When Additive Manufacturing comes to composites fabrication, we did not expect this combination to work and lead to the development of some niche yet interesting applications for the industry. In their latest report, SmarTech Analysis announced this market segment would surpass $9 Billion in 2028. What explains the host of new opportunities for the composites industry? More importantly, what drives this market segment?
Composite 3D printing is a key topic that has been addressed in the September-October Issue of 3D ADEPT Mag. Today, we would like to share the series of questions, Kim Ly, Lead Scientist at SABIC, answered as part of this dossier.
In what form do we find composite materials for AM (liquid, powder or filament)?
SABIC offers a portfolio of glass- and carbon-reinforced polymer pelletized compounds used in Large Format Additive Manufacturing (LFAM), also known as Fused Granular Fabrication or pellet extrusion Additive Manufacturing (AM). LFAM is commonly associated with print envelopes of 1 cubic meter and larger and pellet feed rates ranging from 5-250 kg/hr. Our primary base polymers include ABS (Acrylonitrile-Butadiene-Styrene), PC (general purpose and high-heat polycarbonate), PPE (NORYL™ polyphenylene ether resin), and PEI (ULTEM™ polyetherimide resin), as well as a new compound based on our FST PC for enhanced performance with respect to low flame, smoke and toxicity.
The application base for LFAM is proliferating in both tooling and direct manufacture of finished parts. The tooling category encompasses general purpose jigs, fixtures and manufacturing aids, specialty molds (such as foundry patterns and architectural forms for pouring precast concrete) as well as tooling designed for use at elevated temperatures (for example, autoclavable composite layup tools). Printed components of the Olli, Local Motors’ self-driving electric vehicle, are among the best-known examples of LFAM applied to direct manufacturing. Printing of decorative and structural architectural components with these composite materials is also growing at a rapid rate.
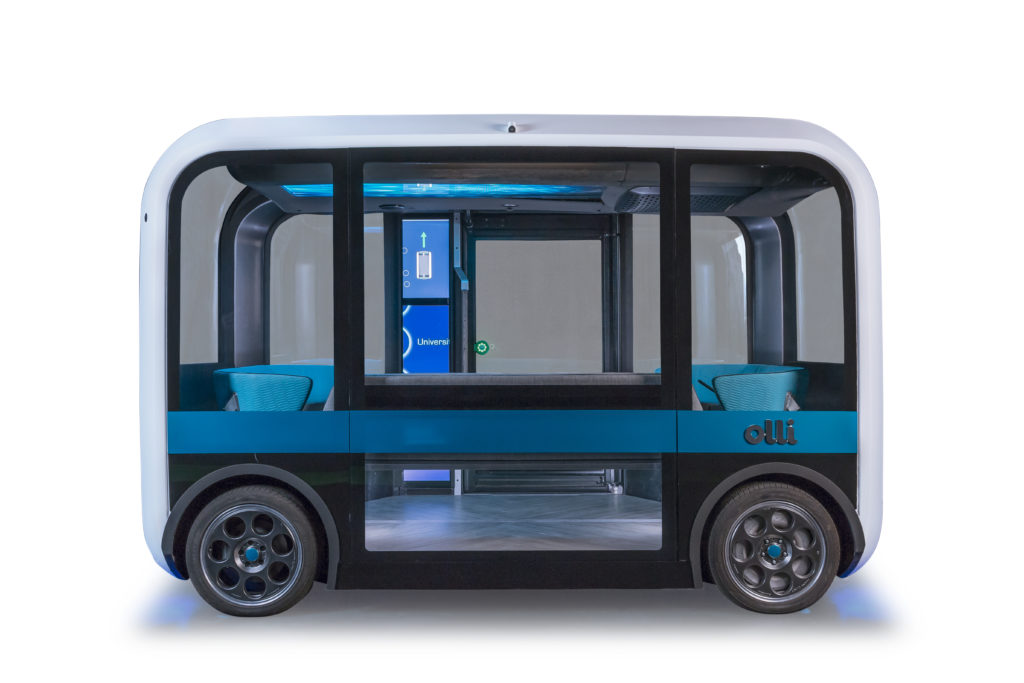
What’s the difference between Continuous vs Chopped fibres
Printers built for LFAM utilize compounds based on chopped fiber to take advantage of the strength properties along with widespread availability and lower cost of pellets as compared to filaments. Use of chopped fiber provides distributed reinforcement throughout the matrix of the print. Printers that incorporate continuous fiber into a matrix of molten polymer have more recently been introduced and offer additional functional capabilities; however, use of continuous fiber may have some limitations on design and full incorporation into the matrix, particularly in gantry-based AM systems.
