Fondée en 2014, Arevo a fonctionné en mode furtif jusqu’en 2018, date à laquelle la société a dévoilé son premier eBike en fibre de carbone imprimé en 3D. L’entreprise californienne développe une plateforme robotisée de fabrication additive pour la fabrication de pièces composites.
« Dès le début, nous avons réalisé que l’impression 3D permet une automatisation efficace de la fabrication. Notre objectif était de tirer parti de cette technologie pour fournir à l’industrie des pièces composites ultra résistantes et légères, rapidement et en grand volume », déclare Hemant Bheda, co-fondateur et président de la société, notre invité dans cette série « Opinion de la Semaine ».
En effet, les industries aérospatiale et automobile sont parmi les premiers secteurs qui ont utilisé des composites dans la fabrication. Les défis à relever varient d’une industrie à l’autre. Dans l’industrie automobile, par exemple, le développement de structures légères et composites permettrait d’obtenir des véhicules de transport plus efficaces sur le plan énergétique et plus respectueux de l’environnement.
Malgré les avantages indéniables, la structure des coûts élevés, le manque de production de masse et de techniques d’automatisation ont limité l’adoption en masse de pièces en composites.
La première application d’Arevo, un cadre de vélo en composite fabriqué par FA, valide l’avantage de sa technologie de fabrication localisée à la demande. Il s’agit de l’e-Bike, un vélo assisté par batterie qui intègre un cadre 3D en fibre de carbone. Pour rappel, l’entreprise technologique s’est associée à OECHSLER, fabricant de pièces automobiles et médicales, pour adapter sa boîte automatique à trois vitesses DRIVEMATIC au cadre en fibre de carbone imprimé 3D d’AREVO pour un vélo électrique imprimé 3D.
En parlant du fonctionnement de leur technologie robotique FA, Bheda souligne que leur bras robotique multi-axes permet un dépôt en mouvement libre. Plutôt que d’utiliser une buse chauffée comme on le voit habituellement dans les procédés d’extrusion de matériaux, la technologie d’Arevo utilise le laser pour assurer un chauffage rapide. C’est ainsi que la technologie permet d’obtenir un processus de « dépôt direct d’énergie » pour des taux de dépôt très élevés. Baptisée « Aqua« , la cellule de fabrication additive composites à fibres continues de qualité industrielle est aujourd’hui reconnue pour sa capacité à imprimer des pièces d’un volume cubique allant jusqu’à un mètre.
Le développement de ce vélo électrique imprimé en 3D ne démontre donc pas seulement les capacités de la technologie d’Arevo, mais permet également à l’entreprise de définir des domaines stratégiques clés :
« Le cadre du vélo 3D en fibre de carbone est la première application que nous avons développée avec notre technologie de fabrication additive. Il s’agit d’une opportunité passionnante puisque 2 millions de cadres de vélo en composite sont fabriqués chaque année. Aujourd’hui, ils sont produits sous forme de 20 à 30 pièces faites à la main, et collées ensemble. Notre mission reste donc la même : combiner les capacités d’automatisation de notre technologie avec les avantages de la fibre de carbone pour produire un cadre monocoque à la demande tout en obtenant des performances supérieures.
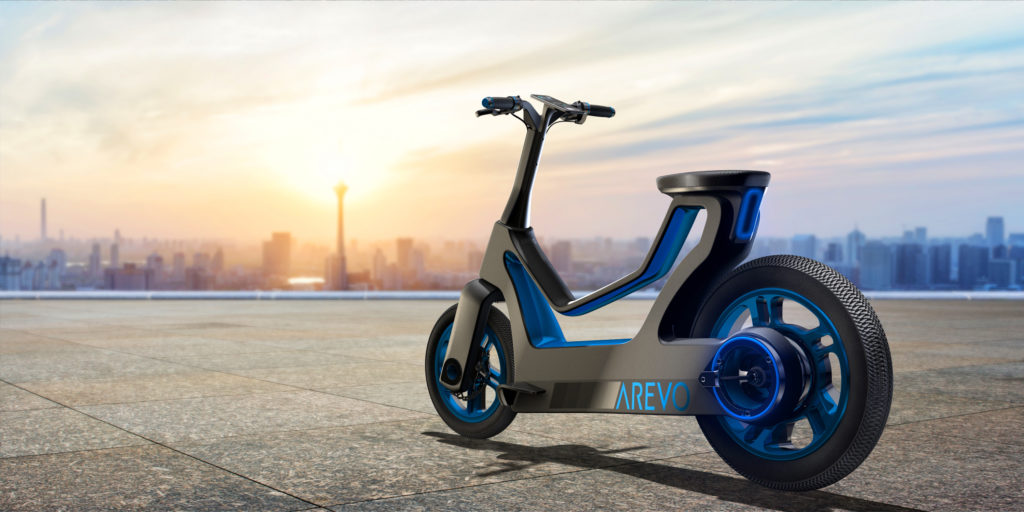
En effet, la fibre de carbone est utilisée comme matériau de renforcement dans les composites pour améliorer les performances des plastiques. Ce matériau est plus résistant que l’acier mais plus léger que l’aluminium. Il répond à la plus grande exigence qu’un composant à haute performance devrait avoir : la solidité et la légèreté.
