Avec un premier brevet accordé dans les années 1920, la fabrication additive arc-fil (en anglais WAAM = Wire-Arc Additive Manufacturing), est certainement l’un des plus anciens procédés de fabrication additive (FA) qui existent, et pourtant cette technologie est la moins mise en avant dans la gamme des procédés de FA reconnus. La raison de cette lente adoption au niveau industriel réside peut-être dans le vide qu’il reste à combler dans la chaîne d’approvisionnement.
Stimulé par la demande d’amélioration de l’efficacité de la fabrication des structures d’ingénierie, la fabrication additive arc-fil, également connu sous le nom de dépôt d’énergie dirigée (DED-arc = Directed Energy Deposition-arc), peut être considérée comme l’intégration d’un principe « additif » dans le processus de soudage à l’arc. Selon les fabricants, étant donné que dans un processus de soudage, l’énergie thermique est utilisée pour faire fondre les bains métalliques fusionnés les uns aux autres, la transformation du processus en un procédé additif était tout à fait compréhensible. D’un point de vue technologique, le procédé additif permet d’obtenir un taux de dépôt élevé de la matière première métallique sous la forme d’un filament, comme dans le cas du procédé de soudage conventionnel. Cela pourrait expliquer pourquoi les premiers fabricants de systèmes WAAM ont une forte expertise dans l’industrie du soudage.
Selon Wim Verlinde, consultant et ingénieur en soudage à l’Institut belge de soudage (Belgian Welding Institute – BWI)), d’autres raisons et questions peuvent expliquer cette influence du WAAM dans l’industrie du soudage : « Il existe encore un nombre limité de procédés conventionnels pour la fabrication de grandes pièces. Le moulage est l’un de ces procédés, mais il nécessite encore un certain nombre de développements, tels que des moules, et il devient difficile de fabriquer de grandes pièces pour de petites séries, ce qui, au final, peut s’avérer extrêmement coûteux. Une autre raison est que le WAAM peut servir à beaucoup d’autres applications telles que les pièces de réparation comme réalisées par Guaranteed, les pièces de rechange à la demande, le prototypage, etc. »

Il y a deux ans, par exemple, l’équipe de BWI a lancé un projet de recherche (financé par VLAIO – Agentschap Innoveren en Ondernemen – Vlaanderen) lorsqu’elle s’est aperçue que de nombreux robots étaient expédiés vers leurs installations et restaient inutilisés la nuit ou le week-end. Verlinde a expliqué que son équipe s’est demandé si elle pouvait transformer un robot de soudage traditionnel normal en un robot d’impression 3D.
Selon le consultant en soudage, l’impact perturbateur du WAAM sur l’industrie du soudage peut résider dans le fait que le processus requiert un matériau spécifique à différents endroits de la pièce imprimée en 3D pour fournir par exemple, la fatigue, la corrosion ou les contraintes élevées. Dans ces cas, la pièce est construite dans des zones spécifiques avec des matériaux spécifiques, ou le processus de fabrication peut nécessiter l’utilisation de deux fils qui sont mélangés in-situ et composés ensemble pour atteindre un objectif spécifique. (Selon l’expert, de tels scénarios de production sont assez complexes car ils peuvent conduire à certains problèmes métallurgiques).
Même s’il est reconnu pour l’industrie manufacturière à grande échelle, le procédé WAAM s’accompagne d’un certain nombre de contraintes au niveau de la fabrication. Le présent dossier vise à :
- Aider les professionnels à comprendre le fonctionnement du processus WAAM ;
- Mettre en lumière les différents défis que les ingénieurs rencontrent souvent lors de la fabrication avec le WAAM et mettre en lumière les solutions potentielles qui pourraient être utilisées pour les surmonter. Cela inclut mettre en avant le vide qui reste à combler dans la chaîne d’approvisionnement comme nous avons mentionné ci-dessus ;
- Partager quelques exemples d’applications et quelques solutions dédiées au procédé WAAM disponibles sur le marché.
WAAM : procédés et principales caractéristiques
En termes simples, dans un procédé WAAM, un arc électrique est utilisé comme principale source de chaleur pour obtenir des préformes de forme quasi nette sans avoir recours à des outils, des moules ou des matrices complexes. Tout comme il existe plusieurs types de procédés de FA métallique, on peut identifier plusieurs sous-catégories de procédés WAAM.
Selon Mark Douglass, Responsable du développement commercial chez Lincoln Electric Additive Solutions, ces sous-catégories sont basées sur les différents procédés de soudage à l’arc :
- « Le soudage à l’arc sous gaz (GMAW= Gas metal arc welding) ou, comme on l’appelle souvent en Europe, « MIG/MAG » ; c’est le procédé le plus souvent mentionné et celui qu’utilise Lincoln ;
- Le soudage à l’arc plasma (PAW = Plasma arc welding), est celui que l’université de Cranfield a popularisé ;
- Le soudage à l’arc en tungstène (GTAW = Gas tungsten arc welding) [également connu sous le nom de soudage au gaz inerte (TIG)] ».
Cependant, en ce qui concerne l’équipement lui-même, les développements des systèmes WAAM varient d’un fabricant à l’autre (comme nous le verrons à la fin de ce dossier) mais la plupart des machines relèvent soit de la robotique, soit de la machine-outil. « Certains fabricants partent d’une machine à commande numérique et transforment cette dernière en imprimante à souder, puis ils réalisent l’usinage et l’impression au sein d’une même plateforme. Le fabricant de machines GEFERTEC, par exemple, développe ses machines de FA sur la base de ce principe », note Verlinde. En outre, comme il l’a expliqué précédemment, il est possible de combiner n’importe quel manipulateur à trois axes avec un bras de robot à six axes et une source d’énergie de soudage à l’arc pour développer un système WAAM de base. Ce dernier peut être combiné à un robot de meulage (dans une seule plateforme) ou à une CNC traditionnelle pour la finition de surface.
