Used for everything from cars, medical implants, jewelry to heat exchangers and more, titanium is appealing for its lightweight, strong, stable properties and ability to withstand corrosion. Its low density and high strength make it the ideal material for a wide range of demanding applications, but these characteristics are also the ones that make it difficult to process via conventional manufacturing routes such as casting, hence the increasing interest for additive manufacturing users in exploring it. Here is the thing, titanium often suffers from a bad reputation due to its “rarity”. While manufacturers do not explicitly say it is “rare”, they do recognize it is rarer than other metals, which results in a higher selling price.
This manufacturing and economic context has drawn the attention of Anastasios “Taso” Arima, Founder and CEO of IperionX, who has made it a key business goal to revitalize a low cost, low carbon U.S. titanium industry.
“Titanium has the potential to be a key critical material that can be substituted for more widely used higher-carbon metals, particularly stainless steel and aluminum. It is a superior metal to stainless steel and aluminum due to its properties such as high strength-to-weight ratio and excellent corrosion resistance and is critical to the global aerospace, medical, space and defense sectors. Not to mention, titanium was listed in the top 50 minerals deemed essential to the economic and national security by U.S. Department of the Interior”, Taso told 3D ADEPT Media.
Founded in 2020, IperionX turned stealth mode off this year by planting its flag to be the first name in American titanium, from raw materials to manufacturing. The company’s bold ambition to develop US-based sustainable critical mineral and critical material supply chains, to facilitate the global transition towards a closed-loop, low-to-zero carbon, resource efficient and socially inclusive green economy is backed by the founder’s strong experience in the exploration, implementation, financing and permitting of projects.
“I successfully developed one of the leading lithium projects in North America, Piedmont Lithium. Once that project was well advanced and with a strong management team in place, I began to look at other supply chains in the United States that are vulnerable and need to be re-shored; titanium was a standout. We identified very quickly that both titanium mineral and metal supply chains need to be rebuilt in the U.S., and we have secured a very large mineral deposit in Tennessee, and have combined it with an advanced, highly sustainable titanium metal production technology”, Taso points out.
In just one year (since it turned stealth mode off), IperionX has achieved milestones that others couldn’t achieve in several years of activity. A few of them include a partnership with ORNL to develop low-cost titanium alloys for additive manufacturing, the production of low-carbon spherical titanium from Tennessee minerals, a listing on Nasdaq and even a partnership with luxury watchmaker Panerai to additively manufacture titanium watches.
Each of these milestones has been propelled by a range of proprietary production technologies capable of producing the low-carbon spherical titanium metal using “100% recycled titanium scrap metal as a feedstock”.
How does the production process work?
In order to understand the capabilities of these production processes, it’s crucial to shed light on the various grades of titanium for outsiders to this sphere. Indeed, determining that titanium is the correct metal for a production is one thing, choosing the right grade of this material is another one – and certainly one of the most crucial steps as the right grade is essential to ensure a successful completion of a production.
Four commercial pure titanium grades (grades 1, 2, 3 and 4) have been identified on the manufacturing market. As far as titanium alloys are concerned, some of the widely-known grades include Grade 5 (Ti 6Al-4V) Titanium, grades 7, 12 and 23 (Ti 6AL-4V ELI).
While all grades are corrosive resistant, strong and lightweight, there are still some important differences that could impact the final results. Choosing a titanium grade requires to consider how the metal will be used, what conditions the titanium will be in, and the size of the titanium parts.
Taking the example of the recently developed spherical titanium powder alloy Ti64, Taso explained how their team has been able to meet the important Grade 5 quality specifications. The grade 5 is said to be the “workhorse” of the titanium alloys – and of the aerospace industry. It accounts for 50% of total titanium usage the world over.
From a manufacturing standpoint, it can be heat treated to increase its strength, used in welded construction at service temperatures of up to 600° F, and it delivers high strength at a light weight, useful formability and high corrosion resistance.
Such material is a great fit for the production of aircraft turbines and structural parts; it is also used in high-performance engine parts, sports equipment biomedical implants, to name a few applications.