Pour tirer le meilleur parti de ce matériau et de la technologie de dépôt, il était crucial d’améliorer les cycles de conception. Aujourd’hui, une pièce composite prend de 12 à 18 mois, de la conception à la production. Nous avons développé un logiciel facile à utiliser pour accélérer les cycles de conception, qui passent de quelques mois à quelques semaines. Notre logiciel effectue une conception générative pour minimiser l’utilisation de matériau et optimiser l’orientation des fibres dans l’espace 3D pour une performance optimale de la pièce. Notre logiciel offre six degrés de liberté, ce qui permet une véritable fabrication additive en 3D.
Enfin, nous parions sur la fabrication à la demande. Plutôt que de faire des investissements incertains, nous avons réalisé qu’il est plus économique pour les industriels de ne fabriquer les pièces que quand et où elles sont nécessaires, d’où le lancement récent de notre programme MaaS », explique Bheda.
MaaS, abréviation de Manufacturing-as-a-Service, est un programme conçu pour les partenaires d’Arevo dans le monde entier qui fourniront la production à la demande de pièces composites ultra résistantes et légères imprimées en 3D.
Ces partenaires sont choisis en fonction de « leur expertise et de leur engagement à travailler dans la fabrication de pièces composites ainsi que de leur situation géographique », souligne le président, lorsqu’on lui demande comment la société choisit ses partenaires pour ce programme. Le conglomérat industriel AGC Inc. basé au Japon, par exemple, est le dernier partenaire annoncé pour ce nouveau service. En tant que partenaire d’Arevo, l’entreprise a installé la technologie de FA d’Arevo dans ses installations et se trouve dans une position unique pour répondre aux spécifications de fabrication les plus rigoureuses de l’industrie aérospatiale — pour les structures primaires et dans d’autres industries comme le transport ou les biens de consommation.

Bien qu’il est trop tôt pour que Bheda dévoile les plans futurs de la société, le co-fondateur de l’entreprise confirme que la crise actuelle a validé leur modèle d’entreprise : « une crise met généralement en évidence les forces et les faiblesses d’un système, et surtout d’une entreprise. Dans notre cas, je pense qu’elle a validé notre modèle d’entreprise, qui est la fabrication à la demande. Notre logiciel peut concevoir instantanément une pièce composite digne d’être produite, et grâce à notre réseau de cellules de fabrication, nous pouvons fabriquer cette pièce partout dans le monde de manière rentable ».
« La FA a démontré sa capacité à résoudre de nombreux problèmes auxquels nous avons récemment été confrontés dans la lutte contre la pandémie de Covid-19. La technologie peut être exploitée davantage dans le monde entier, mais l’automatisation est cruciale pour favoriser son adoption et c’est là qu’Arevo entre en jeu », conclut Bheda.
N’oubliez pas que vous pouvez poster gratuitement les offres d’emploi de l’industrie de la FA sur 3D ADEPT Media ou rechercher un emploi via notre tableau d’offres d’emploi. N’hésitez pas à nous suivre sur nos réseaux sociaux et à vous inscrire à notre newsletter hebdomadaire : Facebook, Twitter, LinkedIn & Instagram ! Si vous avez une innovation à partager pour le prochain numéro de notre magazine numérique ou si vous avez un article à faire connaître, n’hésitez pas à nous envoyer un email à contact@3dadept.com. Bonne année !