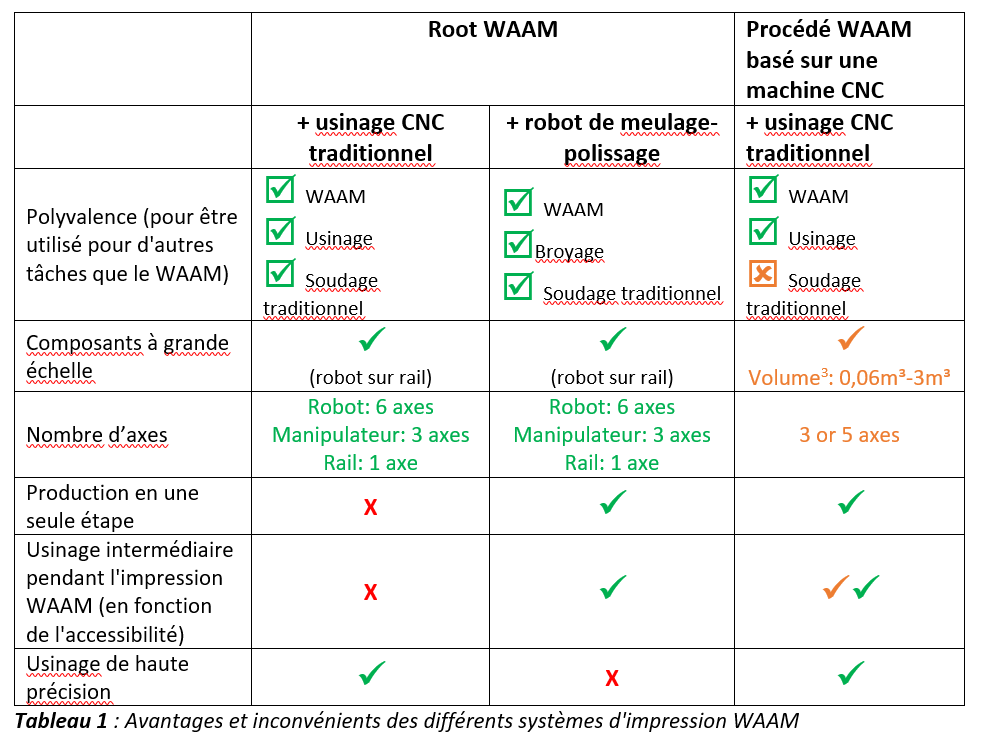
Quelle que soit la façon dont elles sont construites, ces machines doivent être soutenues par un solide logiciel de CFAO (CAD/CAM).
Du côté du logiciel
Le processus de fabrication avec WAAM commence par un logiciel de FAO qui aide à générer le parcours d’outil et les paramètres de soudage pour la table à portique ; on peut ensuite contrôler les points de départ et d’arrêt du soudage et déterminer la vitesse d’avance du filament métallique. Comme dans tout processus additif, le logiciel doit être capable de convertir le modèle CAO en un code imprimable en suivant le principe du tranchage. Une fois le processus lancé, la torche de soudage se déplace dans une direction donnée sur la plaque de construction et déclenche le dévidoir de fil pour déposer le matériau sur le trajet.
Les outils et systèmes logiciels jouent un rôle important dans la préparation du processus. Aujourd’hui, il est possible de diviser les logiciels existants pour le procédé WAAM en deux catégories principales : les applications autonomes et les plug-ins qui sont intégrés dans les logiciels de CAO/FAO existants. Les plug-ins pour WAAM sont développés et intégrés dans un certain nombre de logiciels de CFAO. Le principal avantage est la possibilité de préparer à la fois le WAAM et les étapes d’usinage au sein d’une même plateforme logicielle. La fonctionnalité, comparée aux applications autonomes, est parfois limitée : principalement dans la variété des stratégies de trajectoire de dépôt, le contrôle et le réglage des paramètres de soudage, etc.
Plug-ins (=basé sur la FAO CNC) | Applications autonomes (= spécifiques au procédé WAAM) |
• Sprutcam robot • PowerMill (Autodesk) • Robotmaster • Hypermill (Dassault Sytems) • Siemens NX • Eureka | • Metal XL (MX3D) • Factory OS (OQTON) • WAAMMat (Cranfield University) |
L’Institut belge de soudure (IBB), VIVES et KULeuven sont des instituts de recherche indépendants. Tout fournisseur de logiciel de FAO WAAM peut être ajouté à ce tableau. Lors du choix, les caractéristiques suivantes du logiciel doivent être évaluées en fonction de l’application, de la complexité, de la forme, etc :
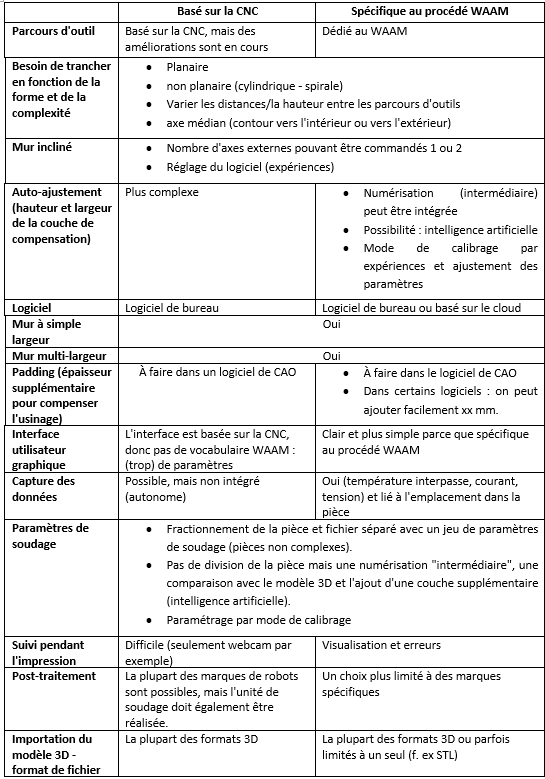
Pour Verlinde, « l’ingénieur concepteur a ici une tâche importante. Contrairement à d’autres industries, comme les constructions métalliques ou les appareils à pression, où tout est régi par des normes (harmonisées) pour l’ingénieur concepteur, ici, ce dernier doit décider des caractéristiques des matériaux, des défauts potentiels, du type de finition nécessaire – puisque la finition dépend de l’application. Malheureusement, il est toujours limité dans son travail par les normes. Pour certaines applications par exemple, qui sont soumises à des réglementations strictes, il n’a pas la liberté de décider comment il va construire la pièce. » L’ingénieur concepteur peut avoir besoin d’une équipe multidisciplinaire compétente pour prendre des décisions sur tous les sujets en fonction de la complexité et des risques de la pièce.
