Although dentistry has long time been associated with subtractive manufacturing – milling especially – , a report from market intelligence firm CONTEXT reveals that this field makes up over one fifth of the end market for professional polymer 3D printers (5,000 USD upwards). Despite the significant improvements made to advance the use of AM within this field, some technological and cost impediments still raise a number of questions among experts. This feature will discuss these advancements and the improvements that still need to be made to enable a wider adoption of AM technologies in the field. To discuss this issue, Stijn Hannsen – Sales, Marketing & Applications Manager at 3D Systems and Mayra Vasques, founder of Innov3D have been invited to share their insights into the topic. Hanssen will share the point of view of a 3D printer manufacturer whereas Dr. Vasques will bring the user’s perspective on the table.
No exact figures reveal the number of dentists and dental technicians who are well acquainted with digital manufacturing technologies. Nevertheless, over the past decade, developments in computer technology and software applications have facilitated the adoption of 3D printing.
With a dental 3D printing market poised to reach 9.5 billion USD by 2027, it is easy to understand the increasing investments in the development of dental 3D printers from manufacturers and the willingness of clinics to improve the way they provide care. Despite the options they have, the choice of manufacturing tools may vary from one clinician to another.
Main manufacturing tools used in a dental lab
From a technological perspective, the use of digital manufacturing technologies in dental labs started by the adoption of a dental 3D scanner to provide an accurate 3D model. As you may know, 3D printers are nothing without a computer-aided design (CAD) software, but all clinicians do not always have the required knowledge to virtually design a model. Today, several routes are offered to surgeons and dentists who have ready access to volumetric data in the form of computed tomography (CT) data, cone beam computed tomography (CBCT) data, and intraoral or laboratory optical surface scan data. On the other hand, with the number of affordable dental 3D printers that are popping up, manufacturers increasingly develop more user-friendly software to support these users, thus questioning the role of a dental 3D scanner in the dental lab. According to Hanssen:
“dentistry is going through fundamental changes, starting with analogy and moving towards digital workflows with digital scanning, design, 3D printing materials. Traditional lines are being blurred in the dental field. We think that most dental care providers will find the use for an intraoral scanner as a more accurate and convenient alternative to analogue impression materials. For the scanning process there are several options depending on the clients’ case; scanning an impression or intra oral scanning. Key is what is done with the scan afterwards. The accuracy in design and in printing is very important for a better patient outcome.”
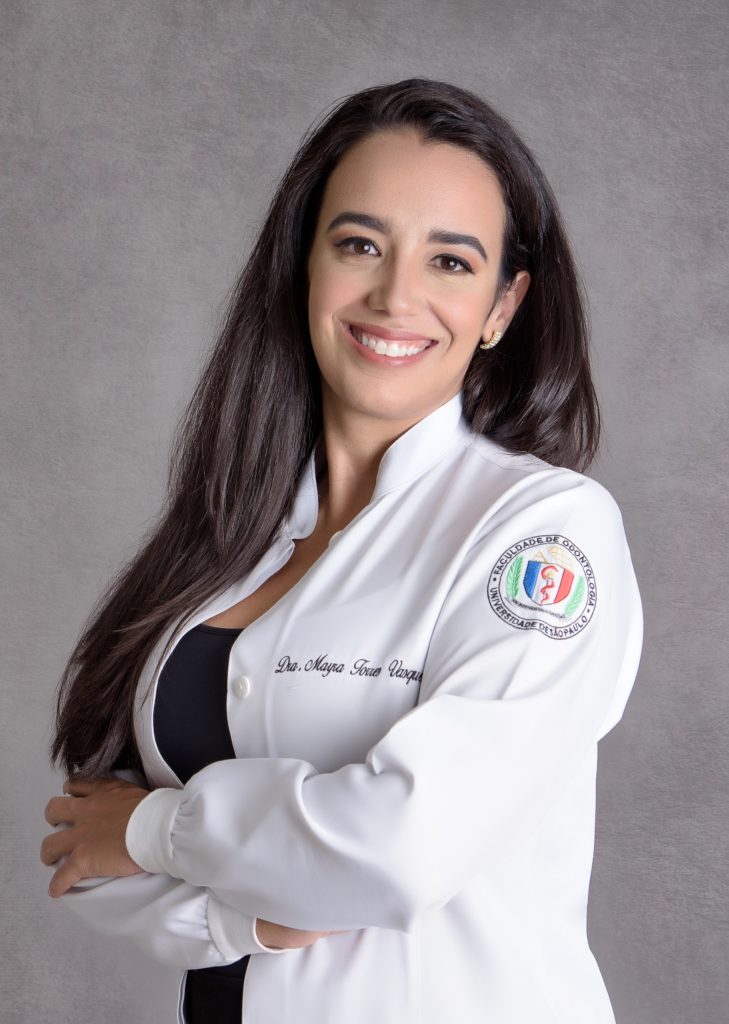
As a user, Vasques believes that a dental 3D scanner continues to have a unique role to play in the digital workflow: “The digital workflow in dentistry consists in 3 steps: data acquisition, design, and manufacture. I´m used to explain this as, first you must transform the real into digital by data acquisition, then you will be able to create your project using the design software and after that you will turn this virtual project into reality using digital manufacturing. Affordable dental 3D printers make it possible to spread this technology in dentistry and improve the in-office 3D printing modality, but they are not a substitute for the 3D scanner, each one belongs to a different part of the process.”
