I would have loved to start this article like many people on social media, by saying that formnext was wonderful from the beginning to the end of my participation but I can’t. If I want to be honest with myself – and obviously to you, formnext was strange to me on the first day of the show. Strange, because despite an intense preparation upfront, I had this feeling of “déjà vu” when I entered Hall 12, where I had my very first meeting of the day. I was left with that sentiment until the middle of the afternoon, when I realized, I just needed to pay more attention.
Before I tell you what I should have paid more attention to, let me share a few interesting numbers. This year, Mesago hosted:
- 859 exhibitors (59% of which were international) in an exhibition space of 54,000 m²
- 32,851 visitors (specialists and managers – 50% international). A number that represents a further increase of 11,1% on the numbers already recorded for the previous year.
This impressive track record shows that Mesago is fully back on track – when compared to the post-pandemic period, and continuously goes the extra mile to provide AM users and exhibitors the most diverse and comprehensive experience.
That experience is where I should have started assessing. A quick look at the multifaceted conference program highlights for the first time three stages: Application, Industry, and Technology. Designed for AM users, industry insiders with cross-disciplinary expertise, and AM solutions providers, each of these stages featured a number of experts with a wealth of expertise in the industry.
These stages clearly highlight the fact that the AM industry is much more than technology solutions themselves. It’s a wide range of related topics that also contribute to the advancement of the industry as a whole.
Take the example of the Industry Stage only, companies from the partner region Nordic, including Equinor, Lego Group, Danfoss A/S, and Grundfos Holding A/S, discussed their use of Additive Manufacturing to conserve resources. Other key topics, such as supply chain resilience and cybersecurity – amongst others Viaccess-Orca and Daimler Truck AG – Daimler Buses GmbH, as well as emerging technologies such as bioprinting and 3D Printing of medicine were at the heart of the debates. Furthermore, experts from NewCap Partners, HZG Fund Management, Freigeist Capital GmbH, and AM Ventures Management GmbH discussed investment and financing options for startups of the industry.
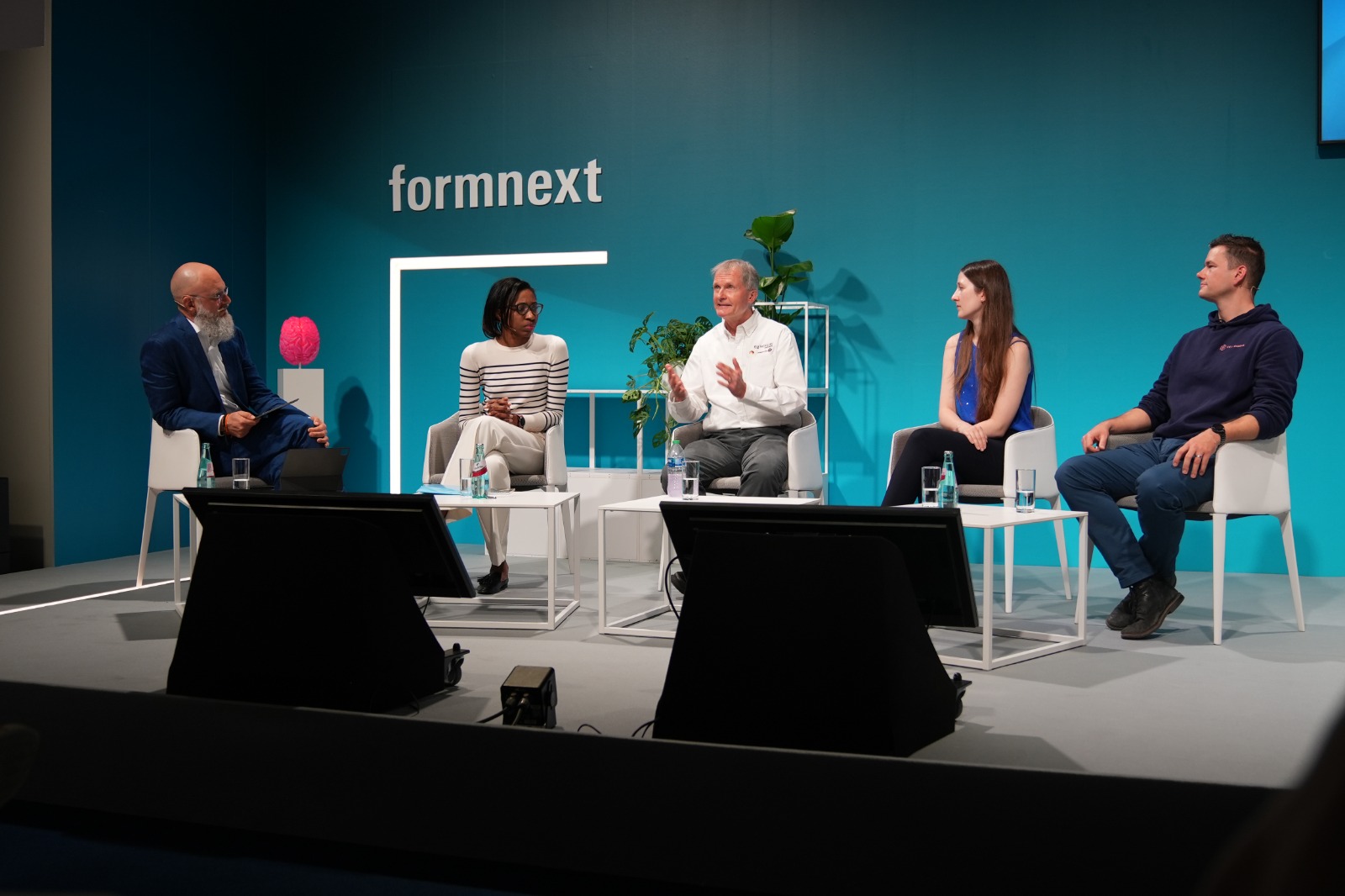
Image credit: 3D ADEPT Media
The uniqueness of this year’s edition was hidden in details you would not have seen at first glance.
Business
The Nordic region was maybe the partner country of this 2023 edition of formnext but Mesago hosted AM companies from all regions (Europe, Australia, Canada, USA, China). Europe left apart, there was a prominence of Chinese companies and visitors – accompanied by an interpreter who facilitated their tour of the show.
