Les professionnels des industries maritime, pétrolière et gazière (MOG – Maritime, Oil & Gas) prennent des risques importants pour obtenir de précieuses opportunités au niveau international. Certains de ces risques impliquent l’adoption de nouvelles réglementations et lois, le changement climatique, ainsi que la production de pièces, d’où l’importance d’une surveillance continue sur un certain nombre d’opérations quotidiennes.
En ce qui concerne la production de composants, le réseau global de DNV GL, spécialisé dans l’investigation des défaillances, a réalisé un rapport qui a révélé que les tubes et les conduites sont les composants les plus sujets aux défaillances dans les industries MOG ; la fatigue et la corrosion étant les types de défaillance les plus courants.
La recherche s’est basée sur plus de 1 000 cas de défaillance étudiés aux États-Unis, en Europe et en Asie.
« Le coût de la prévention, de la surveillance, de la réparation ou du remplacement à la suite de ces formes de dégradation des composants peut se chiffrer en milliards de dollars. Potentiellement, des pénalités financières peuvent se produire si des incidents majeurs et des pertes de vies humaines résultent d’une telle défaillance », a expliqué Koheila Molazemi, directeur de la technologie et de l’innovation, DNV GL – Oil & Gas.
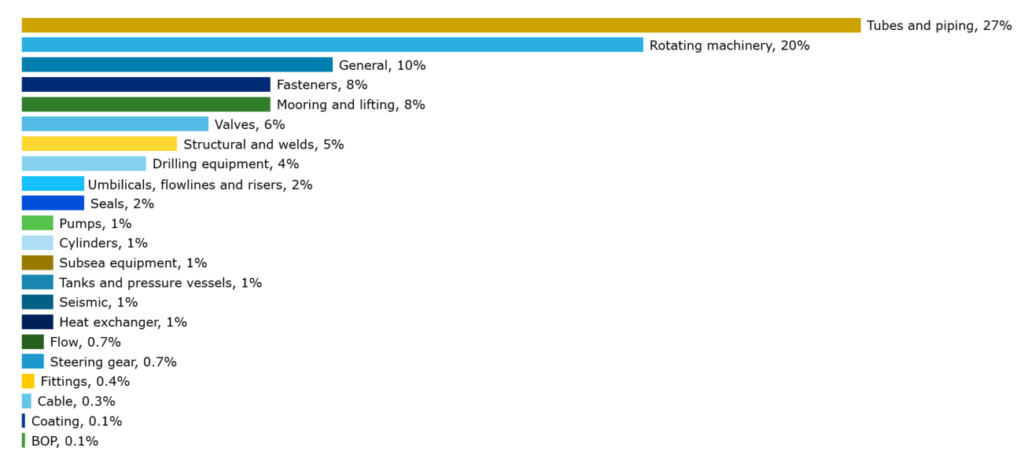
Pour éviter ou minimiser ces types de défaillance courants, les professionnels ont envisagé des solutions numériques et des technologies de fabrication numérique qui offrent une meilleure durabilité. L’une de ces technologies est la fabrication additive. Cependant, alors que la fabrication additive a été largement adoptée dans les secteurs de l’aérospatiale, de l’automobile et de la médecine, les industries MOG restent un adoptant naissant de cette technologie.
Cet article vise à mettre en évidence les principales caractéristiques et opportunités commerciales à prendre en compte lors de l’étude de la FA dans ce secteur d’activité.
Pour aborder ce sujet, nous avons fait appel à l’expertise de deux entreprises :
– DNV GL, une société de classification et d’enregistrement accréditée au niveau international qui fournit des services à plusieurs secteurs, notamment le secteur maritime, les énergies renouvelables, le pétrole et le gaz, l’électrification, l’alimentation et les boissons et les soins de santé.
– Guaranteed, une société dérivée de Finindus, ArcelorMittal Belgium et OCAS, qui vise à assurer la production de pièces de première main et à offrir à ses clients un guichet unique fiable. La société utilise un logiciel de contrôle des processus unique qui permet de réduire considérablement le nombre de boucles d’essai et d’erreur coûteuses.
