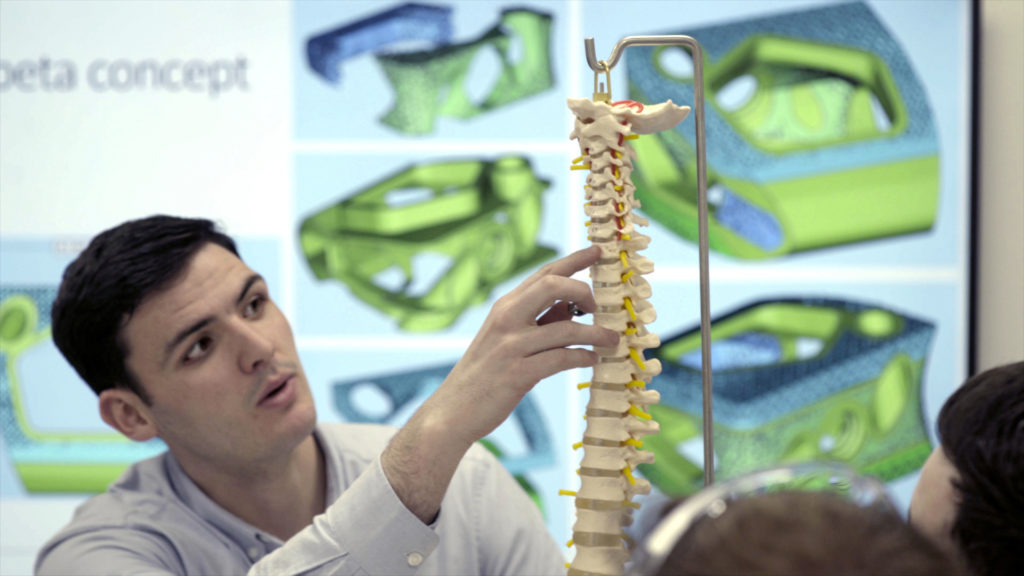
A report from the National Center for Health Statistics demonstrates that one in four individuals suffers from chronic low back pain. Furthermore, treatments for low back pain are expensive both at the individual and national levels. Therefore, prevalence of spinal ailments, development of safer technology and cost-effective spinal devices as well as increasing request for minimally invasive spine surgery are part of the factors that drive the growth of this market.
As far as technology is concerned, companies increasingly demonstrate the potential of AM in the production of spinal implants. Renishaw recently showed a great example of the use of this technology by collaborating with Irish Manufacturing Research (IMR) and nTopology. The teams that worked on the project demonstrate how streamlined the transition from design to AM can be when working with the right partners.
As part of this collaboration, IMR designed a representative titanium spinal implant, aimed at the cervical spine (c spine), using advanced manufacturing software company nTopology’s generative design software. The research institute thereafter produced the implants using Renishaw’s RenAM 500M metal AM system.
Ed Littlewood, Marketing Manager of Renishaw’s Medical and Dental Products Division explained: “an implant with a lattice structure is lightweight, can be optimised to meet the required loading conditions and has a greater surface area, which can aid osseointegration. Therefore, AM implants can be designed to mimic the mechanical properties of bone, resulting in better patient outcomes. But all of this comes to nothing if you do not have the tools to create the design.”
“Traditional CAD tools weren’t built to design complex lattice structures; the job would be difficult or even impossible,” explained Matt Rohr, nTopology’s Application Engineering Manager. “nTopology was designed to complement existing workflows and make the job easier. We cut the design time of complex structures from days to minutes which was a crucial component in helping this project run to schedule.”
For further information about 3D Printing, follow us on our social networks and subscribe to our newsletter!
Would you like to be featured in the next issue of our digital magazine? Send us an email at contact@3dadept.com
//pagead2.googlesyndication.com/pagead/js/adsbygoogle.js (adsbygoogle = window.adsbygoogle || []).push({});