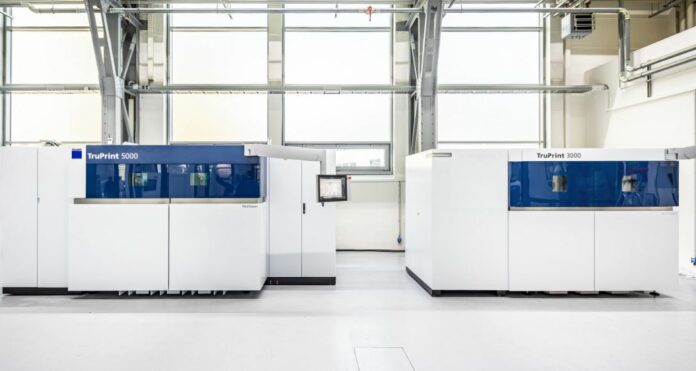
In a major development, aerospace giant Airbus Helicopters has used 3D printed parts created by high-tech manufacturing solutions provider TRUMPF to improve its fuel consumption.
Now, Airbus Helicopters has used some TRUMPF metal 3D printers to mass produce 3D printed parts for aircraft components. As a reminder, TRUMPF specializes in the development of (Laser) Powder Bed Fusion (PBF/LPBF) or Laser Metal Deposition (generative laser deposition welding).
Airbus Helicopters achieved two objectives through this – lightweight construction and fuel saving.
Recently, the aerospace giant has expanded its additive manufacturing capabilities with a new 3D printing center in Donauwörth, Germany and TRUMPF has supplied the necessary machines for 3D metal printing there.
Speaking about using TRUMPF machines to generate 3D printed parts for the aerospace industry, Helmut Färber, Site Manager at Donauwörth Airbus Helicopters center said: “With innovative manufacturing processes, we are working on the helicopters of the future in Donauwörth. Among other things, 3D printing helps reduce the weight of components”.
According to Airbus Helicopters, 3D-printed aircraft parts will help aircraft operators in reducing fuel consumption, ultimately lowering their costs. These 3D printed parts can also make the aerospace industry more eco-friendly as it reduces the sector’s carbon footprint by lowering CO2 emissions in flight.
The aerospace giant is taking advantage of 3D printing technology to make aircraft components for its electric-powered CityAirbus and also the high-speed racer helicopters. Passenger aircrafts like Airbus A350 and A320 will also have 3D printed parts.
The CEO of TRUMPF Richard Bannmüller underlined how adopting 3D printing technology saves cost and reduces waste by stating, “Additive manufacturing saves expensive raw material and can lower production costs in the aviation industry. 3D printers only use the material that designers actually need for their components and that ends up taking off in the aircraft. Conventional manufacturing processes, on the other hand, require up to ten times more raw material than the final product. Therefore, when milling or chipping, much of the raw material ends up being wasted”.
Remember, you can post job opportunities in the AM Industry on 3D ADEPT Media free of charge or look for a job via our job board. Make sure to follow us on our social networks and subscribe to our weekly newsletter: Facebook, Twitter, LinkedIn & Instagram! If you want to be featured in the next issue of our digital magazine or if you hear a story that needs to be heard, make sure to send it to contact@3dadept.com