With thousands of layer images to analyze when searching for errors, it’s easy to miss a critical defect that will result in the non-validation of a part. The fact is the powder recoating conducted after each printed layer is prone to error: If the surface to be exposed is not coated evenly and completely, this can lead to defects in the component.
To address this solution, AM users increasingly turn to automated software solutions that could help them do the job during the 3D printing process. It’s the case of aerospace company Isar Aerospace that recently integrated the nebumind software into its 3D printing process (LPBF – Laser Powder Bed Fusion) to automate the identification and reporting of defects during the application of a new powder layer.
The company of the same name is based in Germany and develops analytics software stores and visualizes manufacturing data as digital product twins. Its software detects defects through automated analysis of the powder bed images, providing the engineer with important information for evaluating the quality of the printing process.
The problem with the manual analysis of recoater images
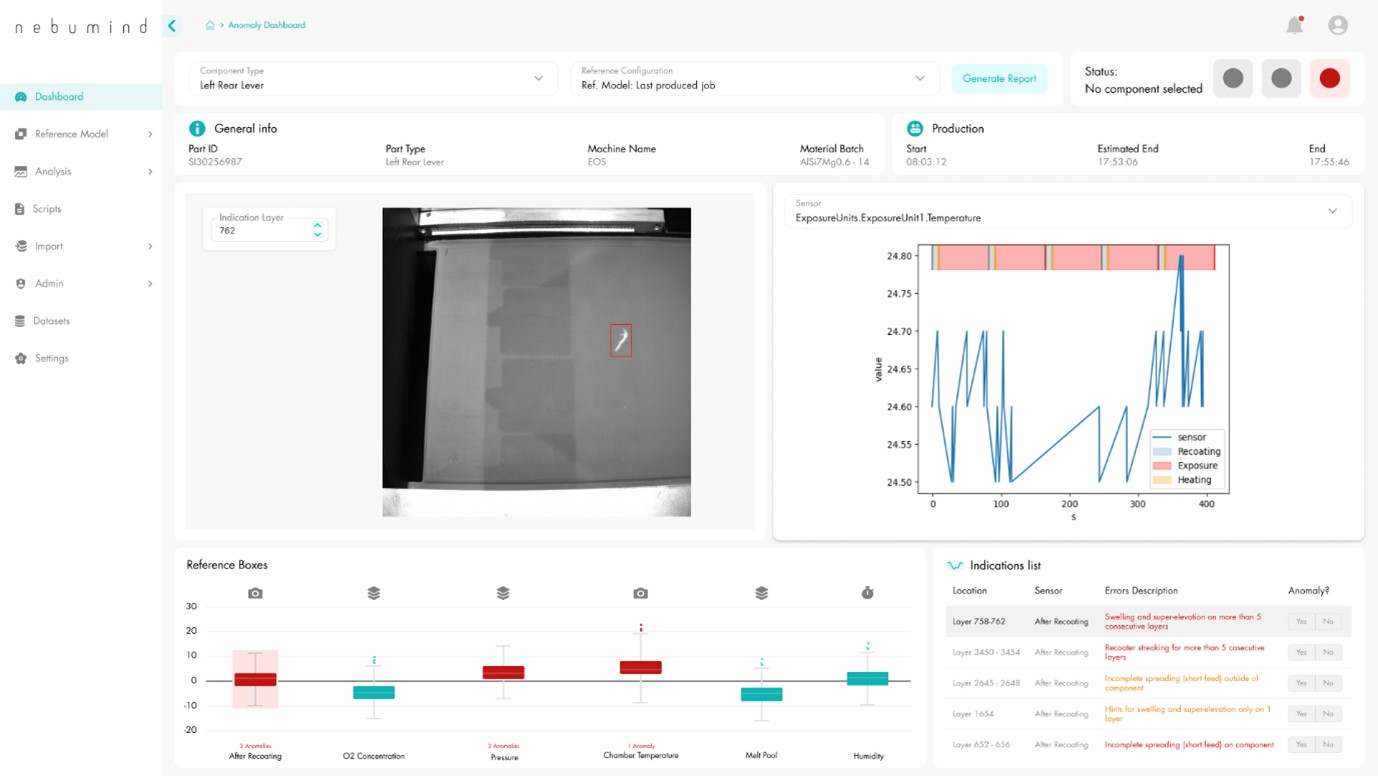
The problem is simple: sensors and cameras integrated into the L-PBF systems monitor the coating step, that are manually analyzed for uncoated areas, damage to the recoater or other defects by engineers responsible for the process. This approach is extremely time-consuming: for instance, if a 3D printed metal component generates 2,500 recoater images and an engineer takes 3 seconds to analyze each image, they spend more than 2 hours on this task for one build job alone. Moreover, as the analysis is conducted in a post-processing step, defects are usually only identified after a component has been printed.
nebumind automates image analysis and presents defects in-process in digital twin format
To prevent this manual process, Isar Aerospace has connected the nebumind software into its machine environment automating the defect detection for each recoating layer. The software receives powder bed images before and after recoating, generated by an optical camera with a resolution of 1280×1024 pixels, and extracts them automatically via the direct machine interface. The software uses an algorithm to spot defects in the images automatically. For its algorithm, nebumind has employed primarily stable algorithms from image and edge detection. In addition, the positions of the defects are analyzed across multiple layers to minimize the false positive rate.
