With the contribution of XYZprinting
Apart from FDM and metal 3D Printing technologies, resin 3D Printing remains one of the most widely used techniques for producing high-quality 3D prints. The recent years have seen the development of several types of resin 3D printing technologies as well as the launch of several cheap resin 3D printers raising several questions regarding its value in the professional sphere and the way it should be leveraged. What is really resin 3D printing? When does it make sense to go for a resin 3D printing technology? Is resin eco-friendly or poisonous? – We will address these questions in the following lines. When speaking about resin 3D printing, the first technology that comes to people’s mind is stereolithography and for good reason: the printing process was first invented in the 1980’s. It was one of the first 3D printing technologies that professionals used on the market. A few years later, the other processes, DLP and LCD, emerged and became an additional option in the user portfolio.
In general, resin 3D printing is about converting a liquid plastic into solid objects. However, understanding the principle of SLA helps to understand the main differences between the three processes. So, SLA works by curing resin with light. The light solidifies a liquid resin via a process called photo-polymerization and builds objects layer by layer. A vat or tank contains the resin which is cured against a build platform. It thereafter slowly rises out of the tank as the object is formed. With a digital light processing (DLP) technology on the other hand, a digital light projector cures photo-reactive polymers. Images of whole layers are flashed onto the bottom of the vat. Layers generated using DLP 3D printers are made up of voxels, the 3D equivalent of pixels. Indeed, in this case, the projector screen itself consists of pixels. As for LCD 3D printing, it does not have the reputation of the two others. There is not a big difference between LCD and DLP. This technique also flashes complete layers at the resin tank. However, in this case, the UV light comes from an array of LEDs and no device is required to direct the light as it is with the previous ones.
What to consider when choosing a resin 3d printing technology ?
Among all the additive manufacturing technologies that exist, resin 3D printing is mostly compared to FDM 3D printing. If the first reason that might explain such a comparison is the price of both types of technologies, it should be noted that other characteristics might help tip the balance in favour of one rather than the other. Indeed, the printing process, design considerations, pre-processing, and post-processing are very different.
More importantly, when it comes to compare resin 3D printing technologies to one another and how they achieve the desired accuracy and precision, these features – alongside materials and software settings – also come into play. Indeed, we shouldn’t forget that 3D printing remains an additive process. Therefore, each layer might lead to an opportunity for inaccuracy and the printing process can determine the level of precision of each layer. Accuracy and precision are crucial in some applications like dental or surgical guides and despite the various analyses we could make, reality shows that accuracy and precision are often better portrayed and evaluated when we discover the differences between machines supplied by various manufacturers.
The most noticeable difference is size
The first and most noticeable difference between resin 3D printers and other types of 3D printers is size. If DLP 3D Printers tend to be much larger than their SLA counterparts because they house the actual projector, it should be noted that build platforms for resin generally seem surprisingly small – compared to other types of 3D printers. It is even possible to find a DLP 3D printer with the size of a cell phone screen.
Almost no tolerance for overhangs and bridging
It looks like there is virtually no tolerance for overhangs. If an unsupported overhang occurs during the printing process, it is likely to break or to remain stuck to the build surface, contaminating therefore the resin while interfering with the print. That being said, if a part orientation enables layer changes, this will reduce the steepness of overhangs, and therefore the need for supports.
A great investment in post-processing
As you may know, post-processing is no longer a step to neglect since every operator almost always has to go through it before getting the final and desired result.
Surprisingly, resin 3D printing requires more extensive post-processing in the form of part washing, additional curing, and support removal. The user must rinse the prints free of uncured resin. To do so, he just needs to wash them in isopropyl alcohol and dries them. After this stage, they may still require exposure to UV for additional curing.
However, in this specific case, the post-processing stage should not always be seen as the “dirty work” to do. With resin 3D Printing, depending on the resin material that has been chosen – as well as the post-processing and finishing possibilities, the operator can achieve a very nice rendering.
Why should we use one specific resin 3D printing technology over another?
To answer this question, we invited Fernando Hernandez, Head of EMEA at XYZprinting. For those who do not know the company, XYZprinting is a manufacturer of 3D printers based on different technologies including SLS, SLA, FDM, inkjet and DLP. One of their latest solutions is the PartPro120 xP, a DLP 3D printer.