Ramesh Babu Govindaraj, Spécialiste principal maritime pour la fabrication de matériaux, de soudures et de la FA et Eva Junghans, Ingénieur principal maritime pour les matériaux et les soudures ont répondu à nos questions dans l’équipe de DNV GL. Les deux collègues donnent de plus amples informations sur l’utilisation de la FA dans l’industrie maritime.
Joachim Antonissen et Sander Plasschaert ont répondu à nos questions concernant l’utilisation de la FA dans les industries pétrolières et gazières.
Anticiper les risques dans les secteurs pétrolier, gazier et maritime
Le dernier rapport de SmarTech Publishing sur la fabrication additive pour le secteur pétrolier et gazier prévoit que ce secteur générera 2 milliards de dollars (USD) de revenus d’ici 2027. Cet avenir semble encore plus prometteur pour l’industrie de l’impression 3D, car selon Research and Markets, l’utilisation de l’impression 3D dans le secteur du pétrole et du gaz est estimée à 32 milliards de dollars d’ici 2025.
Sur la base des expériences en matière de prototypage rapide et d’outillage dans d’autres industries, plusieurs opérateurs et fournisseurs du secteur pétrolier et gazier ambitionnent maintenant d’utiliser la fabrication additive pour obtenir un avantage concurrentiel clé dans la production de pièces finales avancées et complexes.
DNV GL est l’une des entreprises qui a très tôt anticipé cette croissance mais aussi les défis et les risques auxquels seraient confrontés les adeptes de la FA dans ce secteur. C’est pourquoi, en 2017, elle a publié un guide de classification pour l’utilisation de la fabrication additive (FA) dans les industries maritime, pétrolière et gazière.
Pour les fabricants, les sous-fournisseurs de matériaux, pièces et composants, les fournisseurs de services et les utilisateurs finaux qui adoptent les technologies de la FA, cette ligne directrice servira d’outil qui garantira que les pièces ou composants créés par un processus de FA et les matériaux à partir desquels ils sont créés ont le même niveau d’assurance qualité que les produits fabriqués de manière traditionnelle.
Il y a deux ans, un consortium pétrolier et gazier a lancé deux projets d’innovation conjoints (JIP – Joint Innovation Projects) qui visaient à définir une ligne directrice et un modèle commercial pour l’utilisation de la FA dans les industries pétrolière, gazière et maritime. 11 entreprises ont lancé le projet en 2018 et ont été rejointes par 9 autres entreprises à la fin de 2019.
« L’approche du programme JIP DNVGL était basée sur l’atelier FMEA (Failure Mode and Effects Analysis) qui a été suivi par tous les participants. Le processus d’atténuation des défaillances y a été établi et les essais pour capturer la zone la plus faible dans les applications ont été considérés.
Dans le cadre de ce projet, les opérateurs sont les utilisateurs finaux et répondent à leurs attentes en matière de qualité, de fonctionnalité et de durabilité des services pour leurs actifs.
Les entrepreneurs réalisent la conception, spécifient les exigences détaillées des composants et optimisent la conception pour tirer pleinement parti de la FA.
Les fabricants fournissent des informations relatives au processus d’impression et établissent les variables essentielles qui sont importantes pour obtenir des propriétés matérielles répondant aux exigences » ont commenté Ramesh Babu Govindaraj & Eva Junghans.
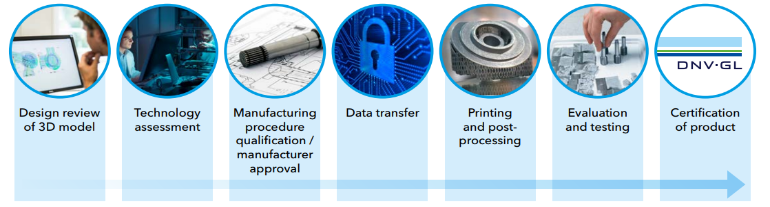
L’achèvement de ces projets a conduit à des applications tangibles de la FA dans ce segment et à une meilleure compréhension des défis qu’un fabricant peut rencontrer pour produire une pièce imprimée en 3D pour ce segment. Nous avons demandé à Guaranteed, l’une des entreprises impliquées dans ces projets, quels peuvent être ces défis et en quoi le processus de fabrication est différent de ce que les opérateurs ont l’habitude de voir avec les processus de fabrication conventionnels.
