Professionals of the Maritime, Oil and Gas (MOG) industries take major risks to gain valuable global opportunities. Some of these risks involve adopting new regulations and laws, climate change, as well as production of parts, hence the importance of continuous monitoring on a number of daily operations.
As far as production of components is concerned, DNV GL’s global network that specializes in failure investigation carried out a report that revealed that tubes and piping are the most failure-prone components in the oil, gas and maritime industries; fatigue and corrosion being the most common failure types.
The research was based on over 1 000 failure cases studied across the United States, Europe and Asia.
“The cost of prevention, monitoring, repair or replacement as a result of these forms of component degradation can run into billions of dollars. Potentially, financial penalties can occur if major incidents and loss of life result from such a failure”, explained Koheila Molazemi, Technology and Innovation Director, DNV GL – Oil & Gas.
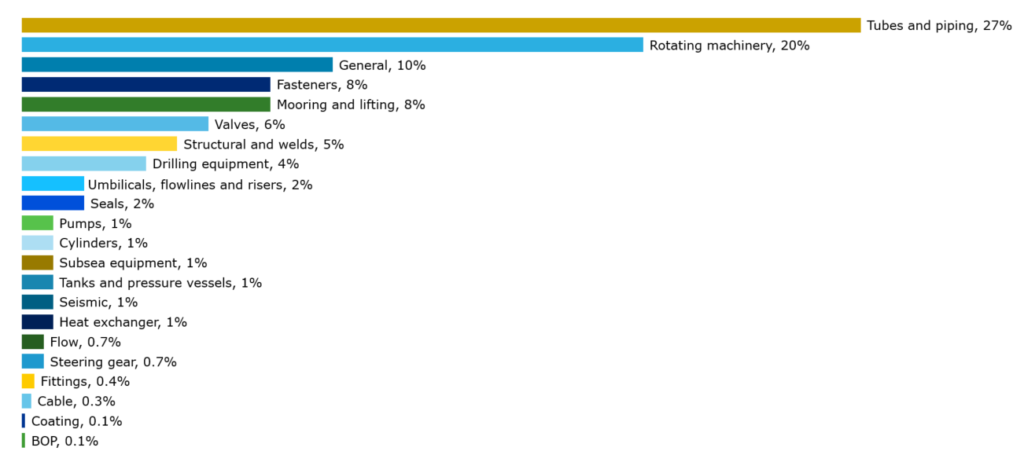
To avoid or minimize these common failure types, professionals have been considering digital solutions and digital manufacturing technologies that deliver better sustainability. One of these technologies is Additive Manufacturing. However, while AM has been widely adopted in aerospace, automotive, and medical industries, the MOG industry remains a nascent adopter of the technology.
This article aims at highlighting the main outlines & commercial opportunities to take into account while considering AM in this sector of activity.
To discuss this topic, we have called for the expertise of two main companies:
- DNV GL, an international accredited registrar and classification company that provides services for several industries including maritime, renewable energy, oil & gas, electrification, food & beverage and healthcare.
- Guaranteed, a spin-off company from Finindus, ArcelorMittal Belgium and OCAS, that aims to ensure first-time-right part production and provide one-stop-shop reliability, for their customers. The company leverages a unique process control software that enables to significantly reduce the number of expensive trial and error loops.
Ramesh Babu Govindaraj, DNV GL – Maritime Principal Specialist for Material, Welding and Additive Manufacturing and Eva Junghans, DNV GL – Maritime Senior Principal Engineer for Materials and Welding have answered our questions in the DNV GL team. The two colleagues give further information about the use of AM in the maritime industry.
Joachim Antonissen and Sander Plasschaert have answered our questions in regard to the use of AM in the oil & gas industries.
Anticipating the risks in the oil, gas and maritime sectors
SmarTech Publishing’s latest report on additive manufacturing for the oil and gas sector predicts that the oil and gas sector will generate $2 billion (USD) in revenues by 2027. This future seems even more promising for the 3D Printing industry, as according to Research and Markets, the use of 3D Printing in Oil & Gas sector is estimated to be worth $32 Billion by 2025, which means this sector would become a major adopter of additive manufacturing technologies.
