Dans un secteur comme celui de la fabrication additive (FA), il y a tellement d’esprits brillants que c’est souvent un véritable casse-tête de choisir qui devrait être récompensé par un « Innovators Award » – un prix d’AMUG décerné à ceux qui ont cultivé des idées novatrices qui ont fait progresser le secteur de la FA. AMUG étant un événement unique en son genre, l’organisation continue de refléter son engagement envers des innovateurs uniques en leur genre. Cette année, Greg Morris sera le lauréat de cet estimé « Innovators Award » et il a fallu une conversation avec lui pour comprendre ses nombreuses réalisations. Il est intéressant de noter que cette conversation va au-delà de son parcours pour englober l’adoption des technologies de FA dans les industries verticales et l’avenir de Zeda.
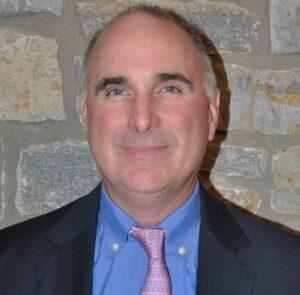
Nous avons d’abord connu Morris comme l’un des cinq fondateurs de Vertex Manufacturing, une société qui a fusionné l’année dernière avec PrinterPrezz et qui opère maintenant sous le nom de Zeda. En réalité, Morris est un homme aux multiples casquettes qui nécessiteraient probablement le chapitre entier d’un livre pour les mettre en évidence. Le point commun de ces casquettes est qu’elles ont toujours eu un lien avec la fabrication additive métal.
« Lorsque notre entreprise de l’époque, Morris Technologies, a introduit la technologie de fusion des métaux par lit de poudre laser sur le marché nord-américain en 2003, j’estime que nous avons eu la chance de nous trouver au bon endroit au bon moment. Nous avons rapidement compris que cette technologie était très prometteuse et nous y avons investi massivement au cours des années suivantes. Heureusement pour nous, ce « pari » a porté ses fruits puisque la technologie a évolué et mûri de telle sorte que nous avons pu travailler avec nos clients pour l’utiliser dans des prototypes fonctionnels et, finalement, dans des pièces de production. Comme beaucoup le savent, nous avons travaillé en étroite collaboration avec GE Aviation pour développer la partie additive de leur embout de tuyère LEAP. Une fois cette information rendue publique, de nombreuses autres entreprises ont perçu le potentiel de cette technologie et ont commencé à l’exploiter pour leurs propres produits et objectifs. Avec le développement de nouveaux alliages, une meilleure compréhension de la manière de « concevoir en fonction du processus » et les progrès globaux de la technologie des machines, nous avons vu l’impression 3D de métaux devenir un outil puissant pour de nombreuses entreprises cherchant à exploiter les avantages inhérents à la flexibilité et à la liberté de conception de leurs produits, contribuant à donner aux produits de nouvelles capacités, à réduire les coûts et souvent à alléger les contraintes de la chaîne d’approvisionnement qui ont contribué à réduire les délais de livraison. Aujourd’hui, nous continuons à voir non seulement des avancées technologiques avec beaucoup de ces types de machines, comme les systèmes multi-laser, l’amélioration de la surveillance de la machine et de la qualité et beaucoup d’autres éléments similaires, mais nous voyons aussi un certain nombre de modalités métalliques intéressantes qui aident à répondre à des applications spécifiques qui élargissent également la capacité des ingénieurs et des concepteurs à choisir le type d’impression 3D métal qui pourrait correspondre le mieux à leurs applications et utilisations », a déclaré Morris à 3D ADEPT Media.
