Put two Additive Manufacturing veterans together, with respective expertise on both the commercial and current economic market of the AM industry and the technological side, and you can expect a conversation on insights that matter into the additive manufacturing world. A few weeks ago, during a morning coffee discussion, Markus Glasser, Senior Vice President of EMEA at EOS & Marius Lakomiec, Team Manager Digital AM Solutions at EOS, sat down with me to discuss digitization and automation. It’s fair to say I went through a wide range of emotions on that day – and I am going to tell you why below – but I eventually had to admit that Industrial 3D Printing company EOS makes magic happen when it comes to the integration of digitalization and automation across the most demanding industries that leverage AM technologies.
If you had told me four years ago to sit down with Glasser and Lakomiec to discuss digitalization and automation within the AM industry, I would have said no. The reason for this is simple: I am very cautious about buzzwords – If not well utilized, they can easily become a solid marketing weapon that companies use to promise a lot and deliver little on the production ground floor. And if we had to make a list of the top five buzzwords used in our industry, digitalization and automation will be on top of it. So, while I was dubious at the beginning of this conversation with EOS representatives, I paid great attention to the team’s mindset, strategy, and technology strengths and how they are currently deployed to achieve their objectives.
On another note, it’s crucial to take into consideration the current market – which is driven by a lot of economic, political and even sanitary changes (due to the Covid-19 pandemic), and these changes urge industries to recognize the now vital importance of digitalization and automation processes, to foster their adoption for the good of their business.
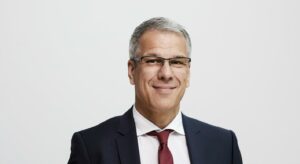
“We cannot move forward without taking into consideration all of these aspects”, Glasser says, talking about the current economic, political and even sanitary changes. “We now even have to take into consideration the increasing energy costs that the market has to deal with. This means that we have to explore new ways of creating markets and products that save energy. Digitalization and automation play a key role in enabling that. Let’s take the example of the automotive industry: while the world needs a dependable alternative to fuel-based transportation – something that electric vehicles may very well help with, automotive OEMs face several challenges regarding procuring components, supply chain and quality concerns – to name a few -, all of which can be addressed through digital transformation, AM and automation. Similar concerns are faced by manufacturers in the consumer goods industry who depend a lot on resources that come from China to manufacture their final products. One thing we learned from the pandemic is that there is an opportunity to explore if we focus on the local market and this can be done safely if digitization and automation help to mitigate these risks”, he adds.
Before emphasizing Glasser’s statements, Lakomiec’s first words implied that he had understood those feelings raised by buzzwords: “The thing with buzzwords is that they do not enable professionals to focus on what matters: the technology that enables real transformation not to mention that they give this impression that [manufacturing processes can be adjusted and improved in the blink of an eye]. Industry 4.0, digitization and digital thread are truly buzzwords and make the whole work on a factory floor takes time. It should be about technology and how it enables transformation.” Taking the example of the supply chain within the automotive industry, Lakomiec explains that automotive OEMs have started reconsidering their strategy for the production of components. The reality is, the number of hurdles keeps increasing: the shortage of raw materials, price inflation, not to mention manufacturing issues that could have been prevented, etc. creating a domino effect across the whole value chain.
The automotive industry is just one example among many and the truth is, there are so many items to consider that it can quickly become overwhelming for companies trying to find their path in this journey. While taking into account the current economic, social and political environment, my conversation with EOS’ representatives highlights three areas of interest for the current AM market:
- Where it makes sense to integrate digitization and automation right now
- The cost consideration and
- The next area of focus.
Where it makes sense to integrate digitization and automation right now
The topic of digitalization and automation is so broad that it can fill an entire magazine. As a global trade press that focuses on AM, it made sense to discuss it through the prism of vertical industries adopting AM technologies.
