While we take great care not to use the buzzword “sustainability” without key data, we do recognize that it will take time for OEMs and AM users to provide quantitative analysis that demonstrates how efficient AM technology aligns with a “sustainability vision” that takes into account the “triple bottom line” we highlighted in various ways in the latest edition of 3D ADEPT Mag. What we can do though, is to highlight the arguments that would play to the strengths of manufacturers’ technologies, arguments they may focus on, to deep dive into this much-needed quantitative analysis. This is what this article ambitions to explore with a key focus on Large-Scale Additive Manufacturing, short for LSAM.
Developed by Thermwood, machine manufacturer headquartered in Indiana, USA, LSAM appeared on a market as an alternative to the widely spread polymer 3D printing approach which consists in fabricating the part with a print bead onto a hot table, in a heated chamber, keeping the fabricated component hot until the manufacturing is complete. For the provider of large format 3D printing hardware and services with composite chopped Fiber Reinforced Polymer (FPR) pellet materials, this approach was hard to scale up, especially for large near-net-shape parts, hence the focus on the development of dedicated systems. The latter feature a large bead, can 3D print at room temperature in an essentially “continuous cooling” process. It’s been over five years that Thermwood has been tuning its processes, and so far, has demonstrated that there is a market for very large 3D printed parts.
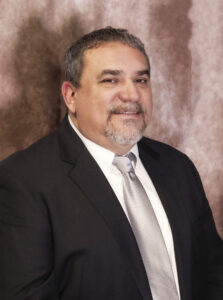
Over time, we witnessed the possibilities of Thermwood’s Large Scale Additive Manufacturing and we saw the development of new approaches and features such as the Vertical Layer Print (VLP) technology or the thermal sensor, that aim all to improve the manufacturing processes with these machines. “LSAM is a tool that when yielded by a skilled craftsman, can produce items not originally considered for the technology. Prototyping of large components is of particular interest as of late. [However], Collaboration with industry to showcase what is achievable with Large Scale Additive is paramount in effectively getting the information across to the right people” Jim Bullis, VP of Sales at Thermwood told 3D ADEPT Media.
As the current manufacturing landscape is currently driven by the emergence of manufacturing processes that are enabling more cost, and resource efficient scale production through significant sustainability benefits, it makes sense to discuss how LSAM is contributing to this new era of manufacturing.
The sustainability performance indicators
There are currently various principles of sustainability that are explored and adopted in manufacturing. At 3D ADEPT, we believe that it should be a continuous journey where organizations should commit to focusing as much on social and environmental concerns as they do on profits (economic) hence the triple bottom line profit, people and planet. This journey doesn’t have to be taken in the rush. For many organizations, each of these bottom lines includes various categories and sometimes sub-categories that may serve as indicators of where to improve processes.
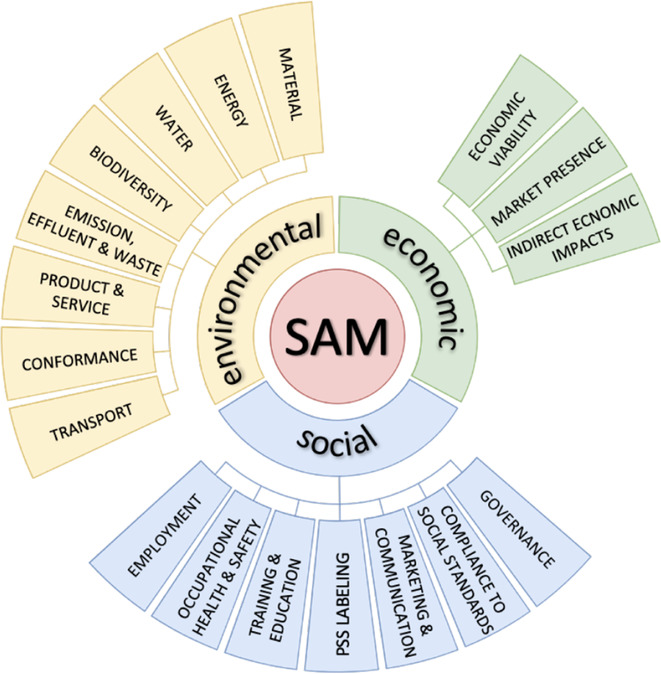
Interestingly, while the focus is often made on manufacturing processes, we come to realize that changes brought to one bottom line may positively affect other performance categories. That’s anyway what the example of Thermwood’s LSAM reveals.
