It’s been several weeks now that we actively monitor 3D printing initiatives to fight this pandemic. To help companies around the world support medical staff locally, we also spread requests from the healthcare industry.
From AM users to AM technologies providers, several companies continue to leverage 3D Printing technologies to combat COVID-19 across the world.
June 01st
{Denmark} Robots perform Covid-19 tests to patients using a 3D Printed disposable tool
A team of researchers from the University of Southern Denmark has developed an automatic throat swab robot, scheduled to swab the first patients for Covid-19 already by late June.
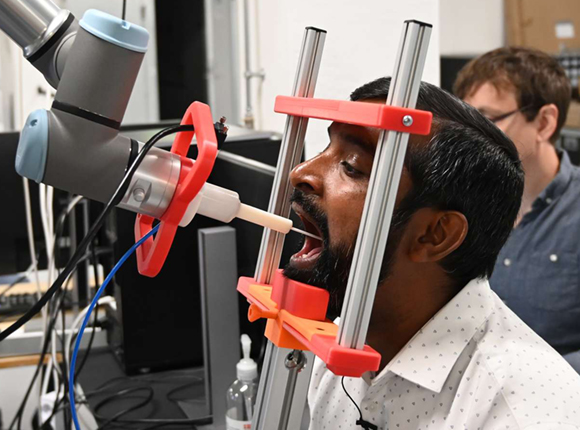
With a 3D printed, specially designed disposable tool, the robot holds a swab and hits the exact spot in the throat from which the sample is to be collected. Subsequently, the robot puts the swab into a glass and screws the lid on to seal the sample. And the researchers have tested the robot.
“I was one of the first to be swabbed by the robot. It went really well. I’m still sitting here”, laughs Professor Thiusius Rajeeth Savarimuthu of SDU Robotics who led the team of researchers who have been working on this project. “I was surprised at how softly the robot managed to land the swab at the spot in the throat where it was supposed to hit, so it was a huge success.”
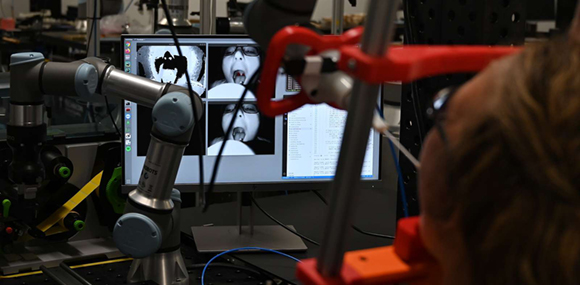
World Health Organization strongly advises to test people but at the same time, health professionals are at risk of becoming infected when doing throat swabs on potential corona patients.
As experts expect a second wave of Covid-19 patients, the research team already created a company to enable an easy commercial use of the robot.
Named Lifeline Robotics A/S, the company’s vision is to get the robot out to do good on the global market as quickly as possible: in airports, in refugee camps or where else it might be needed.
“There are prospects in developing a throat swab robot so that robots can take over the throat swabbing work both in relation to Covid-19, but also in all future viruses”, says Thiusius Rajeeth Savarimuthu.
May 26th
{USA} GE Additive Engineer designs a face mask frame and makes the 3D printable files available via the open source community
Mark Fuller’s job at GE Additive is to design parts for aircraft, rockets and even race cars that can be metal 3D Printed. The Covid-19 pandemic brought unexpected priorities, especially in terms of protective solutions.
Fuller realized that with the shortage of protective solutions, thins quickly become expensive. A simple mask he used to buy for 50 cents was going for $30. He therefore decided to design a face mask frame that could print out of low-cost plastic.
“Fuller wanted to design a face mask that would be easy, low-cost and fast to make and flexible enough for anyone to use, regardless of the materials they had on hand. He surveyed the mask designs the 3D-printing community was churning out and noticed flaws: One popular 3D model took 10 hours to print, another couldn’t be printed successfully and a third that got a lot of attention required a scuba mask and specific HEPA filters”, explains GE Additive who told the story.