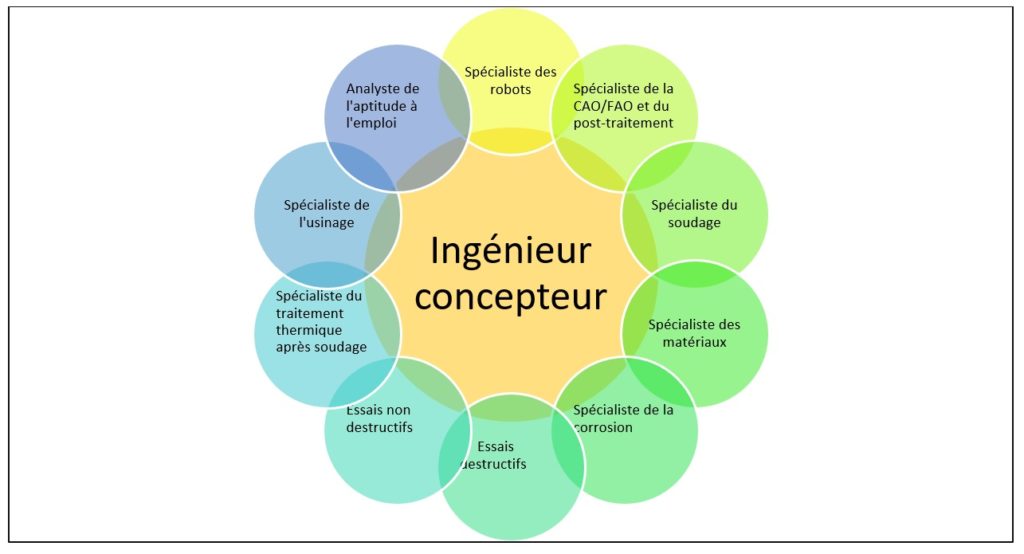
En d’autres termes, concevoir pour un procédé WAAM signifie identifier toutes les géométries de pièces qui conviennent le mieux aux applications finales dans le monde réel. Dans l’industrie aérospatiale, par exemple, de nouveaux raidisseurs légers sont utilisés pour répondre à des contraintes mécaniques spécifiques.
Dans le même ordre d’idées, étant donné que le procédé WAAM offre des taux de dépôt élevés, l’ingénieur concepteur doit tenir compte du fait que l’important apport de chaleur de ces procédés peut également entraîner des contraintes résiduelles et des distorsions importantes.
Dans de tels cas, le « ‘préchauffage’ peut être utilisé pour contrôler la distorsion. Il est possible de modéliser la distorsion et de la compenser dans le parcours de l’outil en fonction de la prédiction, mais je ne pense pas que des outils efficaces aient encore été développés. Sinon, l’expérience peut être d’un grand secours pour gérer la distorsion », observe Douglass. Le fait est que ces problèmes peuvent avoir un impact considérable sur la précision de la forme finale des pièces et sur leurs performances mécaniques. Il est donc important de prendre en compte le comportement thermo-mécanique du procédé WAAM lors de la phase de conception.
Du côté des matériaux
Pour chaque type de source d’énergie disponible, le matériau utilisé peut déterminer le processus de dépôt à l’arc. Par exemple, les alliages de titane sont largement traités avec le soudage à l’arc en tungstène gazeux ou l’arc transféré par plasma, tandis que la plupart des matériaux sont déposés avec un équipement MIG/MAG.
D’une manière générale, tous les matériaux disponibles en tant que fil de soudure peuvent être utilisés pour la production de pièces via le WAAM, même si, selon Douglass, « certaines précautions telles que le préchauffage peuvent encore être nécessaires. »
S’il est d’accord avec cette généralisation, Verlinde nuance néanmoins sa réponse :
« La plupart des matériaux sont adaptés à l’impression parce que nous les soudons, mais tout dépend de ce que vous attendez au final des caractéristiques du matériau et ce sans prendre en compte les imperfections de la soudure qui peuvent en découler. Certains matériaux comme l’aluminium et le titane sont plus difficiles et sont utilisés dans des applications critiques haut de gamme, mais ils permettent de réduire les délais de production. Le problème de la plupart des entreprises sur le marché est qu’elles pensent que le WAAM est déjà au même niveau que la fusion sur lit de poudre, mais ce n’est pas encore le cas. Cependant, il est clair qu’à de nombreux niveaux (logiciel, usinage, recherche…), de grands progrès ont été réalisés depuis le début du projet. » D’autre part, le soudage à l’arc sous gaz tungstène peut traiter une large gamme de matériaux, notamment les aciers au carbone et faiblement alliés, l’acier inoxydable, les alliages à base de nickel, les alliages de titane et les alliages d’aluminium.
