In general, many seem to agree with the design flexibility and material efficiency AM provides but despite those undeniable benefits, one thing AM technologies manufacturers struggle to significantly improve in their process is speed. We came to realize that there is one manufacturing technique that is particularly acknowledged for its ability to meet production speed requirements for certain industries: Supersonic Particle Deposition (SPD also known as Cold-Spray).
This exclusive feature aims to discuss the methods, challenges, and applications of this process and the reasons why it is uniquely positioned to meet the requirements of certain industries. To discuss these topics, we have invited two companies that have made this technique their core business: Titomic and SPEE3D. Jeff Lang, Founder of Titomic Limited, Executive Director and CTO as well as SPEE3D co-founders Byron Kennedy and Steven Camilleri are the main contributors of this exclusive feature.
Manufacturing at double speed
From an economic point of view, the ideal speed of manufacturing requires the perfect balance between the physical processes of production, the wider system that allows these processes to operate, and the co-ordination of a supply chain in the pursuit of meeting customer needs.
However, in manufacturing – and in additive manufacturing processes especially, things are slightly different. Speed starts raising challenges when manufacturers have to deal with short lead-times and when the goal is large-scale production. From this manufacturing perspective, operators who work on metal AM will tend to look for a process that opens up more possibilities in terms of materials and that would withstand very high melting temperatures to go very fast.
The only thing is, as per the words of Jeff Lang, “the main factor, the metal 3D printing industry has struggled to realise, is its viability against the speed of traditional metal fabrication for industrial-scale metal parts, especially in the aerospace and defence industries.”
Indeed, “in traditional AM, the metal powder is melted with a laser – that process takes a solid powder, melts it into a liquid, and then reforms that into a solid. That process takes time, based on physics, and is easy to calculate. In order to speed this process up for more efficiency, you needed a process that does not melt the powder”, explain Byron Kennedy and Steven Camilleri.
Those challenges, therefore, lead to the increasing interest in supersonic particle deposition (SPD) additive manufacturing (AM) technology (also known as Cold-Spray).
So, what is Cold Spray?
As Titomic’s Jeff Lang notes, Supersonic Particle Deposition (Cold-Spray) has been in commercial use for over 30 years but its application in additive manufacturing is quite recent.
Cold Spray is defined as a materials consolidation process whereby micron-sized particles of a metal, ceramic, and/or polymer are accelerated through a spray gun with a De Laval rocket nozzle using a heated high-pressure gas (i.e. helium or nitrogen). In this process, particles are said to exit at supersonic velocities and consolidate upon impacting a suitable surface to form a coating or a near-net shaped part using ballistic impingement.
The key innovation in this process would be the use of a “de Laval nozzle”, a convergent-divergent nozzle that enables the metal powder to reach supersonic speeds. According to experts, the process has gained traction in additive manufacturing due to its ability to apply multi-component coatings.
Furthermore, unlike other powder deposition technologies, four main benefits characterize SPD: no heat-affected zone, no interface oxides, generation of surface compressive stresses as well as no thickness limitations.
This means that bonding between materials and particles does not usually require a thermal source. There is no melting and cooling cycle as the process is a solid-state one.
Materials Considerations & Post-processing
Since there is no heat, operators can easily explore the use of reactive materials such as titanium, aluminium, and magnesium.
According to SPEE3D’s founders, “every powder has what is called a deposition speed. When accelerating a power if its speed is too slow, the powder bounces off, too fast, and the powder will erode the substrate. In between is what we call the “speed deposition window”. For example, copper can be deposited at 450 metres per second, aluminium at 600 metres per second, and stainless steel at 700 metres per second. These are the ideal speeds.”
As far as SPEE3D is concerned, the founders explain that they accelerate “the power to in-between Mach 1.5 and Mach 2 depending on the material we use (supersonic speed is greater than Mach 1 or greater than 343 metres per second).”