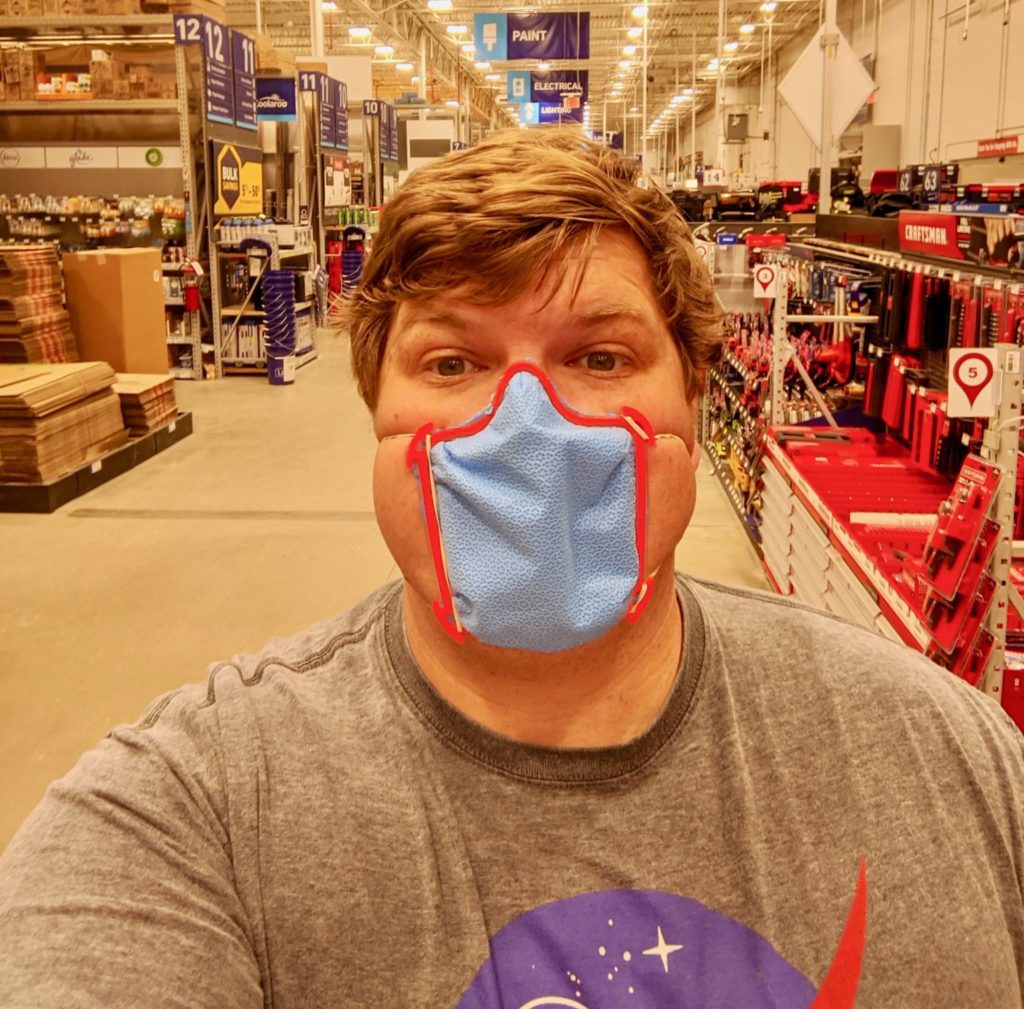
The model must be simplified. Fuller therefore stripped away everything from the face mask people usually 3D printed and just left a thin ring of moldable plastic with small cleats for string or rubber bands to hold the frame to the wearer’s face.
Fuller’s goal was to achieve something that could be produced with any technology, be it conventional or additive manufacturing technology.
Following the feedback, he received from a Facebook group focused on open-source medical equipment to fight COVID-19, the GE Additive engineer improved his model and started the production of face masks that the GE Additive COVID-19 Task Force sent to local hospitals.
Over time, the design made open-source went global and was quickly adopted by several organizations.
“The GE face mask design gives us a way to immediately provide protective gear to our sailors and Marines anywhere there is 3D printer available — including aboard our ships and submarines, as well as with our expeditionary forces. It was fantastic to have a design that afforded us the opportunity to rapidly respond to this urgent fleet need,” says Liz McMichael, additive manufacturing integrated program team lead for the U.S. Navy.
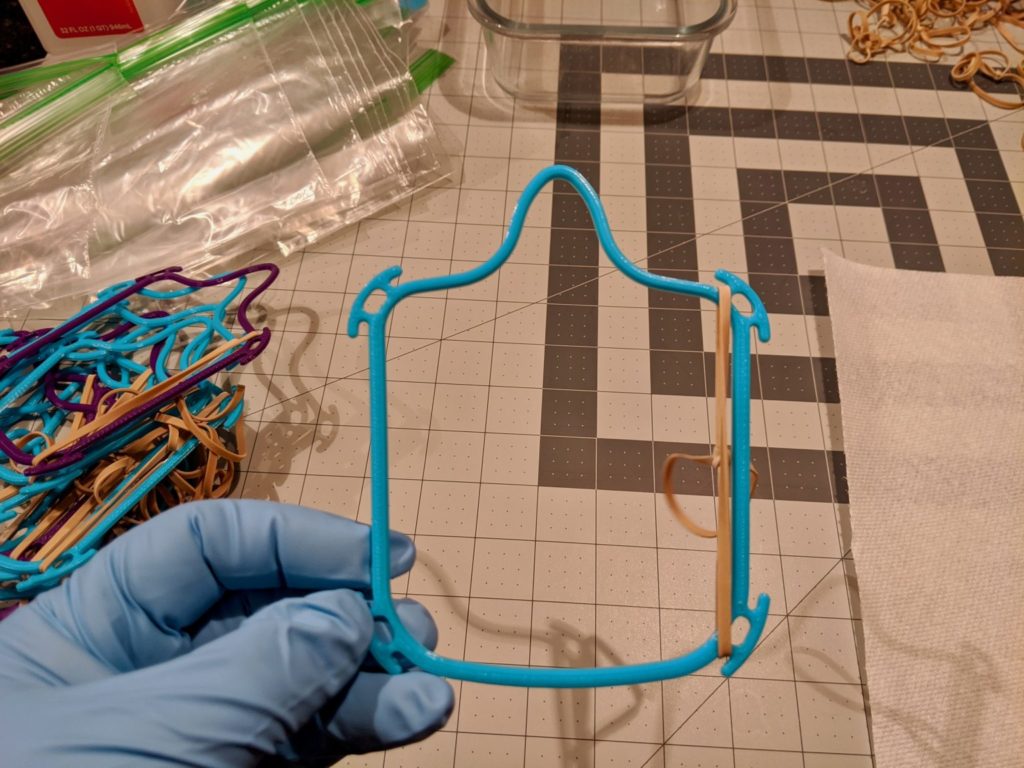
“Throughout the COVID-19 crisis and our collaboration with the Food and Drug Administration, NIH and Veteran Affairs, our goal has been to help provide a centralized location for safe and effective 3D-printed PPE,” says John Wilczynski, executive director of America Makes. “This design was really a proof point of that approach. There was an immediate need, a capability, and an avenue for the resulting design to be reviewed for appropriate use and shared.”