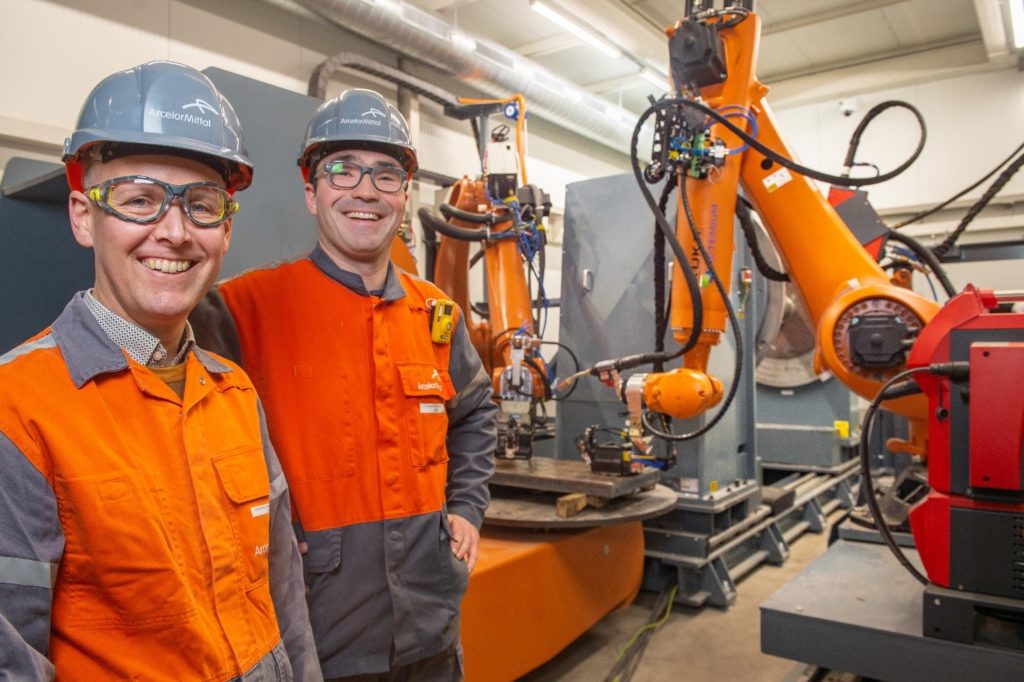
Joachim Antonissen et Sander Plasschaert ont expliqué que les industries pétrolière et gazière utilisent souvent des composants moulés ou forgés en alliages spéciaux assez coûteux comme l’Inconel. D’une part, le processus de forgeage lui-même entraîne un important gaspillage de matériaux, tout en étant caractérisé par des délais d’exécution prolongés et des taux de défaillance non négligeables qui peuvent avoir un impact sur les opérations futures. Bien que cela souligne clairement l’opportunité de la FA dans le secteur, les conditions d’exploitation sévères exigent un cadre d’assurance qualité clair, tout en imposant souvent des composants de grande taille et lourds.
« En même temps que la technologie passe du laboratoire à la fabrication, l’analyse de rentabilité doit vraiment être présente pour que l’industrie adopte la FA. La combinaison de la taille des composants et de la complexité fonctionnelle fait de la technologie DED un argument convaincant en faveur des procédés à base de fil, comme le procédé WAAM proposé par Guaranteed B.V., car il permet de produire des pièces de plusieurs mètres en quelques heures à un coût compétitif. Le large choix de matériaux disponibles pour les fils, dont le coût est considérablement inférieur à celui de leurs homologues en poudre, combiné au fait que des pièces denses à quasi 100% sont produites, sans qu’il soit nécessaire de les hacher, contribue encore à l’attrait économique de cette technologie pour ce segment. Comme la technologie WAAM permet en outre de déposer sur un composant existant (par exemple, une plaque ou un cylindre) ou même de réparer une pièce existante, l’analyse de rentabilité peut être améliorée même sans tenir compte des économies logistiques telles que la réduction des délais ou des coûts de stockage. Outre les avantages économiques qui en résultent, la réparation localisée ou la production à la demande de formes proches de la forme nette contribue également à la durabilité car elle réduit considérablement le besoin de matières premières et de logistique de transport.