Interestingly, to produce such a high-quality spherical titanium alloy powder and make it compatible with AM, the IperionX team relies on a three-step patented production process: they sourced medium grade titanium minerals (ilmenite) that they upgraded to a +99% titanium dioxide feedstock using the proprietary Synthetic Rutile and Alkaline Roasting and Hydrolysis (“ARH”) process technologies. They blended the high-grade titanium feedstock with oxides of the alloying elements and reduced it using the patented Hydrogen Assisted Metallothermic Reduction (“HAMR”) technology to obtain low-carbon angular titanium powders. The last step consists in utilizing the patented Granulation Sintering Deoxygenation (“GSD”) technology to produce the high-quality spherical titanium powder alloy Ti64.
“We can process this scrap metal to create angular and spherical titanium powder as commercially pure titanium, or as various titanium alloys to be used in applications including additive manufacturing and powder metallurgy”, Taso explains.
While the conventional Kroll process continues to be the dominant technology for the production of titanium metal, the founder of IperionX outlines that avoiding this process has enabled the team to bypass a series of energy intensive titanium melt processes, ingot manufacturing, wire production and gas atomization, which in the end take time, increase the final cost of the material and are not necessarily environmental-friendly.
How sustainable IperionX’ proprietary titanium metal processing technologies are?
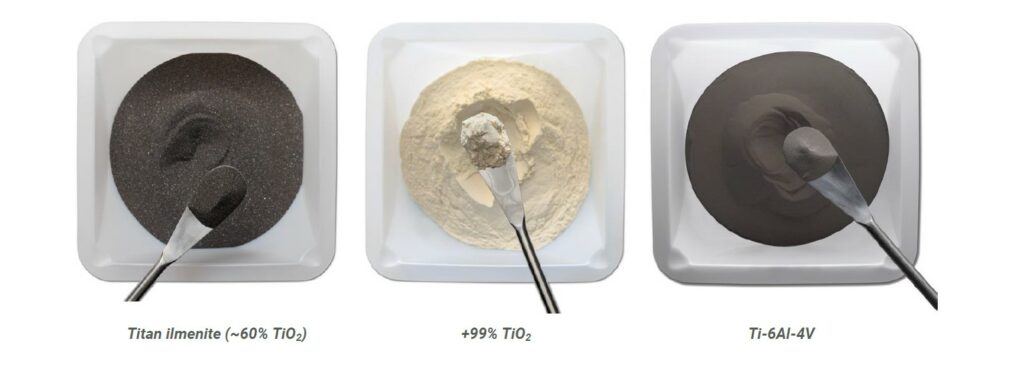

As discussed with Michela Ferraro-Cuda in the article dedicated to precious metals AM (page 29 of this edition of 3D ADEPT Mag), “an organization can truly say it is sustainable when it is responsible vis-à-vis these three aspects: it should be profitable, and responsible vis-à-vis its people and the planet.”
Despite the current burden that weighs on most material producers, it turns out that IperionX is in a position to legitimately say it is a sustainable-focused organization. Indeed, producing high-quality materials is great, being able to do so while meeting eco-friendly production requirements is even better. By doing both, IperionX has currently nothing to envy to other metallic powder producers.
“In our current economy, we often take materials from the Earth, make products from them, and eventually throw them away as waste – the process is linear. Companies in the minerals industry tend to produce a lot of waste with their processes and then products aren’t recycled. Right now, a significant amount of titanium scrap ends up in the landfill and is too hard to recycle because of its high oxygen levels, but with our technology that is all going to change. Our HAMR technology enables us to significantly lower the oxygen content in titanium produced from scrap metal, and enables a fully recycled, high quality, integrated and low-cost supply chain of titanium”, the company’s representative highlights.
