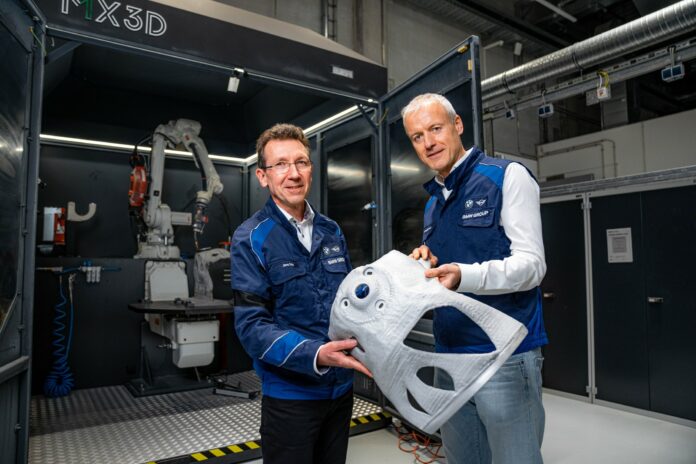
BMW Group engineers were able to demonstrate that WAAM components can be used for high loads, including cyclical loads, even without post-treatment of the surface.
During the past years, car manufacturer BMW Group has always shed light on the use of laser powder bed fusion as the main AM process it relies on for production parts. As time is going by, AM users show they are more and more open to explore other AM processes and the next one they seem to target is DED – WAAM in particular.
As a matter of fact, DED was one of the main technologies that raised AM users’ interest during the 2024 edition of AMUG.
In case you do not know, in wire arc additive manufacturing (WAAM) in particular, a wire made of aluminium or similar is melted using an arc. Then a software-controlled robot places a large number of welding seams on top of each other with precision, until the complete component is finished. Because the pressure means that layer by layer there is no need to pay attention to demouldability, hollow structures with an optimum ratio between rigidity and weight are possible. This means that the components can be lighter and more rigid than comparable die-cast parts currently manufactured in series production. They can also be produced more sustainably thanks to lower energy requirements and less material waste.
Read more: Unveiling the disguised complexities of Wire-Arc Additive Manufacturing
The use of WAAM at BMW Group
The BMW Group is trialling this process at the Additive Manufacturing Campus in Oberschleißheim, where they have pooled production, research, and training in this area under one roof.
BMW Group employees have been focussing on the WAAM process, also known as build-up welding, since 2015. A WAAM cell for the production of test components has been in use there since 2021. One of these example applications is a suspension strut support, which, in extensive testing on the test bench, is being compared with the series production component made from aluminum pressure die-casting.
“In this early stage it is already clear that the WAAM process can result in lower emissions in the production process. The lower weight of the components, their advantageous material usage ratio, and the option to use renewable energy means that the components can be produced more efficiently,” said Jens Ertel, Head of BMW Additive Manufacturing. The next stage of development on the road to series production is testing components in the vehicle, which will start in the foreseeable future.
The wider welding seams in the WAAM process mean that the surfaces of the components are not smooth, but slightly rippled and must be finished in critical areas. However, BMW Group engineers were able to demonstrate that WAAM components can be used for high loads, including cyclical loads, even without post-treatment of the surface. Optimized process parameters are crucial for ensuring durability directly from production, so the combination of welding process and robotic path planning must be coordinated optimally.
Configuration with generative design and algorithms
To make optimum use of the components produced in the WAAM process, the combination of the manufacturing process and a general new component design is paramount. To this end, the BMW Group continues to accelerate the use of generative design. Here, the computer uses algorithms to design optimised components based on the specific requirements. These algorithms are developed in close collaboration with interdisciplinary teams and are in part inspired by evolutionary processes in nature. As with bionic structures, the first step is to use only the material that is actually required for the topology of the component, and during fine-tuning in the second step, the component is reinforced only where necessary. This ultimately results in lighter and more rigid components as well as greater efficiency and improved vehicle dynamics.
“It’s impressive to see how WAAM technology has developed from research to become a flexible tool for not only test components but also series production components. The use of generative design methods enables us to make full use of design freedom and thus the potential of the technology. That was unthinkable just a few years ago,” said Karol Virsik, Head of BMW Group Vehicle Research.
Images: BMW Group. Remember, you can post job opportunities in the AM Industry on 3D ADEPT Media free of charge or look for a job via our job board. Make sure to follow us on our social networks and subscribe to our weekly newsletter : Facebook, Twitter, LinkedIn & Instagram ! If you want to be featured in the next issue of our digital magazine or if you hear a story that needs to be heard, make sure you send it to contact@3dadept.com