Based on experiences in rapid prototyping and tooling within other industries, several oil and gas operators and suppliers, ambition now to use additive manufacturing to gain a key competitive edge in the production of advanced and complex final parts.
DNV GL is one of the companies that early anticipated this growth but also the challenges and risks adopters of AM in this sector would face. That is why, in 2017, it released a classification guideline for the use of additive manufacturing (AM) in the maritime and oil & gas industries.
For manufacturers, sub-suppliers of materials, parts and components, service suppliers and end users adopting AM technologies, this guideline would serve as a tool that will ensure the parts or components created by an AM process and the materials from which they are created have the same level of quality assurance as traditionally manufactured products.
Two years ago, an Oil & Gas Consortium launched two Joint Innovation Projects (JIPs) which aimed at defining a guideline and a business model for the use of additive manufacturing in the Oil, Gas and Maritime industries. 11 companies started the project in 2018 and they were joined by 9 other companies at the end of 2019.
“The approach by the DNVGL JIP programme was based on the FMEA (Failure Mode and Effects Analysis) workshop which was attended by all participants. There the failure mitigation process was established and the testing to capture the weakest zone in applications was considered.
Operators: They are the end-users, and provide their expectations for quality, functionality and service durability for their assets.
Contractors: They do the design, specify the detailed requirements for the components and optimize the design to achieve the full benefit from Additive Manufacturing.
Fabricators: They provide information related to the printing process and establish the essential variables which are important in order to obtain material properties meeting the requirements” commented Ramesh Babu Govindaraj & Eva Junghans.
The completion of these projects led to tangible applications of AM in this segment and a deeper understanding of challenges a manufacturer can encounter to produce a 3D printed part for this segment. We’ve asked Guaranteed, one of the companies involved in these projects what these challenges can be and how is the manufacturing process different from what operators use to see with conventional manufacturing processes.
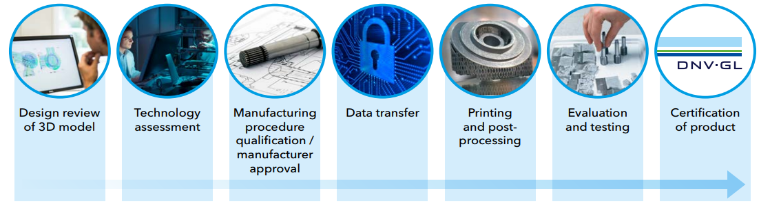
A question of price
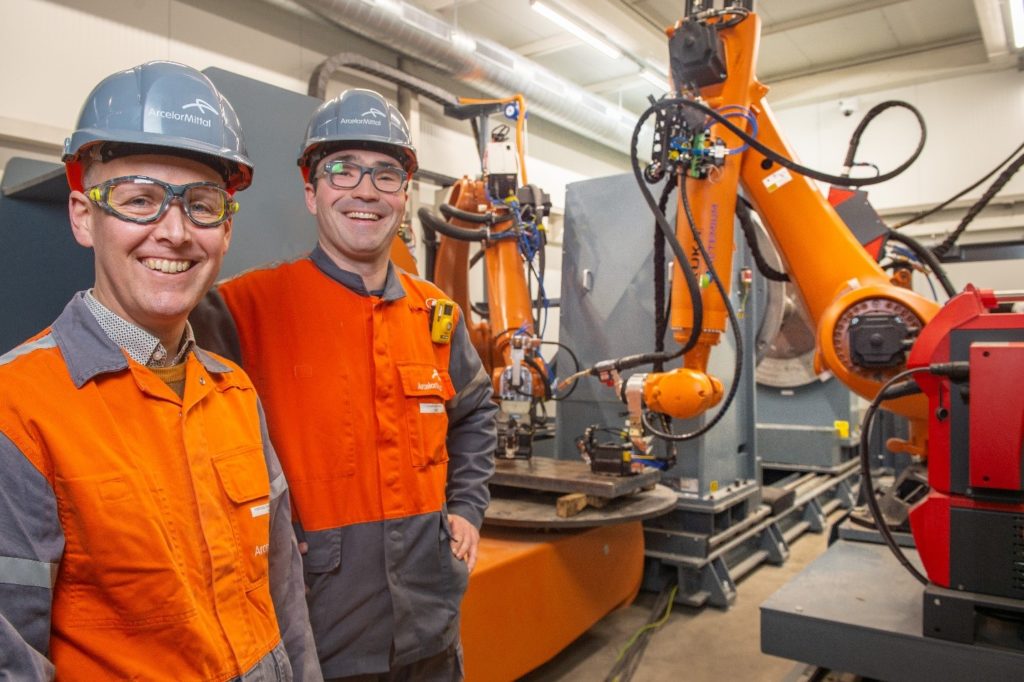
Joachim Antonissen and Sander Plasschaert explained that,“the oil & gas industry often uses cast or forged components made out of rather expensive specialty alloys such as e.g. Inconel. On the one hand, the forging process itself results in significant material waste, while also being characterized by extended lead times and non-negligible failure rates which potentially impact the future operations. Although this clearly emphasizes the opportunity for AM in the sector, the severe operating conditions call for a clear quality assurance framework, while also often imposing components to be large and heavy.
