Il y a deux types de personnes qui travaillent avec des pièces imprimées en 3D : celles qui savent comment gérer les structures de support et celles qui ne le savent pas. L’année dernière, à Formnext, en me promenant dans les allées, j’ai vu quelques pièces fabriquées sans structures de support et quelques autres où elles semblaient nécessaires. Cela m’a fait réfléchir : l’opérateur devrait-il élaborer une stratégie en matière de « structures de support » ?
Le mot « stratégie » est peut-être un peu fort, mais dans le domaine de la fabrication additive, je me suis rendu compte qu’en dépit de la philosophie « out of the box » prônée, tout doit être pensé à deux fois, y compris les choses auxquelles on s’attend le moins.
Dans ce cas, les mots « structures de support » eux-mêmes sont assez explicites. Décrites par de nombreux acteurs de l’industrie comme un « mal nécessaire », il existe des structures qui soutiennent votre composant pendant le processus de fabrication additive. L’objectif ? Faire en sorte que la pièce sorte de l’imprimante 3D sans déformation due à un affaissement. Néanmoins, le processus de réflexion préalable vaut la peine d’être mené une fois que vous réalisez qu’elles peuvent en fait affecter le prix de votre pièce.
L’article ci-dessous a pour but de discuter :
- Quels processus de FA peuvent conduire à la formation de structures de support (SS) – au cas où vous ne connaîtriez pas la FA – et surtout, pourquoi en avons-nous besoin ?
- Quel est le coût à prendre en considération ?
- Et comment devrions-nous aborder une stratégie de « structures de support » ?
Quels processus de gestion de la FA peuvent conduire à la formation de structures de support (SS) et pourquoi en avons-nous besoin ?
Quels processus de FA peuvent conduire à la formation de structures de support (SS) et pourquoi en avons-nous besoin ?
Ailette de turbine produite à l’aide de supports de rupture. Crédit : 3D Adept. Images prises sur le stand de 3D Systems à Formnext 2022.
Tout d’abord, des « structures de support sont nécessaires pour relier les pièces à la plaque de construction ». En l’absence de connexion, la machine à recouvrir pousserait le matériau fondu vers une autre position. En outre, les supports sont nécessaires pour absorber les tensions matérielles qui se produisent pendant la solidification du matériau fondu. En outre, les structures de support dissipent la chaleur de la pièce vers la plaque de base et évitent ainsi la surchauffe, affirme d’emblée Dominik Maurer, TRUMPF Additive Manufacturing, Application and Process Development (fabrication additive, développement d’applications et de processus).
Toute personne ayant un peu d’expérience dans l’impression 3D FDM a peut-être déjà eu l’occasion d’utiliser les SS. Étant donné que le processus technologique consiste à déposer couche après couche de filament, chaque nouvelle couche doit être soutenue par celle qui se trouve en dessous. C’est de la physique !
Cette raison de « fixation » s’applique également à la SLA et à d’autres technologies à base de résine telles que la DLP et la LCD.
Il est surprenant de constater que si les SS ne sont pas nécessaires pour la technologie SLS, ils le sont pour le procédé DMLS (Direct Metal Laser Sintering). En outre, compte tenu des températures élevées dans le volume de construction, ils garantissent également une dissipation uniforme de la chaleur.
Il va sans dire que la formation de SS implique certaines spécifications propres à chaque technologie :
« Les structures de support sont nécessaires pour différentes raisons en fonction de la technologie, et dans certains cas, elles ne sont pas nécessaires du tout. Par exemple, dans le frittage sélectif laser (SLS), il n’y a pas de structures de support, les pièces flottent librement dans la poudre de construction adjacente, ce qui permet de construire des pièces complexes avec peu de compromis géométriques.
Dans le cas de la stéréolithographie (SLA), c’est-à-dire de la méthode descendante sans membrane basée sur la cuve, des supports très minimes sont nécessaires car le processus de construction est largement flottant, et les supports que vous utilisez sont très fins, efficaces en termes de matériaux et faciles à retirer. En général, ils sont nécessaires pour initier, stabiliser et fixer avec précision les sections transversales émergentes. Avec la SLA, il est possible d’obtenir des surfaces très peu profondes et de grandes portées autoportantes.
Lorsqu’une membrane est introduite, comme c’est le cas pour les systèmes DLP, LCD et certains systèmes à base de laser, les supports deviennent plus robustes, en fonction du type de membrane et de la nature de la géométrie.
Avec les systèmes FDM et/ou les systèmes d’extrusion plastique généraux, les supports sont assez étendus car vous construisez dans l’air et les effets de la gravité ainsi que la tension du processus provenant des formes de refroidissement nécessitent des ancrages étendus. Cela dit, il existe des astuces qui vont de la modification de la conception à des réglages spéciaux du processus pour interagir avec les interfaces afin de réduire la densité et d’améliorer le processus d’enlèvement.