Carbon-fiber remains the most-used material in Composite 3D printing. Why?
For the primary application uses to date in LFAM, carbon-fiber and glass-fiber are by far most commonly used. While carbon-fiber-reinforced compounds are more expensive than glass-fiber compounds, carbon fiber offers higher strength and modulus and thermal conductivity and a lower coefficient of thermal expansion, all highly critical for tooling applications. Carbon-fiber compounds are also less prone to warpage, an important benefit for robust manufacturing.
What other 3D printing materials are suitable for composite 3D printing?
To date, LFAM has been largely focused on the carbon- and glass-fiber compounds; however, SABIC’s comprehensive LNP™ product portfolio offers over 10 different filler systems in 25 polymers to provide potential solutions for applications with performance requirements such as wear and friction, thermal management, shielding and electrical conductivity. We work with customers to review their specific application requirements and provide material options for printing. To date, amorphous polymers such as ABS, PC, and PEI have been most commonly used in LFAM printers because they are more easily processed over a wider range of operating parameters; however, there is increasing interest in developing compounds based on semi-crystalline polymers such as PP, PBT, PEEK, and nylon.
What challenges can operators encounter at the materials level?
We have learned that many early LFAM adopters have less experience processing polymers than our traditional customer base in injection molding, particularly in the areas of material selection and Design for Additive Manufacturing. Also, understanding best practices in material handling, drying, and processing are critical since there may be differences in the behavior of grades, even within the same polymer family. For that reason, SABIC also provides support including fundamental polymer education when needed. Further, since we use our Large Format printer to screen compounds under development, we are very aware of the potential design and processing challenges that can arise, so we offer to review proposed print configurations and can be present either in person or online during first prints to help diagnose any issues. This can help accelerate the learning curve for our customers.
As a material producer, do you think the need for open-3D printers is also prevalent to foster the adoption of composite 3D printing?
Yes. Fortunately, by definition, LFAM is open format. Most, if not all, equipment types allow storing setup files for individual compounds to facilitate starting a print. However, there is also a need to build the proper knowledge of polymer processing as it is not as simple as “plug and play”.
Anything else you would like to share ?
LFAM as a technology is less than 10 years old and the introduction of new equipment is accelerating. With this growth, comes a number of equipment features aimed at improving print robustness and process economics. Service bureaus are emerging to fill the gap and allow potential adopters to validate the technology before making a capital investment in printing capacity. The value proposition in creating large parts and tools in days rather than months includes speed-to-market, reduced development costs, and often increased revenue from faster sales.
From the perspective of the material supplier, improvements in material quality and consistency continue to be a primary focus. Because prints can span hours or even days of run time, errors that may occur well into the printing cycle can result in material waste and highlights the need to minimize process fluctuation. Grades for LFAM processing help address process optimization and are contributing to the growing adoption of LFAM and related application successes.
Remember, you can post AM job opportunities for free on 3D ADEPT Media or look for a job via our job board. Make sure to follow us on our social networks and subscribe to our weekly newsletter: Facebook, Twitter, LinkedIn & Instagram! If you want to be featured in the next issue of our digital magazine or if you hear a story that needs to be heard, make sure to send it to contact@3dadept.com