The arguments that play to the strengths of LSAM
Needless to say that common characteristics of AM technologies in general imply common sustainability benefits. For example, since AM enables decentralized production – thus the ability to be closer to the point of consumption – this does not only simplify supply chains but also results in lower environmental impact and easy resource management.
One of the very first arguments that enables Thermwood to stand out from the crowd is the hybridization of its processes. Despite its flexibility, AM suffers from a bad reputation due to the fact that it often delivers poor surface finish and accuracy. Thermwood has alleviated this hurdle by combining CNC routers to 3D printing capabilities.
Simply put, after the 3D printing process of the part, it is trimmed to its exact desired size and shape using a CNC router. “The LSAM can perform both the “additive” and “subtractive” functions on the same machine. This approach, called “Near-Net shape”, uses carbon fiber reinforced thermoplastic material to quickly create a part that is nearly, but not exactly, the final net shape. The “subtractive” function then machines the part to the exact final net shape”, Dennis Palmer, Former Vice President of Sales at Thermwood once told 3D ADEPT Media.
This hybridization of AM and CNC machining is highly relevant in the context of future manufacturing. It removes the need for the inefficient and error-prone transfer and setup of parts, while saving large amounts of valuable shop floor space. In doing so, the LSAM user benefits from the economic sustainability of AM by increasing the profitability of capital investment (bottom line = profit).
Moreover, this hybridization of AM & CNC machining processes presents opportunities for the current workforce that has built up expertise in conventional manufacturing process. For this workforce, it won’t be difficult to translate their hard and soft skillsets into an industrial environment with AM
The second argument that is worth mentioning is recycled materials. We used to highlight reusable and recyclable powder materials or recycled filaments in other AM processes. It turns out that Thermwood’s LSAM machines can also process recycled composite chopped fiber-reinforced polymer (FRP) pellet materials, thus improving materials efficiency and reducing material waste by lowering the carbon footprint (bottom line = planet).
As a matter of fact, “recycled materials are currently being used in a variety of LSAM 3D printed applications”, Bullis notes. “Some of the complexities related to getting past prior experiments that may not have proven successful. Material producers are continuously working to develop new formulations. LSAM allows for owners/users to work directly with material producers to develop novel formulations that may provide a competitive edge. Users are not “handcuffed” to any particular material provider, this allows them to be more competitive”, he adds, speaking of the complexities in the utilization of FRP composite 3D printing.
A reduced number of processing steps. We see the ability to manufacture in one “piece” as a sustainable performance indicator as most manufacturing processes often require several processing steps and sometimes multiple machines to achieve the final part. “The LSAM flagship model can be up to 100’ long and 15’ wide” (2.5mx 0.4m) Bullis recalls. Being able to use an LSAM machine to create parts in their entirety may result in the reduction of energy needs, can also reflect on other cost considerations or categories.
