Dans une industrie où l’un des enjeux majeurs consiste à réduire les cycles de « mise sur le marché » des produits, la fabrication additive est souvent directement classée comme une technologie permettant de produire plus rapidement par rapport aux procédés de fabrication classiques. Pourtant, pour certaines applications telles que l’outillage de moule – qui est essentiel pour le développement de nombreux produits -, certains procédés de FA sont non seulement coûteux, mais sont aussi longs que l’usinage conventionnel, sans compter qu’ils obligeront toujours l’opérateur à effectuer certains usinages avant d’obtenir la pièce finale imprimée en 3D.
Il est intéressant de noter qu’une autre alternative est récemment apparue sur le marché, une alternative qui offrirait un pari plus intéressant en termes de délais d’outillage et de mise sur le marché des produits ; une alternative qui est basée sur des pâtes métalliques.
Mantle, une start-up basée à San-Francisco qui a récemment abandonné le mode furtif, après une levée de fonds secrète de 13 millions de dollars, propose ce concept fascinant sur le marché. Avec une solution technologique appelée TrueShape, la société a décidé de se concentrer uniquement sur le marché de l’outillage (pour l’instant) ; un intérêt spécifique, qui est parfaitement compréhensible quand on connaît le parcours et l’expertise des fondateurs. En fin de compte, c’est souvent votre expérience qui détermine comment vous allez façonner l’avenir, n’est-ce pas ?
Eh bien, Mantle a été fondée par Ted Sorom (CEO) et Steve Connor qui sont respectivement ingénieur en conception mécanique et chimiste de formation. Même si l’entreprise est officiellement entrée sur le marché en février 2021, il convient de noter que Sorom et Connor l’ont fondée il y a plus de cinq ans.
Leurs expériences professionnelles respectives ont conduit au développement de TrueShape dans la mesure où, dès le début de sa carrière, Connor a acquis une expertise et a décidé de se spécialiser dans les nanoparticules et les pâtes métalliques. Il a même développé avec succès un « produit de remplacement à moindre coût pour les pâtes métalliques d’argent coûteuses utilisées dans l’industrie solaire. » « Il a ensuite changé de vitesse pour voir si une technologie similaire pouvait être utilisée pour la fabrication additive« , a déclaré Sorom à 3D ADEPT Media.
L’accent mis sur le marché de l’outillage pourrait s’expliquer par le fait que sa taille était évaluée à 212 500,0 millions de dollars en 2020, et qu’elle devrait atteindre 439 994,9 millions de dollars d’ici 2030, enregistrant un TCAC de 7,5 % de 2021 à 2030. Au-delà de ces chiffres, notons que Sorom a également acquis une grande expérience dans le domaine. En effet, juste après l’obtention de son diplôme, il a « rejoint une entreprise verticalement intégrée qui fabriquait des équipements haut de gamme en utilisant des pièces métalliques usinées par CNC et des pièces en plastique moulées par injection. »
« Je concevais les pièces et les moules à l’étage, puis je descendais fabriquer les moules avant de les mettre en pleine production. J’ai vu de mes propres yeux combien le processus de fabrication d’outils était long et coûteux, même pour une simple pièce en plastique. Le calendrier de lancement de nos nouveaux produits était conditionné par l’outillage. Malheureusement, mon expérience n’est pas unique ; presque toutes les entreprises de fabrication sont confrontées à ces mêmes défis. Chez Mantle, nous avons concentré nos efforts pour relever ces défis« , se souvient-il.
Comprendre l’épine dorsale de l’industrie manufacturière
Souvent considéré comme l’épine dorsale de l’industrie manufacturière, l’outillage implique la conception et la fabrication des outils nécessaires à la production en série de pièces, pièces qui peuvent impliquer la fabrication de moules et de matrices (presses), le forgeage, le calibrage, les gabarits et les montages, et les outils de coupe, tous utiles pour produire d’autres pièces pour les voitures, les turbines, les hélices, pour n’en citer que quelques-unes.
La conception et la fabrication de ces outils ayant une incidence directe sur la qualité de la production de l’industrie utilisatrice finale, le choix du processus de fabrication utilisé ici est d’une importance capitale. « Les applications d’outillage exigent une finition de surface exceptionnelle et un haut degré de précision« , souligne Sorom. Pour offrir un tel rendu, Mantle a décidé de combiner le meilleur des deux mondes : l’usinage traditionnel et la fabrication additive.