Hernandez specifically explained the pros and cons of each resin 3D printing technology :
“It comes down to the taste of the chef in the kitchen. Each technology will have its fair share of pros and cons, but we maintain today that DLP technology now offers the best combination and balance of resolution, speed, build dimension and cost. That doesn’t mean SLA doesn’t continue to play a big role in the products we manufacture though, since it continues to provide very fine details for large building volumes, all the while keeping prices low.
LCD on the other hand is a technology that often falls short, for the reasons below:
1- LCD life is much shorter for UV light source. The life of the LCD panel with the UV LED back light wavelength (of 365 ~ 405nm) is generally very short (~ 1000 hours of life), which significantly increases the printing cost.
2- LCD uniformity is worse because of crosstalk issues. Once light is emitted from the pixels, it mixes with the light emitted from other nearby pixels. This effect favours consumer markets, since it smooths the image and prevents users from spotting any pixel mesh unless they are looking very closely. This works against 3D printing resolution though, as it means that the images are blurry and not crisp, meaning the models can’t be well-detailed. In LCD, small details are lost, so things like small holes may be closed or not circular, for instance.
3- LCD’s pixel size is larger than the DLP UV light source. Therefore, resolutions advertised on LCD panels are from the origin, but not the resolution at which the light source will reach the print bed.
4- LCD’s light intensity is much weaker and this negatively affects the overall printing quality.
5- The source of an LCD panel is irregular. The LCD panel is used in the consumer market, meaning that printing special sizes is difficult and it doesn’t guarantee supply and/or quality for 3D printing. For the moment, those panel prices are cheap because 3D printing is enjoying a wave of mass production of those panels for consumers Market (TV, tablets, etc). But once consumers jumps to other technologies, 3D printing market quantities won’t be able to sustain the production and therefore it won’t be possible to keep a similar market price to what is available now.
Meanwhile the print quality of the DLP printer exceeds LCD in multiple ways. The details are higher and within all resin technologies, DLP offer the lowest loss of details, and it also proportions from 3D model to physical. Historically, the biggest handicap for DLP was that it was difficult to get a decent building size for decent pricing, but that barrier is fixed nowadays; building plates are bigger and thanks to technologies such as our UFF (Ultra Fast Film) we are able to print up to 70 times faster than before, beating printing speed and productivity of equivalent technologies in FDM and SLA, while also beating in resolution and detail.”
The good and the bad about resin 3D printing materials
In materials science, resin is a solid or highly viscous substance of plant or synthetic origin that can be transformed into polymers. Resins are usually mixtures of organic compounds.
As far as resin 3D printing materials are concerned, they enable the production of objects faster and with finer resolution than the other 3D Printing processes. This speed is due to the photo-curable resin that can produce small solid parts.
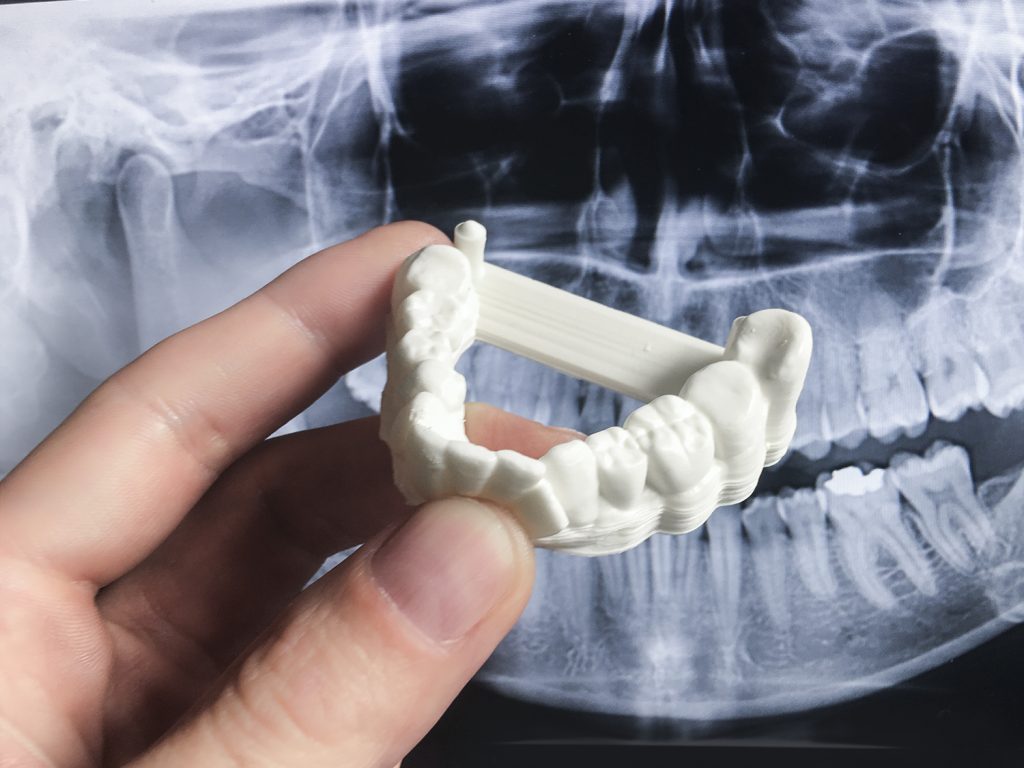