Fuller attributes the success of his design to the engineering methods he works with each day at GE. “I took the same principles we train with at GE Additive and applied it to the face mask,” he says. “A big part was the voice of the customer, the customer being everybody. Working with the GE Additive COVID-19 Task Force, I had the largest pool of customers available.”
May 25th
{USA} Rapid Application Group leads collaboration to enable thousands of FDA approved devices produced using additive manufacturing
Rapid Application Group (RAG), FlightSafety International and Newton Design, responded in mid-March 2020 to deliver thousands of critical Personal Protection Equipment (PPE) devices to local first responders and healthcare teams in Oklahoma.
Pivoting rapidly from their usual aerospace production work, the three companies teamed together to start production of face shields and masks using additive manufacturing. Working with healthcare providers and the FDA, the team at RAG were able to create approved designs within 3 weeks and the three started production of face shields and masks immediately using additive manufacturing with Class VI materials. With hundreds of parts produced per day, the three companies have produced and delivered more than 5,000 parts, with thousands of orders yet to fulfill.
“Terry, Jason and the team at RAG truly exemplify the Oklahoma Standard” said Oklahoma Secretary of Commerce, Sean Kouplen. “Their desire and ability to quickly adapt their business model so they could help our health care workers and citizens of Oklahoma is remarkable. When you put your company and livelihood on the line to help save lives, you are a real hero in my book.”
FlightSafety International is a manufacturer of critical flight simulation systems. The company provides additional additive manufacturing platforms from its plant to help the effort.
Newton Design, a supplier of flight simulation and training systems, also volunteered when they heard what the RAG team were doing. The company also donated their SLS additive systems and started the production of the PPE devices.
As the team ramped up, it was also assisted by companies such as EOS, an additive manufacturing vendor, which donated critical materials for the teams to use.
“We really couldn’t have got to the production phase so quickly without the help of these incredible companies,” said Terry Hill, CEO, Rapid Application Group. “We are all doing 24/7 production to fill the need and protect our healthcare and first responder teams and will continue until the work is done.”
May 17th
{France} Anatoscope develops AnatoMask, a solution for customizable Protective Masks
France-based medical technology company AnatoScope, has developed a protection mask solution that can be tailor-made for any wearer. Named AnatoMask, the eco-friendly solution would ensure both security and comfort for all-day wear, and has been produced with 3D Printing technology.
AnatoScope, the company behind this solution specializes in software solutions that automatically transform imaging to complete 3D digital twins of the patients. Its key fields of operation are usually detal, orthopedics and radiology. However, as a medical technology company, the startup was uniquely positioned to offer the market with a solution that currently meets the most urgent needs.
AnatoMask is said to be “a quick home ready solution”
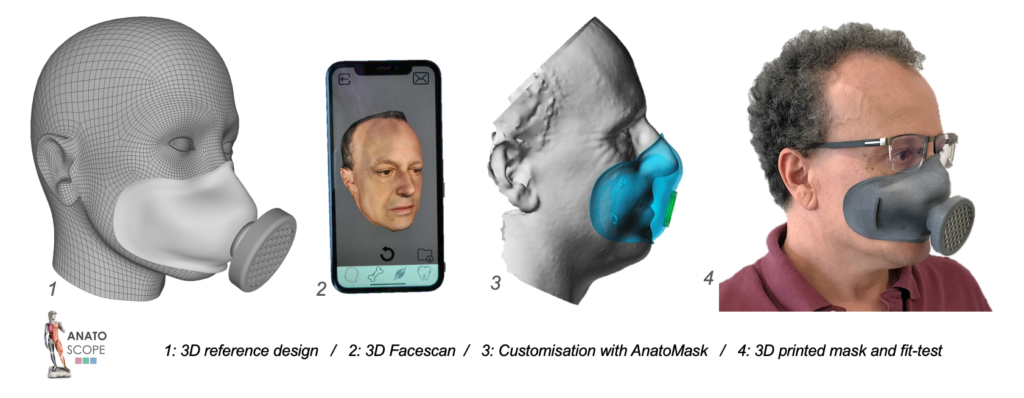
Designed for both healthcare professionals and the mass public, users who would like to have the mask should 3D scan their face and send the file via a smartphone application. The resulting 3D files are then sent to the AnatoScope team, who will analyse your face shape, and then create the custom 3D files for your mask. The 3D printed mask can be easily cleaned and reused, thus limiting the use of disposable masks.
Frédérick Van Meer, COO of AnatoScope states: “This solution is based on our patented technologies that we have already developed for the dental and orthopaedic industry. We initially thought about the medical profession, in particular dentists, as we already have expertise in this field, and they also have a high demand for protective masks for the reopening of their dental surgeries. But we have also thought about the non-medical sectors, and those who must regularly wear masks and persons at risk.”
Anatoscope is also encouraging makers and designers to send their designs to be personalised on their online platform. The company currently works with different partners for the design, 3D printing and for the production of filters. Their next goal is to launch their own 3D face scan application “AnatoFace” for summer 2020, in order to directly receive and respond to customer requests, and facilitate access to this new technology.
{UK} Consultancy firm works with the National 3D Printing Society to improve the existing design of PPE
With the goal of extending the wearability of surgical masks, G2 works with the National 3D Printing society to improve the existing design of PPE.