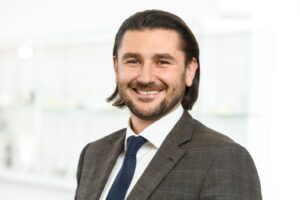
“We should explore each component that may affect manufacturing as part of the supply chain. To do so, in our AM division, we apply real digital twins that may simulate everything upfront”, Lakomiec outlines.
As the drive towards digitalization gains momentum and the value of the digital thread is sung from all corners of the industry, the digital twin has positioned itself as one of the advanced technology concepts that could help manufacturers earn credibility and viability in the new digital manufacturing realm. In a recent dossier dedicated to digital twin (DT) technology, 3D ADEPT Media found out that DT might be a potential solution that can be leveraged to overcome many issues in additive manufacturing but the lack of thorough understanding of the DT concept, framework, and development methods constitute key factors that slow down the development and integration of such technology across AM production environments. The DT concept goes beyond what may happen to a physical product, to encompass the prediction of production and performance within specific environments. This means that industry insiders’ understanding of DT may vary from one situation to another, as they can refer to the DT of a product, production or performance.
In this specific case, EOS’ Team Manager Digital AM Solutions focused on the importance of DT within a production environment. This means that their technology can create a virtual copy of a real-world component in the manufacturing process by using inputs from a real-world component to mirror the real part’s status, functionality, and/or interaction with other devices.
“By applying DT, we can identify, predict and solve issues upfront. We can know exactly the quantity of parts a production might require, the number of machines required for their production – if we apply medium or large size machines -, if there will be bottlenecks, where these bottlenecks would be if they occur, the number of shifts required and even the number of operators that will be needed during the production”, the Team Manager Digital AM Solutions explains.
If you are just like me, and before watching a film, you watch the trailer and read the synopsis (and everything in between) to have the certainty that you will not be disappointed because the film will have a happy ending, then the DT technology is for you. You will not be disappointed at the end of the production because you would have assessed supply chain dynamics, identified issues before they happen and anticipated process success.
Speaking of the vertical industries that will benefit the most from DT, the Senior Vice President of EMEA mentions the “aerospace, energy and medical industries if we stick to metal 3D printing applications.” “Overall, we can ensure that the customer benefits from the entire value chain. We are currently working with various partners such as Siemens Energy to optimize a wide range of solutions. Our long-term objective is to enable the adoption of our DT technology across the entire value chain from product to production and performance”, he adds.
In the meantime, the team focuses on immediate issues to address and works hand-in-hand with partners who bring different technical expertise to the table. By working on specific projects (such as the “air conditioner” project mentioned in the lines below), the EOS team can develop optimized processes for end-use applications. That being said, Glasser notes that the vertical industry that will certainly benefit the most from the DT technology is the aerospace industry. “It’s an industry that is currently leveraging AM [and looking to leverage AM – for OEMs who are not there yet –] for series production. According to Glasser, with aerospace companies, the discussion is no longer about whether or not they should adopt DT but about change management – (a topic we discussed with Oerlikon’s CEO Markus Tacke – specify page in the mag or embed link). “It’s about certifying the entire process to achieve viable end production”, Glasser points out.
So far, in theory, the DT technology is a promising technology that can drastically change any manufacturing business. In practice, we know any advanced solution comes at a price that all companies cannot always afford and that’s a reality leading technology providers should not neglect.