En plus, en ce qui concerne la FA, les fondateurs voient ici une opportunité pour cette technologie d’avoir un impact important sur la production de produits en grand volume.
TrueShape
Historiquement, la fabrication d’outils à l’aide d’une méthode de fabrication traditionnelle nécessite souvent un processus en plusieurs étapes comprenant la programmation, la découpe et la finition des outils – un processus qui, au final, peut prendre plusieurs mois au lieu de quelques jours seulement avec la technologie de FA dédiée.
L’impression hybride de métal lié de Mantle fonctionne en extrudant une pâte métallique propriétaire avant d’affiner la surface de la pièce via un usinage soustractif traditionnel. Pour ceux qui ne les connaissent pas, sachez que les pâtes métalliques sont souvent utilisées pour combler les bosses sur toute surface métallique et solide, ainsi que pour les fixations de granits et autres industries connexes. Habituellement, une résine et un durcisseur sont combinés pour créer une liaison durable et très résistante qui sèche en quelques minutes et peut être utilisée pour réparer, remplir et reconstruire toutes les surfaces métalliques et en béton.
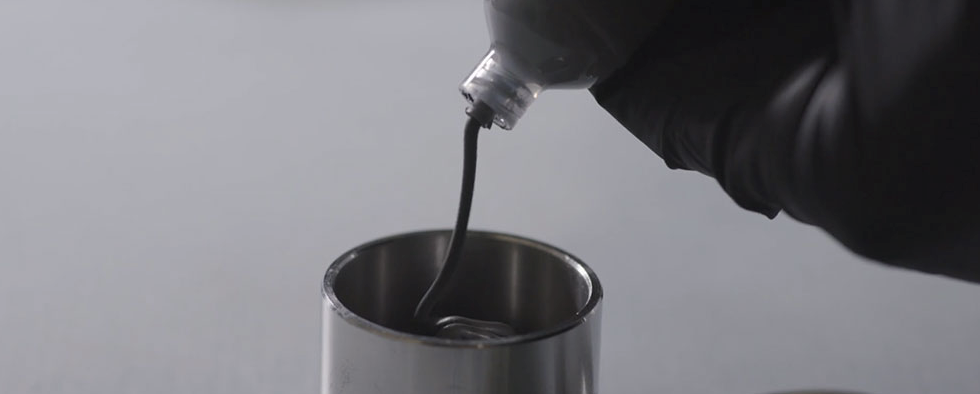
Dans le cas de Mantle, la pâte est composée de particules métalliques et de supports liquides, que l’on extrude pour construire les pièces couche par couche.
« Nous chauffons et séchons ensuite la pâte à l’intérieur de l’imprimante, ce qui élimine le support liquide et laisse un « corps vert » relativement mou qui peut être usiné rapidement et facilement. L’usinage crée la précision, la finition de surface et les caractéristiques fines nécessaires aux pièces de précision comme les moules. L’étape finale est le frittage, qui est important car il permet de fusionner les particules de métal et d’établir les propriétés finales du matériau. Le frittage s’effectue dans un four à haute température qui amène la température des pièces juste en dessous du point de fusion du matériau, puis la refroidit. Lorsque les pièces sortent du four, elles sont des aciers à outils de haute dureté avec des surfaces extraordinairement lisses qui peuvent être utilisées directement dans des applications d’outillage de moules à injection sans aucun post-traitement des surfaces des moules« , a déclaré le CEO à 3D ADEPT.
D’après les explications de l’entreprise, la principale différence avec les autres procédés de FA réside dans l’étape de post-traitement. Ce n’est un secret pour personne que cette étape du cycle de production prend souvent plus de temps que l’étape de fabrication elle-même, et est même plus coûteuse que la fabrication d’une pièce. TrueShape a pour ambition de réduire considérablement, voire de supprimer cette étape, lorsque cela est nécessaire.
Il n’y a pas grand-chose à dire si on la compare aux procédés de fabrication classiques. Cependant, nous savons que cette technique semble avantageuse par rapport à certains procédés de FA qui mettent en avant des avantages de conception tels que le refroidissement conforme. En fait, le procédé de Mantle semble aller au-delà de ces avantages, puisqu’il peut également assurer une certaine uniformité du matériau au cours du processus, ce qui est essentiel pour obtenir la reproductibilité des pièces.