With China being reported as the second-largest market for Additive Manufacturing worldwide, communication on the global business landscape usually highlights the efforts of American and European companies that would like to penetrate this market. The presence of companies like BLT, Elegoo, Scantech, Shanghai Digital Manufacturing Co., Ltd., Shanghai Hangrui Advanced Materials Technology Co., Ltd., CBD-Tech, eMake3D Technology Co., Ltd., and many more is a reminder that there is also a need for these companies to internationalize their operations, and this requires to navigate cross-cultural communication and to adapt localization strategies.
On another note, the wave of mergers and acquisitions that reached its peak last year has been subtler and more strategic this year. From a business perspective, this means fewer investments on the exhibition floors as these companies usually join their marketing forces and handle them under one roof. BigRep is an interesting example to mention here as it has seized the formnext opportunity to announce the acquisition of HAGE3D, an advanced engineering company with 40 years of experience in large-format, special-purpose machine building. Showcased in a very cool way on the show – through a “collabosphere”, the acquisition means that all Hage3D solutions will now be discovered through BigRep’s booths on exhibition floors across the world.
Video credit: 3D ADEPT Media
Another one that we will probably no longer see on its own at formnext is Essentium. Absent from this 2023 edition, we are likely to see the company’s solutions under the umbrella of its soon-to-be parent company: Nexa3D. The announcement was made right before formnext began and puts Nexa3D in a strong position in the industry as it now integrates a diverse range of solutions in its portfolio; a portfolio that has been strengthened this year with the acquisition of Addifab, XYZprinting, and a collaboration with Headmade Materials to enter the metal 3D printing segment.
Newcomers
This has become my favorite exercise on the showfloor: discovering who is new in the market and what value they bring. Interestingly, this year, I met newcomers to the show and newcomers to the industry.
One often assumes that because formnext is one of the most important events in the AM industry, one should meet all the companies that provide services in this industry. Yet, despite the good reputation of the event, there are still companies that choose not to exhibit at the event – for reasons of their own.
In the exhaustive list of companies I met, my favorite one was Deloro Wear Solutions GmbH. New to the show and new in the AM market, the company brings to the AM industry five decades of experience in welding solutions, and metallic wear- and corrosion protection solutions. They bring to the market a range of anti-aging metal powders.
