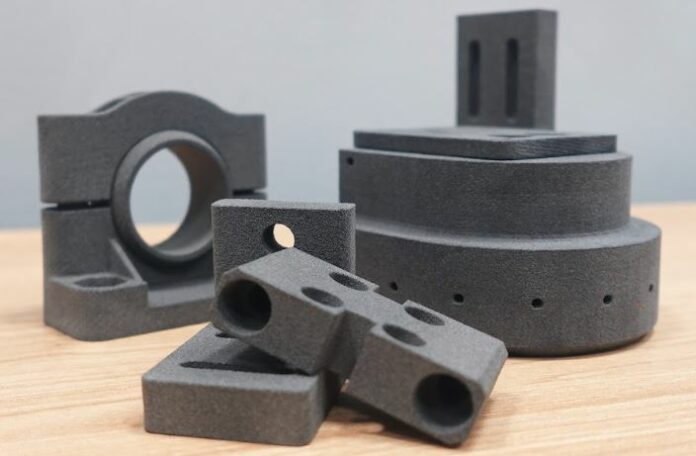
Polish company Johnson Matthey Battery Systems successfully manufactured mechanically resistant 3D printed spare parts for its complex battery systems prototype with the help of Sintratec’s S2 SLS 3D printer.
The Polish company has already pushed the boundaries of innovation in lithium-ion batteries development and Sintratec S2 took that a step ahead.
In the last 20 years Johnson Matthey Battery Systems has produced over 3.5 million lithium-ion batteries every year from their base in the Special Economic Zone in Gliwice, Poland. Most of these advanced battery systems have been used across industries like e-bikes to power tools to healthcare and industrial cleaning equipment.
Now, the battery systems manufacturer has used Sintratec S2, a Selective Laser Sintering or SLS 3D printer in its research and development process to create 3D printed spare parts for the battery system.

The Sintratec’s All-Material Platform was also a key component of the production tools used by the company. As a reminder, the All-MaterialPlatform is a modular and scalable manufacturing platform made up of two main parts for SLS 3D printing.
The test and validation team Leader at Johnson Matthey Battery Systems, Jakub Szafrański revealed that the company reduced cost and lead time for spare parts and prototypes by using Sintratec S2 SLS Printer instead of outsourcing.
The battery systems manufacturer’s in-house engineers rapidly 3D printed the spare parts by verifying the adapters, jigs and machine components using PA12 nylon

Szafrański further explained how the SLS 3D printer streamlined the 3D printed spare parts production.
“Another advantage of the Sintratec S2 printer is its ability to increase efficiency with a relatively small financial investment. Instead of an entire system, we have added an additional material unit and the performance almost doubled. While one build module is printing, you can sieve the powder and prepare the next batch of components with the other”, said Szafrański.
Through this experience, the Polish company understood the benefits of selective laser sintering in speeding up prototyping and optimizing production along with the importance of staying agile and responsive in the market.
Remember, you can post job opportunities in the AM Industry on 3D ADEPT Media free of charge or look for a job via our job board. Make sure to follow us on our social networks and subscribe to our weekly newsletter : Facebook, Twitter, LinkedIn & Instagram ! If you want to be featured in the next issue of our digital magazine or if you hear a story that needs to be heard, make sure to send it to contact@3dadept.com