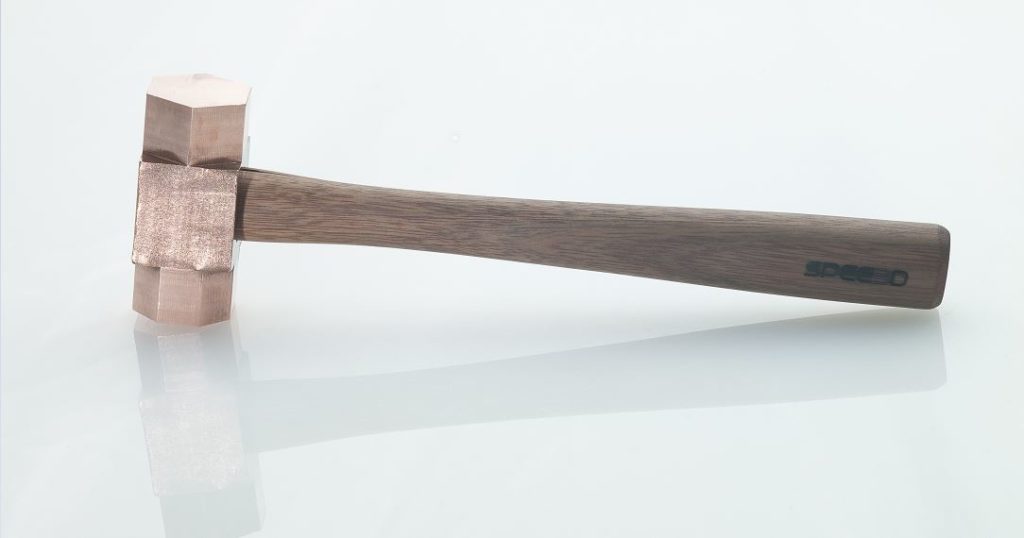
However, attention should be devoted to the ductility of the sprayed material. Indeed, less ductile powders are less subject to deformation. In this case, the 3D printed part reveals a brittleness that one does not see in thermally processed parts. Interestingly, thermal post-processing such as Hot Isostatic Pressing (HIP) can remove these effects. On the other hand, more ductile materials (e.g.: aluminium, copper) do not present this characteristic, therefore require less post-processing.
Different roads lead to “speed”
Amid this array of characteristics, the most impressing feature of cold spray remains speed. Needless to say, that to develop their technology, each manufacturer has brought something unique to their process.
Branded as Titomic Kinetic Fusion (TKFTM), Titomic’s patented process allows for the production of industrial-scale additive manufacturing of Titanium parts.
Lang recalls that in 2008, he was approached by the CSIRO, Australia’s national science organisation, to look at creating a holistic value chain around Titanium of which Australia has the largest mineral reserves of this resource in the world.
“To unlock this value chain required a deep investigation into production technologies for Titanium fabrication with the intent to find the most viable process with the most unique value proposition. After investigating various AM technologies for producing Titanium parts, the one apparent thing was the limitations of build speed and size with melt-based AM processes. As I was looking to utilise large quantities of Titanium powder, I needed to find a suitable AM technology that was commercially viable against traditional Titanium fabrication methods”, Lang explains.