Dans le cas de l’impression directe sur métal (DMP), les supports sont en fait multifonctionnels. Non seulement ils sont généralement nécessaires pour initier la géométrie suspendue, mais ils remplissent en fait deux fonctions : d’une part, ils servent de dispositifs de fixation pour maintenir les sections transversales à partir de l’accumulation de contraintes pendant le processus de construction et, d’autre part, ils permettent de transférer la chaleur hors de la géométrie pendant le processus de construction.
Dans le cas de l’impression directe sur métal (DMP), les supports sont en fait multifonctionnels. Non seulement ils sont généralement nécessaires pour initier la géométrie suspendue, mais ils remplissent en fait deux fonctions : d’une part, ils servent de dispositifs de fixation pour maintenir les sections transversales au sol contre l’accumulation de contraintes pendant le processus de construction et, d’autre part, ils permettent de transférer la chaleur hors de la géométrie pendant le processus de construction.
Récemment, alors que les ingénieurs comprennent mieux la physique complexe impliquée dans la fusion et la resolidification des métaux en poudre, nous avons assisté à des changements remarquables dans la réduction des supports, au point qu’il est souvent possible de se débarrasser de la plus grande partie d’entre eux. Cela a un impact considérable sur la consommation de matériaux, les temps de construction et la main-d’œuvre en aval. Mais c’est sur la conception que l’impact est le plus important. La philosophie « Le meilleur support est l’absence de support » – rendue possible par le développement de processus avancés et le contrôle du niveau vectoriel – élargit l’espace de conception. La conception est une proposition de valeur fondamentale de la FA », déclare Patrick Dunne, vice-président du groupe d’intégration des applications de 3D Systems.
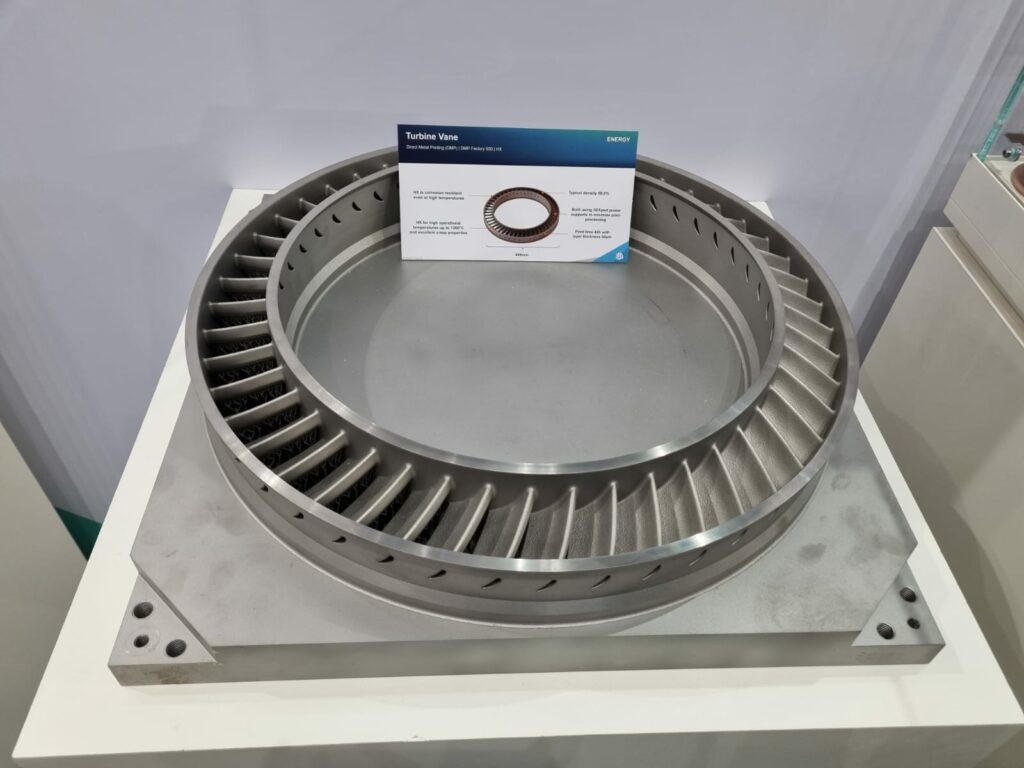
Quelle est cette considération de coût ?
On nous dit souvent que le post-traitement est l’étape de fabrication qui augmente le coût final de la pièce imprimée en 3D. En disant cela, il peut être facile de négliger les autres considérations (mineures) qui continuent d’augmenter le coût final.
Prenons l’exemple du FDM : comme les SS nécessitent du matériel d’impression supplémentaire, cela augmente d’une certaine manière le coût de production au sein de ce processus. Sans oublier que quiconque dit SS implique un travail supplémentaire au niveau du post-traitement, et ce, quel que soit le processus de FA utilisé, ce qui se traduit par un coût final plus élevé de la pièce.
