First industries to benefit from the Solukon Digital Factory Tool include Aerospace and Medical
One thing is certain: no matter how fast and safe Additive Manufacturing production processes are, if they do not comply with the requirements of a certain quality management system, your production will certainly not serve the right purpose.
Needless to say, that this necessity to comply with quality management – and even certain regulations is of paramount importance in demanding industries like aerospace and medical hence the establishment of norms like ASTM F3335 for medical products, Technical Considerations for Additive Manufactured Medical Devices (FDA), MSFC-STD-3716, standard for Additive Manufacturing in Aerospace to name a few.
Irrespective of their field, we have seen AM equipment’s providers develop new solutions to comply with these norms. For postprocessing equipment’s providers especially, the challenge is even harder as they necessarily have to take into account other machines in the production environment.
One solution that has just been launched on the market to address this issue is Solukon’s “digital factory tool”. The announcement follows the recent release of new features in the manufacturer’s automated powder removal systems.
With the goal of continuously improving automation in its powder removal processes, the machine manufacturer has upgraded its sensor concept. This upgrade comes along with the release of an interface management concept that will suit the depowdering process into a holistic digital production environment. The ultimate purpose? Increasing efficiency and ensuring quality control.
What does this digital factory tool include?
From the collaboration with Siemens to develop the intelligent SiDAM software to the digital factory tool today, the company aims to enable an easy integration of automated powder removal into an overall digital AM process.
The new digital package encompasses production control, maintenance management, integration of automation and process validation / quality management.
A closer look at production control
To understand how production control works, we need to explain the concept of OPC-UA for those who are not familiar with it.
OPC-UA stands for Open Platform Communications United Architecture. It is a platform thatprovides the necessary infrastructure for interoperability across the enterprise, from machine-to-machine, machine-to-enterprise and everything in-between.
The expert in automated powder removal has thus integrated an OPC-UA interface into its SFM-AT800 to allow for central controlling and monitoring. At Dresden-based Fraunhofer Institute for Machine Tools and Forming Technology (IWU), there is a Solukon SFM-AT800 that integrates this OPC UA interface within a modular robot cell.
Operators of this Solukon system explain that the robot cell is an example for downstream processing. Apart from powder removal, the robot cell includes a system for optical analytics of the geometry and a system for support removal, not to mention that it can also perform part loading and other jobs related to metal cutting. As pointed out by the concept of OPC-UA, each of these stations communicates with each other.
According to Dr. Juliane Thielsch, department manager of “Laser Powder Bed Fusion” and Dr. Arvid Hellmich, department manager of “IIOT-Controlling and Technical Cybernetics” at IWU Dresden: “Remote controlling the Solukon-system via OPC-UA ensures a flexible and adaptive part processing. As this entire process runs automatically, we are saving much adjustment time and therefore are ready for further functional integration.”
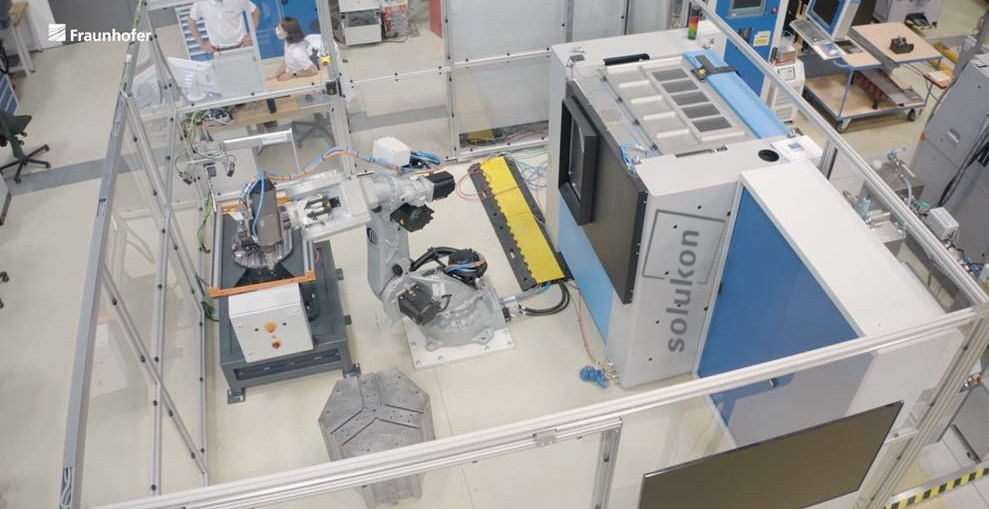
Imagine now an Aerospace factory where a wide range of industrial 3D printers and peripheral equipment operate together. The importance of such OPC-UA interface is pivotal to monitor and control all these machines accurately and in-real time. This way, if a defect occurs, it becomes easy to find out the exact location where it has occurred and to tackle immediately the problem.
