Seule une poignée d’entreprises propose des solutions d’impression 3D composite, alors que beaucoup d’industriels remettent encore en question les capacités de l’impression composite 3D dans la fabrication.
Nous avons récemment contacté le CEO et fondateur d’Anisoprint, Fedor Antonov, dans le cadre d’un dossier exclusif pour discuter des éléments qui font de ce procédé de fabrication un bon candidat pour la production.
Avec une décennie d’expérience universitaire et industrielle dans la conception et l’optimisation des matériaux et structures composites, Antonov est particulièrement bien placé pour clarifier toutes les zones d’ombre autour de cette technologie.
Comment expliquez-vous le fait que l’impression 3D composite soit moins répandue que les autres types de technologies de FA ?
L’impression 3D composite est l’une des plus jeunes branches des technologies de FA. Elle est très récente, c’est la seule raison. Chaque année, nous voyons de nouveaux acteurs entrer sur le marché et le nombre d’applications et de cas d’utilisation augmente rapidement. Je suis presque sûr que dans 5 à 10 ans, l’impression 3D composite sera l’une des plus grandes choses dans le domaine de la FA.
En quoi l’utilisation des composites diffère-t-elle des procédés de fabrication conventionnels et des procédés de fabrication additive ?
Il n’y a pas qu’un seul procédé de fabrication composite conventionnel. Et la plupart d’entre eux sont également « additifs » par définition (les matériaux sont ajoutés pour créer un objet, et non retirés).
En outre, les technologies de placement automatique des fibres (AFP – Automated Fiber Placement) ou de pose de bandes (ATL – Tape Laying), utilisées avec succès depuis des décennies pour produire des pièces composites de haute performance, pourraient être appelées impression 3D.
Certaines des nouvelles sociétés d’impression 3D composite proposent des technologies très similaires à l’AFP ou à l’ATL, et certains des anciens fournisseurs d’AFP/ATL commencent maintenant à appeler leurs machines, des imprimantes 3D. Il existe d’autres technologies de fabrication de composites, telles que la stratification manuelle, l’enroulement filamentaire, la pultrusion, le moulage par transfert de résine et bien d’autres, qui sont très différentes les unes des autres, mais qui sont toutes additives. Ce qui fait vraiment la différence, ce n’est pas le fait que ces technologies soient additives, mais plutôt un niveau plus élevé d’automatisation, de numérisation et de personnalisation du processus de fabrication. La plupart des technologies conventionnelles sont des processus à plusieurs étapes qui nécessitent beaucoup de travail manuel et administratif et présentent de nombreuses limites.
La technologie de fabrication composite idéale du futur (anisoprinting) est un processus de fabrication numérique en une seule étape, entièrement automatisé, qui n’impose aucune limite à la forme et à la structure interne de la pièce.
Quelles sont les technologies de FA qui peuvent traiter les matériaux composites ?
Les matériaux composites nécessitent une approche particulière, de sorte que les technologies existantes, qui n’ont pas été développées pour la fabrication de composites, ne peuvent pas les traiter (à l’exception des composites renforcés par des particules ou des fibres courtes, qui, à notre avis, ne devraient pas être pris en compte, car ils n’offrent pas une proposition de valeur différente).
La plupart des technologies de FA composites sont basés sur l’extrusion de matériaux ou sur la lamination. Pour l’instant, il est assez difficile de les classer, car chaque fournisseur a son propre procédé, qui présente des avantages et des inconvénients.
L' »impression 3D à fibre continue » nécessite-t-elle nécessairement deux buses dans l’imprimante 3D ? En quoi votre technologie diffère-t-elle des autres de la même gamme ?
Non. Une seule buse est nécessaire pour imprimer les composites. Je n’ai jamais entendu parler de technologie qui utilise deux buses pour imprimer des composites. Ce qui rend notre technologie unique par rapport aux autres, c’est le procédé de co-extrusion. Elle n’a donc qu’une seule buse, mais deux entrées : une entrée pour le matériau de renforcement (fibre) et une autre pour le matériau de la matrice (plastique).
Les deux matériaux sont mélangés à l’intérieur de la tête d’impression et sont extrudés par une seule buse. Dans la plupart des autres procédés d’impression 3D par extrusion de fibre continue, la fibre est préalablement imprégnée de plastique, et la tête d’impression a une entrée (pour la fibre, imprégnée de plastique) et une sortie (pour la même chose, mais le plastique est fondu à l’intérieur).
L’approche de co-extrusion nous permet d’utiliser différents types de plastiques comme matériau de matrice (liant), et ce choix est fait du côté du client, ce qui n’est pas possible avec l’approche de pré-imprégnation.