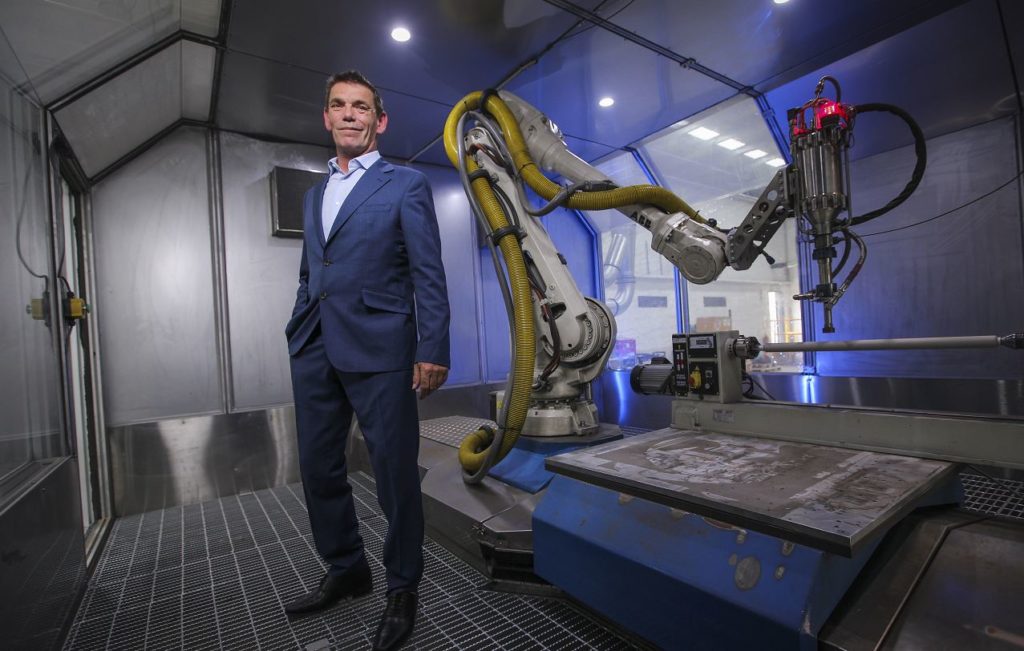
Lang realized that due to its high- deposition rates, the high-performance metal coating process was a great bet to produce AM parts faster and “without the size constraints of melt-based 3D printers.” Today, the metal 3D printer manufacturer commercializes the TKF1000 system that delivers build speeds between 6-10 kg per hour depending on the type of metallic material used and its density.
“Our custom TKF systems can be configured with multiple heads to deliver build speeds of up to 75 kg per hour. As with all additive manufacturing equipment suppliers, there are some bold claims as far as build speeds that are unrealistic even though the machine may be rated to that maximum. On a single TKF system head, we can build 30-45 kg per hour, however there would be considerable porosity at these build speeds which affects the mechanical properties”, the expert adds.
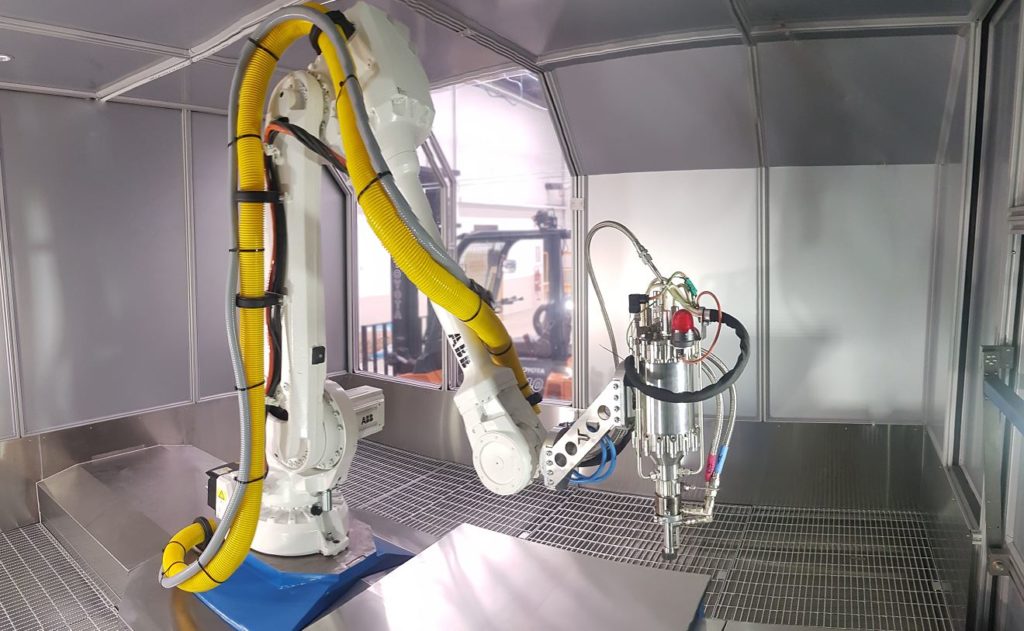
In the case of SPEE3D, it’s a different route that led to the development of their cold spray AM technology. With a decade of experience in manufacturing, SPEE3D is not Kennedy and Camilleri’s first entrepreneurial journey. In the life they had prior to SPEE3D, they realized the potential of metal 3D printing but also deplored its limitations.