Apart from dental 3D scanners, let’s note that 3D printers have also come a long way. Currently, dental applications and collaborations between companies show a key focus on the use of liquid-based 3D printing technologies such as SLA and DLP. Each of these technologies offers its pros and cons, so the ideal choice often comes down to the taste of the chef in the kitchen. We strongly recommend to have a look at this exclusive article on the secrets of resin 3D printing if you consider buying a resin 3D printer.
In terms of technologies, other professionals often go for photopolymer jetting (PPJ) – another form of resin-based 3D printer -, powder binder printers (PBP) which use a modified inkjet head to print, using what is essentially liquid droplets to infiltrate a layer of powder, layer by layer. Other choices also include SLS and FDM. Metal 3D printers on the other hand, often lack the precision that is required of dental models. Moreover, due to their expensive cost, most clinics do not often consider it as a viable option.
Speaking of the main tools a clinician may use before and after the printing process of a model, Vasques explains:
“The ideal process requires an intraoral scanner to obtain patients digital cast and a resin 3D Printer (SLA or DLP technologies) due to accuracy and the different options of biocompatible resins. To complete the process successfully, it´s necessary to carefully proceed the post processing method washing the printed parts properly and post-curing to reach the best characteristics of the materials.”
Applications and production
Applications in dentistry are extensive. Two of the most common applications of 3D printing in the field are transparent aligners and night guards. Others include but are not limited to crowns and bridges, temporaries, surgical guides, splints, try-In, dentures, and gingiva masks – According to the founder of Innov3D, all these products can be divided into two categories: “The first category comprises products that will be used over a long period of time inside the mouth. They include for instance dental prosthesis, aligners and night guards. The second category comprises products intended for procedures. They include surgical guides and a wide range of other guides such as bio models and customized instruments. There is a lot of room to innovate to create new techniques and new solutions”.
Despite the variety of applications that can be achieved on 3D Systems’ NextDent® 5100, the company’s Applications Manager notes that some 3D printing solutions stand out from the crowd.
“We see a big utilization of 3D printing for temporary or final prosthetics. Dentures have also been an incredible growth market since last year and night guards are gaining popularity.” Moreover, according to the manufacturer, orthodontic tooling models for thermoforming are the applications that require volume production the most. In a more complex environment, it should be noted that one of the earliest applications of 3D printing in surgery – medical modelling – has opened up more possibilities for dentistry in recent years. CBCT (Cone-beam computed tomography systems) has become widely available in dental practices and has revolutionized the way diagnosis and treatment are performed in implant dentistry and endodonctics.