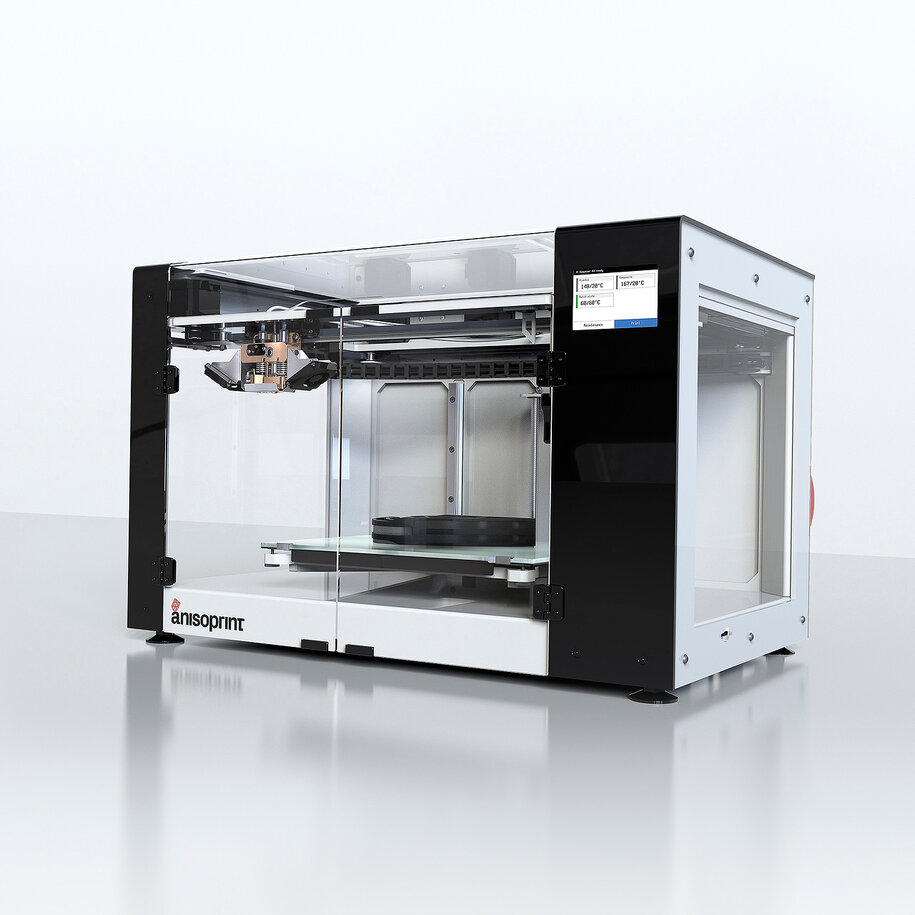
Par ailleurs, avec la co-extrusion, on peut modifier localement la fraction volumique de la fibre, ce qui permet d’imprimer des structures plus complexes comme des treillis ou d’utiliser des couches d’épaisseur variable.
La fibre de carbone reste le matériau le plus utilisé dans l’impression 3D composite. Pourquoi ?
C’est très simple. La fibre de carbone est le matériau le plus performant. Comme le principal UVP de l’impression 3D composite est de haute performance (haute résistance, rigidité et faible poids), il est logique d’utiliser les composants les plus performants. Lorsque les questions de prix deviendront plus importantes avec la maturité de la technologie, probablement, d’autres types de fibres (comme le verre, le basalte, l’aramide ou les fibres naturelles) deviendront plus populaires, mais chacun trouvera son propre créneau.
Enfin, comment savoir si l’impression 3D composite doit être mise à profit pour une application de production spécifique ?

C’est aussi très simple. La caractéristique principale des composites est leur haute performance et leur légèreté. Donc, s’il y a un besoin de légèreté – normalement, si quelque chose vole, ou se déplace très vite, ou si des personnes doivent le porter – la légèreté est importante. Dans de nombreux cas, vous pouvez fabriquer différentes pièces avec différents matériaux, et elles feront leur travail. La question est de savoir s’il est optimal d’utiliser tel ou tel matériau à cette fin. L’optimalité peut s’exprimer en termes de coût, de cycle de production, de poids ou autre.
Dans les cas où le poids est le plus important, les matériaux composites sont indispensables. En raison de leur nature directionnelle (anisotropie), les composites apportent beaucoup plus de liberté pour l’optimisation. Avec les métaux non directionnels (isotropes), vous pouvez uniquement optimiser la forme de la pièce, tandis qu’avec les composites, la forme et la structure interne peuvent être optimisées.
Nous couvrons Anisoprint depuis quelques années maintenant, mais 2020 a révélé une nouvelle dynamique pour l’équipe et sa capacité à obtenir d’énormes résultats au milieu de la crise.
N’oubliez pas que vous pouvez poster gratuitement les offres d’emploi de l’industrie de la FA sur 3D ADEPT Media ou rechercher un emploi via notre tableau d’offres d’emploi. N’hésitez pas à nous suivre sur nos réseaux sociaux et à vous inscrire à notre newsletter hebdomadaire : Facebook, Twitter, LinkedIn & Instagram ! Si vous avez une innovation à partager pour le prochain numéro de notre magazine numérique ou si vous avez un article à faire connaître, n’hésitez pas à nous envoyer un email à contact@3dadept.com