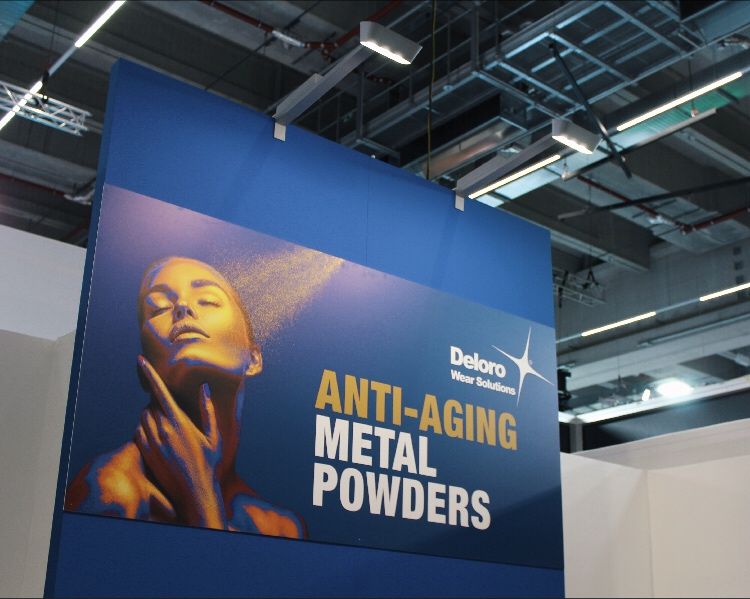
“Some are like water, some are like the heat
Some are a melody and some are the beat
Sooner or later, they all will be gone
Why don’t they stay young?”
Remember these words from Alphaville’s famous single Forever Young? If the German synth-pop band couldn’t find the answer to the question asked in the single that made their success, Deloro seems to have found the secret for long-lasting and reliable 3D printed parts. At formnext, they introduced their Cobalt- and Nickel-based powder for 3D printing, their printed protection, and their powder feeder for Additive Manufacturing.
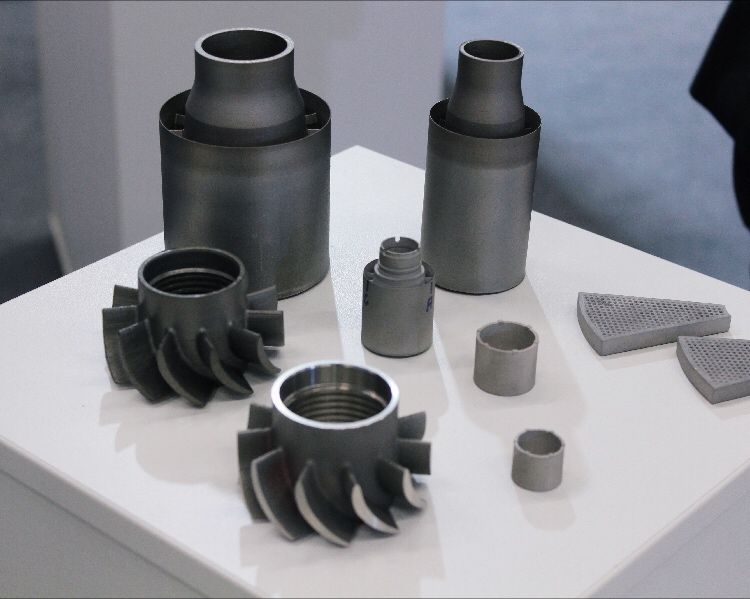
I like their concept, the team is experienced so I am sure you will hear more about them in the upcoming months.
Another company that caught my attention on this show is Fronius. New to the show but not in the AM world, the company’s solutions have already convinced WAAM machine manufacturers like MX3D. The company builds on its strong welding expertise to improve the WAAM process. If you are well familiar with the welding process, you probably know that it needs to be as cold as possible to deliver strong layers. This means that it needs to be sufficiently low energy such that when a new layer is applied, the existing layers do not melt again. Fronius offers a wide range of solutions to address this solution and one of their highlights on the show was the CWC-S Cobot welding cell that guides the welding torch to the appropriate positions.
Fronius presence at formnext reminded me of the prominent presence of robotics companies last year on the show. I thought we would have witnessed more applications in this regard throughout 2023 but in the end, there were not a lot. I still believe it’s only a matter of time before we witness the true potential of robotics in AM.
