There are two types of additive manufacturing companies: those that are building their expertise and experience from scratch and those that rely on a much stronger expertise. Companies from the second group often bring a certain cachet that inevitably makes them credible for the challenge they are addressing.
We came to realize that in the field of “Large Format Additive Manufacturing”, Thermwood meets this unique criteria and an exchange with Dennis Palmer, Vice President of Sales, confirms why.
ITS STRONG BACKGROUND
In the additive manufacturing industry, Thermwood is known as one of the three companies providing very large format 3D printing hardware and services with composite chopped Fiber Reinforced Polymer (FPR) pellet materials and a quick throwback to the 1970s shows that it is far from being insignificant.
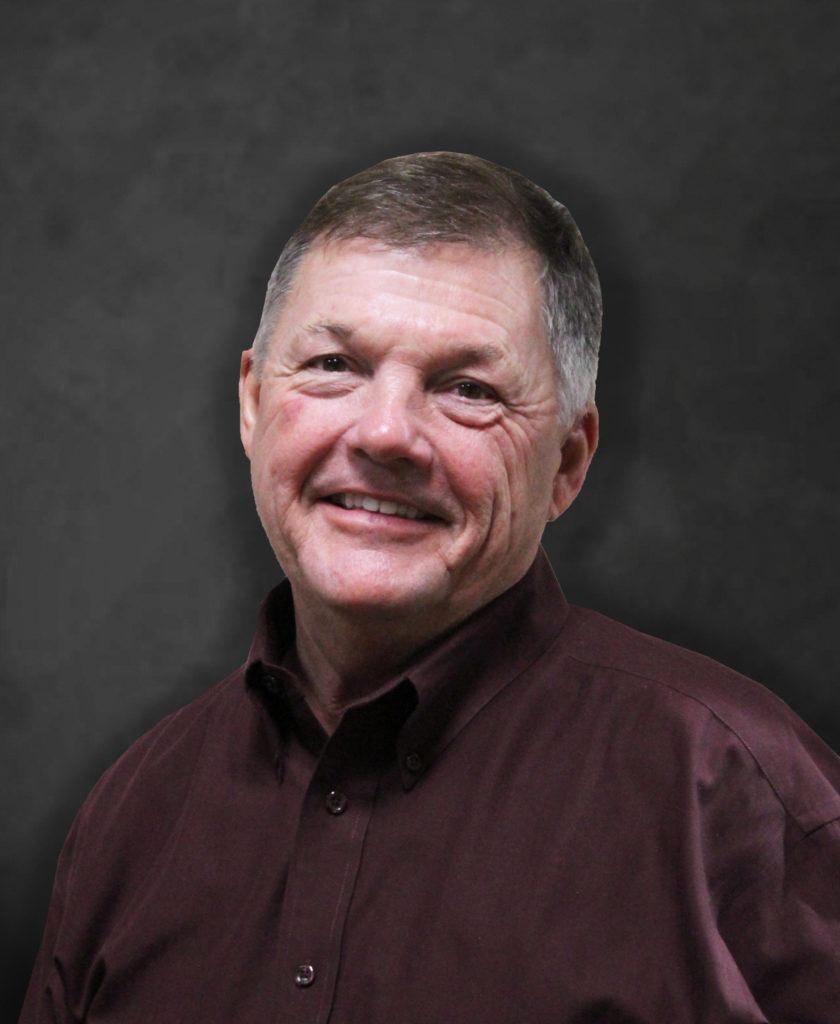
Thermwood’s initial business consisted in extruding plastic parts. “Due to various reasons, the product changed and new markets required three dimensional thermoformed parts to be trimmed. There was nothing on the market to meet our needs for this application, therefore Thermwood designed and built the very first CNC router. We make our own machine control system, and also developed 3rd generation cabinet design software for the woodworking industry”, Palmer outlines.
Over the past 50 years, the US-based machine manufacturer did not only gain knowledge, it has also uniquely positioned itself as a company capable of addressing the requirements of this specific area of manufacturing.
With headquarters in the town of Dale, Indiana, an area known as the ‘Wood Capital of the World’ for the many woodworking companies and furniture companies operating there, one quickly understands the products portfolio delivered to the woodworking industry.
However, the focus on large scale AM of composites in the AM industry makes more sense when one knows that CNC routers (three-axis machines and five-axis machines) are mainly utilized in the aerospace, marine, automotive, plastics and military/defense industries; in other terms, industries that are upgrading their manufacturing portfolio with new technologies.
Not to mention that, at the technological level, Thermwood’s Large Scale Additive Manufacturing | LSAM (pronounced L-Sam for Large Scale Additive Manufacturing) is a hybrid technology that requires the capabilities of 3D Printing and CNC routers to deliver the desired part.