G2 Innovation is a UK-based consultancy firm that specializes in R&D Tax credits, Industrial product design and Concept development.
“The previous design snagged on hair and was difficult to put on and take off many times throughout the day without touching the mask – a big no for contamination. The previous grip was quite large, so when users wore it on the tighter hooks it stuck out from either side of the head which they found irritating. In the improved design, it was also imperative to fit as many grips on a 3D printer bed as possible, reduce the amount of material used, and speed up printing time so as many as possible could be manufactured for distribution around the country”, explains the company about the previous masks and the alternative.
Even though they do not reveal which AM technology is used to produce the mask, we do know that the improved grip uses 57% less material, and is produced in one third of the time and at least twice as many can fit on the printer bed at one time. Furthermore, a distribution network of over 2200 3D printers has been leveraged to provide the medical staff across the UK with the new materials.
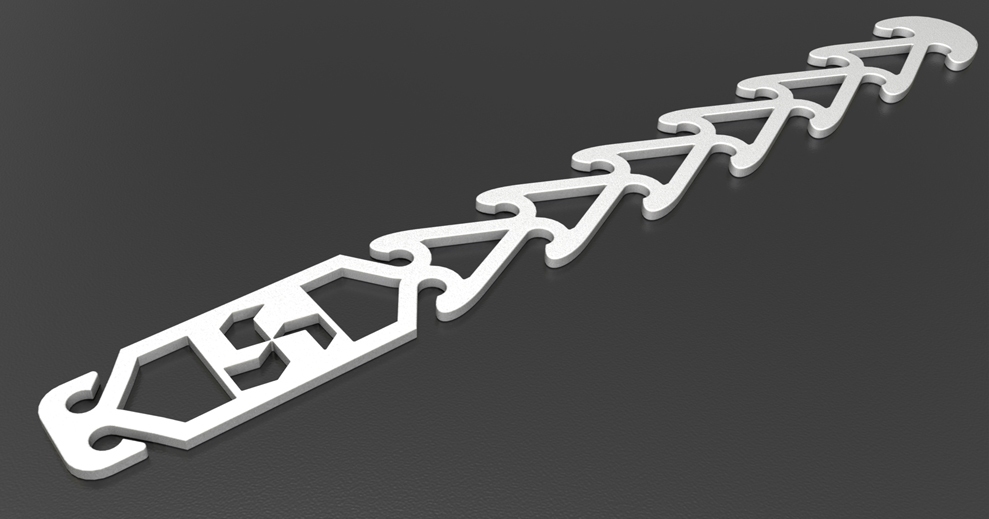
Last but not least, as far as comfort is concerned, the UK-based company said that the new grip sits on the back of the head and holds the mask elastic away from the ears, preventing it from cutting into the backs of the ears and making the masks more comfortable to wear.
The 3D Print STL File has been made available for download on Cults3D.
May 12th
{UK} 3DPRINTUK & Arts University Bournemouth to manufacture face shields for front-line provision of PPE – the face shield design is free and open source
Most of the designs released today can be produced on FDM machines. With the goal of producing a design which is perfectly compatible with SLS 3D Printing, 3DPRINTUK, a UK-based 3D Printing service bureau, has designed its face shield.
Although it was practical, the most widely used face shield design (the one from Prusa) only enabled the printing of 14 individual head bands on the EOS FORMIGA P110 SLS machine at a time. The focus of 3DPRINTUK was therefore to create a design that the P110 could accommodate in much larger numbers. By nesting the main peak component inside one another they were able to create one that allowed for 260 to be printed in a single print with a 27-hour build time.
Nick Allen, MD at 3DPRINTUK explains: “That is 6 minutes per shield, which is a game changer. The design that we created clips together in 10 seconds, uses silicone straps for adjustment, can take an acetate sheet with 3 holes, is lightweight at only 42 g, and is sterilisable with IPA, autoclave, or ethylene oxide (Et0). All in all, we believe that this is the most efficient visor design to produce via 3D printing available today.”
Additional design benefits include a closed peak design for extra protection, the material used (PA2200/Nylon 12) is biologically safe, and the shape has been designed so that it can be flat packed into an A4 envelope for cheap postage and storage.