At the same time as the technology shifts from lab to fab, the business case really needs to be there in order for industry to adopt AM. The combination of component size and functional complexity makes a compelling case for wire based DED-processes such as the WAAM-process offered by Guaranteed B.V. as it allows parts of several meters to be produced within hours at a competitive cost. The wide choice of available wire materials which come at a considerably lower cost as their powder counterparts, combined with the fact that quasi 100% dense parts are produced, omitting the need for hipping, further contributes to the economic attractivity of the technology for the segment. As the WAAM-technology furthermore allows to deposit on top of an existing component (e.g. plate or cylinder) or even repair an existing part, the business case can be further enhanced even without taking into account logistic savings such as reduced lead times or stock keeping costs. Besides the resulting economic benefits localized repair or on-demand near net shape production furthermore also contributes to sustainability as it significantly reduces the need for raw materials and transport logistics.
Simultaneously the strict certification requirements imposed by the severe operating conditions in oil & gas industry also need to be considered when assessing the business case. Depending on the criticality level of the component, certification might impose a substantial amount of destructive test samples to be produced alongside the actual part.”
DNV GL’s experts laid emphasis on the important costs production required to utilize AM in the maritime industry, as compared to well established manufacturing processes such as rolling, casting and forging.
The aviation and automobile industries for instance, mainly deal with closed circle production (mass production) which includes the use of thin materials such as aluminum and titanium while “customized parts made of thick steel with big dimensions are more typical in the maritime industry”.
This question of price had already been raised in a former conversation we had with voestalpine Additive Manufacturing’s Managing Director.
For Armin Wiedenegger, the Managing Director (MD) of the 3D Printing Research and Production group voestalpine Additive Manufacturing Center GmbH, the oil & gas industry has its own guidelines. Quality assurance for the manufacturing of components is not the same than in other industries. The continuous search for lightweight parts that we observe in aerospace and automotive applications for example, cannot be applied in the oil & gas industry. The main challenge here is to produce parts cheaper & faster than with conventionally process routes.
Parts manufacturing in the oil & gas industry
Hundreds of intricate parts are regularly used by professionals of this area of activity. They include for instance, turbine plates, turbo-expanders as well as compressor parts such as pistons, rings, valve seats, seals or cylinder side plates.
Our research shows that most manufacturers of parts for this segment see a demand for components made from very large forgings up to five feet in diameter and weighing nearly 4,000 lbs., and with machining tolerances within .005 required. However, 2019 saw the return of more autonomy to Oil-production parts, that’s why companies are increasingly looking for production applications which include fabrication of spare parts on site, testing new product designs, and simplifying inventory management to save costs; demands that are usually met by 3D Printing technologies.