“The challenge, however, was that traditional metal AM was too expensive and too slow. So, when finishing up with the manufacturing company, we decided to enter the additive manufacturing space. We began to look for a manufacturing-friendly AM technology – a fast and low cost technology. That is when we came across Cold Spray, which at the time was primarily used in military repair applications, and in a “manual way”. We found that this was something that could be fixed. So, with a background in Control Systems and Robotics, we took a manual Cold Spray Process and turned that into a metal AM machine” the founders point out.
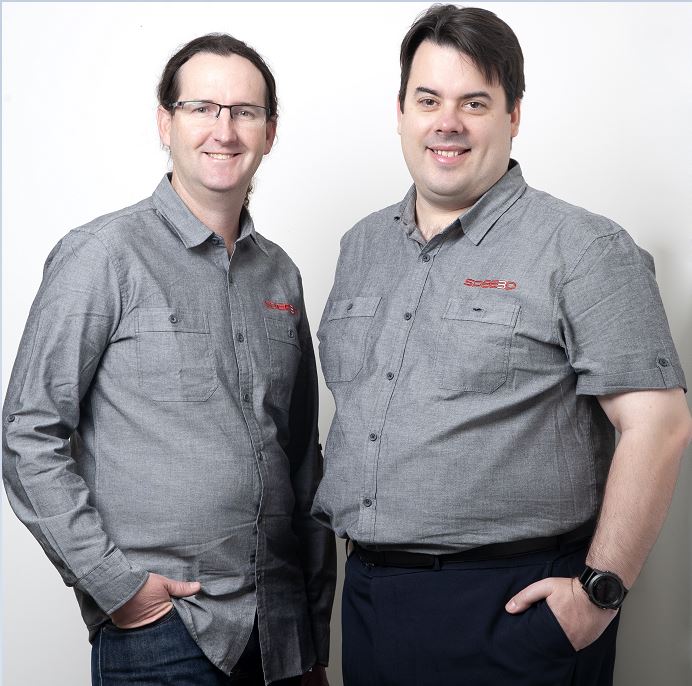
Both founders share their long-term goals : “the limitation in SPEE3D’s printers is not the deposition speed, but the robotics keeping up with the Spray (Cold Spray). Theoretically, the process could be a lot faster, making the AM process even easier, and this what SPEE3D continuously works on as its long-term goal.”

A closer look at those two metal 3D printing processes shows that both technologies enable easy optimization of the build speed to achieve the desired geometries and mechanical properties – not to mention that post-processing (heat treating and/or post-machining) very much depends on the initial choice of material.
Applications & challenges
As it was first acknowledged as a metallic repair technology, first applications of SPD were seen in the repair of magnesium helicopter gearboxes. Manufacturers highlight the technology capabilities to manufacture parts such as tools, brackets, pumps, and as well as in specialty components. According to researchers, this primary focus on military applications is due to the need for frequent repairs on the battlefield.