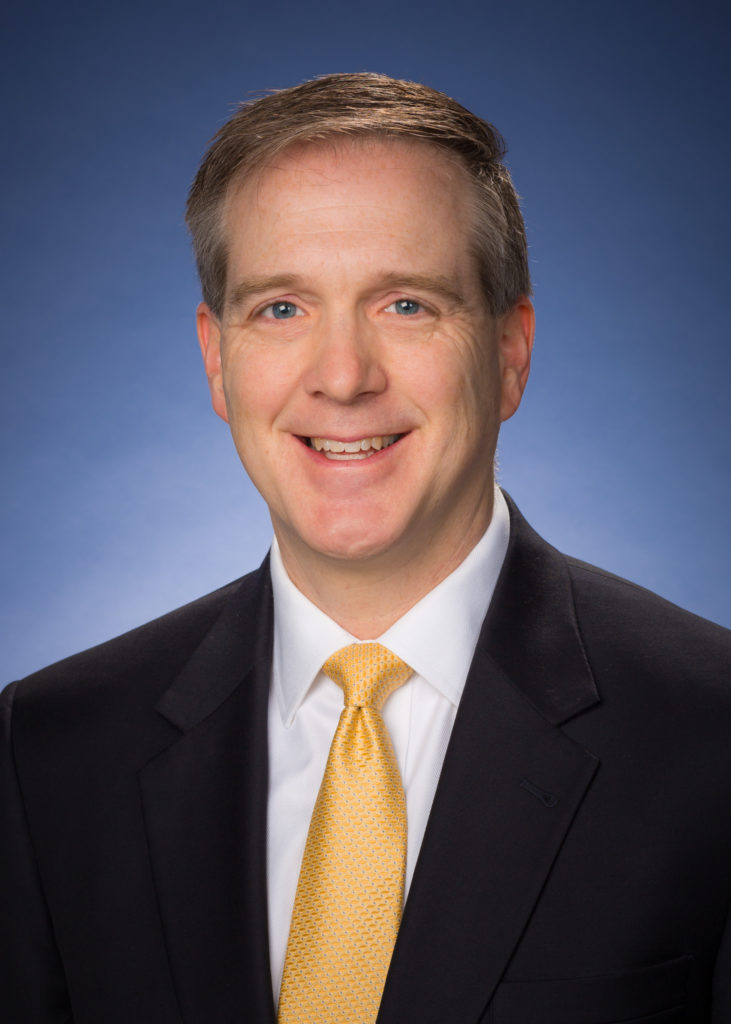
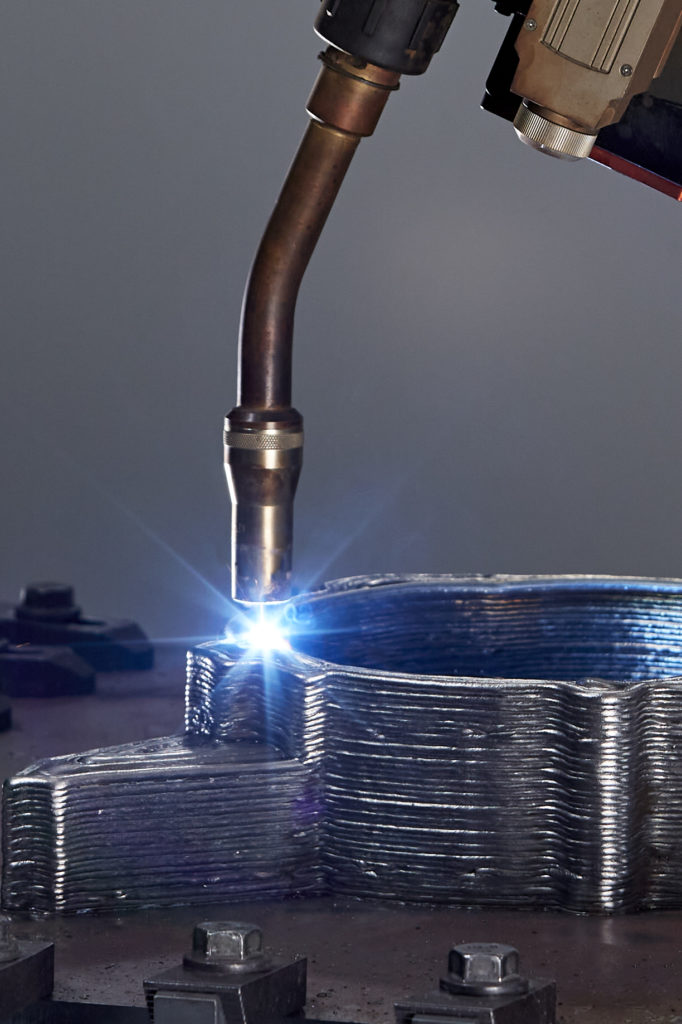
Douglass a également attiré notre attention sur le fait que les comparaisons entre les pièces imprimées en 3D produites via WAAM et les pièces produites avec des matériaux coulés ou corroyés ne sont pas évidentes à faire « car les alliages développés pour le fil de soudure ne sont souvent pas les mêmes que ceux des pièces coulées et corroyées. »
« Par conséquent, il faut faire correspondre les propriétés souhaitées du matériau déposé avec les fils disponibles. En d’autres termes, même si la chimie du fil peut ne pas correspondre à celle d’une pièce corroyée ou moulée donnée, il est souvent possible d’atteindre, voire de dépasser, les propriétés mécaniques souhaitées.
D’autre part, le métal déposé par le procédé WAAM peut être de très haute qualité – aussi bonne que celle du corroyage et souvent meilleure que celle des pièces moulées. Par exemple, dans de nombreux cas, le WAAM présente une porosité nettement inférieure à celle des pièces moulées. Le soudage est utilisé pour assembler de manière fiable des composants très critiques et même pour réparer des pièces moulées critiques depuis de nombreuses décennies, ce qui donne aux utilisateurs finaux la certitude qu’il est possible d’obtenir une qualité interne très élevée », ajoute-t-il.
Néanmoins, une chose sur laquelle la plupart des fabricants s’accordent, c’est le fait que le WAAM est reconnu comme un procédé qui permet de consommer de la matière. Il va sans dire que le pourcentage de réduction peut varier d’une application à l’autre, mais qu’il peut atteindre jusqu’à 70 % dans certaines applications, par rapport aux procédés de fabrication classiques.