According to nebumind, Isar Aerospace has been able to save up to 80% using its software compared to the previous manual analysis, as engineers can focus on the images labeled by the algorithm.
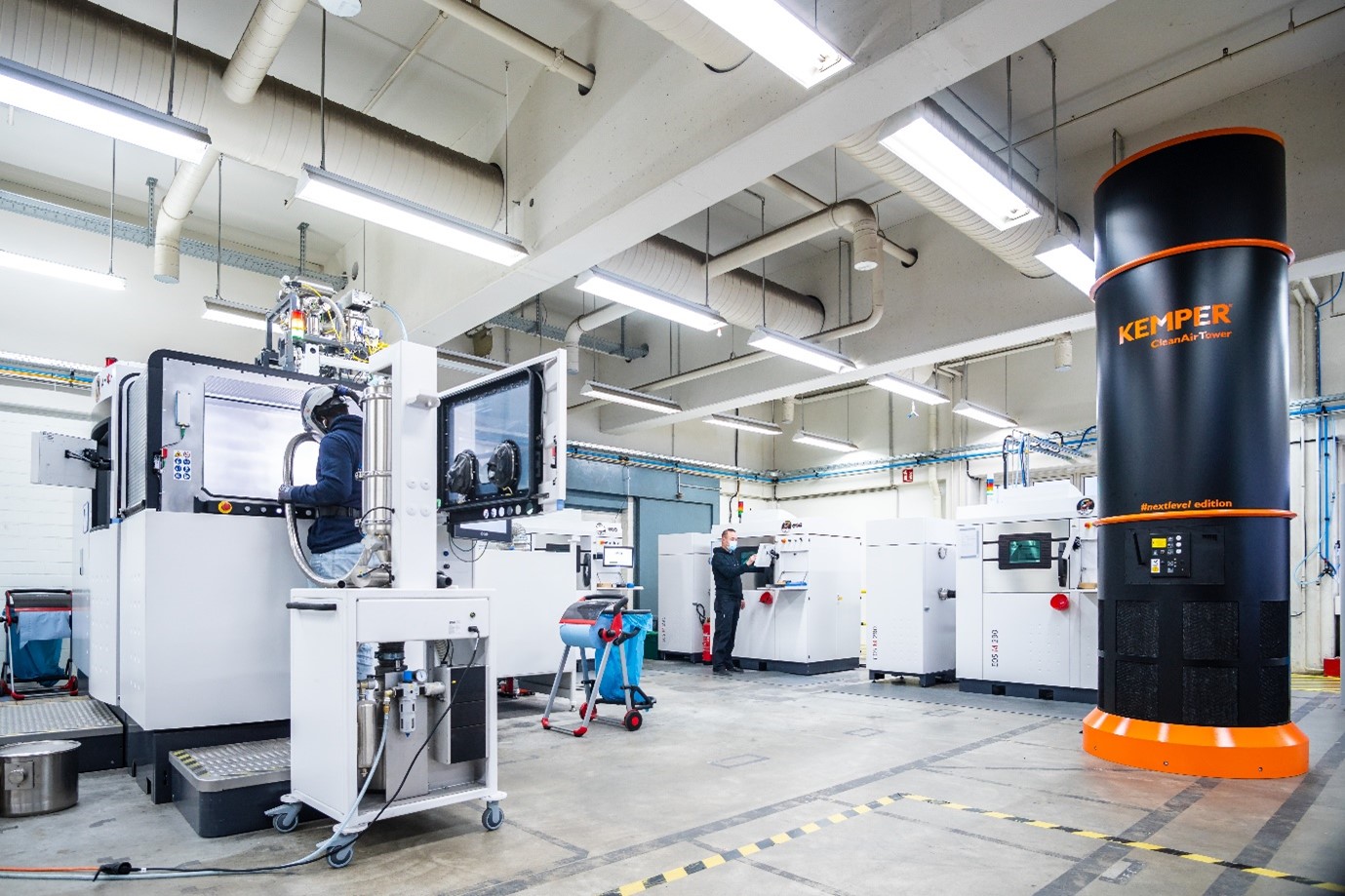
Read more about the identification of defects during the metal 3D printing process.
Moving forward, nebumind’s defect recognition will be moved upstream from post- printing to in-process, so that the software will be able to point out possible anomalies immediately after coating, thereby enabling the user to stop the printing process in the event of an irreparable defect. To further automate the process, it is planned to correlate the found recoater defects with other process data from the print job and CT data from the final quality check to identify root causes and prevent recoater defects from happening in the first place. In the long term, nebumind not only wants to monitor the printing process with its software, but also to intervene in the process in a regulating manner, for example to stop the printing process in the event of irreparable errors or to compensate for an incorrect coating in the subsequent layer, the company explains.
Remember, you can post job opportunities in the AM Industry on 3D ADEPT Media for free or look for a job via our job board. Make sure to follow us on our social networks and subscribe to our weekly newsletter: Facebook, Twitter, LinkedIn & Instagram ! If you want to be featured in the next issue of our digital magazine or if you hear a story that needs to be heard, make sure you send it to contact@3dadept.com