En même temps, les exigences strictes de certification imposées par les conditions d’exploitation sévères de l’industrie pétrolière et gazière doivent également être prises en compte lors de l’évaluation du dossier commercial. Selon le niveau de criticité du composant, la certification peut imposer la production d’une quantité importante d’échantillons de test destructifs en plus de la pièce elle-même. »
Les experts de DNV GL ont mis l’accent sur les coûts de production importants requis pour utiliser la FA dans l’industrie maritime, par rapport à des procédés de fabrication bien établis tels que le laminage, le moulage et le forgeage.
Les industries aéronautique et automobile, par exemple, s’occupent principalement de la production en cercle fermé (production de masse) qui comprend l’utilisation de matériaux minces tels que l’aluminium et le titane, tandis que « les pièces sur mesure en acier épais de grandes dimensions sont plus typiques de l’industrie maritime ».
Cette question du prix avait déjà été soulevée lors d’une précédente conversation que nous avions eue avec le directeur général de voestalpine Additive Manufacturing.
Pour Armin Wiedenegger, le directeur général (MD) du groupe de recherche et de production voestalpine Additive Manufacturing Center GmbH, les industries pétrolière et gazière ont leurs propres codes. L’assurance qualité pour la fabrication des composants n’est pas la même que dans d’autres industries. La recherche continue de pièces légères que nous observons dans les applications aérospatiales et automobiles par exemple, ne peut pas être appliquée dans l’industrie pétrolière et gazière. Le principal défi consiste à produire des pièces moins chères et plus rapidement qu’avec les procédés traditionnels.
Fabrication de pièces détachées dans l’industrie pétrolière et gazière
Des centaines de pièces complexes sont régulièrement utilisées par les professionnels de ce domaine d’activité. Il s’agit par exemple de plaques de turbine, de turbo-détendeurs ainsi que de pièces de compresseur telles que des pistons, des segments, des sièges de soupape, des joints ou des plaques latérales de cylindre.
Nos recherches montrent que la plupart des fabricants de pièces pour ce segment voient une demande de composants fabriqués à partir de très grandes pièces forgées pouvant atteindre cinq pieds de diamètre et pesant près de 4 000 livres, et dont les tolérances d’usinage sont inférieures à 0,005. Cependant, 2019 a vu le retour d’une plus grande autonomie pour les pièces de production de pétrole, c’est pourquoi les entreprises recherchent de plus en plus des applications de production qui incluent la fabrication de pièces de rechange sur place, l’essai de nouveaux designs de produits et la simplification de la gestion des stocks pour réduire les coûts ; des demandes qui sont généralement satisfaites par les technologies d’impression 3D.
« Les ressources pétrolières et gazières étant déployées dans des régions de plus en plus isolées pendant de plus longues périodes, la probabilité que des pièces essentielles tombent en panne, deviennent obsolètes en raison de changements technologiques ou de modifications des normes, ou cessent d’être produites avant que la ressource ne soit mise hors service est donc plus grande. Le petit nombre et la courte durée de vie de ces pièces par rapport au composant présentent un défi unique en matière de gestion des stocks et renforcent encore les arguments en faveur du déploiement de la FA. Les pièces obsolètes peuvent faire l’objet d’une rétro-ingénierie numérique et être fabriquées de manière additive à la demande, ce qui permet d’augmenter la longévité des actifs dans les cas où la partie défectueuse d’un composant critique peut simplement être imprimée en 3D et remplacée comme si elle était identique », a déclaré le porte-parole de Guaranteed.
En outre, il pourrait être nécessaire d’automatiser davantage la production de pièces, mais il convient de noter que les entreprises ne peuvent pas décider seules des pièces qu’elles peuvent produire par FA, étant donné le contrôle des composants dans les installations et les exigences strictes de test et de certification auxquelles elles doivent satisfaire. Pour Guaranteed, les entreprises qui explorent les possibilités de la FA dans les industries du pétrole et du gaz doivent également tenir compte d’autres avantages.
« Nous pensons donc qu’à court terme, l’opportunité dans les industries pétrolière et gazière ne réside pas seulement dans la production de pièces, mais aussi dans les produits qui soutiennent les opérations pétrolières et gazières, qui ont une importance critique moindre, et donc des exigences de qualité moins élevées.