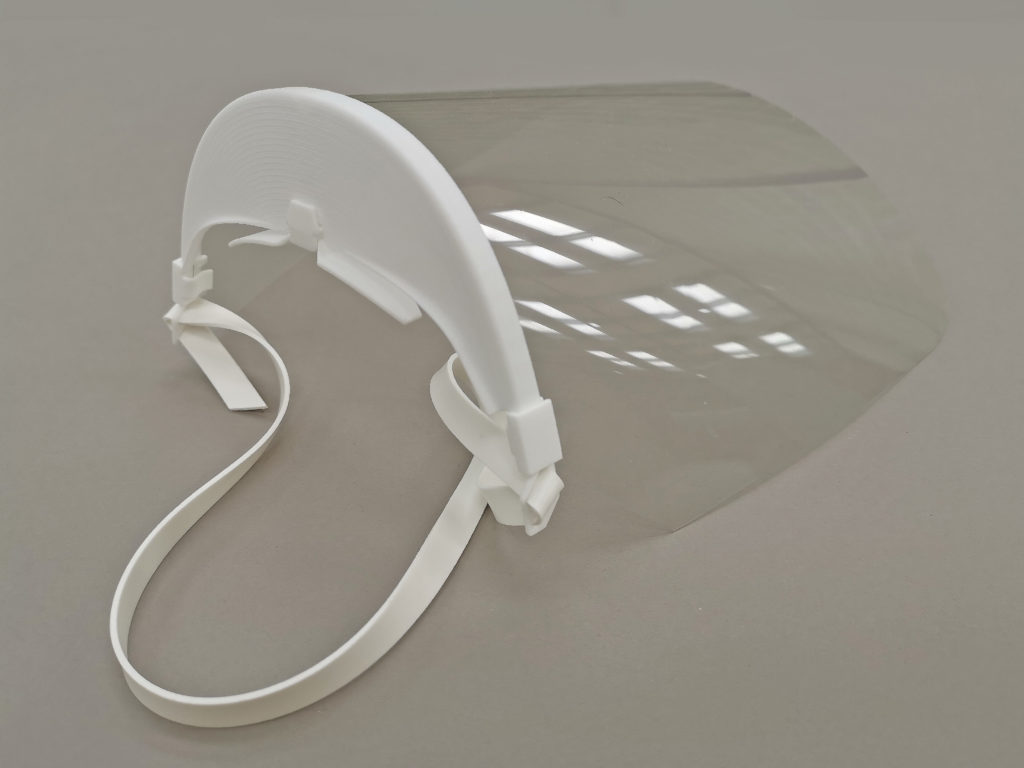
Information relating to the design was released, and the first facility to take on the manufacturing role was the Arts University Bournemouth (AUB) which had access to the P110 machine and also had laser cutting capabilities.
From the get-go, there was a great connection between the 3DPRINTUK and AUB teams, with AUB producing the initial batch of 5000 units and more thereafter. These shields will be distributed for free to front line key workers.
The arts university has been spearheading an effort by educational institutions to manufacture and create vital protective equipment for the healthcare sector. Since its campus closure in March, the university’s facilities have become a production line for visors, facemasks, scrubs and gowns, which are being distributed across a range of public healthcare settings, including doctors’ surgeries, care homes, and volunteers providing door-to-door services for the elderly.
May 08th
{The Netherlands} Hospitals Amsterdam Staff receive 100 3D Printed shoes from the QUANT-U project
The QUANT-U team has come a long way since their launch in 2018. The HQ based in Amsterdam joined the ongoing efforts made by companies across the world to support the frontline medical staff. As the project focuses on the production of customized 3D Printed shoes, it was natural for the team to support with something they have expertise in.
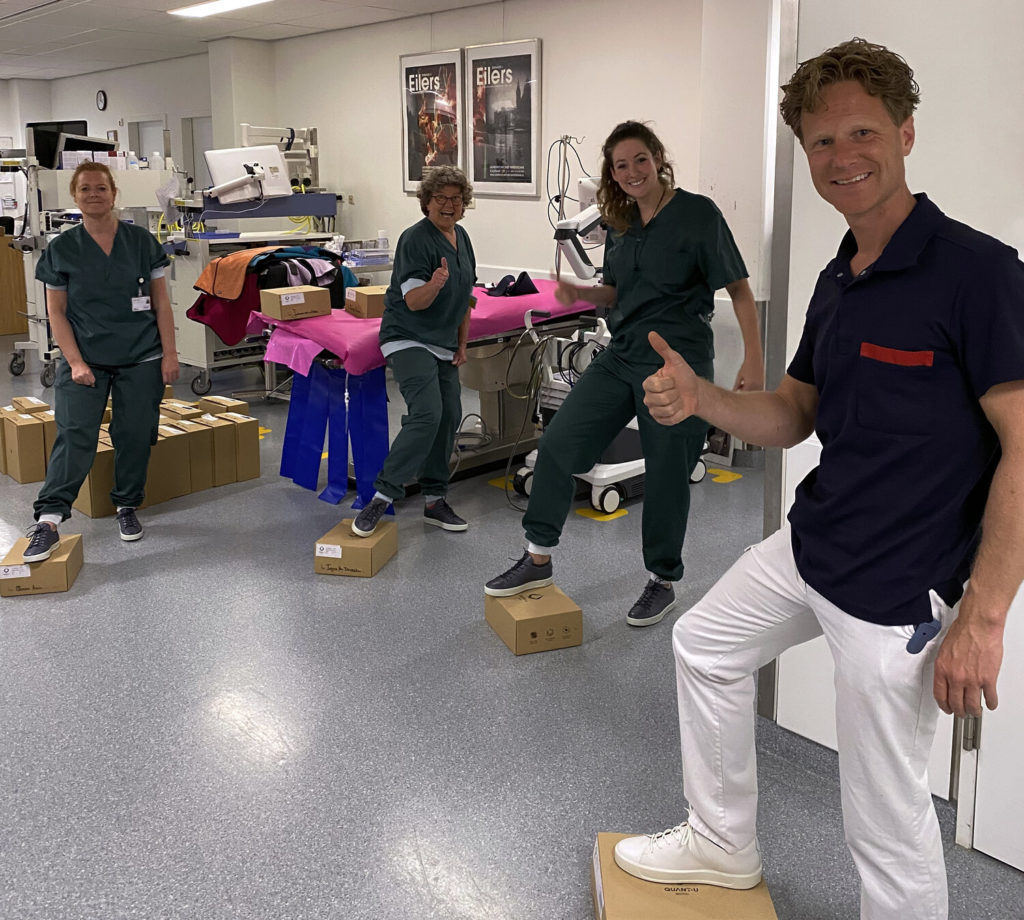
“Continuing with our pilot project Quant-U with OLVG hospitals in Amsterdam focused on Digital Healthcare via Connected Footwear for fatigue reduction, we have donated 100 pairs of Quant-U customised shoes which we hope will contribute to the well-being of our valued heroes during these challenging times. One step at a time, we will get through this. Engage directly with us on how to create more opportunities in your healthcare or workforce domain”, said QUANT-U on its website.
