Vous vous souvenez que nous vous avons dit que le post-traitement est un terme générique qui couvre une variété d'étapes que les pièces imprimées en 3D doivent subir avant d'être utilisées à des fins finales ? Dans le but de fournir une compréhension approfondie de chaque tâche de post-traitement, nous avons commencé à partager des informations clés sur les problèmes soulevés par l'élimination de la poudre métallique, l'utilisation de fours dans la fabrication additive, ou même le processus de teinture automatisé pour les pièces imprimées en 3D. Dans cet article, nous allons examiner les meilleures pratiques et les conseils à connaître lors de la mise en œuvre d'une méthode de traitement de surface en impression 3D métallique.
La théorie veut qu'en FA, les ingénieurs puissent bénéficier d'une liberté de conception pour créer des formes complexes, mais la pratique révèle des contraintes de conception qui montrent que la géométrie que vous imprimez ne sera pas la même que celle de votre modèle 3D.
Plusieurs causes peuvent expliquer cela :
- Lors de l'exportation de votre fichier d'impression par exemple, les bords, contours, surfaces courbes et autres du modèle 3D sont approximés par des triangles dans un processus appelé tessellation. Lorsque cela se produit, les formes des cercles ne sont plus parfaites. Elles deviennent des approximations formées par une série de lignes droites ;
- Malgré l'optimisation de la direction de construction, le mode de fabrication couche par couche de la FA peut toujours être délicat pour les surfaces inclinées, les formes courbes ou les trous, et donner un effet d'"escalier" ;
- D'autres difficultés de fabrication et de conception peuvent être liées à la géométrie du modèle 3D, à la qualité de la poudre métallique ou à l'orientation de la construction. Ils peuvent affecter les dimensions et les tolérances de votre pièce finale imprimée en 3D.
Ces problèmes peuvent être certaines des raisons pour lesquelles les opérateurs décident de mener un processus de traitement de surface ; afin qu'au final, ils puissent améliorer l'apparence de leur pièce, renforcer leur durabilité ou la capacité de la pièce à mieux résister à l'usure, à la corrosion, à la chaleur ou à d'autres éléments, lisser les surfaces inégales ou améliorer sa conductivité électrique.
Ce dossier propose un examen approfondi des méthodes de traitement de surface que les opérateurs peuvent appliquer aux pièces métalliques imprimées en 3D. Pour discuter de ce sujet, nous avons invité des contributeurs clés de deux entreprises : Jan Panhuis, conseiller technico-commercial senior chez Leering Hengelo (Normfinish) ainsi que Paul Gagorik, architecte de solutions et Behrang Poorganji, VP Material Technology de Morf3D.
Au cas où vous ne connaîtriez pas ces entreprises, sachez que Normfinish (connue sous le nom de Leering Hengelo dans la région du Benelux), opère dans le monde du sablage et de la technologie de surface depuis 1980. La société fournit une large gamme de produits et de services pour les opérations liées au sablage fin, au polissage, au matage, à la finition, à l'ébavurage, à l'ébauche de surface, au nettoyage de surfaces telles que la rouille (oxydes) et le revêtement, ainsi qu'au grenaillage.
Morf3D, quant à elle, apporte une expérience d’utilisateur autour de cette "table". L'entreprise s'appuie sur une expérience inégalée pour fournir une production en série par FA aux entreprises aérospatiales. En tant que producteur de pièces, Morf3D exploite ses capacités internes de post-traitement pour obtenir des structures fonctionnelles et des processus de fabrication entièrement optimisés pour des clients de premier plan du secteur aérospatial. Une fois qu'une pièce est retirée de la chambre de fabrication, l'équipe de Morf3D peut effectuer un large éventail d'étapes de post-traitement. Celles-ci comprennent, par exemple, le dépoudrage, l'inspection non destructive (rayons X, tomodensitométrie), le traitement thermique (détente, HIP, solution, vieillissement, trempe), le retrait du substrat (plaque de construction), le retrait du support, l'usinage CNC, le traitement de surface (grenaillage, nettoyage par ultrasons, électropolissage, décapage, passivation, revêtements, peinture), l'assemblage/installation ainsi que le conditionnement et la certification des données numériques. Gagorik et Poorganji se concentreront ici sur les méthodes de traitement de surface.