Les groupes de produits qui promettent une application à grande échelle de la FA pour les composants sont par exemple les valves, les systèmes de tuyauterie, les systèmes hydrauliques, les buses et l’outillage. Divers composants de fond de puits et de surface ont également été indiqués pour montrer les possibilités et les avantages de l’utilisation de la FA », soulignent nos experts.
Technologie et matériaux
Un large éventail de méthodes de fabrication peut être déployé dans le paysage de la FA, en fonction des exigences techniques des composants et de l’environnement dans lequel ils fonctionnent.
Jusqu’à ces dernières années, l’impression 3D polymère était principalement utilisée dans les productions additives pour les industries MOG. Cependant, le lancement des JIPs par DNV GL a fait davantage connaître l’utilisation des technologies de fabrication additive métallique dans ce segment.
Pour rappel, la portée du projet était de fournir un cadre permettant de s’assurer que les pièces métalliques produites par la technologie SLM et la fabrication additive à l’arc métallique répondent aux spécifications de l’industrie pétrolière, gazière et maritime.
En ce qui concerne les matériaux, les experts de Guaranteed ont déclaré à 3D ADEPT Media que les matériaux candidats pour les applications de FA dans les industries pétrolière et gazière devaient répondre à quatre critères principaux :
« – Une résistance et une ductilité élevées dans une large gamme de températures de fonctionnement (de la cryogénie jusqu’à 400°C) pour résister aux conditions de travail
- La résistance à la corrosion induite par la présence d’eau, de C02 et/ou de H2S
- Résistance à la piqûre induite par le chlorure
- Possibilité d’approvisionnement économique (disponibilité dans des délais courts et coût limité) ».
C’est pourquoi l’acier inoxydable duplex ou les alliages à base de nickel tels que l’Inconel 718 conviennent généralement parfaitement aux applications dans ce domaine.
Quelle est la prochaine étape pour les compagnies pétrolières, gazières et maritimes ?
Au niveau de la fabrication, la FA prouve son rôle essentiel en tant que catalyseur de plusieurs nouvelles applications et opportunités dans les industries MOG. Cependant, étant donné les exigences strictes à respecter, il faut du temps pour rendre efficace l’utilisation des pièces imprimées en 3D.
« Dans l’industrie maritime, les fabricants de matériaux pour les composants importants doivent d’abord être approuvés par une société de classification comme DNV GL. DNV GL a développé un programme d’approbation – DNVGL-CP-0267 – spécifiquement pour la fabrication additive ainsi que DNVGL-CP-0291 pour l’approbation des matières premières. Le premier fabricant pour la fabrication additive a été approuvé en 2019. Pour les composants critiques, l’industrie maritime exige un coupon test sacrificiel pour chaque lot. Les règles de DNV GL et les normes offshores ont également été révisées pour accepter la fabrication additive comme une méthode de fabrication similaire au laminage, au moulage et au forgeage », ont déclaré les experts de DNV GL.
Même si ces secteurs sont en passe de devenir l’un des principaux adoptants de la FA, l’environnement actuel est soumis à une certaine volatilité. En fait, la volatilité a toujours été un élément de défi pour le marché du pétrole et du gaz, mais elle a rarement été plus extrême qu’aujourd’hui. Les perturbations de la demande, dues à la pandémie, ainsi que l’impact sur les marchés financiers ont entraîné des fluctuations rapides des prix.
Il est difficile de dire aujourd’hui quel sera l’impact sur le marché de la FA, mais une chose est sûre, les normes environnementales complexes, la volatilité des prix du pétrole et la concurrence croissante inciteront les compagnies pétrolières et gazières à envisager la FA pour atteindre l’efficacité opérationnelle.
Applications notables de la fabrication additive dans les industries pétrolière, gazière et maritime
Comme mentionné précédemment, plusieurs applications peuvent mettre en évidence les possibilités de la FA dans les industries MOG. Nous avons tenu compte du fait que ce secteur en pleine croissance comprend les plateformes de forage, les raffineries et les superpétroliers, tant sur terre qu’en mer. L’industrie maritime en particulier, qu’il ne faut pas confondre avec les applications maritimes, comprend par exemple les compagnies de navigation, la construction navale et les autorités portuaires.
Si de nombreux accords sont encore en cours, un petit nombre d’applications ont déjà été mises en évidence par les entreprises du secteur. Les lignes ci-dessous décrivent les derniers faits marquants en 2019 qui méritent d’être mentionnés en termes d’applications.