{Australia} SPEE3D develops and successfully tests ‘ACTIVAT3D copper’, a solution to 3D print anti-microbial copper onto existing metal surfaces.
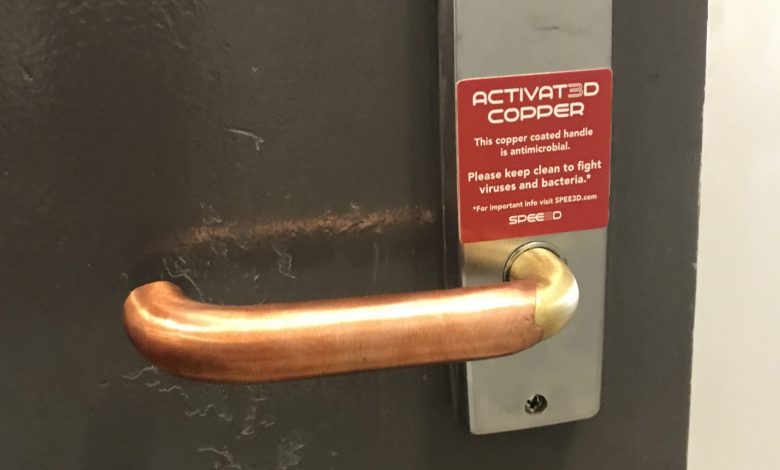
In order to fight the spread of COVID-19, Darwin company installed antimicrobial ACTIVAT3D copper throughout their building. Tests carried out prior to the installation in the Northern Territory Department of Trade, Business and Innovation, confirmed that ACTIVAT3D copper ‘contact kills’ 96% of SARS-CoV-2 (the virus that causes COVID-19, in just two hours).
According to an Australian accredited laboratory, 99.2% of the virus is killed in 5 hours. Stainless steel showed no reduction in the same time frame.
The SPEE3D team then developed a process to coat stainless-steel door touch plates and handles in under 5 minutes. In a wonderful example of the Northern Territory embracing local innovation, the first order for ACTIVAT3D copper came from The Norther Territory Government. SPEE3D was contracted to replace existing door handles within The Northern Territory Department of Trade, Business and Innovation with ACTIVAT3D copper products. With these handles now installed, staff of this Department, and the community they interact with, are already experiencing the benefits of antimicrobial copper.
Department of Trade, Business and Innovation CEO, Shaun Drabsch said “The Department of Trade, Business and Innovation is thrilled to be the first to have this innovative technology installed in our workplace, ensuring an even safer place for our staff and community to do business here. We thank our landlord for agreeing to the installation of copper handles. It is great to see a local Territory company taking advantage of this very challenging time and drive a new innovative product that can further protect Territorians from COVID-19.”
The solution comes right in time as containment measures begin to alleviate around the world and companies are exploring various solutions to combat this pandemic.
{USA} Software company donates $10,000 to the production of 3D Printed PPE to Fight COVID-19
Laplink® Software, Inc., a company that provides consumer, SMB and enterprise PC migration software, has donated $10,000 to Maker Mask for the production of 3D Printed PPE. The software publisher will also focus its upcoming 37th anniversary sales promotions around additional support for the nonprofit.
Maker Mask is a Seattle-based nonprofit, ecosystem and digital platform response to the COVID-19 crisis launched by leaders of technology, industry and government. Launched in March 2020, the organization’s goal is to help fill the critical need for high-quality personal protective equipment (PPE) due to the COVID-19 pandemic. Several organizations are working together, as part of this initiative, to boost the production of respirator-style masks for the public and essential workers.
The organization designed an open source 3D printable protective mask, approved by the National Institutes for Health (NIH), which is available for free download at makermask.com. Within a month, makers from around the world downloaded more than 125,000 free open-source computer aided design (CAD) files for printing the Maker Mask. The Maker Mask network currently supports a global community of nearly 10,000 members, each operating small batch production sites making masks for their local communities. The masks can be manufactured using commonly available materials and hobbyist-grade 3D printers for a cost of about $2.00 to $3.00 per unit for materials.
Laplink’s donation
The donation will back some of the costs of mask-making materials and other operational expenses as the nonprofit organization continues to support the Maker Mask network.
Laplink’s 37th anniversary occurs in May, and while the company was planning its annual celebration, Thomas Koll, Laplink’s CEO, suggested a different sort of celebration: to help a worthy cause.
May 05th
{UK} – AI Build said its open source PPE design could be printed in 60 seconds
In order to contribute to the fight against the Coronavirus pandemic, Ai Build has open sourced a PPE design which could be printed in 60 seconds.
The London-based large-scale additive manufacturing systems manufacturer has optimized the 3D file with its AiSync software so that it could be printed quickly with any 3D printer.
The company explains that unlike conventional 3D printing with flat horizontal layers, AiSync software is using freeform multi-axis paths to generate machine instructions. With this technique Ai Build produced a curved design of a single strand with variable thickness following the shape of the human head. The resultant geometry is not only faster to produce but also stronger and more comfortable to wear, sitting tightly between the ears and the forehead without the need of a rubber band.
A stack of 1200 pieces can be mass manufactured per day per machine without human supervision which is around 100 times faster than a typical design produced by desktop 3D printing software.
