Materials producer IperionX Limited is on a mission to scaling Titanium production for additive manufacturing with 100% recycled titanium metal as feedstock. For the US-based manufacturer, one way to achieve that is to rely on patented low-carbon titanium metal technologies which has been successful since it has recently upgraded Tennessee titanium minerals into high grade +99% TiO2 and then into a high-quality spherical titanium alloy powder.
Testing confirmed that IperionX’s Ti64 powder meets important Grade 5 quality specifications, which accounts for ~50% of global titanium metal use, including in aerospace turbines, structures and engine components.
The low-carbon titanium spherical powder was produced by using a range of patented technologies, including:
▪ Medium grade titanium minerals (ilmenite) sourced from IperionX’s Titan Project were upgraded to a +99% titanium dioxide feedstock using the proprietary Synthetic Rutile and Alkaline Roasting and Hydrolysis (“ARH”) process technologies.
▪ The high-grade titanium feedstock was blended with oxides of the alloying elements and then reduced with using the patented Hydrogen Assisted Metallothermic Reduction (“HAMR”) technology to produce low-carbon angular titanium powders.
▪ The patented Granulation Sintering Deoxygenation (“GSD”) technology was used to produce a high-quality spherical titanium powder alloy Ti64.
Ti64 is a widely used alloy of titanium, aluminum and vanadium that provides high strength-to-weight ratio, excellent corrosion resistance and biocompatibility. Spherical Ti64 powders are used to manufacture advanced components with additive manufacturing / 3D printing.
Titanium alloy powders are currently produced with the Kroll process to firstly create titanium metal sponge, which is then refined via a series of high energy titanium melt processes to produce large batch titanium alloys as ingots. These ingots are then processed into titanium alloy wire/rod, which are feedstocks for high energy plasma / gas atomization that produces spherical titanium alloy powders.
The technologies avoid the high-cost, high-carbon Kroll process to create titanium sponge, but also bypass the series of energy intensive titanium melt processes, ingot manufacturing, wire production and gas atomization, to produce low carbon and low-cost titanium spherical powders. The technologies have the potential for up to a 95% reduction in Scope 1 and 2 carbon emissions compared to the incumbent Kroll titanium supply chain. The technologies eliminate the direct carbon emissions from producing titanium, generate no Scope 1 emissions, and by utilizing 100% renewable power in the production process, Scope 2 carbon emissions can also be eliminated. The technologies can also produce titanium alloys directly from the oxides of the alloy elements. This offers a valuable opportunity to deliver customers a wider range of lower cost, innovative titanium alloys on shorter lead times. This includes the potential to offer titanium alloys which are difficult to produce with incumbent technologies such as Ti-1Al-8V-5Fe (“Ti-185”), which offers high strength and fatigue life for military applications, and Ti-Palladium allow for superior corrosion resistance in demanding applications or luxury goods.
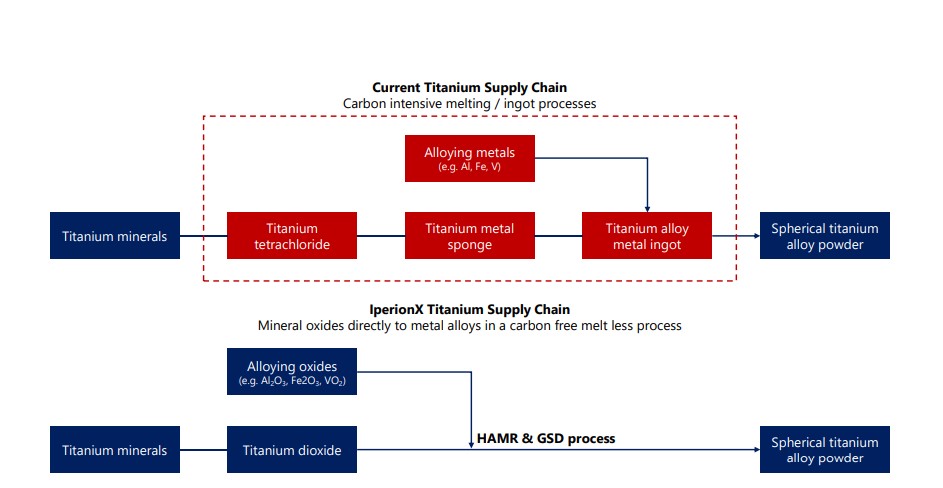
The U.S. is completely dependent on imports of high-carbon primary titanium metal feedstocks produced via the high-cost Kroll process, and it currently lacks the surge capacity required to support defense and critical infrastructure needs in an extended national emergency.
In contrast, Russia and China’s market share of global titanium sponge production continues to increase and is expected to pass over 70% share this year. The ability to produce high quality spherical titanium metal powders using titanium minerals from the Titan Project in Tennessee demonstrates the potential for IperionX to re-shore an all-American low-carbon titanium supply chain – taking raw Tennessee critical minerals, or recycled titanium feedstock – and applying proprietary technology to produce high-quality, low-carbon commercial grade titanium metal and alloys in the U.S.
Further, the production of spherical titanium powders produced via the HAMR & GSD processes from minerals in Tennessee supports IperionX’s collaboration with Oak Ridge National Laboratory under a U.S. DOE approved User Agreement to develop low-cost titanium alloys for additive manufacturing , including opportunities to use titanium powders to parts which currently rely on other metals, such as stainless steel and aluminum.
“The need to secure a cost effective, low carbon, all-American titanium metal supply chain is of critical importance to major U.S. industries and the U.S. defense sector. Today’s announcement highlights that these innovative technologies can produce low carbon titanium metal and its alloys directly from domestically sourced titanium minerals from our Titan critical minerals project in Tennessee. These patented technologies can deliver production of innovative titanium alloys that were not possible with the current melt processes. The signing into law of the Inflation Reduction Act (2022) last week was an important turning point for re-shoring critical low carbon American supply chains and provides a wide range of U.S. government funding opportunities and incentives to accelerate the scale-up of emerging technologies to reduce the U.S. reliance on foreign supply chains. These include $40 billion for DOE Loan Programs Office loan commitments, $500 million for the DOD DPA Title III program, and a 10% production tax credit for critical mineral and metal production in the U.S., enabling the acceleration of actions to fund and secure these critical supply chains”, Anastasios (Taso) Arima, IperionX’s Managing Director and CEO concludes.
Remember, you can post job opportunities in the AM Industry on 3D ADEPT Media free of charge or look for a job via our job board. Make sure to follow us on our social networks and subscribe to our weekly newsletter : Facebook, Twitter, LinkedIn & Instagram ! If you want to be featured in the next issue of our digital magazine or if you hear a story that needs to be heard, make sure you send it to contact@3dadept.com