Nous remercions également le fabricant de machines 3DEO, la plateforme de fabrication en ligne Factorem et SPC – Surface Treatment Experts pour les ressources partagées.
Justifier l'importance des méthodes de traitement de surface
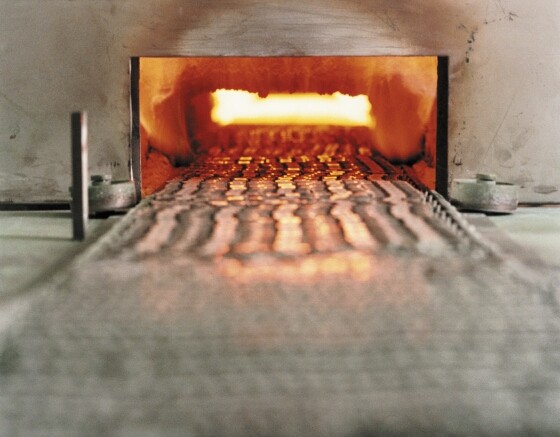
Les catégories de méthodes de traitement de surface ne sont pas normalisées. Par conséquent, leur liste varie souvent d'une organisation à l'autre ; ou bien elle dépend du type de "propriétés esthétiques, de toucher ou de pièces" qu'elles apportent aux pièces. Jusqu'à présent, nous avons identifié
- Les méthodes de finition qui comprennent le polissage à la main, le sablage ou le meulage à commande numérique. La catégorie des "finitions mécaniques" qui comprend le ponçage, le polissage par ultrasons¸ le grattage et le culbutage, le polissage magnétique, le rodage, le limage ou le lissage à la vapeur.
- Les revêtements, qui peuvent inclure l'anodisation, le revêtement en poudre, la peinture ou le placage.
- La catégorie " finition par tranchant non définie " qui comprend le sablage abrasif, et la finition vibratoire.
- La catégorie "finition par énergie électrique" qui comprend l'électropolissage ;
- La solidification par déformation plastique : le grenaillage de précontrainte.
Selon Panhuis, quelle que soit l'option de traitement de surface que vous choisissez, les questions les plus importantes à aborder concernent les "dimensions de la pièce, la rugosité souhaitée, les exigences optiques, le type de traitement (s'agit-il d'un traitement manuel ou automatique ?)". Il va sans dire que le type de pièces que vous traitez peut également jouer un rôle clé dans l'option de traitement de surface que vous choisirez. Une pièce médicale imprimée en 3D fabriquée en titane ne sera pas post-traitée comme une autre fabriquée en acier. Une pièce médicale imprimée en 3D peut n'être que grenaillée, tandis qu'une pièce en acier, en fonction de ses caractéristiques mécaniques et de sa destination finale, peut être peinte, plaquée ou limée. "Pour certaines pièces encore, nous devons vérifier le degré de contamination autorisé par le produit de sablage", ajoute Panhuis.
Gagorik et Poorganji vont plus loin puisqu'ils prennent en compte la complexité de la pièce, ses performances mais aussi toutes les étapes qui peuvent influencer son coût final. Ils attirent l'attention sur le fait que « la capacité d'appliquer correctement/complètement un traitement sur toutes les surfaces prévues peut être entravée par l'augmentation de la complexité de la conception de la pièce ». Dans ce cas, les facteurs clés sont la propreté, la topologie de la surface et l'accessibilité. « Une préoccupation importante est la façon dont les exigences de surface dans les pièces imprimées en 3D sont liées aux propriétés des matériaux (par exemple HCF, LCF, corrosion) et aux performances globales de la pièce. Ce point est essentiel car il dicte le traitement de finition de la surface et les paramètres à atteindre pour chaque pièce CTQs*. Cela déterminera finalement le coût et la viabilité du processus de FA », expliquent les experts.
*CTQ = Critical to Quality specifications
Quid des méthodes de traitement de surface ?