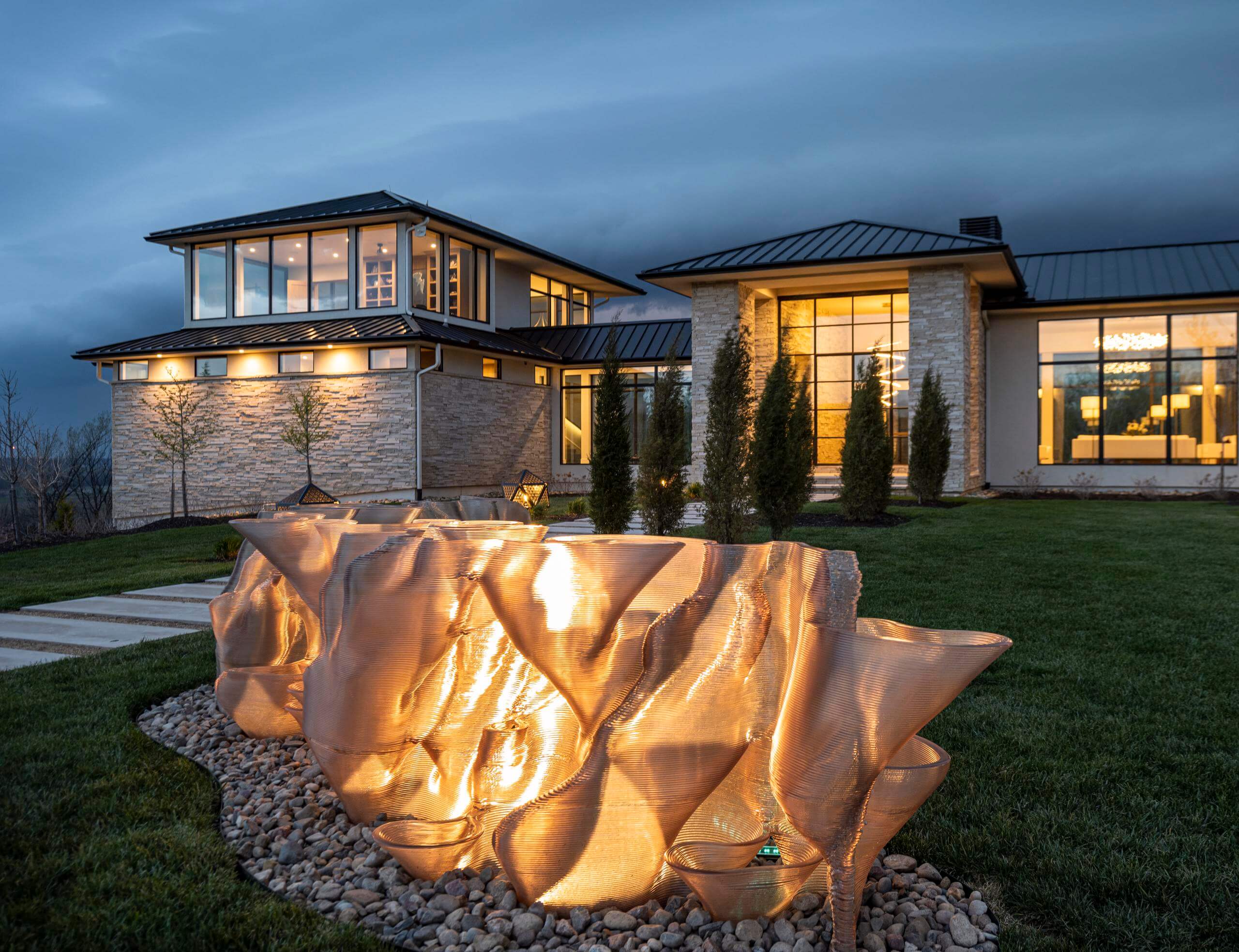
These arguments are the start of a much deeper conversation that we hope to continue with Thermwood moving forward. Indeed, while we want to educate and highlight the sustainable performance indicators that may result from the integration of LSAM into production environments, we also want to warn on these seemingly obvious benefits that AM might introduce which often result in faulty implications for the “green” credentials of the technology.
Remember, you can post job opportunities in the AM Industry on 3D ADEPT Media free of charge or look for a job via our job board. Make sure to follow us on our social networks and subscribe to our weekly newsletter : Facebook, Twitter, LinkedIn & Instagram ! If you want to be featured in the next issue of our digital magazine or if you hear a story that needs to be heard, make sure you send it to contact@3dadept.com