Par ailleurs, alors que nous insistons de plus en plus sur la nécessité de mettre en place des processus de fabrication plus « verts », rappelons que la SS signifie aussi, d’une certaine manière, plus de « déchets de matériaux« . « Certains matériaux nécessitent plus de support que d’autres en raison de différences dans les contraintes internes du matériau lors de la solidification. Par exemple, de nombreux alliages d’aluminium nécessitent peu de supports par rapport à des matériaux soumis à de fortes contraintes comme les alliages de titane », explique Maurer.
Le problème, c’est que le processus de fabrication étant le principal moteur des SS, les ingénieurs n’ont qu’une seule solution pour éviter ou minimiser leur formation : améliorer la conception de leurs pièces. Une idée que Dunne confirme : « [la] présence [de SS] est due à la combinaison du matériel et du processus de fabrication, des matériaux, de la conception de la pièce et, bien sûr, de l’orientation de la construction. La combinaison de la DfAM avec une orientation optimale et des capacités de contrôle fin des processus peut les réduire massivement – dans certains cas jusqu’à zéro ».
La stratégie de “ structures support ”
Puisque tout commence dans le logiciel, l’adoption d’une stratégie SS par le biais de la DfAM signifie que l’ingénieur doit intégrer le SS dans la conception de manière à remplir de multiples fonctions.
« Idéalement, cela se fait en concevant les pièces sans surfaces critiques en surplomb qui doivent être soutenues. Traditionnellement, toutes les surfaces présentant un angle de dépassement inférieur à 45° par rapport à la plaque de base devaient être soutenues. Grâce à des paramètres de processus intelligents pour les zones en surplomb (les « paramètres de la peau descendante »), il est désormais possible d’imprimer des angles en surplomb jusqu’à environ 25° sans aucune structure de support. Avec des ajustements spéciaux des paramètres de la peau descendante, il est parfois même possible d’imprimer des angles allant jusqu’à 10° sans aucune structure de support. Étant donné que la qualité de surface de ces surfaces à faible angle est comparativement mauvaise et que les paramètres spéciaux de la couche inférieure s’accompagnent souvent d’un temps d’impression supplémentaire, les surfaces inférieures à 25° doivent encore être évitées dans la conception de la pièce, si possible », explique Maurer.
En prenant l’exemple spécifique du LPBF où le besoin de structures de support dépend en particulier de la géométrie de la pièce et du matériau d’impression, il ajoute spécifiquement :
« D’une manière générale, la conception des pièces doit être adaptée au processus LPBF. Il existe de nombreuses directives telles que les épaisseurs de paroi minimales, les diamètres de trou maximaux ou l’angle sans support le plus bas. Chez TRUMPF, nous proposons des formations à la conception pour le procédé LPBF aux ingénieurs concepteurs internes et externes afin de leur permettre de sélectionner les pièces LPBF potentielles.
Dans la plupart des cas, la conception des pièces est réalisée à l’aide d’un logiciel de CAO conventionnel. Les concepteurs disposent de nombreuses fonctions utiles pour optimiser leurs pièces pour le procédé LPBF et pour réduire les structures de support. Mais ces fonctions ne remplacent pas la compréhension générale des directives de conception pour le LPBF de l’ingénieur concepteur ».
Cela semble être beaucoup de contraintes pour une technologie qui devrait permettre la « liberté de conception« . Si parfois, l’expérience holistique enseigne les meilleures leçons, voici quelques idées que nous aimerions que vous considériez :
- Utilisez une solution logicielle qui permet de contrôler les supports de vos pièces imprimées en 3D.
- Assurez le contrôle des paramètres de construction dans la zone de surplomb de la pièce.
- Selon l’expert de 3D Systems, des astuces simples comme l’auto propagation de caractéristiques qui n’ont pas besoin de supports ou même l’adoption de supports permanents et intégrés peuvent être très utiles. En intégrant les supports dans la conception et en les laissant en place, vous supprimez la main-d’œuvre nécessaire en aval
- Sinon, le contrôle in situ peut être une autre option. En utilisant un système de revêtement sans contact, par exemple, l’ingénieur peut supprimer le besoin de supports.
- Une solution intéressante a été présentée au salon Formnext 2022 par le fabricant de machines Duplex. En imprimant en 3D par le dessus de la pièce et par le dessous en même temps, la tête d’impression 3D inférieure devient une réponse au support puisqu’elle est essentiellement le SS. Comme vous pouvez le voir dans la vidéo, la buse elle-même soutient les éléments en surplomb lors de leur fabrication.
- Enfin, un autre exemple récent apparu sur le marché concerne la gestion thermique du bain de fusion. Avec sa solution Free Float, par exemple, SLM Solutions offre aux utilisateurs la possibilité de choisir entre différents profils en fonction de la qualité de la pièce et de l’élimination du support souhaitée.
Conclusion
Les SS constituent sans aucun doute un domaine de développement intéressant pour la FA, car de nouvelles solutions sont mises au point pour parvenir à une fabrication « sans support ». Même si elles peuvent affecter la conception, le matériau et même les décisions de post-traitement en FA, elles renforcent l’idée qu’il n’existe pas de solution « unique » en FA.
Ce dossier a été publié dans le numéro de Juillet/Août 2023 de 3D ADEPT Mag.