“With oil and gas assets being deployed in increasingly isolated regions for longer durations, there is a correspondingly larger likelihood of essential parts breaking down, becoming obsolete due to technological changes or changes to standards or going out of production before the asset is decommissioned. The small numbers and short life-cycles of these parts relative to the component present a unique challenge in inventory management and further strengthen the case for the deployment of AM. Obsolete parts can be reverse-engineered digitally and additively manufactured on demand, leading to greater asset longevity in cases where the faulty part of a critical component can simply be 3D printed and replaced like-for-like”, Guaranteed’s spokesperson stated.
Furthermore, there might be a need for more automation in parts production, but it should be noted that companies cannot decide on their own of the parts they can produce via AM, given the screening of components in facilities and the stringent testing and certification requirements, they need to meet. For Guaranteed, companies that are exploring the opportunity of AM in the Oil & Gas industry should also take into account other advantages.
“We therefore believe that on short term, the opportunity in the oil and gas industry is not just in parts production, but also in the products that support oil and gas operations, which have lower critical importance, and hence lower quality requirements.
Product groups that hold promises for large scale application of AM for components are for instance valves, piping systems, hydraulic systems, nozzles and tooling. Various downhole and topside components have also indicated to show possibilities and benefits for using AM”, our experts point out.
Technology & materials
A wide range of manufacturing methods within the AM landscape can be deployed, depending on the technical requirements of the components and the environment in which they operate.
Until the recent years, polymer 3D Printing was predominantly used in additive productions for the MOG industry. However, the launch of the JIP by DNV GL has publicized the use of metal additive manufacturing technologies in this segment.
As a reminder, the scope of the project was to provide a framework to ensure that metal parts produced via SLM technology and wire arc additive manufacturing meet the oil, gas, and maritime industry specifications.
As far as materials are concerned, experts at Guaranteed told 3D ADEPT Media that candidate materials for AM applications in the oil & gas industry should meet four main criteria:
- “high strength and ductility within a broad range of operating temperatures (from cryogenic up to 400°C) to withstand the working conditions
- corrosion resistance induced by the presence of water, C02 and/or H2S
- chloride induced pitting resistance
- economic sourcing possibility (availability within short time and limited cost)”
That is why, duplex stainless steel or nickel-based alloys such as Inconel 718 are usually a great fit for applications in this field.
What’s next in the pipeline for oil, gas and maritime companies?
At the manufacturing level, AM is proving its essential role as an enabler of several new applications and opportunities in the Oil, Gas & Maritime industries. However, given the stringent requirements to meet, it takes time to make the use of 3D Printed parts effective.
“In the maritime industry, material manufacturers for significant components must first be approved by a Classification society like DNV GL. DNV GL has developed an approval programme – DNVGL-CP-0267 – specifically for Additive Manufacturing as well as DNVGL-CP-0291 for Feedstock Approval. The first manufacturer for Additive Manufacturing was approved in 2019. For critical components, the maritime industry requires a sacrificial test coupon for each batch. DNV GL rules and offshore standards have been revised, too, to accept Additive Manufacturing as a manufacturing method similar to rolling, casting and forging”, DNV GL’s experts said.
Even though these sectors are set to become one of the major adopters of additive manufacturing, the current environment is subjected to volatility. In fact, volatility has always been a challenging element of the oil and gas market but it has rarely been more extreme than it is today. Disruptions in demands, due to the pandemic, as well as the impact on financial markets have led to rapid price swings.
It’s hard to tell now what will be the impact in the additive manufacturing market, however one thing is certain, the complex environmental norms, volatile oil prices and growing competition will make oil and gas companies to consider AM to achieve operational efficiency.
Notable applications of Additive Manufacturing in the Oil, Gas & Maritime industries
As mentioned before, several applications can highlight the possibilities of AM in the MOG industry. We have considered the fact that the ever-growing sector of the Maritime, Oil and Gas (MOG) industry includes drilling rigs, refineries and supertankers both on- and offshore. The maritime industry especially, which should not be confused with marine applications, includes for instance, shipping companies, ships manufacturing, and port authorities.
While many agreements are still in progress, a small number of applications have already been highlighted by companies of the industry. The lines below describe the latest highlights in 2019 that are worth mentioning in terms of applications.