Cela est principalement dû à la façon dont la pâte métallique fluide est distribuée, afin de créer des microstructures plus solides directement dans la pièce imprimée en 3D. Jusqu’à présent, Mantle a développé deux matériaux d’acier comparables aux aciers à outils très courants, P20 et H13, pour les besoins spécifiques de l’industrie de l’outillage.
Pour illustrer les capacités de sa technologie, Sorom a cité l’exemple d’un fabricant mondial de dispositifs médicaux qui a utilisé TrueShape pour fabriquer des inserts de moule en acier pour cavités et noyaux. Grâce au procédé d’impression hybride sur métal, cette entreprise a réussi à faire passer sa production de 7 semaines à 8 jours, et à réduire ses coûts de plus de 50 %.
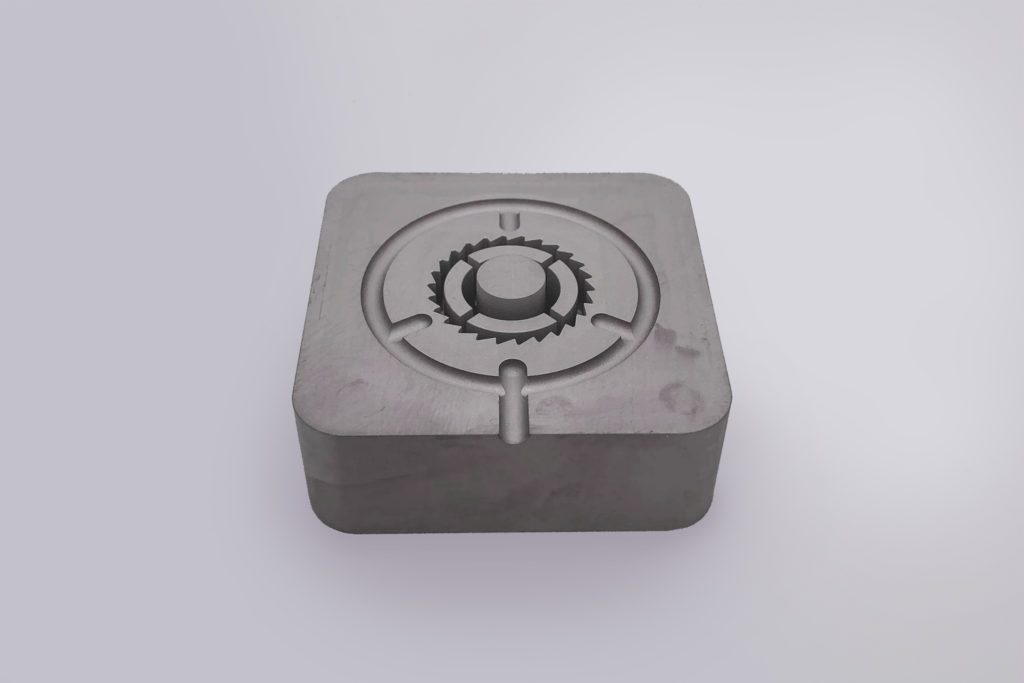
La prochaine étape dans le pipeline
Le premier objectif de Mantle est de démontrer comment TrueShape est capable de fabriquer des composants de précision, en mettant l’accent sur l’outillage comme première application. Pour l’avenir, la société s’attend à ce que ses clients trouvent toutes sortes d’utilisations pour cette technologie.
« Les autres domaines d’application comprennent les gabarits et les montages de précision et les pièces de rechange/à faible volume pour les applications industrielles », note le PDG. « Nous prévoyons également que, dans plusieurs années, notre technologie sera qualifiée pour des applications finales dans les domaines médical, aérospatial et automobile« , complète-t-il.
Enfin, en tant que jeune fabricant de machines, nous pourrions nous attendre à ce que Mantle développe de nouveaux matériaux, des processus d’impression plus rapides et des enveloppes de construction plus grandes, mais ce que nous sommes impatients de voir pour l’instant, c’est la livraison de leurs premiers systèmes, car cela marque souvent un véritable positionnement sur la scène internationale de l’industrie.
Ce dossier exclusif a été initialement publié dans le numéro de Juillet/Août de 3D ADEPT Mag.
N’oubliez pas que vous pouvez poster gratuitement les offres d’emploi de l’industrie de la FA sur 3D ADEPT Media ou rechercher un emploi via notre tableau d’offres d’emploi. N’hésitez pas à nous suivre sur nos réseaux sociaux et à vous inscrire à notre newsletter hebdomadaire : Facebook, Twitter, LinkedIn & Instagram !