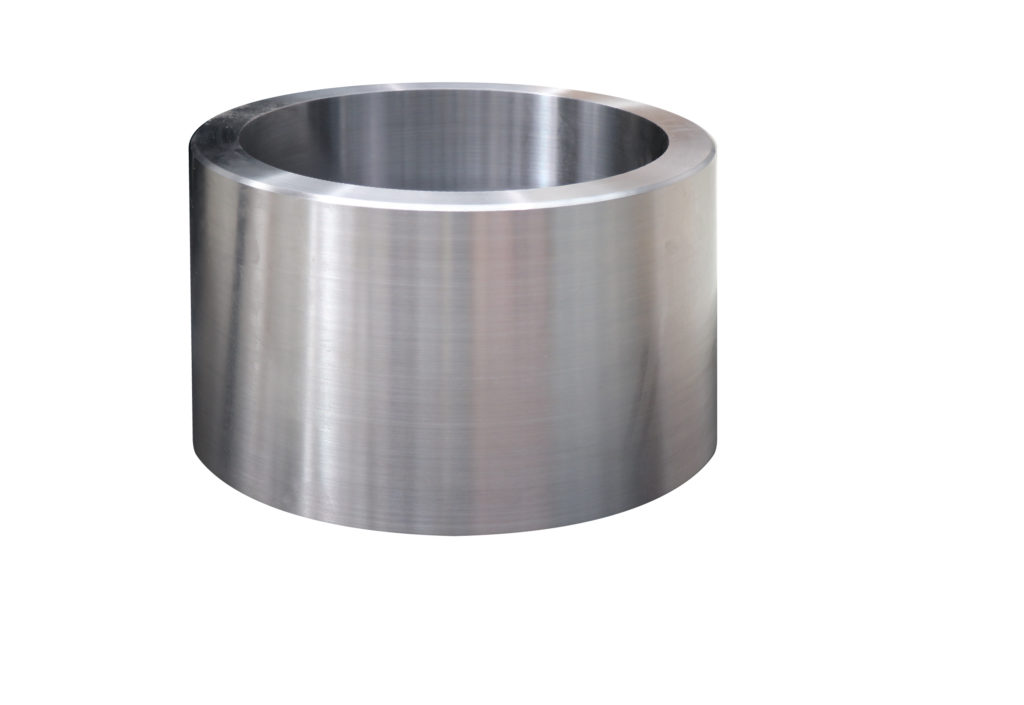
Speaking of helicopter gearboxes, Danielle Cote, assistant professor of materials science and engineering and director of WPI’s Center for Materials Processing Data notes: “If you need to replace a part like that, it can take months or even years, and the cost is significant—assuming that the part is available or even still being made. To repair a gearbox with cold spray, you need alloys with high strength, toughness, and ductility. Our methodology will enable us to develop powders that can be used to effectively repair or even manufacture parts like that and get helicopters back in the air quickly. The Army is especially interested in portable cold spray systems, but the technology can also be used on a larger scale—in industry, for example—and it will be exciting to see how robots can help expand the use of this and other additive manufacturing processes.”
Apart from military and defence applications, we have also seen Cold Spray AM applications in the space industry and certain luxurious consumer products.
Nevertheless, Cold Spray AM seems to have great promise for mid-size companies. We cannot deny the technology readiness to meet certain industries’ demands but its ability to meet large-scale production requirements remains to be demonstrated.
Furthermore, researchers strongly encourage manufacturers to have a close look at materials selection as well as the microstructure and mechanical properties of deposits that may depend on different process parameters. In this vein, geometric control can often be a quite disturbing issue. “Low geometric control is attributed to a range of key issues that limit the application of additive manufacturing technologies such as the necessity of post-machining, difficulty in fabricating complex shapes, geometry-induced property variations, and inconsistent quality of fabricated parts. Therefore, addressing the challenge of geometric control is undoubtedly of great importance in Cold Spray AM as well as other high-speed additive manufacturing technologies”, the study reads.
Concluding notes
Cold spray AM has opened up a new niche within the additive manufacturing industry due to its ability to manufacture near-net-shape parts in a variety of metals. The military industry is one of the primary fields that sees potential in the technology. Nevertheless, the adoption of the technology might be extended to sectors of activity that are looking to significantly reduce machining time and material waste and to produce parts in remote locations.
This exclusive feature has first been published in the January/February Issue of 3D ADEPT Mag.