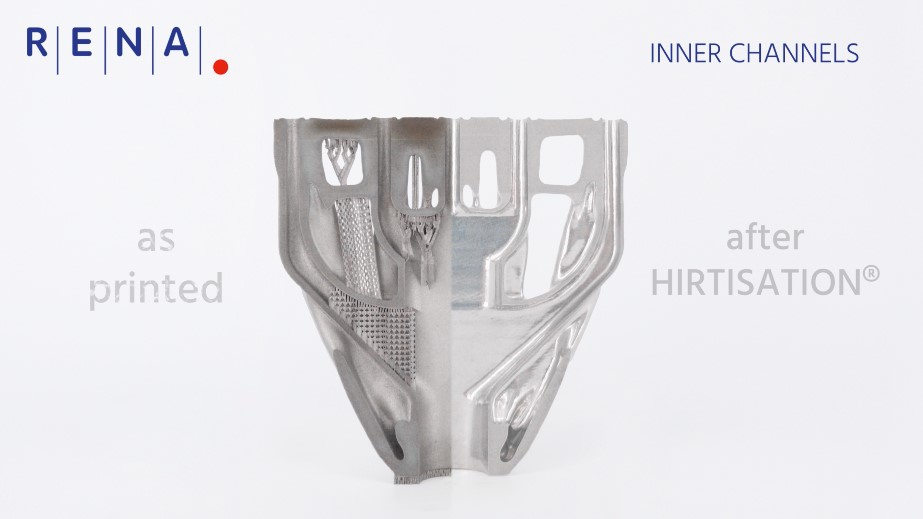
Si bon nombre des mêmes raisons de choisir une option de finition de surface s'appliquent aussi bien aux pièces imprimées en 3D qu'aux pièces fabriquées par des procédés de fabrication conventionnels, les premières caractéristiques à prendre en compte lors du choix d'une méthode de finition de surface sont celles de la pièce.
« Il doit être largement déterminé par l'environnement d'exploitation prévu (assemblage/installation, fonctionnement/performance, maintenance, mise hors service) de la pièce. Elle ne doit pas être déterminée uniquement par les normes, spécifications, "meilleures pratiques" existantes, etc. – car toutes ces approches ont été créées avec des hypothèses/conditions spécifiques qui peuvent ne pas s'appliquer dans tous les cas. Des économies importantes (en termes de délais et de coûts en aval) peuvent être réalisées en prenant le temps d'interroger votre application avant de la concevoir/définir. Le traitement de surface est généralement déterminé par les CTQs de la pièce, les exigences dimensionnelles, et dépend fortement du processus de FA (Modalité) », soulignent les experts de Morf3D.
Ceci étant dit, examinons certaines de ces méthodes – indépendamment de leur catégorie principale :
- Le ponçage est l'une des méthodes de traitement de surface les plus connues. Elle consiste à frotter des particules abrasives sur la surface d'une pièce en créant une texture de surface aléatoire et non linéaire. En d'autres termes, un matériau rugueux tel que le papier de verre peut être utilisé pour lisser et éliminer les petites imperfections d'une surface. Le ponçage est le plus utile lorsqu'il est appliqué à des surfaces courbes ou profilées. Toutefois, les experts doutent de son efficacité lorsqu'il s'agit de coins serrés.
- Le polissage par ultrasons, quant à lui, est idéal pour la finition interne des coins, trous ou poches serrés qui peuvent être assez difficiles d'accès. Dans cette méthode, un outil souple à pointe fine monté sur une broche à ultrasons vibre à 30 kHz, ce qui, en combinaison avec une pâte abrasive, induit une onde de pression qui travaille en toute sécurité la surface pour créer un polissage fin. Ce qui est intéressant dans ce procédé, c'est que la pointe de l'outil n'est pas en contact avec la surface de travail. Il fonctionne bien sur l'acier trempé, et il y a peu de risques d'endommager la pièce.
- Les options de polissage comprennent également le polissage au laser, où un faisceau laser à haute énergie fait fondre à nouveau le matériau de surface des pièces pour réduire la rugosité de surface. En théorie, cette méthode permet d'obtenir une rugosité de surface de 2~3μm (Ra). En pratique, le coût élevé des équipements de polissage au laser ralentit l'adoption de cette technique dans les processus de post-traitement de la FA.
