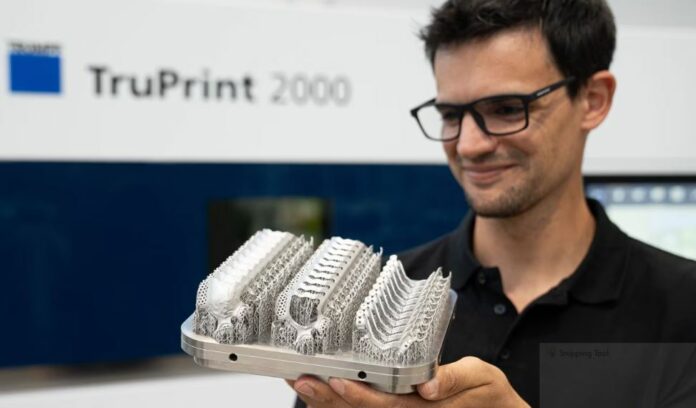
100-year-old machine manufacturer TRUMPF will be showcasing a new 3D Printer at Formnext 2023.
The company uses its 3D printers for its own sustainable production of series AM parts and also provides services to other industries like aerospace. Recently, Airbus Helicopters reduced costs and fuel consumption by making 3D-printed aircraft parts for passenger airplanes using TRUMPF 3D printers.
The TRUMPF 3D printers can run 24 hours a day for the whole week while experts identify and develop 3D printed series components. Hence, they are useful in many industries like dental, medical, aerospace and others.
Speaking about AM technologies, the CEO of TRUMPF Laser and System Technology, Richard Bannmüller said : “Additive manufacturing beats all conventional manufacturing methods in terms of cost and carbon footprint for some of our components. One example is the production of engine coolers built into the cutting units of the TruLaser 5030. We save costs and have been able to reduce CO2 emissions per part produced by 83 percent compared to a conventionally manufactured assembly”.
Key specifications of the upgraded TruPrint 2000 3D printer
As a reminder, the upgraded industrial 3D printer is designed for medical engineering and other applications with lofty standards and quality demands. It serves the production of removable partial dentures, spine cages or even knee implants. First unveiled in 2019, the 3D printer has been enhanced to reflect the latest developments of TRUMPF’s core technologies.
With its so-called motorized beam expander, the TruPrint 2000 automatically adjusts the spot diameter of the laser to the task at hand. Depending on the application, the spot diameter is 55 or 80 micrometers. The 80-micrometer spot enables higher productivity. Users can use the 55-micron spot when special metal powders require a higher energy density. The machine comes with a multilaser option and a powder bed monitoring option. This means that OEMs of highly regulated industries such as medicine can improve their productivity with two TRUMPF fiber lasers. The high-tech company has increased the power of the integrated fiber laser to 500 watts as an alternative to the 300W laser in the basic configuration. In such case, a 55-µm beam diameter can be exposed simultaneously in the build area and generate up to 80% more parts in the same time with flexibility.
Designers can use the TruPrint series of 3D printers to rethink the design of components in additive manufacturing and print hard to implement geometries. This has been utilised by other industries to make things like 3D printed bicycle parts, said TRUMPF CEO.
Read more about the TruPrint 2000 3D printer in the September/October edition of 3D ADEPT Mag.
Remember, you can post job opportunities in the AM Industry on 3D ADEPT Media free of charge or look for a job via our job board. Make sure to follow us on our social networks and subscribe to our weekly newsletter : Facebook, Twitter, LinkedIn & Instagram ! If you want to be featured in the next issue of our digital magazine or if you hear a story that needs to be heard, make sure to send it to contact@3dadept.com