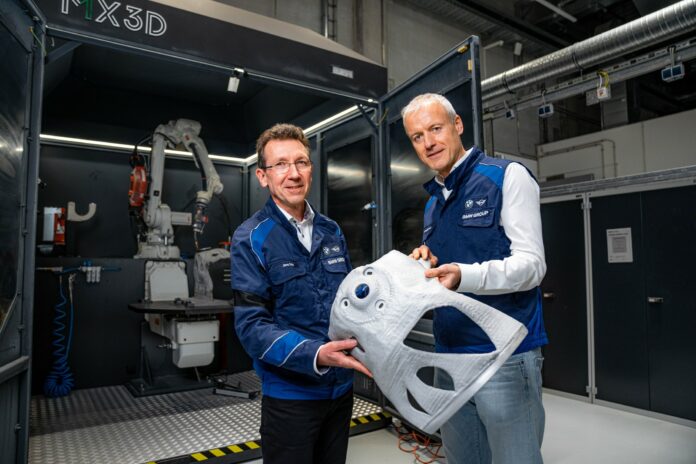
Les ingénieurs de BMW Group ont pu démontrer que les composants fabriqués avec le procédé « WAAM » peuvent être utilisés pour des charges élevées, y compris des charges cycliques, même sans post-traitement de la surface.
Au cours des dernières années, le constructeur automobile BMW Group a toujours mis en avant l’utilisation de la fusion laser sur lit de poudre comme principal procédé de fabrication additive pour la production de pièces. Au fil du temps, les utilisateurs de FA se montrent de plus en plus ouverts à l’exploration d’autres procédés de fabrication et le prochain qu’ils semblent cibler est le DED – WAAM (wire arc additive manufacturing ) en particulier.
En fait, le DED a été l’une des principales technologies qui a suscité l’intérêt des utilisateurs de FA lors de l’édition 2024 d’AMUG.
Au cas où vous ne le sauriez pas, dans la fabrication additive par arc électrique (WAAM) en particulier, un fil en aluminium ou similaire est fondu à l’aide d’un arc électrique. Ensuite, un robot commandé par logiciel superpose avec précision un grand nombre de soudures, jusqu’à ce que le composant complet soit terminé. Grâce à la pression, il n’est pas nécessaire de prêter attention à la démoulabilité couche par couche, ce qui permet d’obtenir des structures creuses présentant un rapport optimal entre la rigidité et le poids. Cela signifie que les composants peuvent être plus légers et plus rigides que les pièces moulées sous pression comparables actuellement fabriquées en série. Ils peuvent également être produits de manière plus durable grâce à des besoins énergétiques moindres et à une réduction des déchets de matériaux.
Découvrez plus : Les complexités cachées de la fabrication additive arc-fil.
L’utilisation du procédé WAAM chez BMW Group
Le groupe BMW teste ce procédé sur le campus de fabrication additive d’Oberschleißheim, où il a regroupé sous un même toit la production, la recherche et la formation dans ce domaine.
Les employés de BMW Group se concentrent sur le processus WAAM, également connu sous le nom de soudage par accumulation, depuis 2015. Une cellule WAAM pour la production de composants d’essai y est utilisée depuis 2021. L’un de ces exemples d’application est un support de jambe de suspension qui, dans le cadre de tests approfondis sur le banc d’essai, est comparé au composant de série fabriqué à partir d’aluminium coulé sous pression.
« À ce stade précoce, il est déjà clair que le processus WAAM peut entraîner une réduction des émissions dans le processus de production. Le poids réduit des composants, leur ratio avantageux d’utilisation des matériaux et la possibilité d’utiliser des énergies renouvelables signifient que les composants peuvent être produits plus efficacement », a déclaré Jens Ertel, responsable de la fabrication additive chez BMW. La prochaine étape de développement sur la voie de la production en série consiste à tester les composants dans le véhicule, ce qui commencera dans un avenir proche.
Les joints de soudure plus larges dans le processus WAAM signifient que les surfaces des composants ne sont pas lisses, mais légèrement ondulées et doivent être finies dans les zones critiques. Cependant, les ingénieurs de BMW Group ont pu démontrer que les composants WAAM peuvent être utilisés pour des charges élevées, y compris des charges cycliques, même sans post-traitement de la surface. L’optimisation des paramètres du processus est cruciale pour garantir la durabilité dès la production, de sorte que la combinaison du processus de soudage et de la planification de la trajectoire robotique doit être coordonnée de manière optimale.
Configuration avec conception générative et algorithmes
Pour optimiser l’utilisation des composants produits par le procédé WAAM, il est essentiel de combiner le procédé de fabrication et une nouvelle conception générale des composants. À cette fin, BMW Group continue d’accélérer l’utilisation de la conception générative. Dans ce cas, l’ordinateur utilise des algorithmes pour concevoir des composants optimisés en fonction des exigences spécifiques. Ces algorithmes sont développés en étroite collaboration avec des équipes interdisciplinaires et s’inspirent en partie des processus évolutifs de la nature. Comme pour les structures bioniques, la première étape consiste à n’utiliser que le matériau réellement nécessaire à la topologie du composant et, lors de l’affinement de la seconde étape, le composant n’est renforcé que là où c’est nécessaire. Cela permet d’obtenir des composants plus légers et plus rigides, ainsi qu’une plus grande efficacité et une meilleure dynamique du véhicule.
« Il est impressionnant de voir comment la technologie WAAM est passée du stade de la recherche à celui d’un outil flexible, non seulement pour les composants d’essai, mais aussi pour les composants de production en série. L’utilisation de méthodes de conception générative nous permet d’exploiter pleinement la liberté de conception et donc le potentiel de la technologie. C’était impensable il y a seulement quelques années », a déclaré Karol Virsik, responsable de la recherche sur les véhicules de BMW Group.
Images: BMW Group. N’oubliez pas que vous pouvez poster gratuitement les offres d’emploi de l’industrie de la FA sur 3D ADEPT Media ou rechercher un emploi via notre tableau d’offres d’emploi. N’hésitez pas à nous suivre sur nos réseaux sociaux et à vous inscrire à notre newsletter hebdomadaire : Facebook, Twitter, LinkedIn & Instagram !