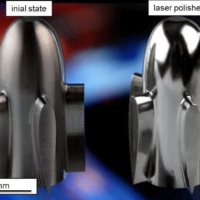
- Le polissage chimique peut également réduire la rugosité de surface d'une pièce donnée à 0,2~1μm.
- Le grattage et le culbutage sont similaires au ponçage dans la mesure où des particules abrasives sont utilisées pour modifier la rugosité de surface de la pièce imprimée en 3D. Selon SPC – Surface Treatment Experts, le grattage est similaire à la vibration, mais il fait tourner les composants et le milieu de polissage dans un tambour plutôt que de les faire vibrer. Il s'agit d'un mouvement plus doux, ce qui rend le grattage meilleur pour les pièces plus délicates et celles comportant des détails fins. L'appareil utilisé est souvent appelé système à barillet centrifuge.
- Destiné à accroître la résistance et la durabilité d'une pièce, le grenaillage de précontrainte consiste à utiliser de l'air sous pression pour projeter de minuscules billes de métal ou de plastique sur une surface à grande vitesse.
Le processus de grenaillage de précontrainte est très similaire au grenaillage à billes. Ce procédé permet d'atteindre facilement l'intérieur des canaux et autres endroits délicats. L'opérateur utilise ici un pistolet pour projeter des thermoplastiques finement rectifiés sur la surface, éliminant ainsi les imperfections et lissant la surface.
- Dans la méthode de sablage, l'opérateur projette des particules abrasives sous haute pression sur la surface de la pièce. Ces particules abrasives peuvent être utilisées en combinaison avec de l'air et de l'eau, et couvrent une grande surface assez rapidement. Différents niveaux de finition de surface peuvent être obtenus en utilisant différents types de médias abrasifs. En fonction du cas d'utilisation, l'opérateur peut améliorer les propriétés mécaniques du métal en augmentant sa résistance à la fatigue et en améliorant sa résistance à la corrosion grâce au grenaillage.
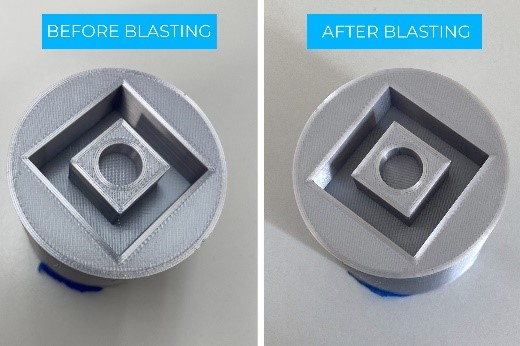
- La finition vibratoire est un procédé d'usinage avec une arête de coupe indéfinie. L'objectif est d'améliorer la qualité de surface des petites pièces. Pour ce faire, on arrondit les bords, on effectue des opérations de lissage et on rectifie.
- Le placage consiste à recouvrir l'acier d'une petite couche d'un matériau inerte. Il permet de protéger la pièce de base contre la corrosion et l'oxydation. Malgré ces avantages, il faut noter que la pièce peut être endommagée par les chocs, l'usure et d'autres facteurs externes.
Une méthode de traitement de surface peut être effectuée après que la pièce a refroidi et est exempte de poudre. Cependant, comme vous pouvez le deviner, les avantages d'une méthode de traitement de surface peuvent compenser les inconvénients qu'une autre méthode peut causer à la pièce. C'est pourquoi, selon Gagorik et Poorganji, l'ordre approprié des étapes de post-traitement dépend des exigences de la configuration finale d'une pièce donnée.
« Les processus de préparation de surface (y compris le nettoyage par ultrasons, l'écoulement abrasif, l'électro-polissage, le fraisage chimique) interviennent généralement avant tout revêtement de surface (y compris l'anodisation, la métallisation/céramique, la peinture), et peuvent parfois être nécessaires (en tant qu'opérations de nettoyage) avant les traitements thermiques et les processus d'assemblage également. Habituellement, la finition de surface intervient aux étapes ultérieures/finales du post-traitement. Toutefois, les séquences du processus sont conçues de manière à maximiser la performance et à minimiser le coût », soulignent les experts.