Douglass rappelle ici que pour une application réalisée pour un client d’équipement minier, ils ont obtenu des économies de poids et de matière de plus de 20% pour un composant d’environ un mètre de long et de près de 200 kg.
Et le post-traitement…
Comme dans toute méthode de FA, la plupart des applications nécessiteront une gamme spécifique de tâches de post-traitement pour atteindre les objectifs de fabrication souhaités. Dans ce procédé de dépôt d’énergie par arc, l’expert de Lincoln Electric Additive Solutions souligne que ce processus de fabrication peut nécessiter l’utilisation des mêmes tâches de post-traitement que celles utilisées pour tout composant moulé ou fabriqué : « traitement thermique (pour la réduction des contraintes et/ou l’amélioration des propriétés mécaniques), usinage, fabrication supplémentaire ou assemblage à d’autres composants ». Néanmoins, « les composants WAAM sont entièrement denses, et il n’est donc pas nécessaire de recourir au pressage isostatique à chaud (HIP) », précise-t-il.
Avantages, points à améliorer et perspectives d’avenir
Ce dossier ne peut présenter qu’un aperçu général du procédé WAAM. Sur la base de nos échanges avec les deux experts qui ont été invités à partager leur vision du sujet, nous pouvons résumer les avantages suivants et les défis qui doivent encore être relevés par les fabricants :
Avantages | Points d’amélioration |
Idéal pour la fabrication de (très) grandes pièces | Longs délais d’exécution pour les moulages et les forgeages de nouvelles pièces, d’outillage ou de prototypes. |
Taux de déposition élevé et haute résistance mécanique des pièces | Contraintes résiduelles et distorsions – (L’expérience de la fabrication permet de mieux maîtriser ces problèmes). |
Des pièces plus légères et moins de déchets. | Blindage pour certains matériaux |
Essais de prototypes plus rapides. | La plupart des responsabilités incombent à l’ingénieur concepteur, ce qui est certainement dû au manque de normalisation dans le domaine. |
Réduction des délais de livraison de plusieurs mois à quelques semaines. | Les tests de produits et les réglementations industrielles qui peuvent entraîner des retards et/ou des délais supplémentaires pour la reconception ou la refabrication. |
Les processus ont tendance à être plus automatisés | Usinage – finition de surface (CNC ou meulage) |
Depuis son premier brevet accordé dans les années 1920, il faut reconnaître que le procédé WAAM a bien évolué. En 1983, le soudage de forme était utilisé pour fabriquer de grandes pièces d’acier nucléaire. Une décennie plus tard, Prinz et Weiss ont breveté la « fabrication par dépôt de forme » avec le fraisage CNC. À la fin du XXe siècle, l’université de Cranfield s’est vu accorder un brevet pour le procédé de dépôt de métal façonné pour le développement de carters de moteur utilisant différents matériaux.
Nous pouvons envisager une adoption rapide du WAAM grâce aux ressources appropriées apportées par les principaux acteurs de la chaîne d’approvisionnement ; ces ressources comprennent les outils logiciels appropriés, les machines plus précises, les matières premières, la formation et les services, mais aussi l’usinage et, surtout, la normalisation.
Aujourd’hui, les experts du domaine continuent de repousser les limites de ce processus de FA des métaux. Des livres blancs et des livres ont été rédigés par des entreprises et mis à la disposition des professionnels qui souhaitent explorer davantage ce processus. Plusieurs recherches continuent d’être entreprises pour étudier ses avantages, l’alliage in situ par exemple, ainsi que les méthodes qui utilisent le fil pour créer de nouveaux composites.
Nous sommes convaincus que la meilleure façon d’évaluer objectivement les capacités du WAAM en tant que procédé viable de FA des métaux est de le faire en évitant la comparaison avec d’autres procédés de FA métallique. Le WAAM est le WAAM et ne sera jamais la fusion sur lit de poudre, ni le jet de liant ou quoi que ce soit d’autre. En fin de compte, chacune de ces technologies de FA des métaux a ses avantages et ses inconvénients, et le WAAM mérite d’être pris en considération car plus le marché évolue, plus les fabricants développent de nouveaux équipements et services conçus pour le WAAM, ce qui entraîne encore plus d’applications réussites dans ce domaine.
Exemples d’applications et quelques solutions dédiées au WAAM
Pour une technologie dont on dit qu’elle recèle un énorme potentiel pour les applications de FA à grande échelle dans de multiples industries, nous avons tenu à découvrir la taille d’une pièce. À cette question, Douglass répond : « En théorie, il n’y a pas de limite, même si, de manière réaliste, il y a éventuellement une limite pratique avec les systèmes robotisés ou à portique. »
Les applications de WAAM peuvent être explorées dans l’aérospatial, l’automobile, le pétrole et le gaz, l’énergie et d’autres industries lourdes.
Sur le marché actuel, la liste des entreprises et des organisations qui ont développé des solutions dédiées au WAAM est relativement exhaustive. Il s’agit par exemple de : Lincoln Electric Additive Solutions, Gefertec, MX3D, Ramlab, Guaranteed, OQTON, AML3D, WAAM3D, Addilan, KRAKEN, voestalpine Böhler Welding Automation et Vallourec.
Outre ces organisations, il existe également des instituts de recherche qui explorent en permanence le procédé de fabrication WAAM et développent de nouvelles techniques pour l’améliorer. Parmi les instituts de recherche présents sur le marché, nous avons invité l’Institut belge de soudage qui soutient les entreprises désireuses de s’engager dans la voie de la fabrication additive de métaux par WAAM, depuis les essais mécaniques et de corrosion jusqu’aux premières études de faisabilité, en passant par les pistes industrielles permettant d’intégrer la technologie dans votre environnement de production. Wim Verlinde, expert sur ce sujet, nous a dit que l’Institut et ses partenaires de projet KU Leuven et VIVES ont déjà travaillé avec des logiciels WAAM comme MX3D, Sprutcam, OQTON, PowerMill (Autodesk) ou des fournisseurs de services comme MX3D, Guaranteed, OQTON, … sur des projets dédiés au WAAM. Ils sont actuellement impliqués dans des projets de standardisation qui pourraient permettre une meilleure adoption de la technologie à travers les industries et aider les concepteurs à prendre des décisions plus facilement en ce qui concerne la caractérisation des matériaux.