Anyway, today we have discovered a company that supplies machines, parts and service to various branches of the U.S. government as well as to U.S. defense contractors. As per the words of Palmer, 2020 saw a busy team supplying “machines to companies that were manufacturing COVID PPE products, as well as to industries [that provide items in need to those that elected to remain]home and not spend their money on vacations”; industries that provided items such as motor homes, marine products and off-road vehicles. Furthermore, as AM received positive media hype in 2020, this also helped the company maintain “a large backlog of orders for [its] Large Scaled Additive Manufacturing (LSAM) systems.”
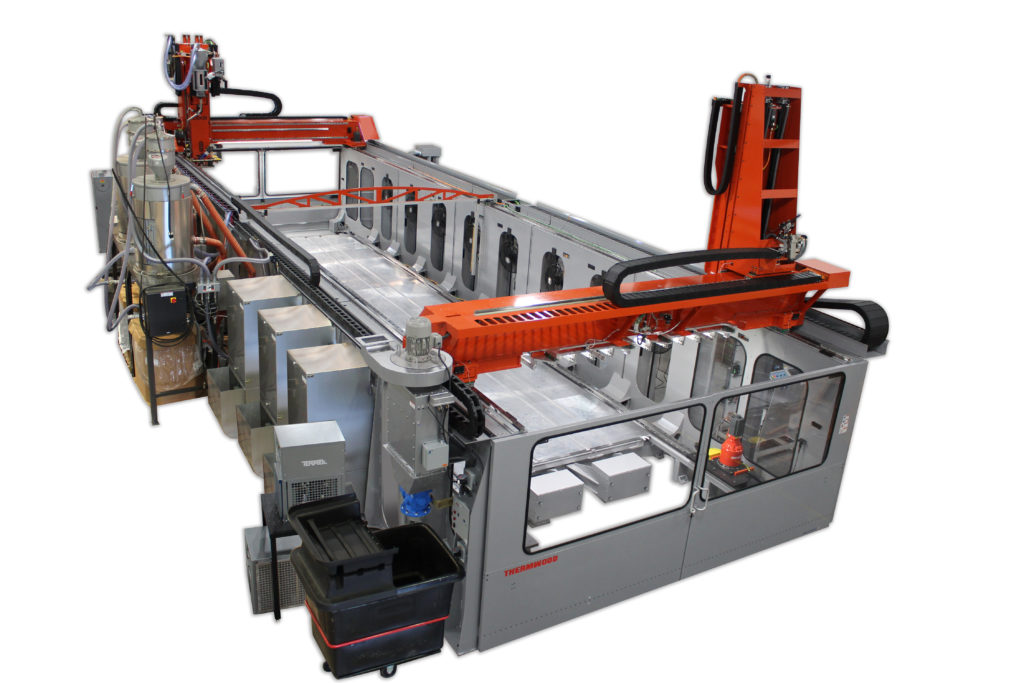
EXISTING & EMERGING APPLICATIONS
Although it was first seen as a process for concept modelling and rapid prototyping, AM in general has rapidly expanded to include applications in many sectors of activity. Despite their potential, it should be noted that all additive manufacturing technologies do not advance at the same pace.
As far as “Large Scale Additive Manufacturing” process is concerned, our expert states that it is still an emerging market.
“The machine has proven its worth in our current target markets, but only time will tell what future market sectors will be able to utilize the near net shape printing capabilities”, the Vice President of Sales confirms. Current markets that already adopt LSAM include aerospace, automotive, marine and foundry. As a matter of fact, multiple machines from Thermwood are currently installed in several facilities across these industries.
Among the numerous applications that have been achieved using Thermwood’s LSAM, the largest part to date the machine has ever 3D printed was a display. The enterprise’s representative explains that it “was designed utilizing 225 printed blocks that were assembled to create a 93’ tall structure with the base being approximately 30’ in diameter.” (That translates into a 28m structure with 9m in diameter).
Moreover, among the numerous applications that have been made public, marine applications have increasingly raised a key interest within the manufacturing field.
Example of marine applications achieved with Thermwood’s LSAM
Whether it is due to the surge of sales during the pandemic or not, companies are increasingly looking to improve the performance of boats. If carbon fiber continues to raise interest, the manufacturing stage sees more and more a focus on recycling and the combination of fiber composites and 3D printing.
The latest example shared by the Indiana-based manufacturer highlights a new approach to 3D printing a yacht hull mold.
With the goal of demonstrating how only a single mold may be needed for the manufacture of larger vessels, Thermwood has 3D printed various sections from a 51-foot (15m) long yacht. For the manufacturing of a 10 foot section from the 51 foot long yacht hull mold (which means a 304 cm section from 1554 cm long yacht hull mold), a mold design was specifically developed with DfAM requirements in mind.
What’s fascinating is that during the design phase, each mold section was associated a molded in rocker.