Directly coming from New Zealand is, Foundry Lab, another company that caught my attention with another super cool marketing approach: “Mom was wrong, you should put metal in the microwave; it won’t go bang!”.
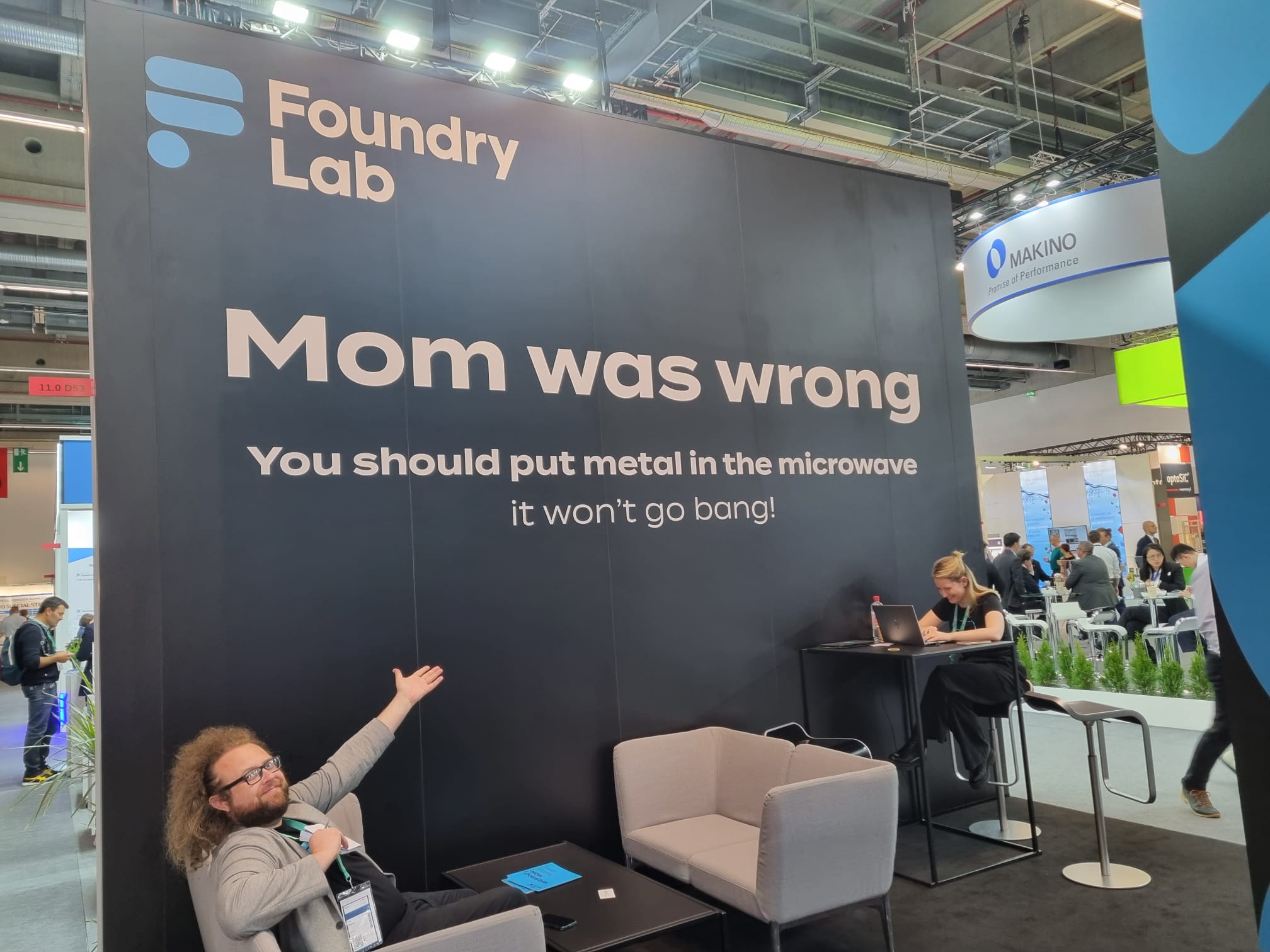
First and foremost, moms are always right – how dare they? Well, the company is bridging the gap between casting and 3D printing with their Foundry Lab printer, a system that can produce reusable diecast equivalent molds within hours in only 4 steps: print – set – load and cast.
