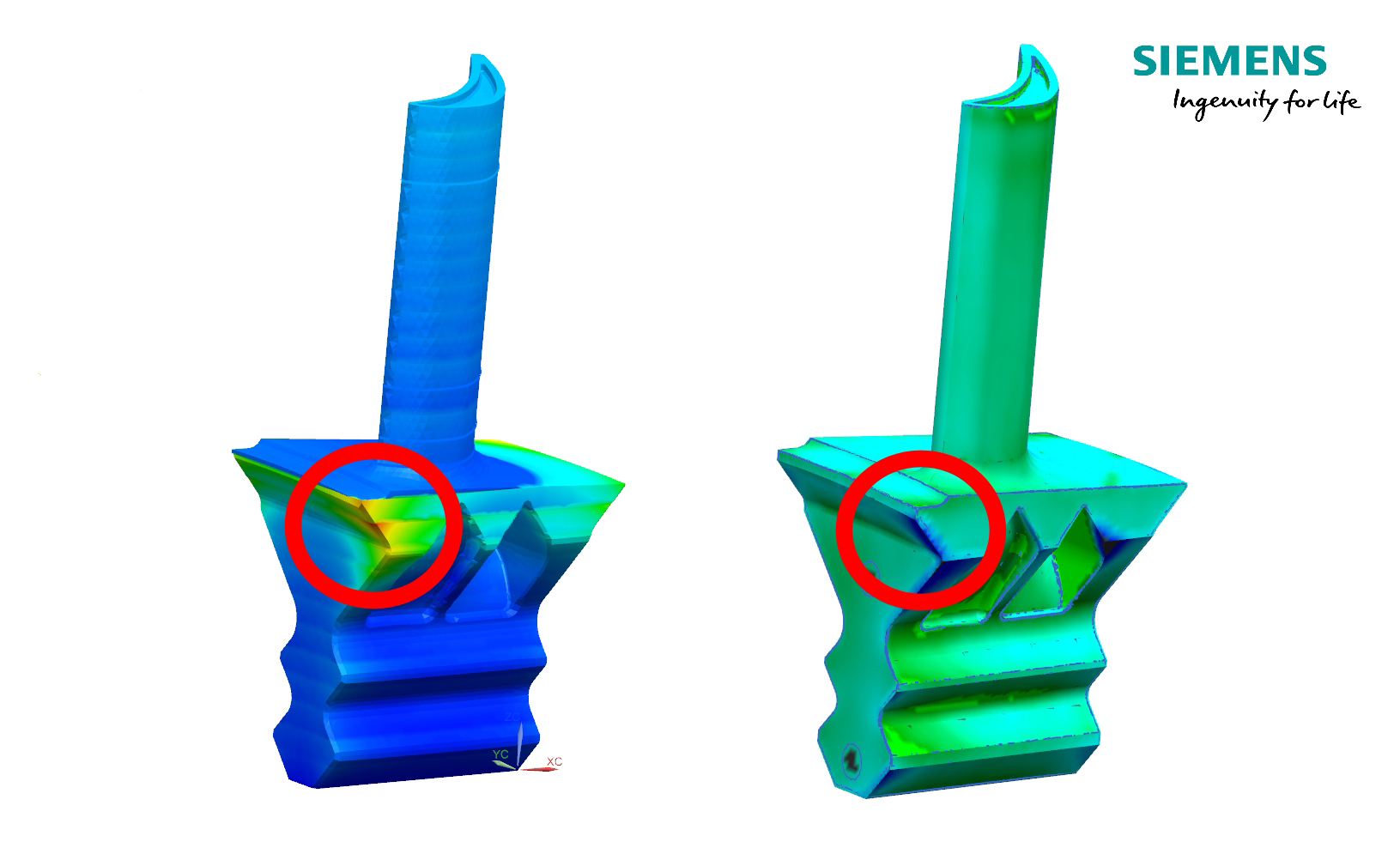
So far, 3D printing companies have been using Siemens software either for the design of parts or to address waste avoidance issue in manufacturing. Siemens is also aware of accuracy issue when it comes to manufacturing and offers today a simulation software to tackle this issue.
The product is fully integrated into Siemens’ end-to-end Additive Manufacturing solution, which assists manufacturers in designing and printing useful parts at scale.
The AM Process Simulation solution uses a digital twin to simulate the build process prior to printing, anticipating distortion within the printing process and automatically generating the corrected geometry to compensate for these distortions.
This simulation is paramount for constructing a ‘first time right’ print, and necessary for achieving the efficiencies required of a fully industrialized additive manufacturing process.
When metal parts are 3D printed, the method used to fuse the layers of the print typically involves heat. As the layers build up, the residual heat can cause parts to warp inside the printer, causing various problems, from structural issues within the part itself to print stoppage. Issues such as these cause many prints to fail, and make getting a “first-time-right” print very difficult. Simulation of the printing process can help to alleviate many of these problems.
The AM Process Simulation solution offers the ability to iterate on a solution between the design and build tray setup steps of the workflow, and the simulation step. This closed feedback loop is possible due to the tightly integrated nature of the Siemens digital innovation platform. The simulation data created feeds into the digital thread of information which informs each step of the printing process.
This digital backbone enables the system to develop pre-compensated models and, more importantly, to feed those seamlessly back into the model design and manufacturing processes without additional data translation. This high level of integration is what customers need today in order to be successful in industrializing additive manufacturing.
For further information about 3D Printing, follow us on our social networks and subscribe to our newsletter
Would you like to subscribe to 3D Adept Mag? Would you like to be featured in the next issue of our digital magazine? Send us an email at contact@3dadept.com
//pagead2.googlesyndication.com/pagead/js/adsbygoogle.js
(adsbygoogle = window.adsbygoogle || []).push({});