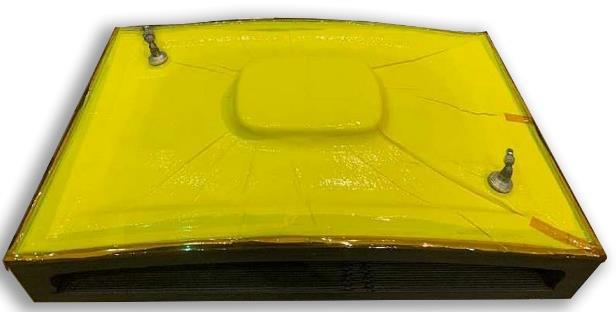
Autoclave tooling has become pivotal for processing high quality polymer composite aerospace structural components. For an industry like the aerospace, an investment in such equipment needs to be done very strategically because its manufacturing often comes with certain challenges.
The fabrication of this component usually requires a rigid mold that defines the final shape of the composite part, and the final part should deliver high-performance properties and withstand austere environments.
SABIC’s Specialties business and Thermwood Corporation recently explored a new manufacturing approach to produce autoclaves. In the additive manufacturing industry, SABIC is known for its ability to deliver tailor-made AM materials through a specific chain of collaborations. The company has particularly built expertise in the manufacturing of 3D printed parts requiring the use of composite materials.
Thermwood, on the other hand is one of the three companies providing very large format 3D printing hardware and services with composite chopped Fiber Reinforced Polymer (FPR) pellet materials.
As part of this project, both companies leverage their respective expertise to produce tools with complex geometry that can withstand multiple cycles of thermoset composite autoclaving while maintaining dimensional accuracy.
The manufacturing process
Both companies first assessed the viability of their solution that consists in leveraging Thermwood’s large format additive manufacturing (LFAM) technology and high performance thermoplastics from SABIC.
To do so, the 3D printer manufacturer has fabricated an aerospace panel tool of 1150mm x 760mm. The printing process of this tool required eight hours and they required 12 more hours for machining using the LSAM®printer and SABIC’s LNP™ THERMOCOMP™ AM EC004XXAR1 compound. The latter is a 20 percent carbon fiber-filled ULTEM™ resin material.
After the 3D scanning of the printed tool was performed – using a CreaformHandy SCAN 700, SABIC produced the required composite parts using the printed tool and an epoxy resin on a high-modulus carbon fiber weave named HexPlyF263.
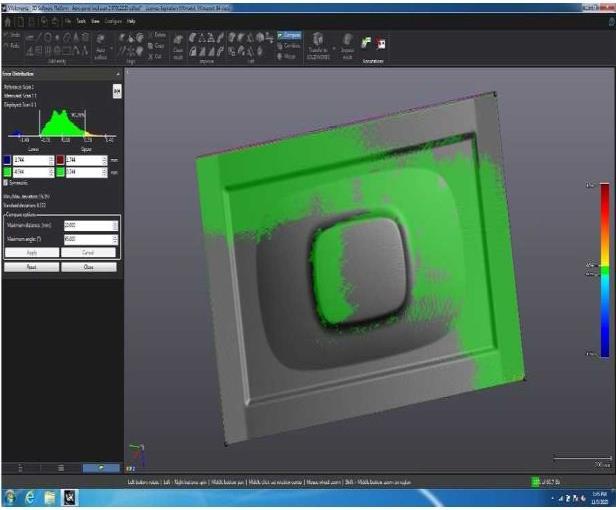
The materials’ producer reported that “the tool was visually inspected after each autoclave cycle and no signs of wear were observed. Furthermore, after 10 autoclave cycles, the tool was scanned againand those findings were compared to the original scan data. No significant movement was observedand dimensional differences were within the error accuracy of the scanning equipment.”
To ensure the viability of the process, the team compared tool dimensions to end part dimensions in the X and Z directions. In this vein, they placed pins in 3D printed flat plaques and results revealed that there was only approximately a 0.025 percent difference in the X-direction and a 0.25 percent in the Z-direction. Those results corroborate the CLTE testing per ASTM E-831 and outlines the anisotropic behaviour of the part.
Major benefits
Both companies have been able to deliver a high-performance autoclave tool in less time than one usually does with conventional manufacturing processes and in a more cost-effective way. Not to mention that, further LFAM autoclave tool testing beyond 10 cycles can be considered to exemplify further efficiencies compared to traditional processes.
Remember, you can post job opportunities in the AM Industry on 3D ADEPT Media free of charge or look for a job via our job board. Make sure to follow us on our social networks and subscribe to our weekly newsletter : Facebook, Twitter, LinkedIn & Instagram ! If you want to be featured in the next issue of our digital magazine or if you hear a story that needs to be heard, make sure to send it to contact@3dadept.com