The section has required the 3D printing of various parts, each about five foot tall (152 cm) before being assembled using high strength polymer cables. The company explained that when the mold is fully assembled, it rests on the floor on these rockers. At this point, the mold can be rolled over to tilt about 45 degrees to either side, kind of like a giant rocking chair. This allows for easier access during the layup process. A set of molded wedges are clamped to the rockers to hold the mold in the desired position. Once the hull has been laid up and fully cured, the mold is rolled to level and the printed wedges are clamped to both sides, holding them level. Then the two mold sides can be un-bolted and slid apart to release the finished boat hull.
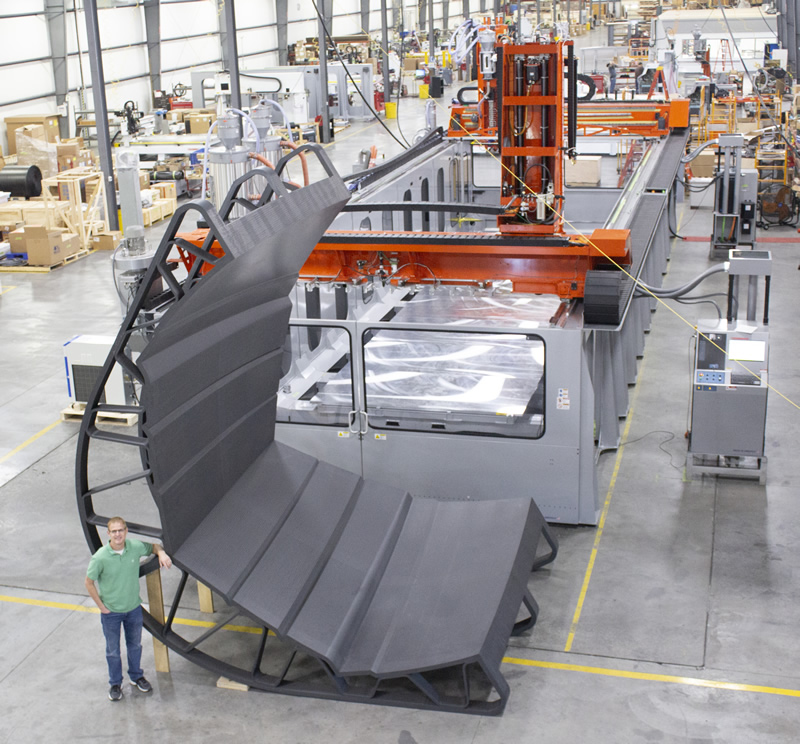
Fabricated and trimmed on the company’s 10×10 foot LSAM MT – the smallest machine from the manufacturer – the team used carbon fiber reinforced ABS as material because it is quite affordable compared to other reinforced thermoplastics.
This successful demo application may show the capabilities of Thermwood’s LSAM but what makes it more interesting is that it truly works in practice – and this, beyond the boatbuilding.
As Palmer points out, “the LSAM can process parts from virtually any thermoplastic composite material used, including high temperature materials that are ideal for molds and tooling that must operate at elevated temperatures. LSAM’s unique printing capabilities produces parts that are fully fused, vacuum tight and virtually void free”.
Existing and long – term challenges to address
It is of ten said that AM of composite materials poses three main challenges: the problem of the homogeneous distribution of reinforcement material in the matrix, the availability of the raw material in a proper form and its imperfections while looking at the chemical variations of the feedstock materials as well as the selection of the ideal process parameters to manufacture these composite materials.
One cannot legi t imately attribute these challenges to all manufacturers who specialise in the field, even less when these manufacturers develop hybrid and large-format AM technologies – bringing therefore the best of both worlds to industrials.
In the case of Thermwood, one of the main issues the company is currently addressing, is the reduction of the operator’s need to monitor temperatures during the print process.
“Currently a thermal imaging camera is utilized, but this still requires the operator to manually change settings during the print process. Even though modifications are rarely needed, an operator needs to be in place when control parameters need to be modified. We anticipate the operator’s participation will be greatly reduced by LSAM control capabilities”, the VP of Sales explains.
Reality shows that the production of large parts typically requires hours and even days of printing and trimming. That is why the Thermwood Mobile App has been developed to make it easier for operators to monitor machine processes, program progress, any error messages or any impromptu events that may occur during the printing process.
AND NOW?
Thermwood’s long outstanding business has demonstrated that the company has “the experience, the ingenuity and the building blocks to address Large Scale Additive Manufacturing.” From the M400 – the largest machine it has ever built to increase LSAM production, to the LSAM MT or even the LSAM 1010 3D printers, the company is ready to meet the increasing production demand of companies with very bold manufacturing goals.
This content has been written in collaboration with Thermwood.
This dossier has first been published in the January-February issue of 3D ADEPT Mag