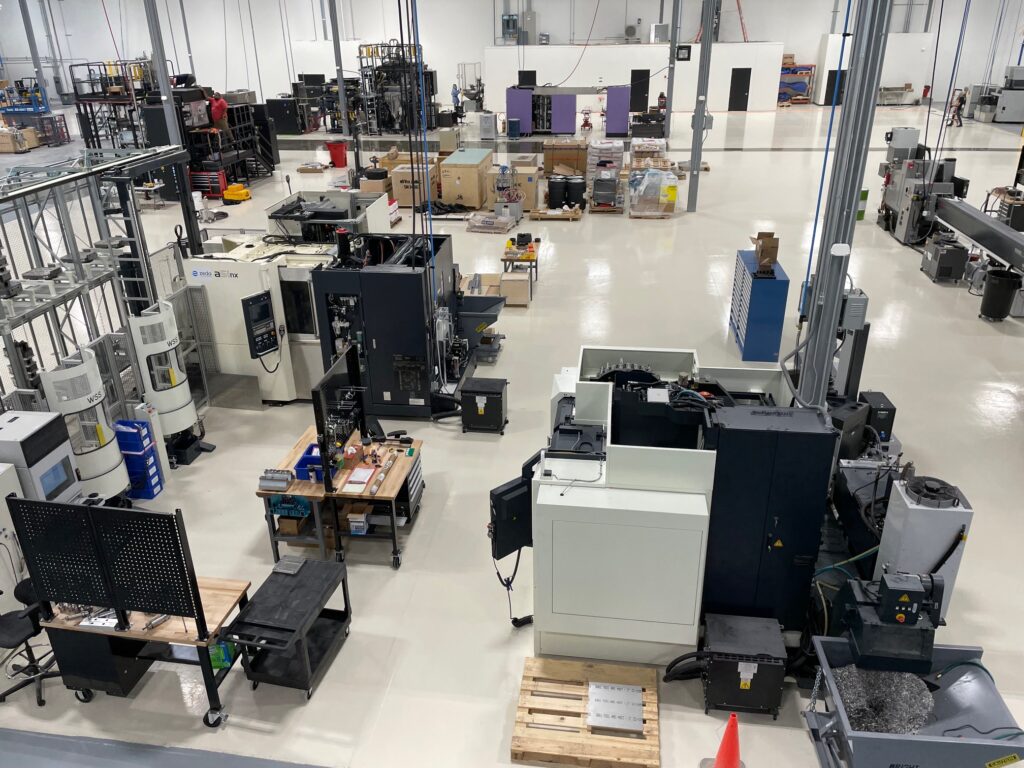
S’il ne s’agit là que d’une petite partie de l’histoire qui a marqué son parcours, Morris reconnaît que cette histoire n’aurait pas pu être partagée aujourd’hui sans les nombreuses mains qui ont uni leurs forces pour la rendre possible. À ce jour, l’homme que nous avons d’abord connu en tant que directeur technique de Zeta Technologies est en train d’évoluer vers un rôle plus stratégique au sein de l’entreprise, tout en restant conseiller auprès de quelques start-ups et entreprises.
L’adoption de la FA dans les secteurs de l’espace, de la défense et de l’aérospatiale
Vertex Manufacturing est l’un des bureaux de services qui a eu l’audace de parier sur l’imprimante 3D Xerox ElemX™ – une technologie d’impression 3D métal liquide qui était encore considérée comme « nouvelle » sur le marché, mais apparemment suffisamment viable pour imprimer en 3D de l’aluminium de manière cohérente et fiable.
Si nous avons toujours espéré que Vertex ferait de la technologie Xerox son arme secrète pour propulser la FA à travers les industries de l’espace, de la défense et de l’aérospatiale, Morris a révélé qu’ils ont commencé avec une machine LPBF de GE Additive et ont ajouté une technologie EBM de GE après l’intégration de la solution Xerox. Il ne sera donc pas surprenant d’apprendre que la technologie LPBF était, est et restera probablement la principale technologie du segment de la FA des métaux – chez Zeda et pour d’autres utilisateurs de la FA.
Pour notre expert, il existe des technologies de FA des métaux qui conviennent mieux que le procédé LPBF pour certaines applications. L’une de ces technologies est la projection de liant, dont les parts de marché augmentent sûrement, mais lentement. « Alors que je dirais que la différenciation de la conception peut transformer la façon dont on produit certains composants, d’autres facteurs ont le potentiel d’avoir un impact plus important du point de vue du volume, comme le coût par pièce. Je pense qu’il y a une variété de facteurs qui empêchent l’impression 3D métal d’être plus omniprésente, le coût étant probablement l’un des principaux facteurs à prendre en compte. Les technologies telles que la projection de liant et les technologies similaires peuvent apporter à la fois les avantages conceptuels d’un processus de stratification avec un débit et donc une compétitivité des coûts que les technologies telles que le procédé LPBF ne sont parfois pas encore en mesure d’atteindre », explique Morris.