Lincoln Electric Additive Solutions
Lincoln Electric Additive Solutions est la division de fabrication additive de Lincoln Electric, une multinationale américaine experte dans la conception, le développement et la fabrication de produits de soudage à l’arc et de systèmes automatisés d’assemblage, de montage et de découpe. Grâce à l’héritage de 126 ans de sa société mère et à son activité d’automatisation de 500 millions de dollars, Lincoln Electric Additive Solutions a développé un robot de soudage à l’arc métallique gazeux.
Mark Douglass, Responsable du développement commercial chez Lincoln Electric Additive Solutions, qui a été invité en tant que contributeur clé à ce dossier, explique le fonctionnement de leur technologie :
« Un courant électrique crée un arc entre un fil-électrode et le substrat, ce qui fait fondre le fil et dépose des cordons de soudure qui forment les couches. Le courant électrique est généré et contrôlé avec précision par notre source d’énergie Power Wave®, grâce à laquelle nous pouvons programmer des formes d’ondes de courant avancées pour obtenir des caractéristiques d’arc optimales pour un alliage donné ».
Conscient de l’importance cruciale du logiciel dans un processus WAAM, Lincoln Electric Additive Solutions a développé un logiciel. Nommé SculptPrint™ OS, il découpe les fichiers CAO, planifie le parcours de l’outil pour le robot et programme le robot.
La société a intégré un mouvement coordonné avancé entre un robot industriel à 6 axes et un positionneur multi-axes afin de produire des géométries plus complexes tout en minimisant, voire en éliminant, les structures de support. Selon Douglass, ses contrôles adaptatifs exclusifs de la hauteur et de la largeur des couches garantissent le maintien d’une hauteur de couche appropriée par rapport au modèle prévu.
Un avantage distinctif intéressant peut être le fait que Lincoln contrôle l’ensemble de la chaîne de valeur du processus, puisqu’elle « fabrique ses propres sources d’énergie, ses fils d’alimentation, ses positionneurs, ses systèmes robotiques intégrés, ses logiciels et ses commandes ».
Il convient de noter que, même si la société développe ses propres systèmes, elle ne les vend pas pour une production commerciale et agit plutôt comme un fournisseur de services de fabrication.
En ce qui concerne les applications, l’équipe d’ingénieurs a déjà produit des pièces individuelles de plus de 2 mètres et de 635 kg (1 400 lb).
Focus sur les applications avec Guaranteed
Guaranteed est une entreprise spin-off de Finindus, ArcelorMittal Belgium et OCAS. Nous avons découvert l’expertise de l’entreprise lorsqu’elle a participé à un dossier explorant la FA dans les industries pétrolière, gazière et maritime (édition de juillet-août 2020 de 3D ADEPT Mag). Verlinde a mentionné le prestataire de services belge comme une entreprise qui fabrique des pièces de réparation à l’aide du procédé WAAM.
Nous avons également appris que pour chaque application, le logiciel de l’entreprise programme automatiquement le robot et les systèmes de soudage, tandis qu’un second logiciel peut simuler le processus de soudage et fournit des certitudes au niveau micro. Cela signifie que des informations supplémentaires peuvent être fournies sur les propriétés dynamiques et la qualité des pièces réparées.
L’entreprise explique sur son site web qu’elle peut traiter des pièces allant jusqu’à dix mètres sur six sur cinq, avec un poids maximal de 20 tonnes. Elle dispose actuellement d’une base de données d’environ 24 matériaux, qui peut être augmentée sur demande. Selon Joachim Antonissen, Directeur général, ils se concentrent principalement sur le marché de la réparation qui peut générer des millions d’économies.
L’une des pièces de réparation qu’Antonissen a partagé dans le cadre de ce dossier est une douille de mandrin. Il explique qu’au cours du processus de fabrication, le « matériau d’origine a été amélioré pour obtenir une plus grande résistance après réparation et ainsi prolonger la durée de vie du composant. La réparation de la pièce a coûté moins d’un tiers du coût de la pièce neuve, tandis que la consommation d’énergie et les émissions de carbone ont été réduites de plus de 90 %. »
WAAM3D Ltd, une entreprise dérivée de l’Université de Cranfield.
Si vous commencez à chercher des informations sur le WAAM, vous ne pouvez manquer de remarquer que l’Université de Cranfield a été au cœur des principaux développements du WAAM. Suite au brevet que l’Université a obtenu au 20e siècle, les chercheurs continuent d’explorer les possibilités de la technologie via un vaste programme de collaboration appelé WAAMMat. L’année dernière, WAAM3D Ltd, une entreprise dérivée de l’Université de Cranfield, a officiellement annoncé ses premiers pas sur le marché grâce à un investissement d’Accuron Technologies Ltd.
« Les principes de base de WAAM consistent à faire fondre un fil avec un arc électrique. Ce que nous faisons différemment, c’est d’abord de disposer d’un plus grand choix de procédés d’arc électrique en fonction des exigences de nos partenaires (matériau, géométrie, taille, etc.). Deuxièmement, nous disposons d’une méthode brevetée permettant de combiner les arcs électriques et les lasers afin d’obtenir des taux de dépôt plus élevés et un meilleur contrôle de la géométrie finale. Troisièmement, nous disposons d’une autre méthode brevetée pour introduire le travail à froid dans les pièces et améliorer considérablement les propriétés mécaniques qui en résultent afin de répondre aux exigences plus strictes appliquées aux pièces critiques », a déclaré Filomeno Martina, CEO et cofondateur de WAAM3D Ltd à 3D ADEPT Media.
