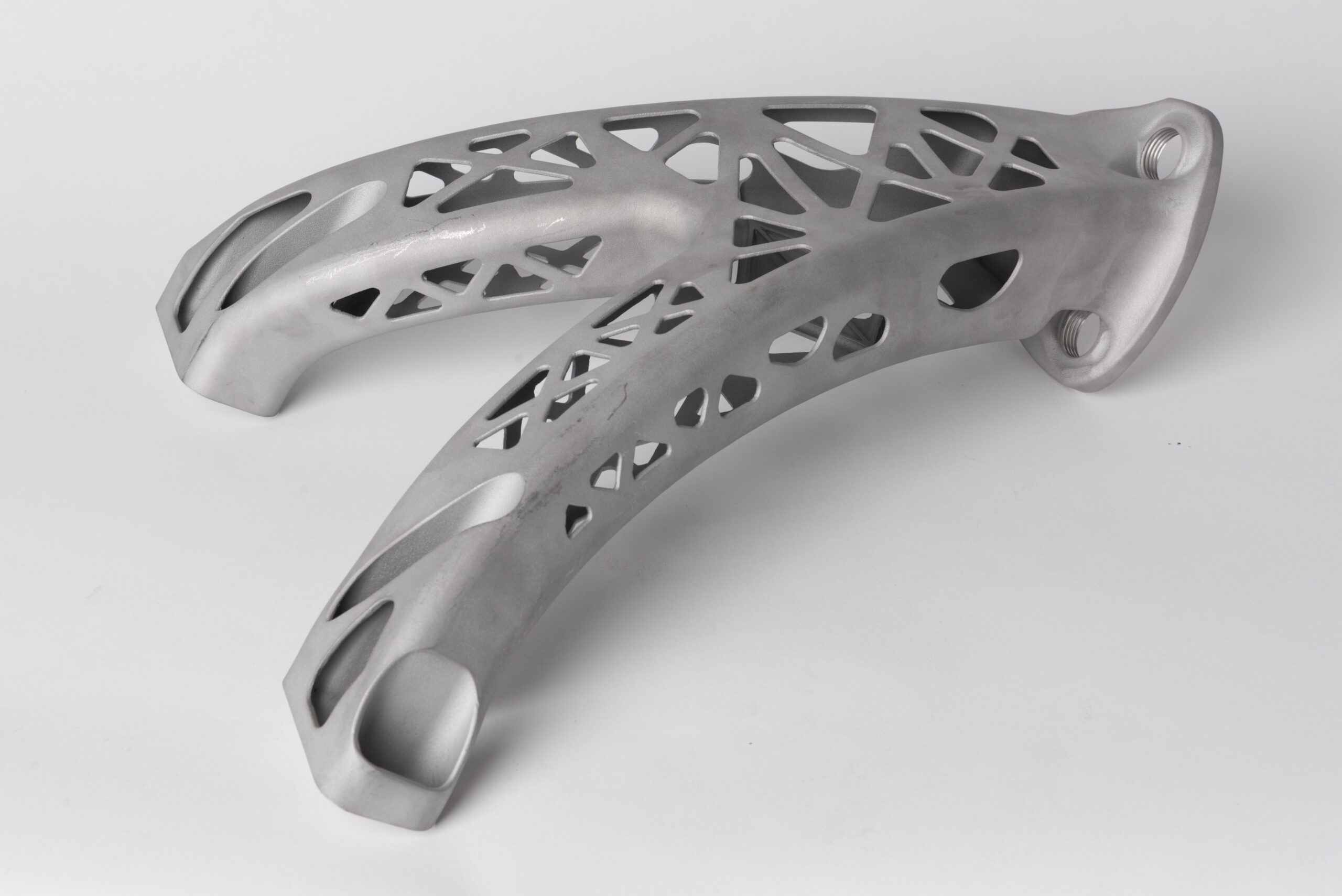
Pourtant, les entreprises du secteur aérospatial (qu’il s’agisse de producteurs de pièces ou d’utilisateurs finaux) continuent d’investir dans la FA. Neff a déclaré à 3D ADEPT Media (Interview avec Sintavia –) que « Cela peut être frustrant, mais pour y arriver, il faut investir dans le vide. Cela peut être difficile à faire pour certaines organisations car il faut beaucoup d’argent, de temps et de dévouement pour en voir la valeur et c’est un risque que beaucoup ne veulent pas prendre. »
Orme complète inconsciemment son propos en rappelant « l’immense valeur que peut apporter la FA ». « Par exemple, elle permet de concevoir des pièces qui sont construites pour s’adapter à des formes petites et impaires dans le véhicule, réduisant ainsi le volume global. Les entreprises aérospatiales voient que la FA offre la possibilité d’optimiser le véhicule, et pas seulement la pièce. Elle permet de créer des véhicules différenciés, offrant ainsi un avantage concurrentiel. Il est également très important de mentionner que la FA produit des échanges positifs en matière de durabilité, ce qui est un point essentiel pour Boeing, comme pour l’ensemble de l’aérospatiale et de la défense », ajoute-t-elle.
