Making Additive Manufacturing (AM) a more common process for serial production requires taking into account the specific challenges of vertical industries using the technology. In the medical industry for instance, being able to achieve surface roughness for spine cages, or a very high surface quality and level of detail in dental applications are a few production requirements that may help medical device manufacturers meet the most stringent standards of their industry.
High-tech company TRUMPF has understood the importance of delivering industry-specific solutions and showcased the new TruPrint 2000 at Formnext, ideal for the needs of the healthcare and medical industries.
With over 17,900 employees and generated sales of about 5.4 billion euros (preliminary figures) in 2022/2023, TRUMPF’s superpower consists in helping industries drive digital connectivity through consulting, platform products and software. The OEM believes that Additive Manufacturing (AM) is the interaction of four components: laser, machine, monitoring and powder, hence the expertise it has built in each of these fields.
Key specifications of the new TruPrint 2000
Designed for medical engineering and other applications with lofty standards and quality demands, the TruPrint 2000 can serve the production of removable partial dentures, spine cages or even knee implants. First unveiled in 2019, the 3D printer has been enhanced to reflect the latest developments of TRUMPF’s core technologies.
With its so-called motorized beam expander, the TruPrint 2000 automatically adjusts the spot diameter of the laser to the task at hand. Depending on the application, the spot diameter is 55 or 80 micrometers. The 80-micrometer spot enables higher productivity. Users can use the 55-micron spot when special metal powders require a higher energy density. The machine comes with a multilaser option and a powder bed monitoring option. This means that OEMs of highly regulated industries such as medicine can improve their productivity with two TRUMPF fiber lasers. The high-tech company has increased the power of the integrated fiber laser to 500 watts as an alternative to the 300W laser in the basic configuration. In such case, a 55-µm beam diameter can be exposed simultaneously in the build area and generate up to 80% more parts in the same time with flexibility.
Furthermore, the scope of materials the machine can process has been extended to include various metal powders for welding such as stainless steels, tool steels, and aluminum, nickel-based, cobalt-chrome or titanium alloys, and amorphous metals.
In addition to automated powder bed and melt pool quality monitoring, the inert machine concept of the 3D printer with powder preparation station, facilitates powder and parts handling under shielding gas.
The TruPrint 2000 works with TruTops Print, the company’s proprietary software that has also been further enhanced throughout 2023.
“Users can now print parts with extreme overhang angles as low as 15 degrees without requiring support structures. In the past, users had to print support structures together with the part to anchor the part to the platform. These structures also serve to dissipate heat from the printed part and prevent internal tensions and deformations during printing. But TRUMPF’s innovative new technology means that many 3D printing applications can now be carried out without those supportive structures, even when tackling hard-to-process materials such as stainless steel,” the company explains.
While a key focus is made on medical engineering here, it should be noted that 3D printers from TRUMPF are often used in a wide range of industries such as tooling, molding, aerospace and automotive.
Other applications where TRUMPF has delivered productivity
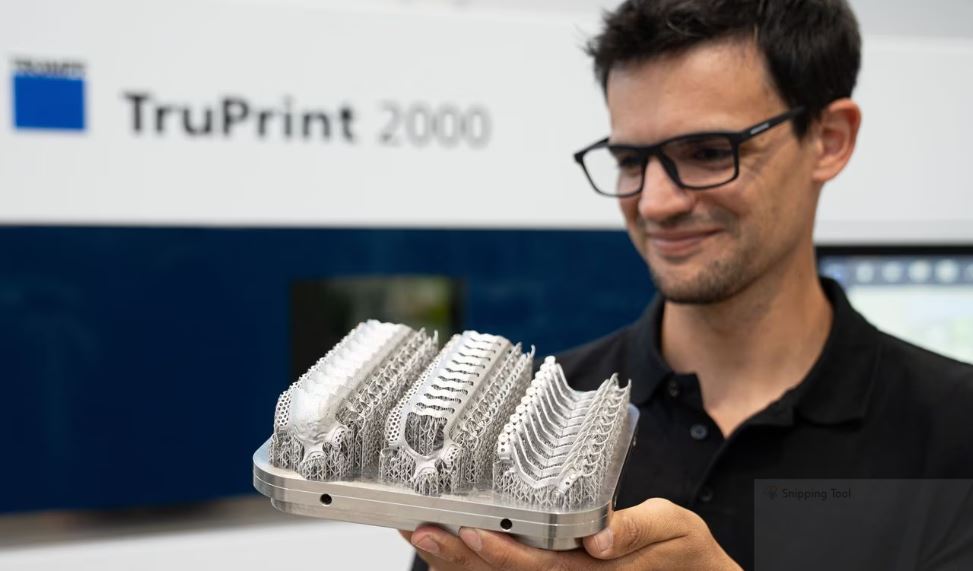
One sector where TRUMPF has shined this year is the bicycle industry. A plethora of examples have demonstrated how AM continuously stands out in this industry as bike manufacturers are continuously looking to unlock new designs, and most importantly to manufacture with lighter materials.
If you’re a cyclist, you probably know that with a light bike, you can ride faster, and easily on hills. With titanium and titanium alloys, it is possible to produce light, strong and durable parts – compared to carbon fiber which may be damaged under certain strains.
TRUMPF and bicycle brake manufacturer Trickstuff have been presenting 3D printed titanium brake levers for bicycles for the first time at the Eurobike bicycle trade show in Frankfurt.
“3D printing is what makes the cost-effective processing of titanium possible in the first place. Manufacturers can use 3D printers to customize brake levers. This does not only apply to the design of the titanium components. Manufacturers can also customize the lever forces of the brake to suit the cyclist. TRUMPF 3D printers also allow companies in the bicycle industry to speed up their prototyping,” the company comments.
What’s next?
One thing we have learned from the company is that it focuses on the entire process chain to further enhance productivity. A key success to achieving true productivity lies in improving the process speed. While its 3D printers are already one of the fastest in their league with significantly reduced non-productive times, for example, due to the outsourced unpacking station and the multilaser principle, TRUMPF continues to commit to improving with automation solutions for the upstream and downstream work steps.
When asked what makes it stand out from the crowd, TRUMPF says that it has built up expertise in laser, machine, monitoring and powder and relies on its own value chain for 3D printing.
“TRUMPF is one of the world market leaders in industrial laser technology. As one of the few suppliers of 3D printing, TRUMPF develops and produces the beam sources, including optics and sensor technology, itself. The components of TRUMPF printers interact perfectly and have been tested for industrial series production. Machine tools for flexible sheet metal have been TRUMPF’s core business for almost 100 years. As such, TRUMPF brings industrial expertise to the table like no other company in 3D printing. TRUMPF machines impress above all with their high robustness and reliability, and this also applies to 3D printing. When it comes to 3D printing, TRUMPF customers receive a complete solution that covers the entire additive manufacturing process chain. Everything from a single source is better than solutions thrown together,” the company concludes.
Remember, you can post job opportunities in the AM Industry on 3D ADEPT Media free of charge or look for a job via our job board. Make sure to follow us on our social networks and subscribe to our weekly newsletter : Facebook, Twitter, LinkedIn & Instagram ! If you want to be featured in the next issue of our digital magazine or if you hear a story that needs to be heard, make sure to send it to contact@3dadept.com