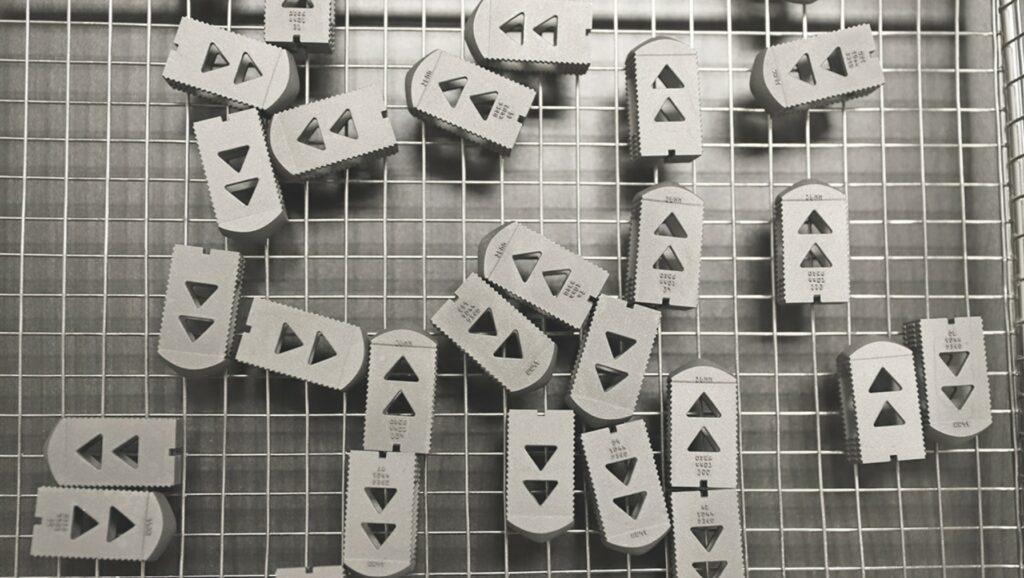
Et si on ajoute les considérations liées aux matériaux, à la taille des composants et à la qualification des machines, on obtient les ingrédients qui pourraient complexifier la recette pour obtenir des pièces pour les industries verticales exigeantes susmentionnées.
Loin d’être pessimiste, Morris se concentre sur les informations dont nous disposons et sur la manière dont nous pouvons en tirer le meilleur parti pour nous développer :
– Étant donné que chaque technologie de FA métal a ses propres nuances et exigences de conception, il faut reconnaître qu’il est très difficile d’être un expert du jour au lendemain dans l’une d’entre elles, sans parler des multiples types d’impression 3D métal. Il souligne donc que les connaissances sur la meilleure façon de concevoir une pièce en tenant compte d’une technologie particulière peuvent ne pas être aussi efficaces qu’elles pourraient l’être jusqu’à ce que l’expérience soit acquise ou que des outils supplémentaires soient disponibles pour aider les ingénieurs et les concepteurs à créer de façon plus « automatisée » une pièce qui sera bien imprimée et qui réalisera la plupart des objectifs qu’ils se sont fixés.
– Soyez attentifs aux matériaux et procédés prometteurs. Leurs progrès peuvent être lents, mais les technologies et les processus sont en train d’être améliorés. Les technologies qui permettent de produire efficacement des pièces plus grandes avec des alliages tels que l’Inconel, le cuivre et l’acier inoxydable gagnent du terrain. Parmi elles, le dépôt d’énergie dirigée (DED), la soudure par friction-malaxage (MELD) et d’autres utilisant des méthodes émergentes et nouvelles de dépôt et de consolidation des matériaux métalliques seront en demande pour leur rapidité et leur capacité à fournir des propriétés mécaniques.
– Proposer des solutions spécifiques à l’industrie et à l’application. Pour Morris, des méthodes plus efficaces de production de pièces additives (coût), des délais plus courts, une qualité et des propriétés de matériaux démontrées et éprouvées jouent tous un rôle important dans la rapidité et l’ampleur de l’adoption de l’impression 3D métal dans un secteur, une entreprise ou une application.
La fusion de Vertex et PrinterPrezz
Si Vertex est reconnue pour la production de pièces pour des industries telles que l’espace, la défense et l’aérospatiale, PrinterPrezz a pour mission de fournir un service similaire aux industries médicales et de soins de santé. Nous avons toujours été intrigués par cette fusion, car chacune de ces entreprises opère dans des domaines d’activité distincts.