En évaluant les défis qui peuvent se présenter lors de la mise en œuvre de cette feuille de route, nous nous rendons compte que les acteurs de l’industrie doivent nécessairement prendre en compte trois considérations principales.
Considérations à prendre en compte dans la feuille de route pour l’intégration des flux de FA dans l’industrie aérospatiale
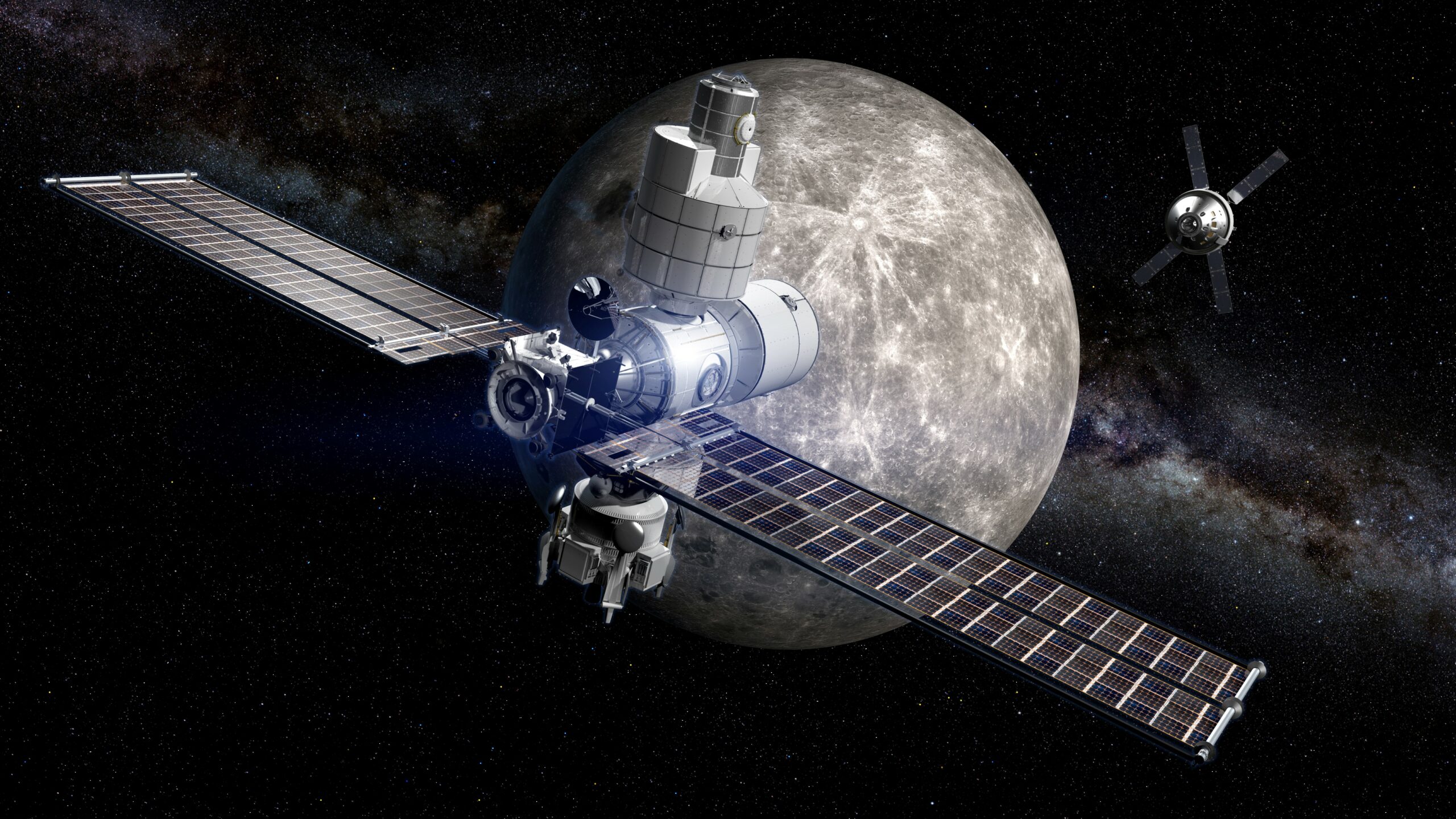
Ces considérations impliquent le point de vue économique, la nature conservatrice de l’aérospatiale ainsi que la considération des coûts.