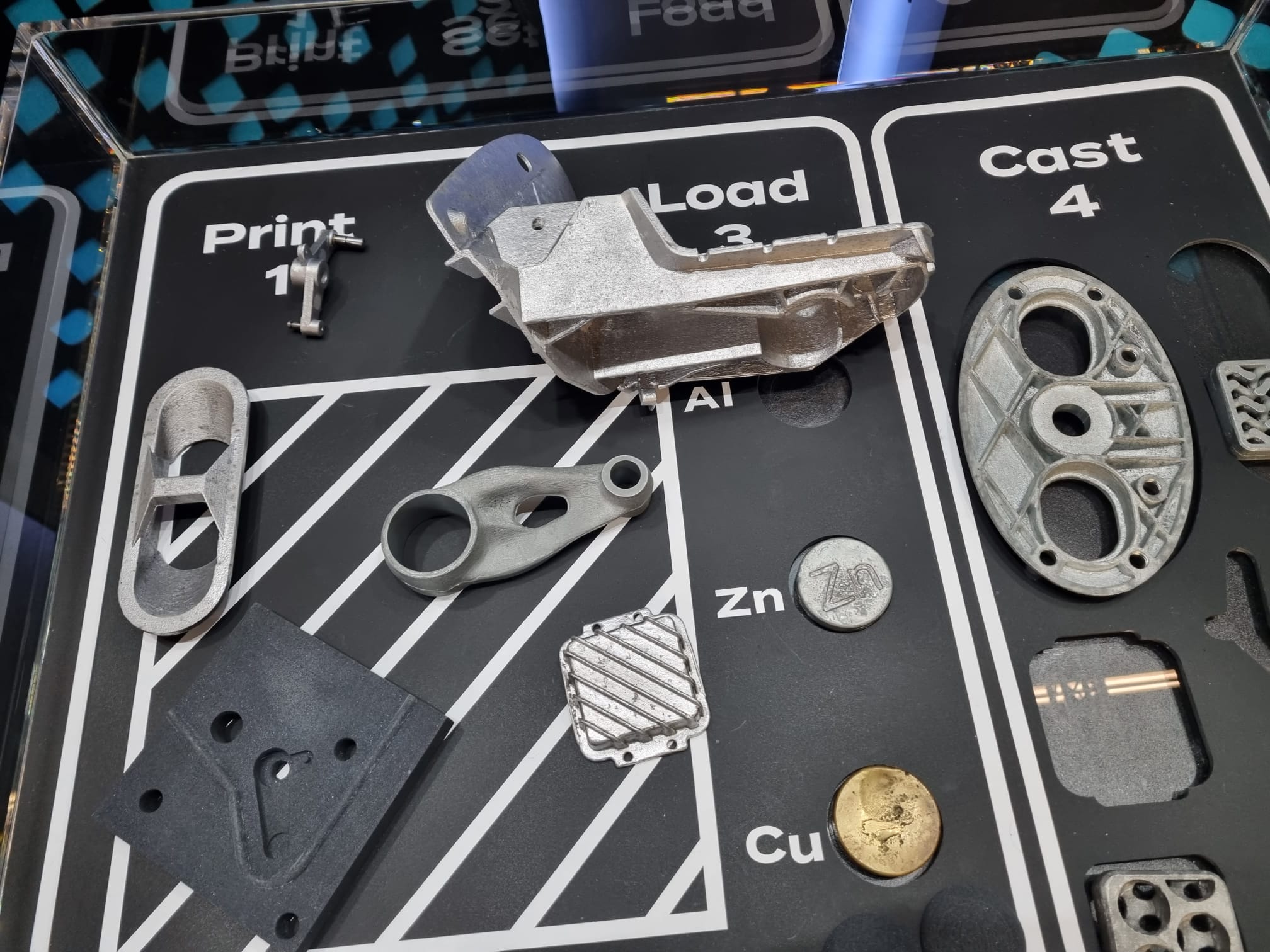
At the heart of their 3D printing process lies binder jetting, but what makes the system stand out in this market is the microwave furnace which allows a casting to be produced within a lead time of less than one day. Whether in automotive, industrial hardware or consumer electronics, Foundry Lab is challenging a field of activity that has long been associated with labor-intensive manual techniques and molds.
The current market: technology & applications
This year at formnext, I was asked one question – several times: “Are there any new technologies that captured your attention (yet)?” Although this is not truly an open question, I found myself providing a somewhat detailed answer.