“The Solukon OPC-UA interface allows both access to machine data and remote control. In addition, the Solukon Digital Factory Tool enables the operator to integrate all information into the dashboard of the machinery app. Data and parameters referring to cleaning programs, such as running time and batch number, can easily be assigned via the network. Regarding the cleaning process the OPC-UA interface enables the operator to start, monitor and modify the cleaning program as desired. Machine state and process progress are accessible in real time”, the company explains in a press communication.
The upgraded sensor concept for maintenance management
Improving maintenance management requires the machine manufacturer to enhance its sensor system monitors. With the new sensor systems, operators can instantly detect any changes in consumption of inert gas, compressed air, chamber atmosphere or energy.
The upgraded sensor concept easily provides the operator with an overview of individual machine components’ performance. Plus, operators get to achieve maintenance at the right time and get to know when to procure wear parts.
This maintenance task remains an external service the team at Solukon can provide.
The next level of automation
As a reminder, as opposed to manual processes, the key value for postprocessing equipment including is the ability to ensure that downstream processes like set-up effort, unpacking, depowdering and sieving are totally automated so that the operator save time and costs in the overall production line.
From day one, automation has been an integral part of the development of Solukon’s machines. The flagship projects HyProCell and NextGenAm reveal that it has addressed it in a different angle.
The company explained that at HyProCell, there is a permanent communication of the SFM-AT800 with a control center while being loaded by a robot. To this end, a special loading door and an automatic clamping system have been added to the automated powder removal system.
“The Solukon system is the first unit right after the building process and is therefore essential for further steps of the automated process chain. With the Hyprocell project, Solukon impressively displayed their high automation potential. Therefore, Solukon systems are ideally suited for further automation projects”, states Dr. Juan Carlos Pereira Falcon, Senior Researcher at Lortek and coordinator of the HyProCell project.
What makes process validation and quality management outstanding
We used to talk about reproducibility of AM parts without paying enough attention to all the systems that enable this reproducibility. As a matter of fact, reproducibility can only be achieved when every step of production is clearly outlined, paving this way an easier path to the very much needed certification required in industries like aerospace and medical. That’s something Solukon has clearly understood since the Solukon Digital Factory Tool takes into account all relevant conditions in the process chamber and records them in a protocol file for quality assurance.
While they have all the tools in hands to achieve continuous documentation and real time monitoring, it goes without saying that, it’s up to the operators to determine to which sensible value they should focus their assessment so that any technical inaccuracies can be noted and adjusted in due time.
“The Solukon Digital Factory Tool marks a significant step towards automation in postprocessing and therefore towards integration into a holistic AM process chain. Especially through process validation in one comprehensive protocol our customers achieve an even faster, more accurate and easier certification. The Solukon Digital Factory Tool is especially applicable to sensitive industries like Aerospace and Medical”, the company concludes.
Remember, you can post job opportunities in the AM Industry on 3D ADEPT Media free of charge or look for a job via our job board. Make sure to follow us on our social networks and subscribe to our weekly newsletter : Facebook, Twitter, LinkedIn & Instagram ! If you want to be featured in the next issue of our digital magazine or if you hear a story that needs to be heard, make sure to send it to contact@3dadept.com