The open sourced face shield design can be downloaded here.
{Spain} – More than 4,000 reusable face shields from BCN3D have reached over 50 hospitals and health centers across all Spain.
Since it announced the availability of its 3D Printing farm, BCN3D has been working with healthcare providers, government organizations, and its network of professionals- on designing, prototyping and producing different vital parts for healthcare professionals.
More than a simple production of equipment, the big challenge for the Spain-based manufacturer was the same other manufacturers around the world faced: achieve a functional validation.
Indeed, for these parts to be used by the healthcare workers, they needed to be comfortable and safe to use. As per the words of BCN3D Farm Technician Ignacio López, “one of the most difficult tasks was to fabricate the parts to be ergonomic and comfortable for the staff while, of course, keeping them protected”. Based on these requirements (comfortability, adaptability, and safety), they leveraged the material PET-G “because of its high chemical resistance” and to achieve a reusable solution. This way, each face shield they produced, could be reused once thoroughly disinfected.
Thanks to the whole community in the Castelldefels area which dedicated time and resources to find and donate all the material they could get, and a network of 400 volunteers across the world, in just a month more than 4,000 units have been distributed to over 50 hospitals and health centers, plus dozens of nursing homes and pharmacies all over Spain.
May 1st
{Canada and the United States} – Core3dcentres® Launches Open Health® to Address the Shortage of PPE
Core3dcentres® launches a new division – Open Health® (Open Health®) whose additive (3D Printing) dental manufacturing technologies and techniques have been retooled to produce Personal Protective Equipment (PPE) and COVID-19 testing swabs for healthcare professionals.
Open Health® is utilizing Computer-Aided Design (CAD) software and skilled technicians to design, build, and ship a variety of PPE products, including custom-printed face masks, custom-printed mask adaptor frameworks, and a number of other PPE solutions. Open Health® also manufactures innovative 3D-printed nasopharyngeal lattice swabs for use in COVID-19 testing kits. The materials used in their customized solutions are FDA and Health Canada approved.
“We pride ourselves on our entrepreneurial spirit and commitment to innovation, so we were fast to respond with the creation of Open Health® when we saw both the scarcity and escalating need for medical-grade PPE” said Mark Maier, President and CEO of The Aurum Group. “In the first week of offering these products, demand has exploded; We’ve been conducting ongoing optimization of our designs to continually improve these products and provide them to the healthcare industry.”
April 28th
{The United States} –ExOne and Pitt to develop reusable 3D printed porous metal filters for respirators
The ExOne Company and the University of Pittsburgh have developed reusable metal filters that fit into a specially designed respirator cartridge for sustainable, long-term protection against contaminants, such as COVID-19.
The two teams have leveraged ExOne’s binder jetting technology, acknowledged for its ability to produce metal parts with specific porosity levels that can effectively filter out contaminants while allowing airflow.
Those 3D printed respirator filters have been produced in two metals — copper and 316L stainless steel. While copper and stainless-steel filters are currently being tested, copper has been known to have antibacterial properties since ancient times. The first recorded use of copper to kill germs was in the Edwin Smith Papyrus, the oldest known medical document in history, according to the Smithsonian. Many studies have proven copper’s disinfectant powers. One landmark 2015 study, funded by the Department of Defense, revealed that copper alloys contributed to a 58% reduction in infections. COVID-19 research also suggests the virus dies faster on copper than on other surfaces.
Initial testing for airflow and filtration efficiency is currently underway, and the filters are being optimized with the goal of adhering to an N95 respirator standard. To test filters in different metals and porosities, Dr. Chmielus, Associate Professor of Mechanical Engineering and Materials Science at the Swanson School, is using CT scanners to analyze the microstructure and porosity of the filters within his research group.
Engineering simulation company Ansys is providing additional computer simulation support to analyze and optimize the performance of the filters.
April 24th
[France] Athletics 3D leverages Zortrax 3D printers to COVID-19 relief efforts
Sports company Athletics 3D usually leverages 3D printing to produce tailor-made equipment for professional athletes. A blatant example that shed light on one of their achievements was the 3D printed equipment from disabled triathlete Florian Jouanny.
The company explained they “have built a map with marked 3D printing providers and hospitals or other organizations in need. This way, a hospital can quickly find the closest person with available 3D printers.”
“We are using 9 Zortrax 3D printers and with them alone we could produce roughly 45 medical helmets per day. But when we partnered with ST, which had laser plotters to cut visors for those helmets out of plexiglass we could go for much simpler design and reach a daily output of over 100 helmets”, says Clement Jacquelin, founder and CEO of the company.
Athletics 3D has already partnered with other French companies like Cap Gemini or MGEN, or ST Microelectronique, to make their manufacturing operation even faster.
[Poland] Sygnis New Technologies additively manufactured over 80 specialized laboratory stands to facilitate COVID-19 testing
Sygnis New Technologies is a Warsaw-based firm that specializes in consulting for additive manufacturing.
Following a request from Warsaw Genomics laboratories, the company designed and manufactured 80 laboratory stands which aim to facilitate Covid-19 testing operations. The Warsaw Genomics laboratories currently perform 2000 tests per day.
The 96-slot stand aims to facilitate and secure (stabilize) the test-tubes while working with samples. The stands are foldable and very easy to print/modify.
The 3D models have been made available as an open-source project. Further information regarding the manufacturing process can be found on Sygnis’ website.