To those who asked me this question on the first day of the event, before the afternoon, my answer was quite short: “not really. Most of these technologies are “déjà vu” to me”. Then, the more I looked, the more details drew my attention. It was no longer a matter of new products, but of improved configurations. For most machine manufacturers – be it 3D printers and post-processing machines, the question they ultimately tried to answer was: How can I make this existing product better?
We saw that with TRUMPF which unveiled an upgraded version of its TruPrint 2000 industrial 3D printer; we saw that with Solukon which announced several key updates for its automated depowdering machines. Between the upgraded Digital-Factory-Tool and the collaboration with Rivelin that focuses on automation, the most important update for this machine manufacturer was probably the automated depowdering machine SFM-AT350-E that integrates for the first time a piezoelectric excitation. Founder and CEO Hartmann told us why this new integration is meaningful in an automated depowdering machine.
In ceramic 3D printing, there were a number of interesting upgrades as well: one in multi-material 3D printing and another one at the software level.
As you may know, multi-material 3D printing is one of the manufacturing techniques with the strongest unique selling proposition: using multiple materials at the same time to fabricate a part. So far, we had identified 6 different types of AM technologies that can use this technique: FFF (with single nozzle or multi-nozzle), SLA, material jetting, binder jetting, DED, and powder-bed/SLS.
Today, Lithoz LCM technology can now be added to this list as the new CeraFab Multi 2M30 3D printer can process multiple materials at the same time.
On another note, software is one of the least highlighted topics in ceramic 3D printing, yet remains one of the most important areas for improvement. I liked that 3DCeram made it its key highlight at formnext and I got to see the interface of their CPS 2.0 which stands for Ceramaker Printing Software. The 2 in 1 software solution can be installed on the designer’s computer or upgraded in 3DCeram’s existing C1000 FLEXMATIC 3D printers.
With the C-PRINT option – ideal for industrials who run a 3D printing farm (at least 6 3D printers), the software solution can be used for the preparation of 3D printed parts, and provides the possibility to duplicate the parts at the manufacturing level.
Furthermore, as speed and details don’t always work hand in hand, the C-PERFORM option can help those users who are looking to produce different parts to tailor the production requirements to a given application.
Another one that I can’t help to mention here is Evolve Additive Solutions. Even though, they can’t produce in high volumes yet, one should recognize the good quality of their polymer 3D printed parts. They are expanding their portfolio with new materials. Let’s hope that their recent distribution agreement with Alphacam will probably further shed light on the applications their STEP process can enable.
Last but not least, if you’re still doubting of the advancement of the market, keep in mind this milestone moment from Conflux Technology and AMCM GmbH, that highlights the ability to produce a 3D printed vital part for a metal 3D printer. This Conflux Cartridge heat exchanger is one of those applications we live for, as it propels AM from a dream technology to a solution that delivers on its promise.
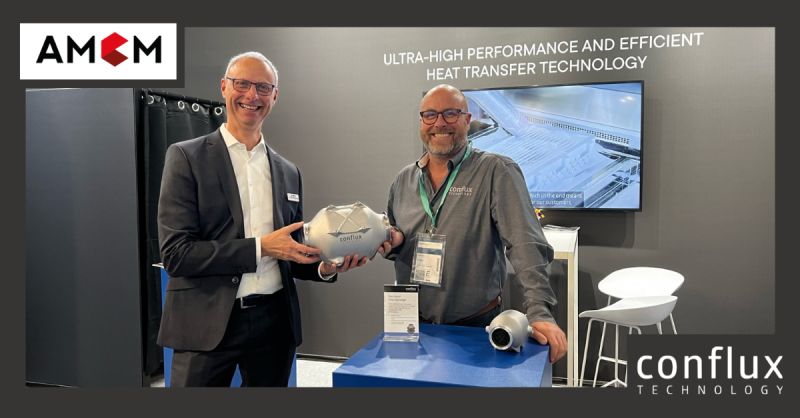
I could talk again for hours, but I would stop here as I believe this short overview of the event has demonstrated real advancements lie in the details that only advanced users can appreciate for their actual value.
Stay tuned here for more coverage of formnext. Content from the stage program will continue to be available on demand even after the event on Formnext streAM (www.formnext.com/stream).
Featured image: Copyright Mesago Messe Frankfurt GmbH_Mathias Kutt