Ce à quoi Morris répond : « Lorsque les discussions sur la fusion ont commencé, Vertex était un fournisseur de PrinterPrezz, proposant des services de post-usinage et de traitement des implants en titane fabriqués par PrinterPrezz. La synergie consistait à combiner le savoir-faire et les antécédents de Vertex en matière d’impression 3D métal, ainsi que les capacités et le savoir-faire en matière de post-traitement de ces pièces imprimées en 3D, avec le désir de PrinterPrezz d’intégrer verticalement toutes ces capacités. Même si Vertex se concentre davantage sur les pièces de type aérospatial, spatial et de défense, la capacité à croiser les apprentissages et le savoir-faire de ces industries disparates a été considérée comme un atout. »
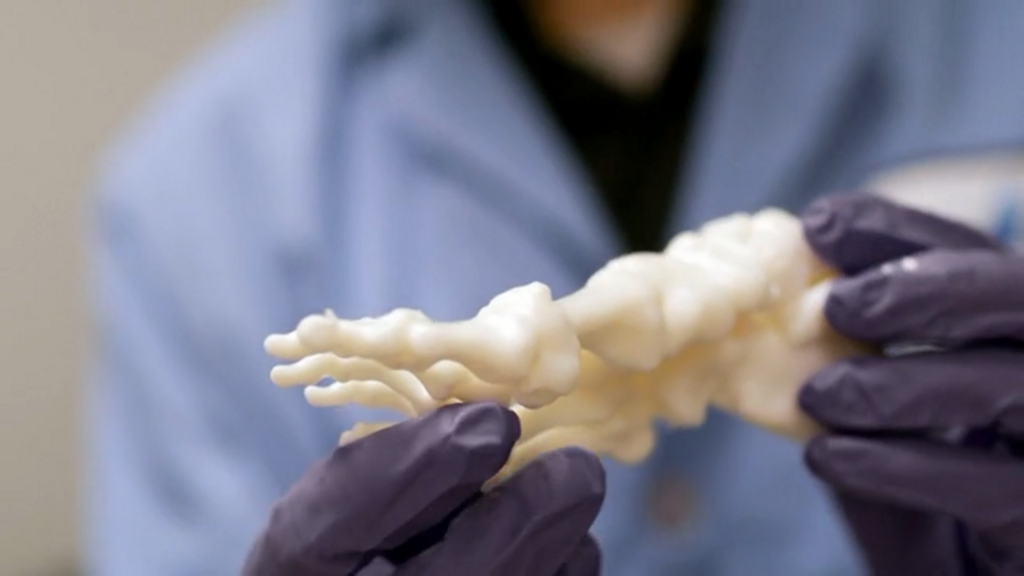
En ce qui concerne les différences qui les distinguent dans l’utilisation des technologies de FA, il ajoute :
« PrinterPrezz s’est concentré sur l’impression pour les applications médicales, qu’il s’agisse d’implants ou d’instruments. Pour cette raison, elle travaillait presque exclusivement avec du titane et des alliages inoxydables. Elle a également mis en place des étapes de post-construction très spécifiques pour travailler avec ce type de petites pièces spécifiques à l’industrie. Vertex, quant à elle, était plus généraliste et se concentrait sur l’aérospatiale, l’espace et la défense. À cette fin, Vertex travaillait avec des alliages similaires à ceux de PrinterPrezz, mais produisait également des pièces dans des alliages plus spécifiques à d’autres industries qui souhaitaient des matériaux à base de nickel ou d’autres types de matériaux similaires. Les étapes postérieures à la construction de Vertex ont également consisté à élargir l’éventail de ses capacités, simplement en raison des besoins accrus de ces différents types de clients. En fin de compte, nous constatons qu’il y a plus de synergies que de différences entre les différents secteurs d’activité. »
Afin de promouvoir l’utilisation des technologies de FA sur les marchés de l’aérospatiale, de l’espace et de la défense, Zeda, la société qui regroupe les activités de Vertex et PrinterPrezz à ce jour, se concentrera sur la production de pièces avec des alliages tels que l’Inconel 718, le cuivre avec GrCop42, l’acier inoxydable tel que 17-4 et 316 et l’aluminium.
Pour marquer sa volonté de continuer à se concentrer sur les différents secteurs qui étaient au cœur des activités de Vertex et PrinterPrezz, Zeda disposera d’une division entière appelée Zeda Health qui sera bientôt basée à Reno, au Nevada, tandis que l’autre partie de l’entreprise sera Zeda Technologies, basée à Cincinnati.
« Ces deux entités relèvent de Zeda Inc. Comme l’environnement général du capital-risque et des investissements privés continue de s’améliorer, je pense que Zeda aura la possibilité d’attirer le montant approprié de capitaux pour poursuivre sa croissance sur tous ces marchés », conclut Morris.
Clause de non-responsabilité : Cet entretien a été réalisé dans le cadre d’un partenariat médiatique avec AMUG.