L’industrie maritime
En ce qui concerne les entreprises participant à ce dossier, il convient de noter que DNV GL a rejoint d’autres projets de développement en Corée avec KOSWIRE ; des projets qui impliquent l’approbation des matières premières et qui sont réalisés en collaboration avec SY Metal Co et HHI, le but ultime étant de développer une hélice de navire.
« La production conventionnelle nécessite des efforts et des coûts élevés pour la préparation, la fabrication et l’expédition de l’hélice de remplacement. De plus, le navire est soumis à un temps de pose obligatoire. La production de l’hélice par fabrication additive réduit considérablement le délai de fabrication. Un autre atout attrayant est de libérer de nouvelles opportunités de conception, par exemple en combinant un acier pratique avec de bonnes propriétés structurelles et géométriques dans n’importe quel ordre, avec un acier coûteux résistant à la corrosion », a déclaré DNV GL.
« De plus, nous travaillons avec SHI, INSSTEK, KOSWIRE, PK VALVE, KIMS et KAERI pour fabriquer une vanne cryogénique. Aux Pays-Bas, un projet est en cours pour développer un crochet de grue offshore avec Huisman et Ramlab. En Allemagne, DNV GL participe au réseau maritime pour l’impression 3D (consortium du réseau MN3D). D’autres projets avec des acteurs réputés de l’industrie maritime sont en cours de négociation », ont ajouté Ramesh Babu Govindaraj et Eva Junghans, en parlant des projets actuels de DNV GL dans l’industrie maritime.
En 2018, le groupe naval, entrepreneur de défense français, et l’école d’ingénieurs française Centrale Nantes ont travaillé ensemble sur le développement d’une hélice militaire imprimée en 3D. L’année dernière, cette même collaboration a abouti à la première pale d’hélice creuse imprimée en 3D au monde.
Financé par la Commission européenne, dans le cadre du projet européen H2020, l’objectif du projet était de tirer parti de nouvelles technologies telles que la FA pour réduire l’empreinte environnementale dans la fabrication de grands navires militaires.
Comme l’expliquent les experts de DNV GL, « la fabrication additive permet de réduire les émissions de carbone en diminuant la quantité de matières premières – et de matériaux qui sont rejetés dans le processus de fabrication – et en raccourcissant les trajets de transport. »
En utilisant le Wire Arc for Additive Manufacturing (WAAM), les équipes ont produit des hélices en acier imprimées en 3D de six mètres de diamètre, mais elles ont produit un prototype à l’échelle d’un tiers. Avec environ 300 kg, la pale a nécessité moins de 100 heures d’impression.
Selon l’équipe du projet, la FA des hélices à pleine échelle a permis de réduire le poids de 40%, ce qui signifie moins de matériau et moins de charge sur les moteurs. La nouvelle production réduit encore la consommation de carburant, donc l’impact environnemental sur le navire. En outre, une meilleure conception des hélices permet d’accroître l’efficacité et la durabilité tout en réduisant le bruit et les vibrations qui ont des effets négatifs sur les animaux marins.
L’industrie du pétrole et du gaz
Dans le secteur du pétrole et du gaz, outre les partenariats en cours, la première pièce métallique imprimée en 3D a été approuvée pour être installée à bord des navires en 2018.
Approuvée par le Naval Sea Systems Command (NAVSEA), cette pièce est un prototype d’orifice de crépine de vidange (DSO) qui a été installé en 2019 pour 12 mois sur l’USS Harry S. Truman (CVN 75). Un certain nombre de tests avaient été effectués avant l’essai d’évaluation en 2019, et pendant l’essai d’évaluation à bord du navire, l’ensemble DSO aurait permis de vidanger/éliminer l’eau d’une conduite de vapeur pendant son utilisation.