L’élément économique nous ramène à un argument dont nous avons discuté avec Neff. L’augmentation des besoins de production dans le monde entier a un impact continu sur la façon dont les affaires de l’aérospatiale et de la défense sont traitées au niveau mondial. Et les acteurs de l’aérospatiale tels que Lockheed Martin, Airbus, Boeing, Northrop Grumman et d’autres, qui sont à l’avant-garde des opérations commerciales, sont le fer de lance de nouvelles considérations commerciales. Il va sans dire que l’environnement économique actuel, provoqué par la pandémie, nous oblige à faire attention à la manière dont nous faisons des affaires. Il peut être difficile d’avoir une évaluation générale de l’impact de cet environnement sur l’industrie de la fabrication aérospatiale, mais pour Boeing, il y a eu un revirement positif.
« Cela est dû au fait que nous avons pu concentrer une grande partie de nos travaux de fabrication additive sur notre division Boeing Defense and Space, où nous avons imprimé littéralement des milliers de pièces pour des satellites, des drones et des applications de levage vertical », note la vice-président. Orme fait allusion aux applications croissantes pour lesquelles l’entreprise va continuer à explorer le potentiel de la fabrication additive. (En effet, l’entreprise a déjà annoncé qu’elle allait développer les capacités de la FA – « en particulier pour sa filiale Millennium Space Systems, axée sur le marché des petits satellites, où l’impression 3D s’avère particulièrement adaptée pour déployer des systèmes en orbite plus rapidement que jamais »).
Dans le même temps, la division a également redoublé d’efforts pour développer ses compétences internes en matière de fabrication additive par le biais des recherches qu’elle effectue et des bases de données qu’elle crée pour démontrer la stabilité et la reproductibilité des performances. Pendant tout ce temps – déclare M. Orme – en parlant de ce qu’ils ont réalisé au plus fort de la pandémie, « nos applications de fabrication additive pour les avions commerciaux ont poursuivi leur chemin de développement et nous prévoyons la livraison de nos premières pièces d’avion de production fabriquées par fusion sur lit de poudre dans un an. »
Dans un autre ordre d’idées, lorsqu’il s’agit d’accélérer l’adoption de pièces imprimées en 3D dans une industrie verticale, le coût – la réduction du coût par pièce – reste un sujet sensible et cela donne lieu à une conversation difficile que j’ai souvent avec les fabricants de machines, quel que soit le segment (imprimantes 3D, post-traitement, etc.). Il est intéressant de noter que la question ne concerne pas seulement ceux qui produisent les technologies de FA. En tant qu’utilisateur final, Boeing estime qu’il a également son rôle à jouer dans cette conversation.