Contrairement à d’autres acteurs qui apportent une expertise clé en matière de soudage sur ce marché, WAAM3D Ltd a déclaré que sa technologie a été développée en pensant directement au procédé de WAAM – et non au soudage. Leurs systèmes intègrent un ensemble de capteurs qui facilitent l’assurance et le contrôle de la qualité, par exemple la mesure en direct de la forme en cours de processus.
Comme d’autres entreprises spécialisées dans ce domaine, la start-up a également développé une suite logicielle dédiée, qui comprend WAAMPlanner et WAAMCtrl.
Le WAAMPlanner est un progiciel de FAO dans lequel l’ingénieur peut dessiner la trajectoire du processus d’impression avec des paramètres de processus intégrés basés sur la CAO de la pièce. WAAMCtrl est décrit comme le « cerveau du processus« . Il permet au superviseur de la machine de surveiller le processus depuis n’importe où, tandis que les données de construction de la pièce sont stockées en toute sécurité.
« Nous fabriquons également des fils conçus pour WAAM, avec une qualité incroyable dans le dépôt qui en résulte. L’expérience de l’utilisateur est donc conforme à ce que l’on peut attendre d’une technologie aussi futuriste et étonnante, qui va sans aucun doute changer la fabrication », déclare Martina.
Bien que la start-up ne puisse pas partager certaines images de ses applications pour des raisons de confidentialité, Filomeno Martina a déclaré que l’une de ses applications préférées est le réservoir de carburant en titane pour les satellites que l’équipe a réalisé en partenariat avec Airbus Defence and Space, ainsi que le travail effectué à Cranfield en partenariat avec BAE Systems sur l’énorme châssis en titane de l’Eurofighter Typhoon.
MX3D, du pont en acier imprimé en 3D à un portefeuille dédié à WAAM
Toute l’industrie a découvert MX3D lorsque l’équipe a dévoilé le pont en acier imprimé en 3D qu’elle a construit au-dessus du canal d’Amsterdam à l’aide de la fabrication additive par fil robotisé. Leur parcours dans l’industrie a commencé en 2014 au sein de Joris Laarman Studio, une agence de design néerlandaise travaillant avec de nouvelles technologies telles que l’impression 3D.
Au fil du temps, l’entreprise n’a cessé d’explorer de nouvelles applications en collaborant avec d’autres entités et d’améliorer ses solutions. Une récente levée de fonds que l’équipe a obtenu, révèle que la société a développé le M1, système de FA métal et MetalXL, un logiciel dédié au WAAM.
Le fabricant néerlandais nous a expliqué que son processus est très similaire au soudage robotisé. Toutefois, plutôt que de placer quelques soudures, les composants sont imprimés en empilant continuellement les soudures les unes sur les autres. La solution comprend donc trois éléments de base : un robot industriel, une machine à souder et un logiciel (MetalXL) qui relie le tout et le transforme en une imprimante 3D pour métaux.
« Ces robots peuvent imprimer dans presque tous les métaux disponibles sous forme de fil à souder et les objets imprimés vont de la taille d’un ballon de football à celle d’une voiture. Outre le logiciel MetalXL qui permet de programmer le robot et la machine à souder pour imprimer le dessin CAO en un objet métallique, nous avons également développé et connecté un système de contrôle MetalXL pour surveiller, contrôler et enregistrer l’ensemble du processus d’impression en temps réel et en haute résolution », note MX3D.
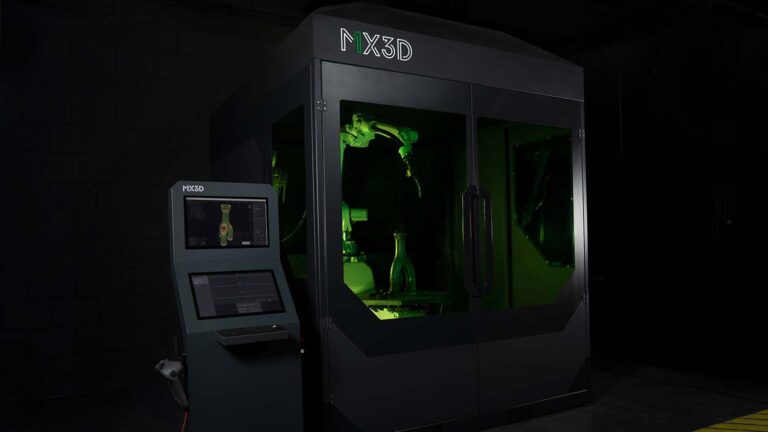
L’équipe de MX3D est l’exemple même d’une entreprise qui apprend sur le terrain. En fait, leur première application – le MX3D Bridge – a révélé des points sensibles tels que la nécessité de combiner divers dispositifs matériels avec plusieurs progiciels, et beaucoup de codage manuel pour obtenir des résultats d’impression optimaux. Le projet suscite également l’intérêt d’autres industries pour le procédé WAAM, ce qui a finalement inspiré le développement de MetalXL. Cette solution peut « transformer en une journée un robot et une machine à souder existants en une imprimante 3D pour métaux de qualité industrielle », affirme la société. Une fois que les utilisateurs ont téléchargé leurs conceptions, ils peuvent choisir leur matériau idéal pour la production (à partir d’une bibliothèque de matériaux ou d’un alliage personnalisé), sélectionner diverses stratégies d’impression et définir les paramètres de processus pertinents.
Outre le pont MX3D, nous avons également fait état, au moyen de notre média en ligne, d’autres applications réalisées par l’entreprise. Il s’agit par exemple d’un bras de robot optimisé, d’un connecteur en acier structurel à haute résistanceréalisé en collaboration avec la société japonaise d’architecture, d’ingénierie et de construction Takenaka, et de deux bicyclettes imprimées. Le dernier en date est un propulseur en acier inoxydable monté sur un système robotique à 8 axes. D’un poids total de 70 kg, l’hélice a nécessité 24 heures d’impression. Elle confirme l’une des principales raisons pour lesquelles les fabricants peuvent être intéressés par la technologie robotique WAAM : la réduction des délais de fabrication, en particulier pour les productions personnalisées de petites séries.