The maritime industry
As far as participating companies to this dossier are concerned, it should be noted that DNV GL has joined other development projects in Korea with KOSWIRE; projects that involve feedstock approval and that are carried out in collaboration with SY Metal Co and HHI, the ultimate goal being to develop a ship propeller.
“Conventional production requires high effort and cost for preparation, manufacturing and shipping of the replacement propeller. Furthermore, the ship is subject to an enforced lay time. Producing the propeller by Additive Manufacturing reduces the lead time significantly. Another appealing asset is to unlock new design opportunities, e.g. combine a convenient steel with good structural properties and geometry in any order, with an expensive corrosion-resistant steel”, said DNV GL.
“Furthermore, we are working with SHI, INSSTEK, KOSWIRE, PK VALVE, KIMS and KAERI to manufacture a cryogenic valve. In the Netherlands, a project is ongoing to develop an offshore crane hook with Huisman and Ramlab. In Germany, DNV GL is participating in the Maritime Network for 3D printing (MN3D network consortium). More projects with reputable stakeholders in the maritime industry are under negotiation”, Ramesh Babu Govindaraj and Eva Junghans added, speaking of DNV GL’s current projects in the maritime industry.
In 2018, French defense contractor Naval Group and French engineering school Centrale Nantes worked together on the development of a 3D Printed military propeller. Last year, that same collaboration resulted in the world’s first 3D printed hollow propeller blade.
Funded by the European Commission, as part of the European H2020 project, the goal of the project was to leverage new technologies such as AM to decrease the environmental footprint in the manufacturing of large naval vessels.
As DNV GL’s experts explains, “additive manufacturing helps to scale down carbon emissions by reducing the amount of raw material – and material which is discarded in the manufacturing process – and by shortening transportation journeys.”
Using Wire Arc for Additive Manufacturing (WAAM), 3D Printed steel propellers with six meters in diameter, but they produced a porotype at one-third scale. With approximately 300kg, the blade required less than 100 hours of print time.
According to the team of the project, AM of the blades at full scale led to a wight reduction of 40%, which means less material and less load on the engines. The new production further reduces fuel consumption, therefore, the environmental impact on the ship. Furthermore, an improved blade design results in further efficiency and durability while reducing radiated noise and vibrations that have negative effects on marine animals.
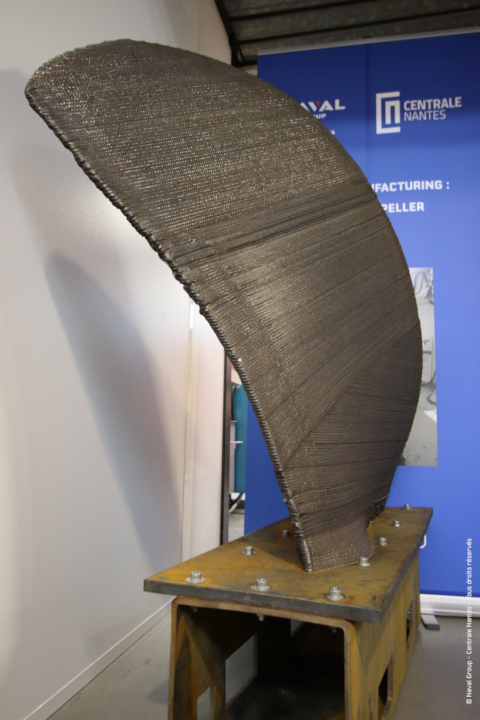
The Oil & Gas industry
In the Oil & Gas industry, apart from the partnerships that are currently in progress, the first metal 3D printed part was approved for shipboard installation in 2018.
Approved by the Naval Sea Systems Command (NAVSEA), the part is a prototype drain strainer orifice (DSO) assembly that was installed in 2019 for 12 months on USS Harry S. Truman (CVN 75). A number of tests had been carried out prior to the evaluation trial in 2019, and during the evaluation trial on the shipboard, the DSO assembly would have allowed drainage/removal of water from a steam line while in use.