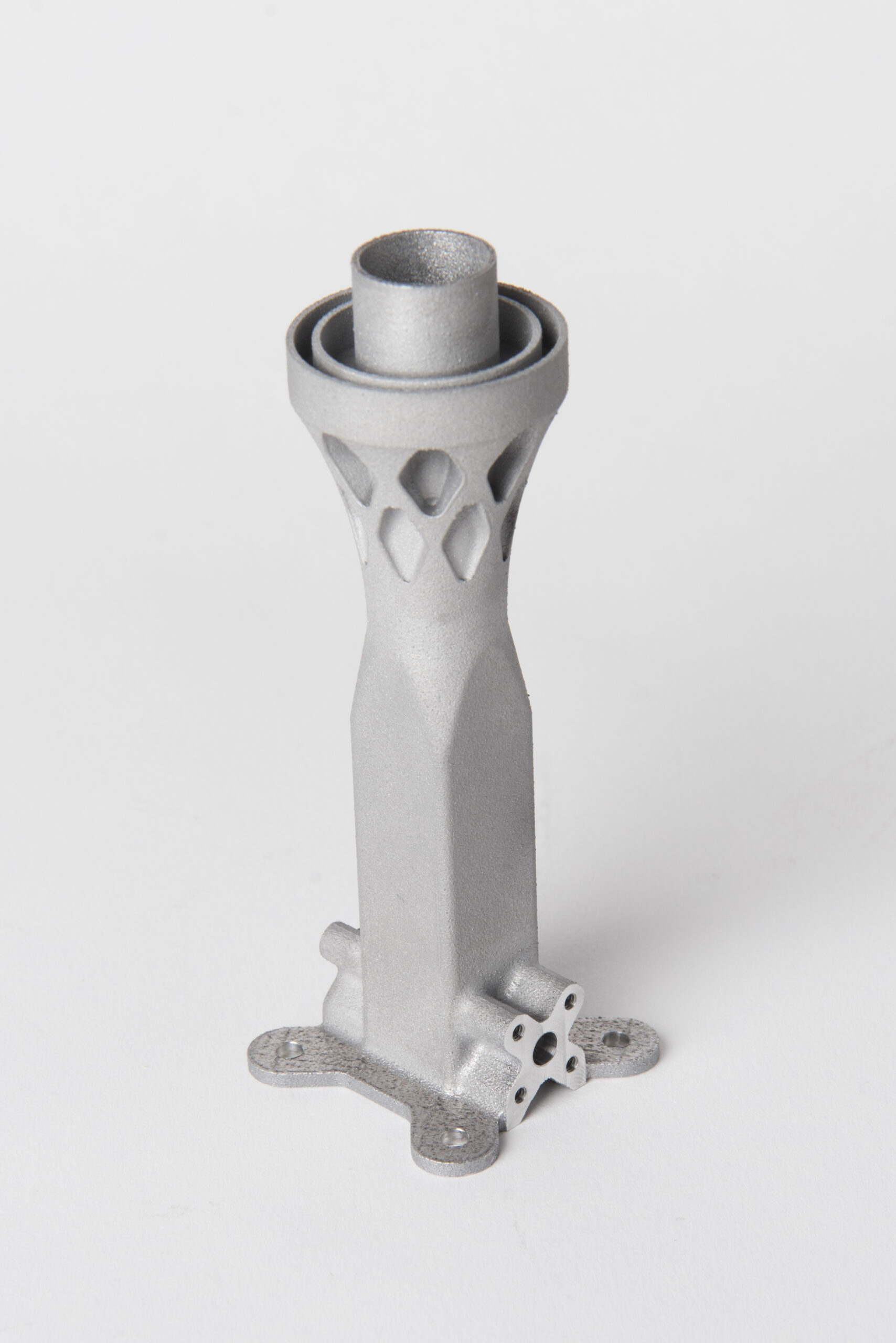
« Nous comprenons que nos premiers efforts dans le domaine de la FA nécessiteront beaucoup de recherche de développement. Au début, cette recherche sera absorbée par le coût des pièces. Nous comprenons également que la FA n’est pas une » marchandise « . Nous voyons une véritable valeur dans l’innovation que permet la FA. Par exemple, certaines solutions innovantes permettront probablement de consolider de nombreuses pièces en une seule, ce qui améliorera la production. Certaines solutions innovantes seront multifonctionnelles, de sorte qu’un élément structurel pourra également être un échangeur de chaleur ou un composant électrique. Nous pourrons utiliser la FA pour rationaliser nos produits afin qu’ils produisent moins de traînée, ce qui nécessitera moins de carburant et rendra leur fonctionnement moins coûteux et plus propre. Cela contribuera à nos objectifs de durabilité. Nous avons également constaté que nous avons réduit le calendrier d’un programme de plusieurs mois en utilisant des solutions additives. Il s’agit d’une économie de coûts considérable. Ainsi, même si la pièce individuelle coûte plus chére, les économies globales réalisées sur le programme l’emportent sur ce coût », souligne Orme.
La dernière considération à prendre en compte – la nature conservatrice de l’industrie aérospatiale – recentre le débat sur l’argument « application contre régulateur » souligné plus haut. Là où je vois des limites, Orme voit l’opportunité de gagner une réelle crédibilité. Elle ne nie pas cette nature conservatrice et ne voudrait pas qu’il en soit autrement. Plus important encore, elle appelle au devoir de l’ensemble de la communauté de FA de s’assurer que [la FA] « peut gagner la crédibilité d’une technologie de fabrication viable ».
« Afin de gagner cette crédibilité, nous avons des devoirs à faire. La fabrication additive ne bénéficie pas de décennies de données comme la fabrication conventionnelle. Nous devons nous assurer que nous comprenons tout risque associé à la fabrication additive et que nous savons comment atténuer ce risque. Ce n’est qu’alors que les ingénieurs choisiront de concevoir en fonction de la solution additive et qu’il sera facile d’intégrer des solutions de fabrication additive dans les avions », conclut notre invité.