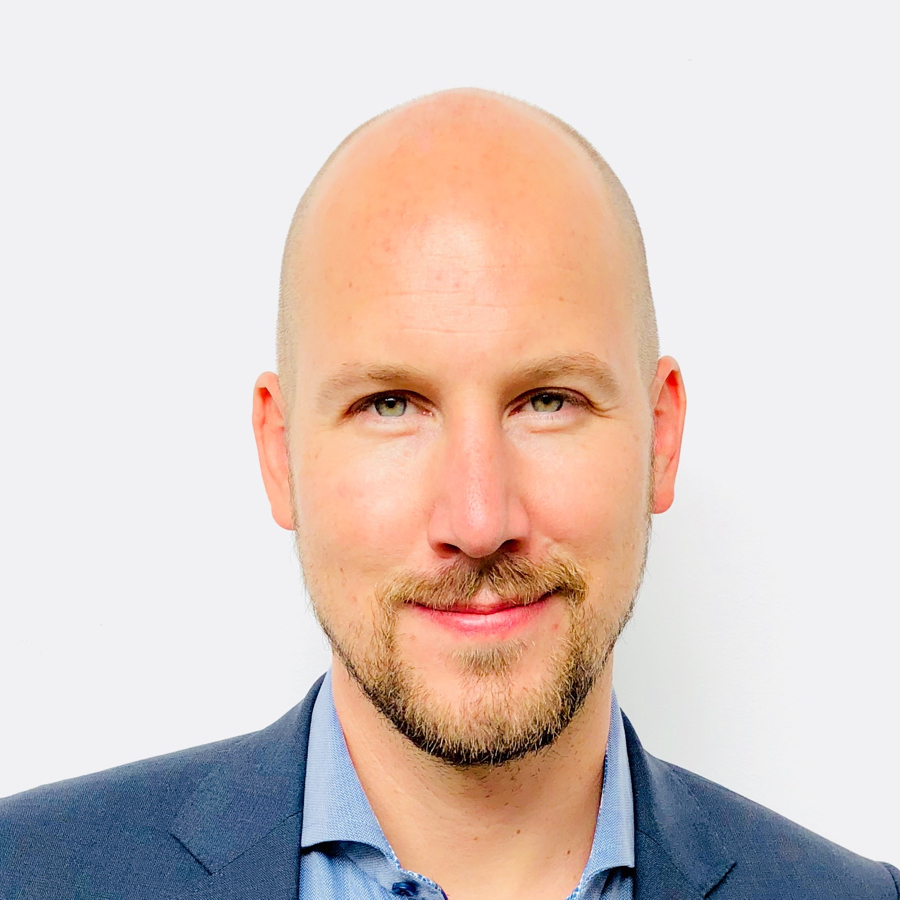
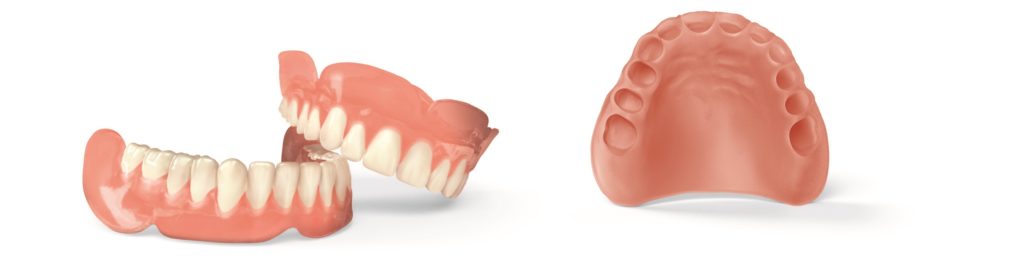
Thanks to CBCT, it is possible to provide volumetric ‘image’ data to a 3D printer before surgery and to make detailed replicas of the patient’s jaws for instance. In a nutshell, this process enables the practitioner to analyse more precisely complex, unusual, or unfamiliar parts of the anatomy, therefore to better prepare prior to the theatre room.
All these applications lay emphasis on the advantages of additive manufacturing (AM) when it comes to customization, and the technology’s ability to meet the same quality and precision seen in other industries. However, even though for now, there are not many applications that require volume production, we couldn’t help but question ourselves if this would not be a challenge in the long-run.
Challenges and future outlooks
Reality shows that it is easy to talk about volume production in other fields of manufacturing. Slowly but surely, the market is growing at its own pace. Therefore, the more the demand will grow, the more dental labs will envision equipping their clinic with a 3D printing farm. In those situations, Vasques believes that manufacturers will need to improve the logistics and equipment so that the clinician spends less time on the floor.
In the meantime, she states that the current area for improvement should be the type and quality of materials for long-term intraoral use. “Dental professionals are more and more open to new technologies, but most of them relate that they are not secure with the longevity and safety of the 3D printed parts”, she adds.
On the other hand, as 3D Systems is working on new materials and 3D printers’ development, Hannsen points out the need for education and training to help advance the utilization of 3D printing among clinicians and dental specialists.
“Dental 3D printing will play an important part in the digital future of dentistry as 3D printing materials will become more advanced and the number of applications will grow. Due to Covid-19, we all aim to assist dental practices to reduce contact with patients. Working with digital patient data helps to reduce patient chair time and improves safety for both patient and practise”, he completes.
Lastly, despite this growing acceptance of digital manufacturing technologies in the field, one notes that the national regulatory bodies have not yet implemented guidance in the use of 3D printing in dentistry. At some stage, regulators will certainly need to set appropriate standards that will facilitate the use of these technologies among specialists.
This exclusive feature has first been published in the 2021 January/February issue of 3D ADEPT Mag.
Remember, you can post job opportunities in the AM Industry on 3D ADEPT Media free of charge or look for a job via our job board. Make sure to follow us on our social networks and subscribe to our weekly newsletter : Facebook, Twitter, LinkedIn & Instagram ! If you want to be featured in the next issue of our digital magazine or if you hear a story that needs to be heard, make sure you send it to contact@3dadept.com