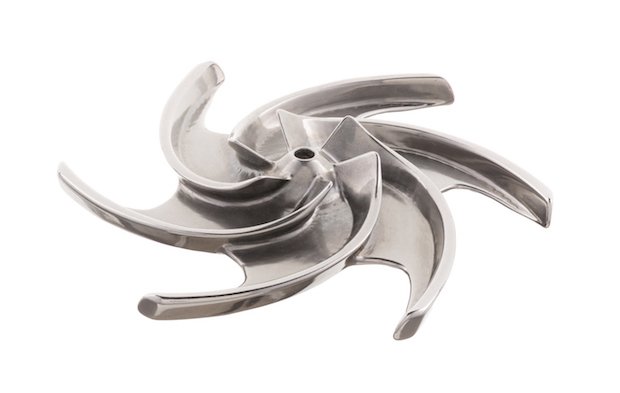
Desktop Metal has added 316L stainless steel to its 3D Printing materials portfolio. Intended for the Studio System™, the material can be used in medical, extreme temperature, highly corrosive and marine-grade environments.
Acknowledged for its corrosion resistance and excellent mechanical properties at extreme temperatures, the 3D printing material stainless steel has a lot of variables and over time, is increasingly adopted by a wide range of metal 3D printing specialists. ExOne for instance added 304L stainless steel to its portfolio and ITAMCO additively manufactured parts made with EOS 17-4 PH IndustryLine metal powder that exceeded 17-4 PH Stainless Steel in tensile strength. Both stainless steel-based materials were exploited in demanding industrial environments.
Burlington-based metal 3D Printing specialist also recognizes the potential of this material. For the CEO and co-founder Ric Fulop, “the addition of 316L enables engineers to print metal parts for a wide range of applications, including engine parts, laboratory equipment, pulp and paper manufacturing, medical devices, chemical and petrochemical processing, kitchen appliances, jewelry and even cryogenic tools and equipment. Teams are now able to iterate quickly on 316L prototypes, print complex geometries that are not possible with most manufacturing methods, and produce end use parts cost-effectively.”
A few examples of applications carried out with their flagship product, the Studio System, include a combustion fuel nozzle for marine tankers, customized ring splint for medical use or Impeller for harsh environments.
The Beth Israel Deaconess Medical Center used Desktop Metal’s material for their ring splint. Dedicated to the medical industry, the ring splint enables to limit the range of motion of injured limbs. Usually made injected-molded plastic, the only thing with this process is that the parts tend to break after a short period of time.
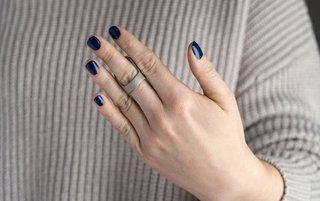
The medical center therefore decided to customize it by 3D printing in 316L and benefits from an aesthetic finish and increased durability.
“Being able to 3D print medical grade steel parts like this finger splint, which is customized to the patient anatomy, offers many advantages as compared to previous fabrication methods that take longer and may have lower efficacy,” said Jim S. Wu, MD, Chief of Musculoskeletal Radiology and Intervention at Beth Israel Deaconess Medical Center, and Associate Professor at Harvard Medical School.
For further information about 3D Printing, follow us on our social networks and subscribe to our newsletter
Would you like to subscribe to 3D Adept Mag? Would you like to be featured in the next issue of our digital magazine? Send us an email at contact@3dadept.com
//pagead2.googlesyndication.com/pagead/js/adsbygoogle.js (adsbygoogle = window.adsbygoogle || []).push({});