The cost consideration
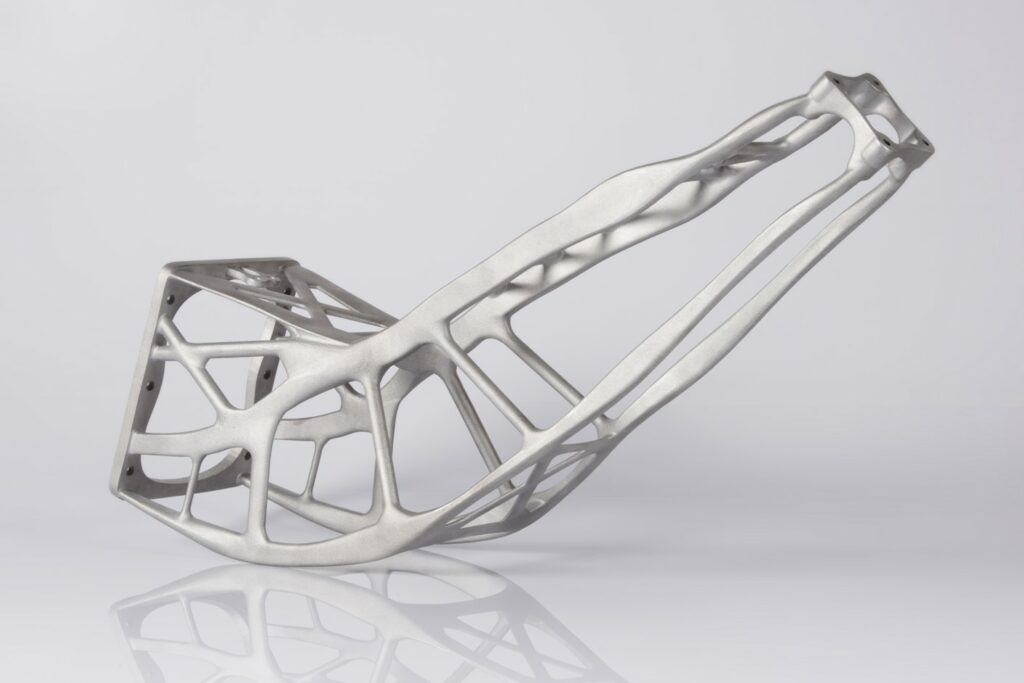
In the current industry, large OEMs and corporations regularly make headlines with announcements related to the inaugurations and creations of “factory of the future” technology centers. The latter showcase digital manufacturing and automation solutions, and require large investments to roll out changes to production. Smaller players have a different history. For them, process and technology changes are driven by more concrete, nearer-term ROI which means they cannot always have the resources to integrate digital manufacturing solutions, yet they should also be able to leverage these technologies.
“And they can”, Glasser enthuses. “We have a contract manufacturing process with certified manufacturers that enables SMEs to benefit from advanced digital manufacturing solutions. We are currently working with Oerlikon in that area. And much more can be done: we can also reshape a bit our portfolio, and reduce the CAPEX for smaller entities and we work to integrate innovation centers where SMEs could learn more about technology solutions they could leverage in their business”.
“We have also seen SMEs get directly involved through projects funded by the EU or regions. Such projects provide companies with standards and regulations they can utilize in their activity. The POLYLINE project is a great example as it gathers experts from science, research and industry around the development of automation solutions for the use of AM in the automotive industry. Other solutions for SMEs could be to explore platforms created by software companies that aim to enable (local) production across several countries”, Lakomiec comments.
The next area of focus
With everything that has been said in the lines above, with the increasing cost pressure on the one hand and the main challenge of AM which is to ensure repeatability, on the other hand, areas of focus right now vary from one company to another.
Lakomiec outlines that quality assurance, digitization and automation are items that will always be discussed at multiple levels and different degrees but the cost conversation, and the ability to secure and control the value chain are items that will affect decision-making processes, therefore they should be the next focus.
For Glasser, on the other hand, the next area of focus should be applications. Like many industry insiders, Glasser believes that working on the right applications helps to advance and optimize manufacturing processes. One of the recent partnerships shows that EOS is currently walking the talk as together with Hyperganic, they will build a residential air conditioner that uses 10 times less energy using AM.
Moving forward I understand each of their different visions: having complete control over costs, QA and value chain is somehow having the certainty that your application will be viable, and meet industry standards but enabling applications through these processes is the tangible example that demonstrates they perfectly work together. It’s a virtuous circle.
This double interview was undertaken on the lead up to AMTC, Europe’s C-level conference dedicated to Additive Manufacturing – and where EOS took an influential role. It has first been published in the September/October edition of 3D ADEPT Mag.