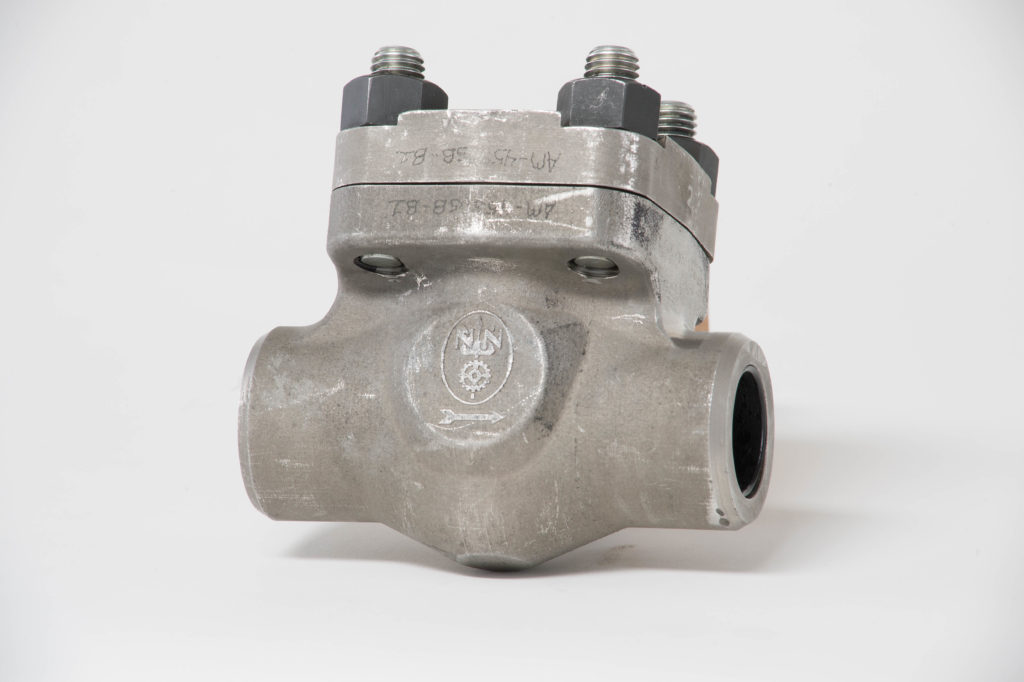
Chez Guaranteed, au début de l’année, la société belge a mis en service la première de deux lignes de production.
« Sur ces lignes, des pièces métalliques provenant de l’industrie lourde, du pétrole et du gaz, de l’offshore, de la navigation, … sont réparées ou produites avec la technologie WAAM. La cellule de production garantie peut traiter des pièces allant jusqu’à dix mètres sur six par cinq, avec un poids maximum de 20 tonnes. Actuellement, la base de données des matériaux est déjà bien remplie (acier, inox, Inconel, Titane, aluminium, bronze, …), mais peut facilement être élargie à la demande des clients. Grâce à sa double proposition de valeur, Guaranteed offre aux clients la possibilité de réaliser des économies directes en réparant les pièces, soit de réaliser des économies logistiques en produisant des pièces de rechange complètes à la demande et rapidement. Pour permettre et soutenir cela, Guaranteed est activement impliqué dans plusieurs projets industriels conjoints gérés par DNV GL pour faciliter l’adoption de la FA dans des secteurs tels que le pétrole et le gaz où la certification est importante », ont déclaré Joachim Antonissen et Sander Plasschaert, en parlant de leurs projets actuels.
Conclusion
Pour conclure, la fabrication additive dans les industries pétrolière, gazière et maritime est encore naissante. Même si la technologie promet de nombreux avantages, elle reste assez coûteuse en termes d’applications. Les entreprises qui débutent sur ce segment devraient se concentrer sur les avantages qui ne sont pas fournis par les procédés de fabrication conventionnels, tels que : la production de pièces de rechange, la production sur site, la liberté de conception et une approche respectueuse de l’environnement grâce à la réduction des émissions de carbone.
Ce dossier a été initialement publié dans le numéro Juillet-Aoüt 2020 de 3D ADEPT Mag.
N’oubliez pas que vous pouvez poster gratuitement les offres d’emploi de l’industrie de la FA sur 3D ADEPT Media ou rechercher un emploi via notre tableau d’offres d’emploi. N’hésitez pas à nous suivre sur nos réseaux sociaux et à vous inscrire à notre newsletter hebdomadaire : Facebook, Twitter, LinkedIn & Instagram ! Si vous avez une innovation à partager pour le prochain numéro de notre magazine numérique ou si vous avez un article à faire connaître, n’hésitez pas à nous envoyer un email à contact@3dadept.com.