Machine manufacturer Solukon has just announced new upgrades for its automated powder removal systems. The upgrades concern the SFM-AT1000-S and the SFM-AT800-S units.
As a reminder, the Germany-based company has been developing automated depowdering systems for six years now. After the real splash it made following its collaboration with Siemens, the company has kept demonstrating how reliable and automated depowdering can address the needs of operators working in the medical, space and even aerospace industries to name a few applications.
With a key interest in addressing the challenges of the aerospace industry, challenges that often include the handling of large and complex components, adaptation of controlling, and even processing of complex powders, Solukon has added new features to its depowdering machines.
It should be noted that the aforementioned systems are based on the manufacturer’s patented SPR® (Smart Powder Recuperation) technology. For those who are not familiar with the technology, it enables the removal of residual powder from complex metal parts by unlimited and programmable part rotation and controlled vibration in a safety-controlled atmosphere.
New improvements regarding the handling of components
Let’s start with the SFM-AT800-S. The intelligent machine had been developed in collaboration with software company Siemens. With its two servo-motorized and endless rotating axes, it enables operators to avoid waste while preserving their health. According to the manufacturer, the machine can now handle parts with a size up to 600 x 600 x 600 mm³ (XYZ) and a weight of 300 kg.
The SFM-AT1000-S on the other hand has been unveiled last year, following an inquiry from 3D printer manufacturer AMCM GmbH. Like we saw with the previous machine, the depowdering mechanism is the same. The system stands out through its ability to process large components that can reach up to 460 x 460 x 1,000 mmÂł and 500 x 280 x 875 mmÂł.
Today, Solukon announces that the machine’s new performance enables the user to operate parts that are up to 600 x 600 x 1.000 mm³ (XYZ) in size and up to 800 kg in weight.
Martin Bullemer, Managing Director of AMCM GmbH testifies to the machine’s new capability: “I am excited about the quick turnaround on the need for larger depowdering volumes. The Solukon offering makes an end-to-end solution for large components possible in the first place.”
Improvements regarding controlling
Another requirement from Solukon’s customers consisted in customizing controlling. To do so, the manufacturer has equipped the two systems with remote gimbal control in the form of a joystick. In a press communication, the company explains that by using this device, the part can easily be moved along any imaginal path with variable speed. The moving path and speed can be recorded simultaneously and can later be used as an automatic program for serial cleaning.
The remote gimbal control feature enables part displacement in any imaginal path with variable speed. With the recording of the operation being performed simultaneously, it is much easier for the engineer to use the recordings as an automatic program for serial cleaning.
That being said, the integration of these features does not mean that the depowdering units will not be able to save single positions. On the contrary, not only will it be still possible to do so, but each position can also later be manually optimized in the software and assigned by intelligent optio such as waiting time, vibrating, knocking and custom-made features like programmable blowing nozzles.
Improvements regarding complex powders: the example of copper
Although AM technologies enable the production of copper components that feature complex geometries, which could be leveraged in applications such as heat exchangers and rocket engine components with internal cooling channels, the manufacturing process of this material often comes with an array of constraints.
Indeed, apart from the physical properties of copper and its alloys that make it challenging to achieve good surface quality and low porosity by the widely used metal additive manufacturing processes, it is worth noting that the printed parts must also be able to withstand handling and depowdering prior to sintering.
In this vein, Solukon has come up with an additional impactor system for breaking up clogged powder bulks. Reality shows that copper and aluminum are some of the complex materials that show a “very sticky behavior and tend to clog in cavities”. Since Solukon’s SPR® technology allows for high frequent vibration, it makes it easy to ensure a fluidization of the powder (Understand “making the powder as flowable that it can flow out of the finest channels and crevices”). The manufacturer guarantees that the impactor treats the part with finely tunable knocks to loosen the clogging.
When it comes to complex materials, the ideal depowdering results therefore come from the combination of the manufacturer’s vibration system and the new impactor – which is now available as an additional option for all Solukon systems.
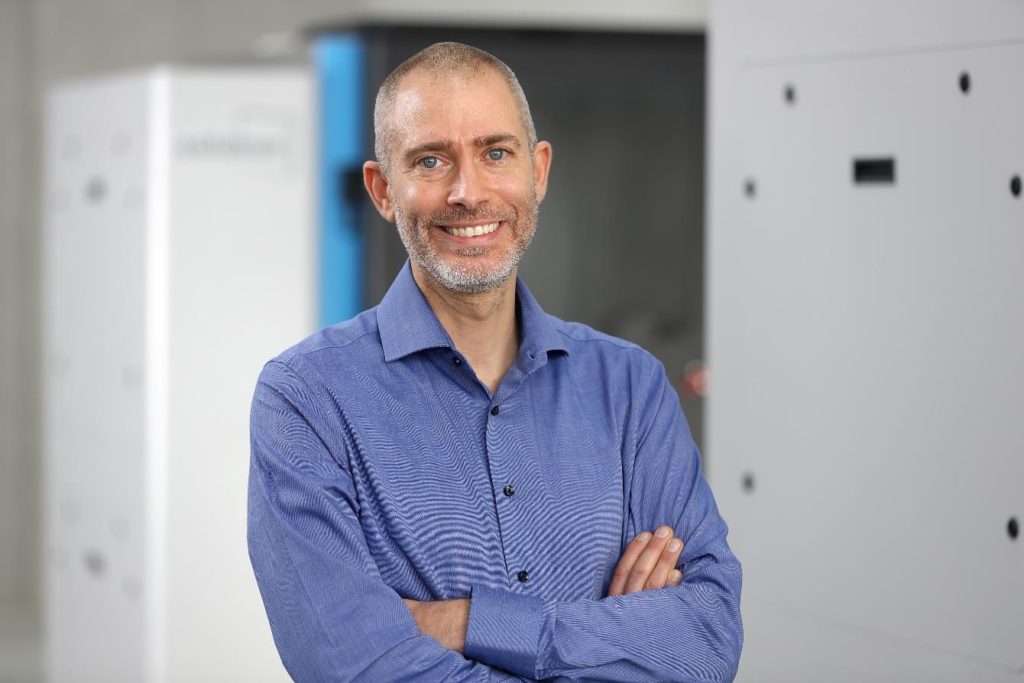
“Taking a closer look at the market, we clearly see a development to larger parts with highly complicated internal geometries as well as a trend for tough-to-handle materials. Especially rocket engineering is a leading force here brilliantly designing with copper. With our latest adjustments we want to give our customers even more opportunities to achieve their goals efficiently and comfortably”, Andreas Hartmann, co-founder of Solukon, states.
“Listening to our customers and continuous improvement of our systems have always been our guiding principle. During this year we are planning to come up with new retrofittable add-ons for our customers”, he concludes.
Remember, you can post job opportunities in the AM Industry on 3D ADEPT Media free of charge or look for a job via our job board. Make sure to follow us on our social networks and subscribe to our weekly newsletter : Facebook, Twitter, LinkedIn & Instagram ! If you want to be featured in the next issue of our digital magazine or if you hear a story that needs to be heard, make sure to send it to contact@3dadept.com