Apart from this noticeable advantage, it is vital to mention that resins can be toxic. Operators that handle such equipment might therefore be exposed to health issues. In the past, safety equipment was always part of the resin-based 3D printers’ package that operators received. These precautions were also the reason why resin-based 3D printers were expensive and only used by industries.
Over time, with the proliferation of cheap although powerful resin-based 3D Printers, such machines are increasingly used in less-secured environments where safety protocols are often forgotten.
With the technology advancements, some material suppliers have been able to develop an eco-friendly resin.
Another disadvantage is the fact the durability of resin-printed parts is fragile. In fact, since the resin is first cured with UV light, the material can remain sensitive to UV exposure. In other terms, if the printed part is exposed to sun for too long, its resin could continue to “cure” until it breaks.
Applications of resin 3D printing technologies
The jewelry industry and the dental industry are the sectors that leverage the most resin 3D printing. The increasing use of resin 3D printing in the aforementioned sectors may have given this technology a reputation of technology designed for prototyping applications.
Fernando Hernandez disproves this “popular belief”: “Printed resin models are not only used for prototyping, but also for creating the finished product. The key to doing this well, however, is to identify the precise mechanical properties required for the part’s final use. We need to consider the forces the end-product will be under, what temperatures it will be exposed to and more, and from there select the resin that is more suitable for the product’s needs. Nowadays, the industry is seeing resin-based printers used for mass production of parts in the automotive industry, production machines and final parts, to name a few. At The New Kinpo Group, we use resin-based printers to print a variety of final product parts.”
Furthermore, depending on the material used, it is possible to explore applications that go beyond these two sectors. “Certain resins can be more rigid, flexible and tougher than other resin strains. Some are able to simulate ABS mechanical properties while others have high temperature resistance, beating many of the most common thermoplastics. At times, the finished product of a resin-based model is smoother than its FDM counterpart for the same price range, making it a more viable and suitable option for creating final products”, explains XYZprinting spokesperson.
For instance, with a high-detail resin (usually compatible with PolyJet technology), the user can get a a smooth surface in the 3D printed part.
The mammoth resin for instance, has a great advantage: the printing of huge sizes. Such type of resins can be used in the production of bikes or a variety of works of art.
Another one is the Gray Resin. Ideal for the printing of figurines, the Gray Resin is a very smooth resin which is easy to paint.
Concluding thoughts
To sum up, resin-based 3D printers are getting more common and much more affordable. The user should keep in mind that affordability is not necessary synonym of bad quality. Also, they are not likely to replace filament-based 3D printers or metal AM 3D printers. The most important though, is to be aware of the pros and cons of each technology. Lastly, a professional does not need to buy several 3D printers in order to know the one that best fits his interest. In addition to what we have said in the above lines, the inspection of real parts produced with these machines or a test print of a design might be enough to help him take his decision.
This dossier was initially published in the January/February issue of 3D ADEPT Mag.