15 companies from science, research and industry will join forces in a project called POLYLINE. Funded by the German Federal Ministry of Education and Research with a total of €10.7 Mio, the three-year project aims to develop a next-generation digitalized production line.
The project is part of the funding measure “Line integration of additive manufacturing processes” as part of the funding program “Photonics Research Germany – Light with a Future”.
Put simply, it consists in strengthening conventional production techniques (e.g. machining, casting, etc.) with additive manufacturing (AM) in the form of high-throughput line production line systems.
The project partners include EOS GmbH, BMW Group – Additive Manufacturing, Grenzebach Maschinenbau GmbH, 3YOURMIND, Additive Marking GmbH, DyeMansion GmbH, Bernd Olschner GmbH, Optris Ltd, Krumm-tec, Paderborn University, Fraunhofer Institute for Casting, Composite and ProcessingTechnology IGCV, Fraunhofer Institute for Material Flow and Logistics IML, Dortmund University of Technology – Chair of Computer Science VII “Computer Graphics”, University of Augsburg, and University Duisburg Essen – Chair of Production Engineering.
How it all started
Despite the advancements of additive manufacturing technologies, it should be noted that there is still a number of limitations in the integration of these technologies in industries that were used to leverage conventional manufacturing processes. These limitations are mainly due to a lack of standards across process chains.
Indeed, AM-specific workflows are very different from conventional manufacturing processes. Added to the low level of automation of the physical handling and transport processes as well as the non-continuity of the digital data chain along the horizontal process chain, the current manufacturing landscape reveals a lack of transparency and an increased risk of errors.
During the upcoming years, the consortium will therefore look for flexible solutions to scale additive production chains.
“To achieve this, it is important to record and document all central characteristic values and quality criteria (including identification, history and measured values) from the CAD model to the final part. The individual sub-processes of production – from process preparation to the selective laser-sintering process, cooling and unpacking as well as cleaning and post-processing – will be automated and integrated into the planned production line, in which all the technological elements of an SLS production chain will be fully linked for the first time”, the consortium explains in a press communication.
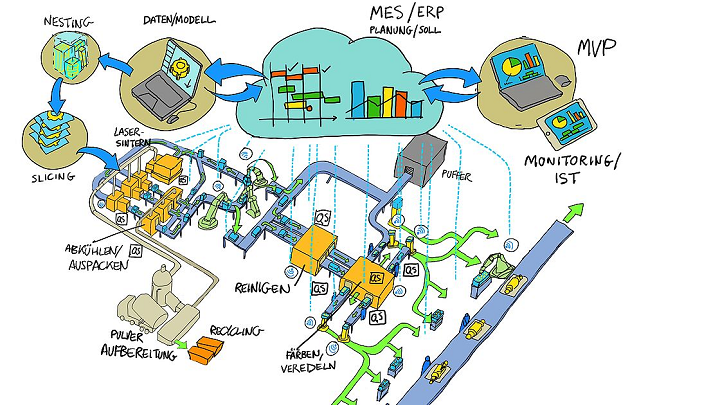
Based on various use cases including customized components as well as serial components in large quantities, POLYLINE will use a holistic method that will take into account all required processes.
Remember, you can post free of charge job opportunities in the AM Industry on 3D ADEPT Media or look for a job via our job board. Make sure to follow us on our social networks and subscribe to our weekly newsletter : Facebook, Twitter, LinkedIn & Instagram ! If you want to be featured in the next issue of our digital magazine or if you hear a story that needs to be heard, make sure to send it to contact@3dadept.com