Un élément clé au cœur des méthodes de traitement de surface : la rugosité de la surface.
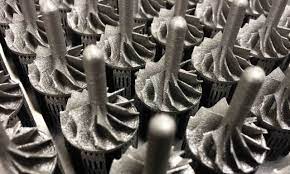
Les experts ont clairement indiqué que tous les aspects de la pièce imprimée en 3D, tels que le matériau, la forme, l'épaisseur et le poids, l'utilisation prévue et l'environnement dans lequel elle sera utilisée, comptent lorsqu'il s'agit de choisir une option de finition de surface. Toutefois, au-delà de tous ces aspects, l'accent a été mis sur "le problème de la rugosité de surface" des pièces fabriquées par voie additive.
« La rugosité de surface est une mesure de la variance de la topologie de la surface d'une pièce. La rugosité peut affecter l'esthétique de la pièce (par exemple, brillante ou maNe) et son comportement mécanique, comme l'amorçage de fissures, la résistance à l'usure, la durée de vie en fatigue, la marine, l'étanchéité, les roulements et la dynamique des fluides. Plus les surfaces d'une machine dynamique intégrée sont rugueuses, moins elle fonctionnera de manière silencieuse, efficace et sûre. La réduction de la rugosité, ou frottement, est essentielle dans les pièces mécaniques telles que les pistons, les roulements et les surfaces d'étanchéité, où un contact trop important entre les surfaces mobiles peut entraîner une usure rapide. Les spécifications peuvent différer selon les cas, mais la rugosité exigée d'une pièce d'utilisation finale peut être un facteur important dans le calcul de son coût. L'analyse de la rugosité de surface comprend l'utilisation de paramètres pour inspecter et déterminer si la pièce fabriquée répond aux normes de contrôle de la qualité. Cela aide les fabricants et les concepteurs à quantifier la rugosité de l'état de surface qu'ils choisissent », commente Matt Sand, fondateur et CEO de 3DEO.
Cette explication en implique une autre : l'état de surface peut varier de manière significative selon le procédé d'impression 3D [même au sein d'un même procédé, mais avec des paramètres différents]. Par conséquent, nous ne pouvons pas légitimement dire que certaines options de traitement de surface fonctionnent bien avec certains procédés d'impression 3D de métaux.
Pour Morf3D, il est essentiel de comprendre les conditions de départ pour une application acceptable du traitement de surface nécessaire pour un matériau et une application de pièce donnés, puis de déterminer les processus de fabrication nécessaires pour y parvenir. Prenant l'exemple de leurs capacités internes, Gagorik et Poorganji notent que les traitements de surface qu'ils utilisent aujourd'hui sont la version avancée/développée des processus existants pour les processus conventionnels qui sont modifiés ou orientés vers les besoins des pièces imprimées en 3D. Par exemple, l'accès aux canaux internes qui sont plus rugueux qu'un canal usiné, ou le polissage chimico-mécanique de la surface d'un composant rotatif.
Enfin, les raisons d'utiliser une finition de surface s'appliquent aussi bien aux pièces imprimées en 3D qu'aux pièces fabriquées par des procédés traditionnels. Étant donné que les différentes options de finition s'accompagnent de coûts différents, la responsabilité, selon les mots des experts de Morf3D, ne repose pas sur la technologie utilisée pour la fabrication, mais sur des équipes de conception et de fabrication informées qui collaborent pour prendre les meilleures décisions sur ce qu'il convient d'utiliser.
Image d’Une : pièces imprimées 3D par 3DEO. N’oubliez pas que vous pouvez poster gratuitement les offres d’emploi de l’industrie de la FA sur 3D ADEPT Media ou rechercher un emploi via notre tableau d’offres d’emploi. N’hésitez pas à nous suivre sur nos réseaux sociaux et à vous inscrire à notre newsletter hebdomadaire : Facebook, Twitter, LinkedIn & Instagram ! Si vous avez une innovation à partager pour le prochain numéro de notre magazine numérique ou si vous avez un article à faire connaître, n’hésitez pas à nous envoyer un email à contact@3dadept.com.