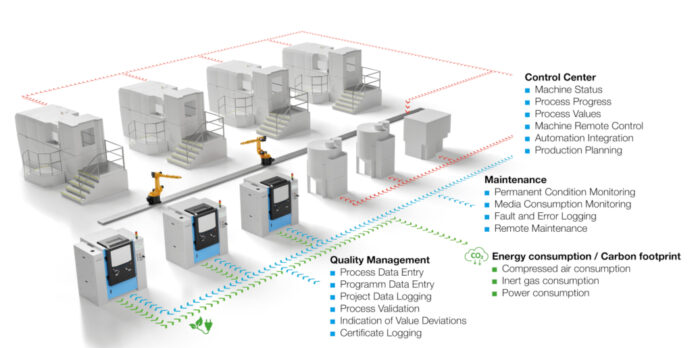
Germany-based automated depowdering company Solukon is enhancing its two-and-a-half-year-old Digital Factory Tool (DFT) with a carbon footprint measuring solution.
To fulfill its role in comprehensive quality monitoring and the digital integration of the machines, Solukon launched DFT with a smart sensor and interface kit in the spring of 2021. The system records and processes all automated depowdering data which can further be used as a standard to assess future deviations. The DFT collects all the data and compiles it through the OPC UA to make it available at the control center’s digital dashboards.
The new improved functions take automated depowdering a step ahead as it makes it possible to measure CO2 emissions and energy consumption which could be part of future legal regulations in machine manufacturing.
The additive manufacturing company is getting future-ready by enhancing its carbon emission transparency as the U.S. Securities and Exchange Commission (SEC) and the Corporate Sustainability Report Directive (CSRD) of the European Union stipulate that companies disclose their environmental behavior in their annual sustainability report from 2024 or 2025.
As you will see in the newly released September/October edition of 3D ADEPT Mag, AM companies must get started on their ESG journey. And among the ESG regulations that companies must comply with, one counts CSRD.
In this specific case, the agencies demarcate emissions generated by machines used by the company as CO2 emissions made by the company which would include automated depowdering machines.
New Digital Factory Tool updates
The Digital Factory Tool calculates the CO2 emissions either from the electricity or from the compressed air consumption. Both these are taken into consideration while measuring the carbon footprint of the automated depowdering process.
The major DFT upgrades introduced by Solukon include:
- Exact value of CO2 consumption per kilowatt hour of electricity
- Compressed air consumption per cleaning step and the inert gas consumption process transparent with a counter.
- Insights into the kilowatt hours of electricity expenditure per cleaning cycle
- Tracking time by monitoring the duration the compressed air gun was open between the flap for manual depowdering and finishing process
Solukon is also planning to integrate customers’ feedback on the DFT platform as 85% additive manufacturing industry customers using DFT leave feedback regarding its performance. This feature will be launched at the upcoming Formnext 2023 expo.
The CEO of Solukon Andreas Hartmann spoke about their efforts to boost data transparency and eco-friendly nature of DFT when he said: “Our concept of full transparency does not stop at the performance values of the depowdering process. It was important to us to quantify the carbon footprint of automated depowdering“.
The concept of sustainability goes beyond powder reuse when it comes to post-processing of 3D-printed parts. As a media company that advocates for a data-driven approach, we believe Solukon opens the door to a measurable methodology which might further help to understand the importance of automated depowdering for companies that would like to be more sustainable.
Solukon will present the upgraded Digital Factory Tool with the SFM-AT1000-S system in booth 12.0, D42 at Formnext 2023 and people can order it there. It’s also compatible with Solukon’s SFM-AT350/-E and SFM-AT800-S systems.
Remember, you can post job opportunities in the AM Industry on 3D ADEPT Media free of charge or look for a job via our job board. Make sure to follow us on our social networks and subscribe to our weekly newsletter: Facebook, Twitter, LinkedIn & Instagram ! If you want to be featured in the next issue of our digital magazine or if you hear a story that needs to be heard, make sure to send it to contact@3dadept.com