« La meilleure façon d’appliquer et d’utiliser efficacement la fabrication additive est de commencer à imprimer. Nous avons appris en faisant, en essayant de nouvelles façons d’obtenir une meilleure qualité et en imprimant des applications très différentes pour une variété d’industries. Avec notre technologie MetalXL, nous permettons désormais à d’autres de se lancer également dans l’impression 3D métal en interne », conclut l’entreprise.
AML3D and its Arcemy®
Fondée par Andrew Sales en 2014, AML3D Limited est un fabricant australien qui a développé une technologie de fabrication additive arc-fil ou WAM® nommée Arcemy®.
Après avoir fait l’expérience du processus de soudage à l’arc traditionnel, le fondateur a fait des recherches, développé des outils et des processus pour améliorer le processus de fabrication additive par fil. Ses recherches ont conduit au développement du module d’impression ARCEMY® qui est commercialisé aujourd’hui.
« Née des procédés de soudage traditionnels, la technologie WAM® émergente d’AML3D est adaptable, ce qui permet une gamme étendue de capacités de fabrication au moyen du soudage point à point (c’est-à-dire le soudage de tuyaux) jusqu’à la stratification additive du métal (impression 3D du métal) pour fabriquer des pièces quasi nettes dans un environnement de forme libre », déclare la société.
La technologie de dépôt par énergie directe (DED) de la société utilise une variante de la fabrication additive par fil et arc (WAAM). Sa technologie ARCEMY® combine les capacités de la science du soudage, de la technologie robotique, de la métallurgie et des logiciels propriétaires de l’entreprise, WAMSoft® et AMLSoft®. Fait intéressant, le fabricant peut surveiller et/ou gérer à distance le module d’impression ARCEMY® depuis la salle de contrôle centrale située à Adélaïde (Australie).
Parmi les principales caractéristiques qui peuvent aider le système ARCEMY® à se distinguer des autres systèmes de la même gamme, on note que le processus de fabrication certifié WAM® utilise des fils certifiés, qui proviennent de sources locales, ce qui permet de conserver la production sur place.
L’expert australien assure que, grâce au processus de fabrication qui a été soutenu par des tests NATA, les pièces imprimées en acier WAM® sont plus solides que les pièces forgées. Du point de vue des matériaux, « jusqu’à 80 % de déchets de matériaux peuvent être économisés par rapport à la fabrication soustractive traditionnelle et il n’y a pas non plus de gaspillage de consommables, car 100 % du fil consommable est déposé pour la pièce/forme quasi nette produite », a déclaré la société à 3D ADEPT Media.
Même si aucune application tangible n’a été partagée pour ce dossier, AML3D souligne que les pièces imprimées par WAM® peuvent être imprimées à la demande – en quelques semaines – et que les applications maritimes peuvent recevoir une vérification officielle de DNV.
GEFERTEC : plus qu’une simple alternative à la FA métal
GEFERTEC est l’un des fabricants de machines que Verlinde a mentionnés précédemment en parlant des systèmes WAAM basés sur des machines-outils. Fondée en 2015, l’entreprise allemande a choisi l’édition 2017 de l’EMO de Hanovre pour sa première apparition publique. À l’époque, le marché de la FA métallique était encore dominé par les technologies à base de poudre. Pour GEFERTEC, arriver sur le marché de la FA métallique n’était pas seulement un moyen de fournir une autre option métallique aux fabricants qui adoptaient les technologies de FA, c’était aussi donner aux fabricants habitués aux processus de fabrication conventionnels, la possibilité de choisir entre une fraiseuse et une machine d’impression 3D métal.
À l’instar des fabricants de machines ici présents, GEFERTEC propose un processus WAAM entièrement intégré qui comprend des logiciels et des machines. L’entreprise explique que son processus basé sur l’arc et le fil fonctionne avec son logiciel de FAO dédié. La stratégie de construction du composant est déterminée et le code G de la machine à arc est créé.
« Ensuite, la pièce de forme quasi définitive est imprimée de manière entièrement automatique et contrôlée. À travers l’arc, le fil est fondu et déposé couche par couche. Le processus de finition de la pièce imprimée en forme de filet est ensuite réalisé sur une fraiseuse ou une perceuse séparée », explique la société.
Du point de vue des matériaux, on constate que l’on peut produire jusqu’à 600 cm³ par heure en fonction du matériau utilisé, qu’il s’agisse d’acier, de matériaux à base de nickel, de titane ou d’aluminium. L’entreprise assure également que l’utilisation des matériaux est hautement optimisée par rapport aux procédés de fabrication par enlèvement de copeaux, ce qui permet à l’opérateur d’économiser jusqu’à 60 % des coûts de matériaux, en particulier pour les matériaux coûteux comme le titane.
Bien qu’aucune information ne soit partagée sur la taille des pièces imprimées en 3D avec une machine GEFERTEC, une application intéressante que la société a partagée pour ce dossier est un projet mené pour Deutsche Bahn AG. Le projet nécessitait l’utilisation de leur procédé 3DMP® pour la fabrication de pièces de rechange liées à la mobilité qui ne sont plus disponibles en stock et dont les délais de livraison sont parfois extrêmement longs.
« Un composant typique est l’arrêt de roulement secondaire requis dans les bogies des trains ICE. Ce composant limite le jeu transversal de la caisse du wagon et assure ainsi la sécurité des virages des trains dans les courbes serrées », souligne le fabricant.
Forte de ses années d’expertise et de ses nombreuses années à venir, GEFERTEC est fière d’être une solution de fabrication WAAM de bout en bout qui développe et qualifie l’application individuelle de chaque client pour l’aider à mettre en œuvre avec succès le procédé WAAM dans sa production.
Ce dossier a été publié dans le numéro Mai/Juin 2021 de 3D ADEPT Mag.