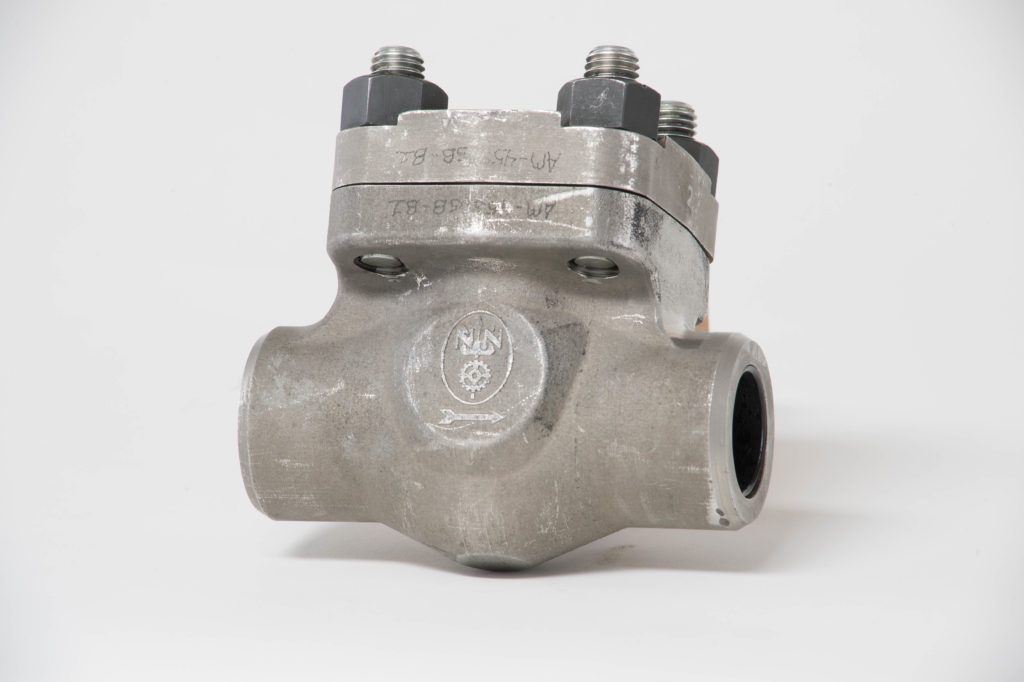
At Guaranteed, earlier this year, the Belgian company has commissioned the first of two production lines.
“On these lines, metal parts from heavy industry, oil & gas, offshore, shipping, … are repaired or produced with WAAM technology. The Guaranteed production cell can process workpieces up to ten by six by five meters, with a maximum weight of 20 tons. Currently the material database is already well populated (steel, stainless, Inconel, Titanium, aluminum, bronze, …), but can easily be expanded at the request of customers. With its dual value proposition, Guaranteed offers potential customers the opportunity to either directly save costs by repairing parts or to realize logistical cost savings by producing complete replacement parts on demand and quickly. To enable and support this, Guaranteed is actively involved in several Joint Industry Projects managed by DNV to facilitate the uptake of AM in sectors such as oil & gas where certification is important”, Joachim Antonissen and Sander Plasschaert said, speaking of their current projects.
Concluding thoughts
To conclude, additive manufacturing in the Oil, Gas & Maritime industries is still nascent. Even though technology promises a lot of advantages, yet remains quite expensive in terms of applications. Companies that debut on this segment should focus on advantages that are not provided by conventional manufacturing processes such as: production of spare parts, production on site, freedom of design and an environmental-friendly approach due to reduction of carbon emissions.
This dossier has first been published in the July-August Issue of 3D ADEPT Mag.
Featured image: Siemens. Remember, you can post job opportunities in the AM Industry on 3D ADEPT Media free of charge or look for a job via our job board. Make sure to follow us on our social networks and subscribe to our weekly newsletter : Facebook, Twitter, LinkedIn & Instagram ! If you want to be featured in the next issue of our digital magazine or if you hear a story that needs to be heard, make sure to send it to contact@3dadept.com