To demonstrate how their technologies do not involve the numerous carbon intensive melting processes seen in the Kroll process, the IperionX team compares the various steps they follow to produce titanium alloys with the ones most manufacturers follow by using the Kroll process:
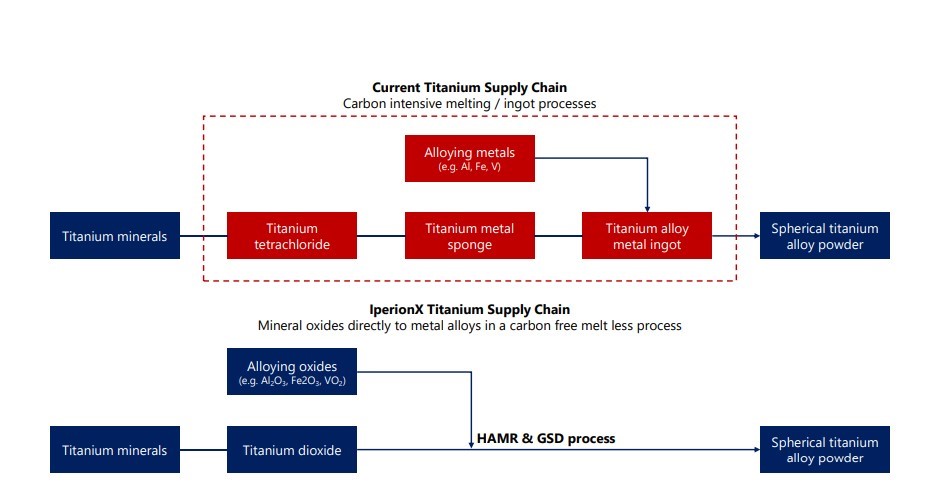
Taso underlines: “Our technologies can produce titanium from either 100% scrap titanium or from conventional titanium minerals. Whilst this image shows the production of titanium metal from titanium minerals, which we have the potential to sustainably source from our Titan Project in Tennessee, we can also do exactly the same thing but with titanium scrap”.
Furthermore, researchers from the University of Utah recently performed a techno-economic analysis and a full process simulation in ExtendSim (a well-known chemical processing simulation software) to estimate the energy consumption, emissions, and cost at mass production; the ultimate goal was to assess the commercial viability of the HAMR process.
With a key focus on the feed materials, reaction conditions (temperature and pressure), and side processes (pretreatment of the feed materials and post-treatment of the products), the findings reveal that the HAMR process is 50% less energy intensive and generates 30% less emissions than the Kroll process, even after accounting for an additional purification step of the TiO2 feed prior to the HAMR process.
The bulk of the energy and emissions savings comes through eliminating the need to chlorinate TiO2 to make TiCl4, and vacuum distillation after the reduction of TiCl4. For the GSD process, the improved yields from this new pathway allows for production to occur at more than 50% lower cost, dramatically lowering the potential price point of high quality Ti powder while keeping energy usage and emissions comparable to the state of practice, a report reads.
In the long-run, from a cost standpoint and thanks to partnerships with organizations such as ORNL, Taso said their “process will potentially be able to lower manufacturing costs by over 75%” – taking into account the fact that current spherical powder pricing is typically in the $150/kg to $250/kg range.
The next step one can expect from IperionX
Although its current focus is to deliver added value for the additive manufacturing market, it should be noted that IperionX can produce both spherical and angular powders. To re-shore the titanium supply chain, the company focuses its operations on the U.S. for now. For Taso, “the US needs to reduce its dependency on Russian and Chinese titanium. Making these processes more sustainable and low-cost is key to ensuring a better future for generations to come”.
“As we grow and continue to scale, we believe we have the potential to produce at a very competitive price point with the potential to capture market share from the aluminum and stainless-steel markets. [For now, we need to focus on the] re-emergence of domestic titanium supply chains – but created sustainably and at low cost”, Taso concludes.
This interview has first been published in the 2022 September/October edition of 3D ADEPT Mag.
Remember, you can post job opportunities in the AM Industry on 3D ADEPT Media or look for a job via our job board. Make sure to follow us on our social networks and subscribe to our weekly newsletter : Facebook, Twitter, LinkedIn & Instagram ! If you want to be featured in the next issue of our digital magazine or if you hear a story that needs to be heard, make sure you send it to contact@3dadept.com