[Italy] – Ferrari harnesses 3D printing to produce respirator valves and fittings
As part of a collaborative effort with Siare Engineering, Italy’s only producer of pulmonary ventilators, Ferrari is leveraging additive manufacturing to produce respirator valves and fittings for protective masks, developed by diving equipment manufacturer Mares.
This technology is usually leveraged for the production of prototypes inside its Maranello plant.
The car manufacturer plans to manufacture hundreds of the parts in the next few days. It is also working with the Italian Civil Protection to deliver the components to a number of Italian hospitals and health specialists.
[India] – Imaginarium provides 3D printed face shields and aerosol box for intubation
India-based Rapid Prototyping and Rapid Manufacturing Center integrates a wide range of industrial 3D printers that can manufacture devices and components using biocompatible Nylon PA12 through SLS (Selective Laser Sintering) and MJF (Multi Jet Fusion).
As far as aerosol box is concerned, it should be noted that it is designed to enable physicians to intubate a patient while better shielding themselves from any aerosol particles that could be released from the patient’s airway during the procedure.
Technically speaking, “a simple transparent plastic box with an opening on one side allowing it to fit over the patient’s chest and neck, while the opposite side has two small holes through which doctors can insert their hands”, explained the company.
Following the release of a recent 3D file shared by Prusa, the service provider now produces 3D Printed circuit splitter and flow restriction devices for multiple patient lung ventilation.
[US] 3D Systems mass produces 3D printed ventilator splitters
On March 26th, 3D Systems announced it offers its services and invites customers and partners to join them in sharing resources to help overcome this pandemic.
Over time, the global provider of 3D Printing solutions has been able to produce ventilator parts on demand, nasopharyngeal swabs, face masks, face shield frames, as well as ventilator splitters.
The latest application shared by the company is the ventilator splitter concept. This device enables a single ventilator to support two or more patients during this crisis. Statistics show that approximately 2.4% of all COVID-19 patients in this pandemic will require mechanical ventilation.
By using T-tubes and adapters, a circuit could be divided so four patients can share a single ventilator in an emergency. One group, Ventsplitter.org has released an open-source file for emergency POC uses along with flow limiters when pairing different patients (body weight, lung compliance, etc). AM remains an ideal candidate to produce these parts for hospitals. 3D Systems for instance leverages its Figure 4 system for the production of these parts and can benefit from the support of its ISO 13485 certified facilities in case hospitals formulate a request.
A wide range of applications are currently in progress and continuously updated on the Covid-19 page of the manufacturer.
[US – Spain] HP is involved in several initiatives
One of the first contributions of HP was to help in the production of ventilators for Spain-based hospitals. Over time the manufacturer of MJF technology has launched several initiatives to help not only the medical staff globally but also to support students and schools impacted by the virus.
Put simply, HP Inc. and its global digital manufacturing community are mobilizing their 3D printing teams, technology, experience, and production capacity to help deliver critical parts required to heal Covid-19 patients.
More than 1000 3D printed parts have already been delivered to local hospitals. HP’s 3D R&D centers in Barcelona, Spain; Corvallis, Oregon; San Diego, California; and Vancouver, Washington are collaborating with partners around the world in a coordinated effort to increase production to meet the most urgent needs. Initial applications being validated and finalized for industrial production include face masks, face shields, mask adjusters, nasal swabs, hands-free door openers, and respirator parts. HP is also coordinating with government, health, and industry agencies in numerous countries to ensure a synchronized and effective approach.
HP Inc. today announced HP Turn to Learn, a new program that will deliver educational content curated from leading scientific, publishing and media companies to support teachers and students in the face of the COVID-19 pandemic.
[US] The Barnes Group Advisors advices the Veterans Health Administration on the potential of AM in this pandemic
The Barnes Group Advisors (TBGA) and TRONIX3D have teamed up as small businesses to provide a unique perspective on how Additive Manufacturing (AM) can support COVID-19 efforts. TBGA is supporting the Veterans Health Administration, and TRONIX3D has been busy making Personal Protective Equipment (PPE) for our healthcare workers. While the type of PPE each team is creating is different, the approach to making a product that meets the right requirements is very similar.
Tronix3D is a Pittsburgh’s based additive contract manufacturer and innovation center.
As one part of an active collaboration, Principal ADDvisor® Chris Aldridge worked with a VA and National Institute of Health (NIH) approved face mask design and made some simple tweaks to shave about 10 minutes off the print time. 10 minutes might sound like a small number, until you need 100,000. That 10 minutes can turn into 10,000 hours of saved print time.
The team TRONIX3D is partnering with a Western PA Wabtec facility to produce and assemble face shield PPE. TRONIX3D provides the printed components, and Wabtec will assemble the face shield in this arrangement.
The design they started with was functional, but it was designed using limited DfAM. Consequently, it was taking too long to produce. TRONIX3D employed their DfAM skills for the Multi Jet Fusion (MJF) system they operate, and they were able to reduce both print time and material consumption. Additionally, using the same DfAM approach, they reduced post processing time by incorporating features that would make the shields easier to handle during bead blasting; this means they can be easily removed when finished, reducing time, labor and, consequently, saving money. The final product design yielded a 75% cost reduction with a 450% increase in production efficiency.
Remember, you can post free of charge job opportunities in the AM Industry on 3D ADEPT Media or look for a job via our job board. Make sure to follow us on our social networks and subscribe to our weekly newsletter : Facebook, Twitter, LinkedIn & Instagram ! If you want to be featured in the next issue of our digital magazine or if you hear a story that needs to be heard, make sure to send it to contact@3dadept.com