In the January-February issue of 3D ADEPT Mag (Focus on YOU Series – pp 18-21), Thermwood told 3D ADEPT Media that one of the main challenges the team was trying to address was the reduction of the operator’s need to monitor temperatures during the print process.
“Currently a thermal imaging camera is utilized, but this still requires the operator to manually change settings during the print process. Even though modifications are rarely needed, an operator needs to be in place when control parameters need to be modified. We anticipate the operator’s participation will be greatly reduced by LSAM control capabilities”, Dennis Palmer, Vice President of Sales told 3D ADEPT Media.
After months of in-house development, the manufacturer of large format 3D printing hardware and services announces a new LSAM additive print technical capability that addresses this temperature issue.
From now on, operators who will utilize Thermwood’s LSAM in their production line will automatically monitor print temperature. The new feature also enhances fusion between large-scale thermoplastic printed layers, no matter what the application is.
Achieving superior printed part quality with “Thermal Sensor Layer Automation”
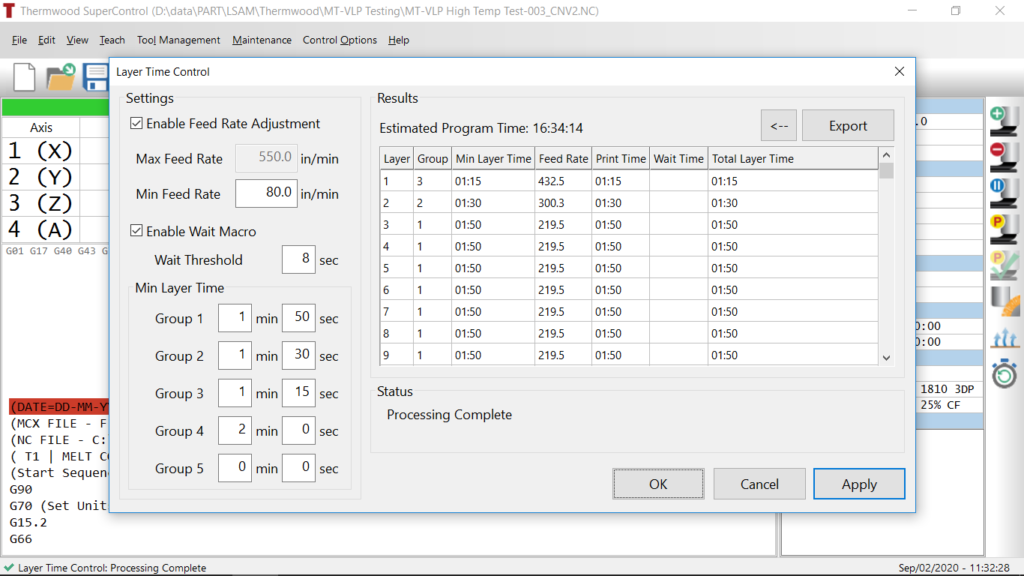
To control the temperature, the US-based company has integrated a “Thermal Sensor Layer Automation” system in its machines. It explains that the system measures the temperature of a printed layer just before a new bead is added which enables the printer to automatically regulate the feed speed, using the “Layer Time Control” option. With this adjustment, the printing process would be at, or very close to, the perfect temperature needed to achieve the best possible layer-to-layer fusion.
This also means that monitoring temperature will no longer required from the operator to have extensive expertise in LSAM. According to Thermwood, the new print technical capability requires “a non-contact temperature sensor which rotates about the print nozzle under servo control and continuously measures the temperature of the existing layer less than a half inch in front of the moving print nozzle. This provides precise feedback of the temperature at the moment of layer fusion, insuring integrity of the bond being generated at every point on every layer”.
As seen in every automated feature, the new system developed by Thermwood also requires to process data. In this specific case, they are coming from the probe and are assessed by an advanced algorithm that regulates the speed at which each layer is printed.
Interestingly, the algorithm also assesses the temperature during the printing process as well as the changing geometry of the part as it is produced. Before this automation of the process, the operator used to define the print speed in the print CNC program. Reality shows that the print environment is very fluctuating, and these fluctuations depend on several variables, which makes the manual control of temperature complicated to handle.
“With Thermwood’s new system, optimum print temperature is now part of the parameters stored in the control for each polymer and is determined when the polymer is first qualified. To run a specific material using a properly equipped LSAM, it is only necessary to load a part program, specify the material and turn it on. The entire build process, including all temperature control, is then pretty well automatic”, the company explains.
Assuring quality control basis for critical parts
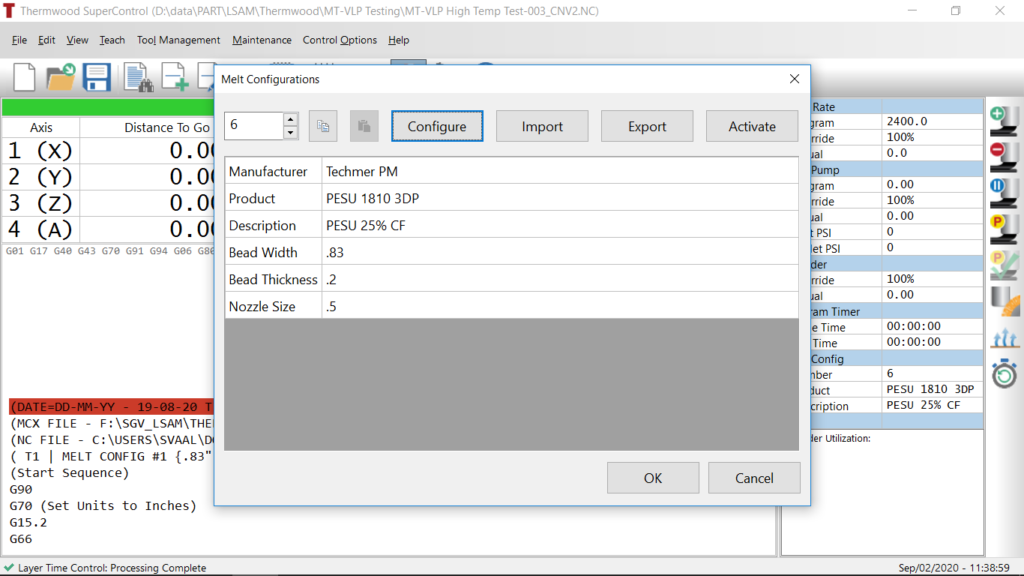
The icing on the cake? The operator can get different forms of temperature data from the print process. On a digital screen that reveals the temperature at a point of printing as well as the average temperature for the layer being printed, information is colour coded to facilitate the understanding of the process by the operator. It goes without saying that, at the end of the printing process, a detailed report the print temperature profile of each printed layer can be obtained by the operator.
Such report reveals its importance during the production of critical parts such as flying parts on an aircraft that require quality control to ensure their compliance with requirements from their industries.
Last but not least, “for the first time in extruder based large scale additive manufacturing, the temperature at the moment of layer fusion can be measured and controlled. This opens the possibility for more advanced research, focused on the very core of an extruder based print process. Research using this technology should result in a better, more thorough understanding of the print and layer fusion process that is at the very core of this emerging industry” Thermwood concludes.
Remember, you can post job opportunities in the AM Industry on 3D ADEPT Media free of charge or look for a job via our job board. Make sure to follow us on our social networks and subscribe to our weekly newsletter : Facebook, Twitter, LinkedIn & Instagram ! If you want to be featured in the next issue of our digital magazine or if you hear a story that needs to be heard, make sure to send it to contact@3dadept.com